
Scrap metal products are maintaining and adding to their value in the era of the circular economy, sustainability and reduced greenhouse gas emissions. For metals recyclers such as those operating auto and metals shredding facilities, revenue is assured, but profits can depend on minimizing operating costs.
The Danieli Centro Recycling (DCR) and Danieli Automation business units of Italy-based Danieli Group are dedicated to working with their shredder operator customers to boost productivity while keeping costs in check. One of the results of this effort—a medium voltage/low voltage (MV/LV) inverter for shredder motors—is earning rave reviews from an initial customer.
Danieli’s patented Smart Power Technology offers an innovative control strategy that provides energy savings, improved productivity, longer life for some wear components and a reduced impact on a facility’s electricity distribution network. It does this by converting an existing, fixed-speed direct online three-phase asynchronous motor (either squirrel cage or wound rotor configuration) to a state-of-the-art variable-speed drive system.
Danieli’s Smart Power Plug & Shred Solution has been on the job for a United Kingdom-based shredding plant operator for several months. The recycling company says its MV/LV inverter has lived up to all the marketed return on investment (ROI) and cost savings benefits promised by Danieli.
Before installing the inverter, the U.K.-based recycler’s shredding plant had been experiencing considerable problems with power peaks on the network, typical of a shredder motor with a liquid resistance starter (LRS). Ongoing problems included flickering, voltage and power factor fluctuations that resulted in financial penalties from the utility company, high electrical costs and limited power availability.

A power measurement analysis found that between 15 and 20 percent of all energy demanded on the network was being dissipated as heat with the LRS in place. The customer decided to invest in Danieli’s inverter upgrade technology to replace the LRS, with an eye on making the shredder more cost-effective and environmentally friendly. An analysis performed after the commissioning of the inverter showed immediate electrical consumption savings of approximately 20 percent, as measured by kilowatt hours per ton.
The cause of the former utility company penalty charges also disappeared since the shredder plant was no longer exceeding a set power limit that triggered both the penalties and unplanned network disconnections. A Danieli control strategy tied to the inverter installation was able to limit the maximum power demanded from the network while increasing motor average utilization (service factor)—resulting in an approximate 40 percent increase in production.
The productivity arises not only from the energy savings costs but also from operational flexibility improvements provided by the inverter.
The recycling company says when it was processing baled material with the LRS, the power fluctuations were at their most troublesome, reaching peaks of up to three times its contracted rated power allocation. To reduce these power fluctuation costs, the customer was forced to reduce the use of bales and to mix the bales with lighter material that offered lower throughput.
With Danieli’s inverter, the customer can process up to 100 percent baled material, improving productivity without impacts on its energy network. During commissioning, the customer accidentally raised the feed rollers, letting three bales and mixed material suddenly enter the shredder chamber. The customer witnessed how the Danieli system handled this overfeeding situation without any issues, such as a stalled motor or taking downtime to clean material from the shredder.
On the cost savings side, the recycler also reports the inverter motor speed can be adjusted to help it find the best setting that maximizes production, energy savings and wear part life.
The benefits experienced by the U.K. recycler are available to shredder plant operators around the world, says Jim Summers and Giuseppe Muscanera of DCR.
“The customer estimates the inverter upgrade will pay for itself in less than six months, stemming primarily from the gains in productivity,” Summers says of the U.K. recycler’s installation.
Muscanera says those same benefits translate across the Atlantic, where North American plant operators can face similar limitations with an LRS configuration.

“In general, every shredder plant will benefit from installing an inverter,” says Jim Stepanek, who is based in Iowa as DCR’s sales leader – North America.
Muscanera and Stepanek say the benefits are most clear for operators who have encountered limitations with their electrical utility provider or who are running older equipment that is due for an upgrade.
Stepanek says he is eager to talk to customers in North America who are considering any kind of upgrade to their shredding plant. “This new DCR technology is ideal to replace older configurations such as DC motors with converters, diesel engines and drivelines with hydraulic couplings. Those setups can create high maintenance costs and offer a low level of reliability. DCR can help—and help immediately.”
Julian Eglinton, sales director for USA, says auto shredder operators anywhere in the world who are linked to “weak power networks, where it is not currently feasible to install electric motors, and so they use diesel engines as the only option” can instantly benefit from DCR Smart Power Technology.
The inverter technology has been used for years by Danieli in its rolling mills and melt shop, then applied in 20 shredder installations in Europe. Recently, Danieli further expanded its experience and implemented this solution on already-installed units worldwide.
