There is an atmosphere of quiet assurance in a company that has been in business for a long time, is doing reasonably well, and has a long-term view of the future. Baker Rubber Inc., headquartered in South Bend, Ind., radiates this assurance. Founded in 1934 by Abraham Baker, and subsequently operated by his son Louis, the company had modest beginnings as a rubber stamping operation, making shims out of tire sidewalls.
Then in the 1960s, BRI began processing its own rubber scrap left over from the stamping operation. Slowly, the company began realizing a market for scrap rubber that was ground into fine particles, or crumb. As time went by, the market requirement for crumb increased, and BRI grew, too. It expanded its South Bend, Ind., plant several times during the 1970s. Then in 1988, it opened a new plant in Chambersburg, Penn., and then another one in Mesa, Ariz., in 1993.
Today, BRI is a private, employee-owned company with about 150 workers. According to company officials, BRI has established itself as the largest crumb rubber producer in the United States, producing roughly 120 million pounds of ground rubber per year. This equates to about 10 million tires annually being removed from the waste stream. It has accomplished that through planned expansions, acquisitions, exclusive joint ventures, a commitment to quality and by marketing its crumb, which the company calls Granulite, as a value-added product.
At the helm of the company is Tim Baker, president, majority owner and son of Louis and grandson of Abraham; Jim Dincolo, vice president, treasurer and part owner, whose father was Louis Baker’s accountant through the years; and Jerry Holland, vice president, technical director and also a part owner.
A BETTER PRODUCT
One way to stay ahead of others in the market is to have a quality product, and BRI has worked on adding value to its crumb. First, by giving it a catchy trade name, Granulite; and second, by making sure the crumb is pure and free from foreign material. Quality control is critical at BRI and it is an area that the company has concentrated on in its efforts to create a superior product.
The process starts with the incoming material, much of which is in the form of tire chips processed by other companies. "We work closely with our suppliers of tire chips to ensure that quality material is coming into the plants," says Holland. "We don’t just call up the vendor and say ‘deliver a load of tire chips.’ We want to make sure it is the right stuff. And that means being free of foreign material, usually smaller than one inch, and sometimes we need all black chips, with no whitewall rubber."
Holland says that BRI will also specify the type of tire chip, too. "There is obviously different compounding from tire to tire, so many times we will specify ‘all passenger tire chips’ or ‘all truck tire chips.’ It gets more critical between truck tire shreds and off-the-road shreds. The OTR shreds are usually significantly different from the rest in terms of compounding, and we need to segregate the OTR chips. So, my message to those who are shredding tires out there is that it pays to keep track of what is being shredded."
"The secret is not that we have phenomenal equipment that no one else has, but our experience and quality controls," says Dincolo. "We have a keen attention to detail."
"Our equipment is basically off-the-shelf stuff, but we make some modifications," says Holland. One of BRI’s methods uses a mechanical cracking system which begins with the whole tire, removes the tire bead, chops the tire, removes the fabric and metal, and grinds and screens the rubber.
Another key to BRI’s continuing success is being able to produce very fine crumb in the 80 mesh and beyond range. That ability comes from BRI’s Micron equipment that it purchased from Goodyear Tire & Rubber, Akron, Ohio, last year. The equipment was transferred to BRI’s Chambersburg plant and has been operational since January 1995. The proprietary equipment takes whole tire material to crumb and produces a very fine end product that is used in products that require that grade. "In many products, finer is better," says Baker.
A NEW PROCESS
Another key to being a successful company is having a product or process that is unique. Last year, STI-K Sdn. Berhad, a Malaysian-based firm with an office in Washington, announced that it had achieved a breakthrough in processing crumb rubber.
The company claimed it was the first company to truly devulcanize rubber. Now, STI-K is working with BRI as an exclusive supplier in the United States to create a significant supply of STI-K’s new product.
Ever since the late 1800s, when Charles Goodyear accidentally discovered that adding sulfur to rubber made it a more predictable and stable substance (that is, the sulfur prevented the rubber from getting gooey in the summer or rock hard in the winter), it has been difficult to break the sulfur bonds in vulcanized rubber. But STI-K has a new proprietary process to do so economically.
