

The founder of Italy-based Danieli & C. S.p.A., Mario Danieli, began working in an electric arc furnace (EAF) steel meltshop in 1914, which helped prepare him for founding his own equipment-making company in 1948.
Mario and succeeding generations of Danieli family members and engineers have helped the company flourish, globalize and expand its product line. Today, more than two dozen Danieli business units and divisions provide technology for the entire steelmaking production chain, including Danieli Centro Recycling, a provider of shredding plants, shears and balers to the metals recycling sector.
The combined knowledge of the entire Danieli organization—including its in-depth meltshop experience—is brought to bear when Danieli is called upon to help recyclers in North America or anywhere else in the world prepare ferrous scrap for meltshop consumption.
“Converting scrap grades into ideal meltshop material requires advanced knowledge of metallurgy, engineering and automation techniques that only a company like Danieli is poised to supply.”
Extending an already admirable definition of 'turnkey'
As a startup in 1948, Danieli produced small shears and anvils before expanding to manufacture machinery for steel rolling mills in 1960, after Mario’s son Luigi joined the company.
Danieli continued to flourish under the leadership of Luigi’s daughter, Cecilia. A testament to this remarkable growth is the fact that the firm has been entrusted to design and equip more than 135 steel mill turnkey installations globally.
From meltshops to casting houses to rolling mills to downstream galvanizing lines, the world’s steelmakers trust Danieli. That trust also extends to systems that provide feedstock for meltshops, whether in the form of direct-reduced iron (DRI) production or scrap processing equipment.
The carefully planned development of Danieli Centro Recycling has involved listening to mill customers and scrap processors to develop new equipment and technology. Additionally, the company has been willing to acquire knowledge and technology through strategic acquisitions of equipment companies deemed capable of meeting Danieli’s standards.
Raffaele Calligaro, executive vice president of Danieli Centro Recycling, lists high productivity and stringent safety standards as the two factors inherent in its equipment that have helped it earn the trust of scrap processors and steel producers that prepare their own scrap.
The company and its product designers and engineers have a keen understanding of the tough environment and long working hours to which Danieli shears, balers and shredders are subjected. Likewise, they know metals recycling plant operators will use their machinery intensively, so they prioritize minimal downtime and ease of maintenance.
Thanks to internal innovation and key acquisitions (such as Lynxs, Henschel and Riverside Products), Danieli Centro Recycling is the only partner with the technology and expertise to bridge the gap between scrap processing and steelmaking, adding the critical step of scrap preparation to its already impressive definition of the word ”turnkey.”

Tough but intelligent systems for a basic but complex industry
Steelmaking might be considered a basic industry, but the chemistry-related challenges and automation-related opportunities present in the sector call for equipment that, while rugged, also needs to pass an IQ test.
Danieli Centro Recycling knows what its scrap processing customers need on a daily basis: robust, safe, reliable equipment built to meet the arduous conditions imposed by the market.
Converting scrap grades into ideal meltshop material requires advanced knowledge of metallurgy, engineering and automation techniques that only a company like Danieli is poised to supply.
One of several breakthrough technologies it has developed is Danieli Scrap to Melt (DSTM), a sophisticated shear downstream system that continuously analyzes (with a PGNAA, or prompt gamma neutron activation analysis, scanner) the sheared scrap’s alloyed metals’ chemical composition, sorting the flow based on a given/known composition. This allows Danieli shears to be much more than size-reduction machines, providing material that can meet specific chemical composition requirements of meltshops.
In terms of safety, Danieli is well-aware of the risks of working inside a scrapyard or a steel mill, which is why the company continuously invests in R&D to manufacture safer and more easily maintainable machinery.
As a result, Danieli has developed and patented the world’s first-ever scrap shear with an automatic blade-changing system. This allows for a full blade replacement in less than 30 minutes, guaranteeing maximum safety as well as a drastic decrease in machine downtime.
Regarding its shredding plants, Danieli offers innovative mill geometry and fully automatic control systems that provide high throughput with low power consumption costs. The company’s mills are designed to produce shred that is fully prepared for the automated separation steps to follow.
In an era of competitive cost consciousness, Danieli’s patented Plug&Shred technology offers an innovative control strategy that provides energy savings, improved productivity, longer life for some wear components and a reduced impact on a facility’s electricity distribution network.It offers these cost-cutting and productivity advantages by converting an existing, fixed-speed direct online three-phase asynchronous motor (in either squirrel cage or slip ring configuration) to a state-of-the-art variable-speed drive system.
Another Danieli innovation that contributes to its shredders’ durability and ease of maintenance is a patented automatic reject door (Q-ARD) that helps divert unshreddable materials before they have a chance to knock a shredder offline.
