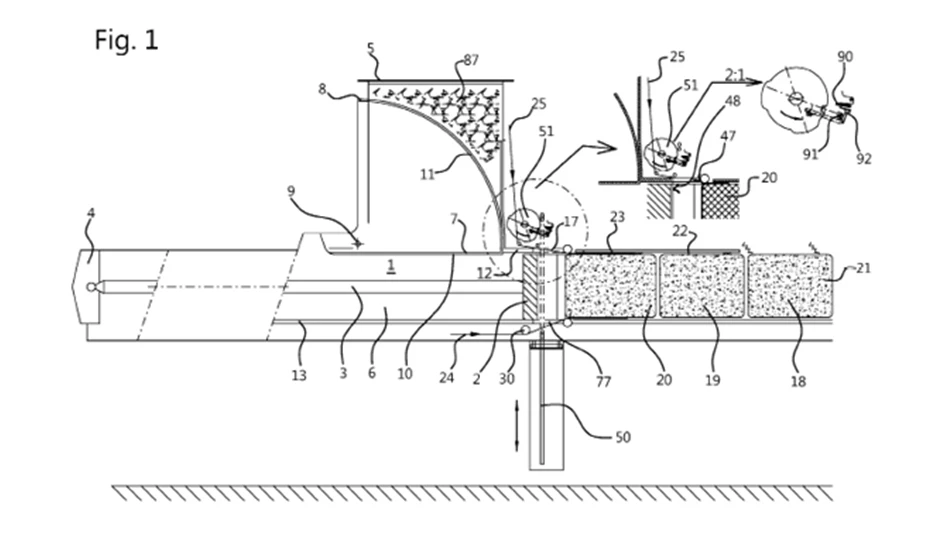
Image courtesy of U.S. Patent Office
Depolymerization process. By employing high pressure, reactor operators can achieve highly efficient depolymerization of polyethylene (PE) of varying densities or polypropylene (PP). The pressure eliminates the need for expensive catalysts, reduces energy consumption and improves the quality of the end products, according to a patent application filed by chemicals specialist Basell Poliolefine, Milan.
The reactor depolymerizes plastic, producing a liquid product and a gas product that can be vented from the reactor or incorporated into another process.
Following depolymerization, the liquid can be subjected to further treatment, such as purification, filtration or chemical reactions, and then directed to a cracking unit where it can be converted it into one or more olefins.Chains of hydrocarbons with fewer carbon atoms generally are prized over those with higher molecular weights.
“Lower boiling points means less energy is required to heat the reactor to effectively carry out the depolymerization reaction and, if maintained at the same temperature, depolymerization can be more complete to yield shorter chain products that are more suitable for further processing,” the application states.
The process subjects postconsumer or postindustrial plastic to temperatures ranging from 752 F to 1,112 F and pressures of between 58 pounds per square inch (psi) and nearly 218 psi. It works with feedstocks with a composition by weight of between 60 percent to 98 percent PE or PP.
According to the patent application, reactor operators can perform the process in the presence or absence of molecular oxygen and can opt to maintain an inert atmosphere.
While operators can choose to employ catalysts, the process does not require them.
“Many catalysts can be poisoned by the additives, pigments and contaminants found in most target waste polymeric material streams,” the application states. “Thus, there exists a need to reduce the amount of high molecular weight hydrocarbons in depolymerization liquids obtained from polymeric materials.”
The patent application refers to high molecular weight hydrocarbons by the carbon atoms they contain. According to the application, the process is efficient in producing chains containing fewer than nine carbon atoms.

“The C9+ hydrocarbon content in the depolymerization liquid may be reduced by 5 percent, 8 percent, 10 percent, 12 percent, 15 percent or more using the systems and methodologies of this disclosure compared to a similar system or methodology operated at lower pressure,” the patent applications reads. “Surprisingly, such reduction may be accomplished without the use of a catalyst.”
Patent application 20230106395; published April 6, 2023
Baling press. A technology patented by a Netherlands-based inventor addresses problems baling press users can experience when using steel or plastic wire by modifying the equipment to better accommodate room to tie knots in rope.
“Compared with tying bales with steel or plastic wire material, tying bales with rope provides the advantage that a wider range of generally lower-cost materials are available and that rope material is generally more robust,” the patent states. In addition to being less expensive, rope made from plastic can be recycled along with the material it’s wrapped around.
The patent, filed by Wouter Hendrik Hogervorst and assigned to Bollegraaf Patents and Brands B.V., describes a baling press with an arm that takes up less space than those on other units. The arm pivots to allow for knotting twined rope around bales.