The STI-K process uses a chemical reactant consisting of chemicals common to the rubber industry, according to the company, to break the sulfur links in vulcanized rubber. Although STI-K says the reactant, called De-Link, only actually devulcanizes the rubber to produce an end product with 75 percent of the properties of natural rubber – because some of the sulfur bonds cannot be broken – it says its final product, called De-Vulc, is good enough for applications that normally require virgin rubber, including new tires. Michelin, which recently announced that it could eventually use up to 10 percent recycled rubber in its new tires, says that its method is different from the De-Link process, although STI-K officials have reportedly met with the tire company.
The benefits for BRI are obvious as long as STI-K keeps its proprietary relationship with the company.
"There is risk with any venture, but this has the potential of being ‘lead to gold,’" says Baker. "It is something that people have dreamt about for a long time. STI-K is marketing its product here and we are the only facility that will be producing a De-Vulc."
Dincolo says that about $400,000 from BRI, another $500,000 from an Indiana Recycling Promotion and Assistance Fund loan and $750,000 from STI-K is being spent to upgrade its South Bend facility so that production of De-Vulc crumb rubber can begin by end of the year.
"Our arrangement with STI-K is simple," says Holland. "STI-K is operating side-by-side with us in our South Bend plant ‘devulc-ing’ the crumb as it comes off the line. We are selling crumb to STI-K, which then is selling its product on the market. So, in effect, STI-K is adding another level to the process."
If De-Vulc lives up to expectations, the potential is far-reaching. "The STI-K product is exciting," says Dincolo. "There is still some skepticism in the rubber industry, but if it works as expected, demand will be significant. The De-Vulc rubber will be less expensive than virgin rubber. This alone could supplant the amount of crumb that was expected to be used for asphalt."
But there are other important factors, he adds. Most importantly, that with De-Vulc, a manufacturer can chemically bond crumb rubber to other materials.
"A tire is a thermoset product. That means it is inert, does not react with anything, and that is also why it does not leach or decompose rapidly," Dincolo explains.
"So when you crumb it, it still is in that thermoset state, just in smaller particles. In order for it to be used again, you need a binder or a glue to bind it to other materials to manufacture a product. And manufacturers don’t like this. They want a chemical bond, and crumb rubber cannot give that right now. With the De-Link process, crumb can be used in even more significant applications."
And more use by tire companies in the manufacturing of new tires can be one of the major markets for De-Vulc. Already, tire companies use recycled rubber in new tires, but it is a very small percentage, less than 1 percent. That’s what makes Michelin’s 10 percent commitment significant.
Holland agrees that the biggest potential is in new tires. "If Michelin’s efforts come to fruition," he says, "it could have major implications in the market."
But this may take longer than expected, warns Mike Blumenthal, executive director of the Scrap Tire Management Council, an arm of the Rubber Manufacturers Association, Washington.
"Michelin’s statement to use 10 percent recycled rubber is pretty bold," says Blumenthal. "The company has given a fairly wide window to accomplish this feat – five years – and a lot can happen from now until then, including the company saying that it needs another five years to develop its process."
As for STI-K, the company says it is making enough De-Link to create 29,000 tons of De-Vulc rubber per month worldwide, and the project with BRI is expected to divert about 1.6 million scrap tires annually from the waste stream.
SCRAPPING A MANDATE
Three years ago, the Intermodal Surface Transportation Efficiency Act of 1992 raised hopes that significant tonnages of scrap tire rubber would be required in federally-funded highways.
It was primarily the expectations of that bill, and the subsequent failure of the mandated provision, that is responsible for the current state of the crumb rubber market today, according to Dincolo.
"Right now, there is more supply than demand, and I think that is because the ISTEA mandate attracted a lot of people into the scrap tire processing business," says Dincolo. "Now, that market has evaporated and there are still all these companies trying to make a living. There is simply nowhere for the product to go. So, I think we are about to go through a ‘shake out’ period."