Find out more information on the Danieli Centro Recycling Smart Power Technology Plug & Shred Solution online at https://bit.ly/danieli-scrap-recycling.
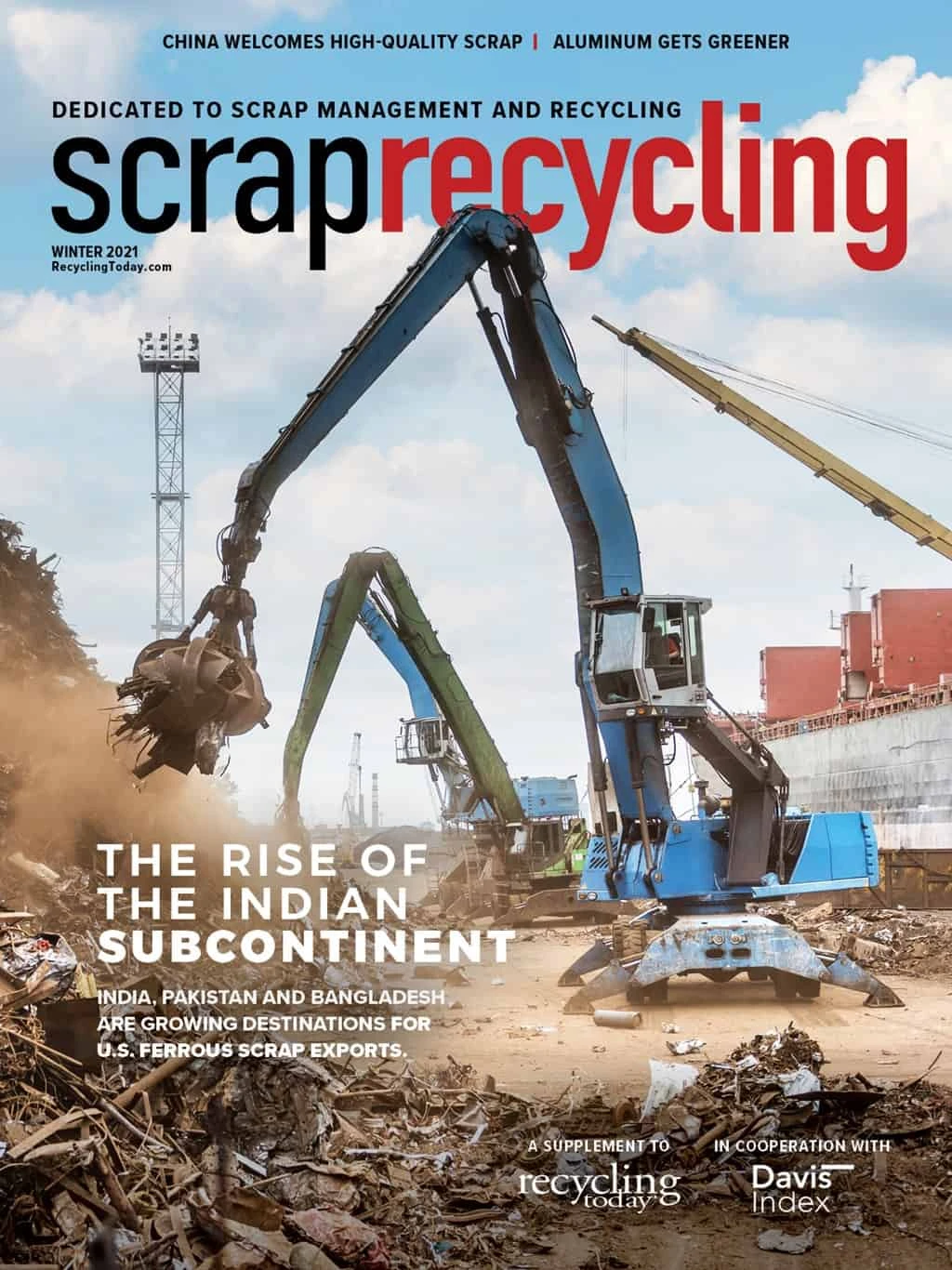
Explore the Winter 2021 Scrap Recycling Issue
Check out more from this issue and find your next story to read.
Latest from Recycling Today
- LumiCup offers single-use plastic alternative
- European project yields recycled-content ABS
- ICM to host colocated events in Shanghai
- Astera runs into NIMBY concerns in Colorado
- ReMA opposes European efforts seeking export restrictions for recyclables
- Fresh Perspective: Raj Bagaria
- Saica announces plans for second US site
- Update: Novelis produces first aluminum coil made fully from recycled end-of-life automotive scrap