Patent 11,618,600; issued April 4, 2023
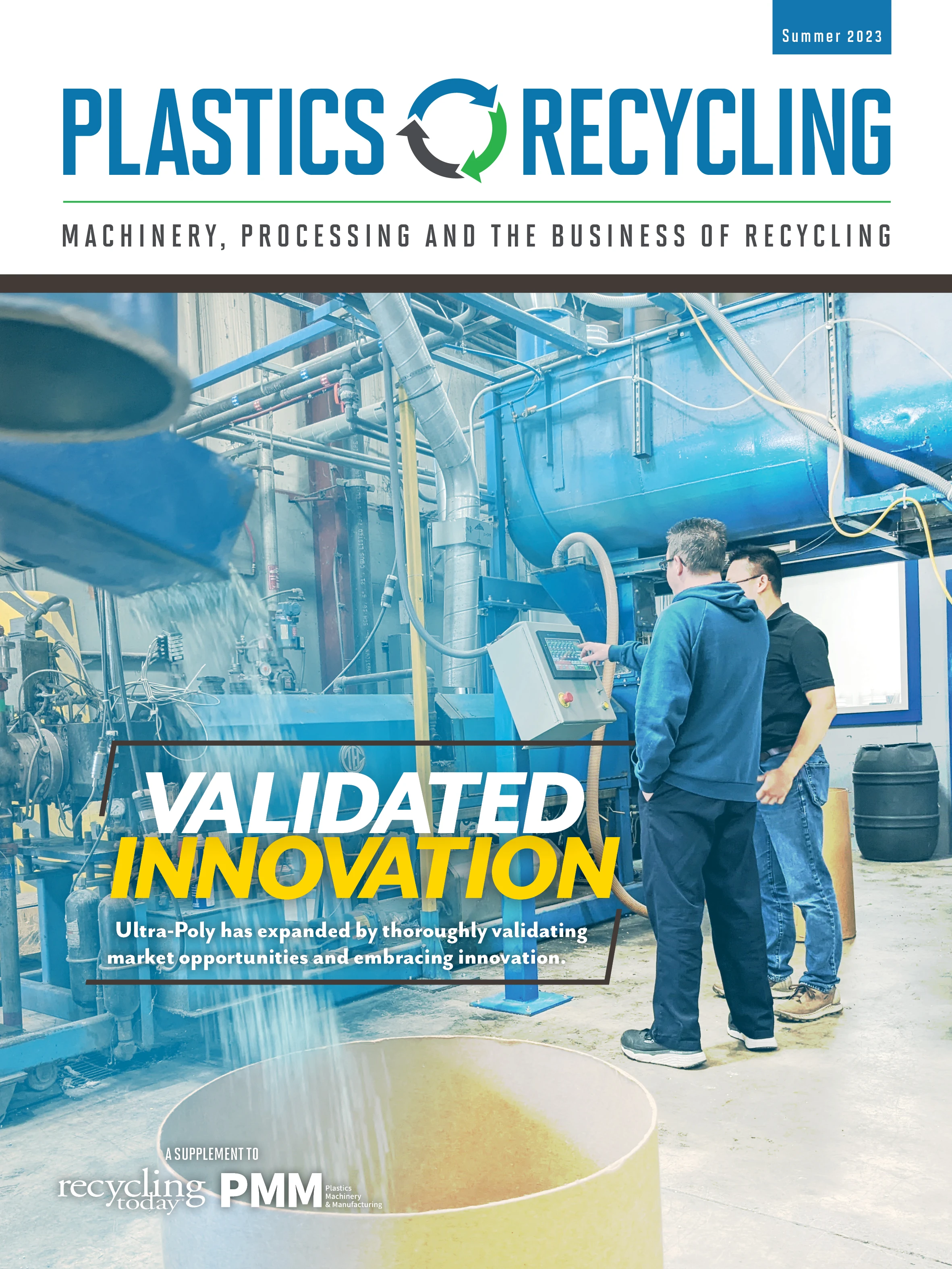
Explore the Summer 2023 Plastics Recycling Issue
Check out more from this issue and find your next story to read.
Latest from Recycling Today
- Green Cubes unveils forklift battery line
- Rebar association points to trade turmoil
- LumiCup offers single-use plastic alternative
- European project yields recycled-content ABS
- ICM to host colocated events in Shanghai
- Astera runs into NIMBY concerns in Colorado
- ReMA opposes European efforts seeking export restrictions for recyclables
- Fresh Perspective: Raj Bagaria