Specifically, ISTEA required every state to use 5 percent crumb rubber in all federally-funded highway projects in 1994; 10 percent in 1995; 15 percent in 1996; and 20 percent in 1997.
However, the mandate has been delayed twice, and many in the industry feel it will never be enacted.
"ISTEA gave minimum use for states," says Baker. "There was resistance from states because it was an unfunded mandate, and from the National Asphalt Pavers Association because it did not want to be told what to put into their product. There are five segments of the legislation, and the minimum crumb rubber content part was the section that was not put into action. The legislation is still out there, and the provisions for continuing education about rubberized asphalt and testing are still there, plus grant money is still being awarded. It is just that now, it is a longer-term situation than before."
Naturally, Baker was expecting increased business due to the mandate. "We did pin some of our hopes and market gains on the ISTEA legislation," says Holland. "We were anticipating that the legislation would help us grow, and we were gearing up to handle the increase business from the mandate, but we also had a healthy dose of skepticism."
Baker, too, says that the mandate would have definitely helped his company, but downplays the coincidental construction and opening of its latest plant in Mesa, Ariz., in 1993, just prior to the time the ISTEA mandate was to take effect.
"We did not build our Mesa plant predicated on ISTEA legislation alone," says Baker. "We built it because both Arizona and California are way ahead of the pack in terms of uses for crumb."
Baker, who is also the chairman of the Rubber Pavements Association, Washington, has examples to back up his belief in rubberized asphalt.
"People say that rubberized asphalt works best in hot, dry climates typical in the Southwest, but those states have climate conditions far worse than any northern state. Look at Flagstaff, Ariz., for instance. The conditions there can get real nasty. Near Flagstaff a badly distressed road was paved with rubberized asphalt and it has performed better than anything to date."
As for scrap tire legislation on a local level, Baker has mixed feelings.
"Some states have done a good job and have helped companies like us, and some have done a miserable job and have been a hinderance," he says.
"It is so complex in terms of regulations and the industry. If there is legislation it should be written around environmentally sound disposal and stimulation of markets. There should not be legislation geared around just processing the tires, because increasing the supply of the processed product will not increase demand."
Baker says that there needs to be a set bottom standard of proper tire disposal. A tire only makes up about 1 percent of the solid waste stream, and Baker says "if proper disposal is not where you want to end up, then put in legislation that stimulates the marketplace."
He also says to make sure that the legislation is enforceable. "If not, you only are penalizing the legitimate businessman," he says.
Overall, though, the BRI leadership is against mandates, even though they may help the company in terms of more business.
"When ISTEA first came out, we thought it was a good thing, but I don’t think mandates work," says Dincolo. "I want the market to stand on its own merit and value. If rubberized asphalt is superior to conventional asphalt, for example, then the market will eventually take care of itself."
PRICING PRESSURES
Even though BRI is doing well, Baker says that profit margins are generally starting to erode. That is due mainly to an extraordinary influx of new processors that were counting on the ISTEA mandate to support their operations.
"This is an industry that currently has a lot of shaking out to do," says Baker. "There is a lot of influence being exhibited by the ‘wanna-bees’ new to the industry who are flooding the market with crumb ... A lot of people are starting in the scrap tire processing business without a business plan, and without a market for their product it makes it difficult for the rest of us because there is a lot of dumping of material and prices are depressed."
Sponsored Content
Labor that Works
With 25 years of experience, Leadpoint delivers cost-effective workforce solutions tailored to your needs. We handle the recruiting, hiring, training, and onboarding to deliver stable, productive, and safety-focused teams. Our commitment to safety and quality ensures peace of mind with a reliable workforce that helps you achieve your goals.
Baker says that there are many questions to ask when considering starting a new rubber grinding plant, such as capacity, type of tires being used, supply of tires, mesh size, quality, financing, quality control, having a reliable shipping network and, most important, having markets for the end product.
"Processors have to realize their costs," says Dincolo. "You can’t keep selling your end product for 10 cents a pound when it is costing you 12 cents a pound to produce. Right now, the margins are so small in this industry that you have to be aware of tenths of a cent in movement in the price of crumb.