Environmental obligations also require top-shelf technology. Danieli’s state-of-the-art dust extraction, suppression and control techniques ensure its equipment meets current and foreseeable statutory emissions requirements.
Danieli Centro Recycling works in close collaboration with processors and steelmakers to understand all aspects of optimal scrap yard operations. This results not only in continual machinery improvement, but it also helps develop the best scrapyard layout for each customer. A typical study of a customized layout is available on the Danieli website.
Recyclers in North America and beyond can contact Danieli now to benefit from more than a century of experience that has created a company prepared to serve those seeking sturdy equipment designed to make meltshop-ready scrap for the global market.
Danieli USA
600 Cranberry Woods Drive, Cranberry Township, PA 16066
Phone: 724-900-8750
Email: info.centrorecycling@danieli.com
Find more information on the Danieli Centro Recycling website.
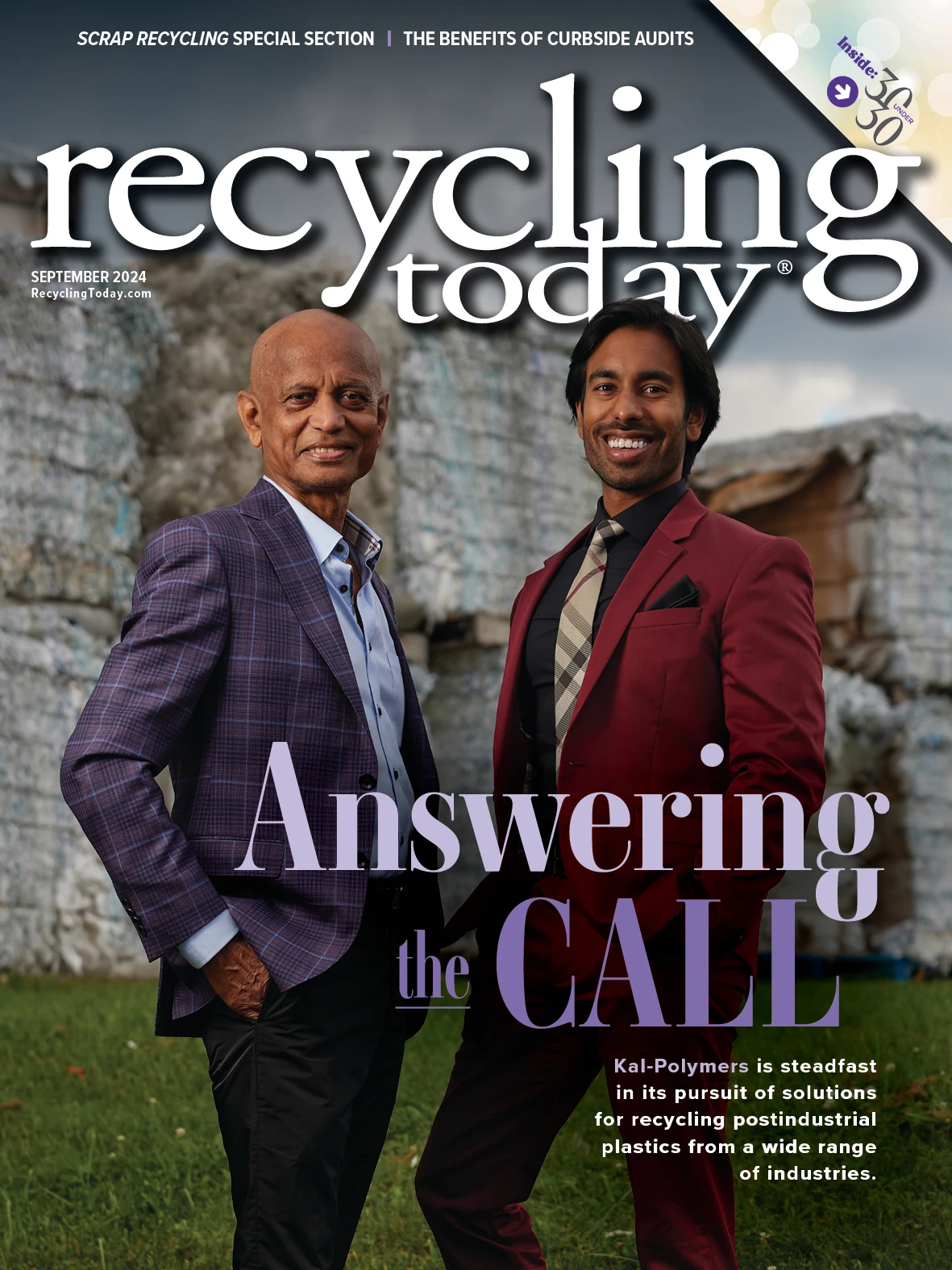
Explore the September 2024 Issue
Check out more from this issue and find your next story to read.