"We are trying to get our customers to understand the technology that we use and the costs associated with that, but currently the basic motivation is price. All purchasing agents want the best price, and they are not always looking at quality. So, we are trying to change that line of thinking."
Holland says that the crumb rubber industry is currently growing by about 10 percent to 15 percent a year, without rubberized asphalt. "But if you do include asphalt, it would not increase the percentage by much," he says. He adds that there is no shortage of scrap tires, even though there are more processors in the industry and fewer tires stockpiled throughout the U.S. than originally estimated.
"In fact, with all the processors coming on line and the cleanup programs, there is an abundance of scrap tire chip material," says Holland. "It’s good because of the supply, and it’s bad because of the depressed prices."
Holland adds that the supply situation is one of the reasons that the Chambersburg plant does not need to shred tires – there is an abundance of tire chips in the East. With the Mesa plant, however, it is a different story.
"We shred whole tires at Mesa for several reasons," he says. "First, the state wanted us to help in the relief of the scrap tire problem. Second, the number of shredding processors in the Southwest is low. The Mesa plant was also built because the use of crumb in asphalt is advanced in the Southwest, especially in Arizona where many roads are already paved with rubber asphalt."
Another source of crumb for BRI is from tread rubber buffings. Although scrap tires are plentiful, buffings from the retreading industry are tight right now because markets have been found for that scrap product. "Buffings are more pure," says Holland, "that’s why they are harder to get, because they don’t contain metal and fiber."
Overall, 95 percent of the scrap rubber that BRI uses is tire-related, including scrap tires, buffings and tread rubber.
With the pricing pressures and abundance of supply, Baker still sees a day when all the stockpiled tires will be gone, and the market will have to rely only on the annual 250 million generation rate.
"The primary method will be energy recovery, but that should not stop people from getting into higher reuses of the material," says Baker.
NEED FOR COHESION
Another area that crumb rubber producers may have to deal with in the future is trading on the Chicago Board of Trade, where crumb rubber futures may be sold and bought and a grading system established.
"I am taking the CBOT proposal seriously," says Dincolo. "But I think first the crumb rubber producers have to act like an industry, and we are not one right now. Scrap tire processors are operating in a vacuum with no direction. A lot of companies are doing their own thing. I am not saying that there should be a cartel, but in other established industries, executives share certain information and react to it in a unified manner. There is a general sense of cohesiveness, and every action and reaction is understood.
"We are not at that stage yet. Many decisions are being made in this business without understanding the consequences of those decisions. So, I think the CBOT will not truly help until we become a cohesive industry first."
Striving toward that cohesiveness, BRI has been active in the scrap tire industry, mainly through RPA and the American Retreaders Association, Louisville, Ky.
In addition, BRI was a founding member of the recently formed Tire & Rubber Recycling Advisory Council, and is involved with the American Chemical Society’s Rubber Division, Akron, Ohio, and its Rubber Recycling Topical Group. BRI also has published several technical papers about crumbing.
"We feel that it is real important to be a part of the industry and through the associations," says Baker.
"I also think this industry really needs some more R&D dollars to learn how to recycle better and make more products with crumb," says Dincolo.
"Creating new markets is the key. It took a long time to figure out what to do with paper and other recyclable material; now we need to do the same with crumb rubber."
The author is managing editor of Recycling Today.
Get curated news on YOUR industry.
Enter your email to receive our newsletters.
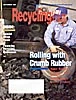
Explore the September 1995 Issue
Check out more from this issue and find your next story to read.
Latest from Recycling Today
- AF&PA report shows decrease in packaging paper shipments
- GreenMantra names new CEO
- Agilyx says Styrenyx technology reduces carbon footprint in styrene production
- SABIC’s Trucircle PE used for greenhouse roofing
- Hydro to add wire rod casthouse in Norway
- Hindalco to invest in copper, aluminum business in India
- Recycled steel price crosses $500 per ton threshold
- Smithers report looks at PCR plastic’s near-term prospects