Recyclers of scrap metal have long used lifting magnets and grapples to unload and load scrap, as well as to move it within the yard and feed it to larger processing equipment.
Magnets and grapples remain on the job in those capacities at scrap yards, but they have been joined by growing numbers of hydraulic shears (and on demolition sites, shear hybrids) that also process and prepare scrap to increase its value.
The shear market has been hot for the last several years, as demolition scrap and other forms of obsolete scrap flow into scrap facilities where yard managers are eager to quickly turn this stream into marketable secondary commodities.
ON ORDER. Equipment dealers who cater to the scrap market say the increasing interest in shear attachments has been clear to see in the past several years.
"Scrap shears, both rotating and non-rotating, are very popular," says Lee Gibson, president of Gibson Machinery LLC, Cleveland.
By concentrating his dealership on the scrap and demolition industries, Gibson says he has become a leading dealer for Genesis Attachments, earning a No. 1 ranking from the shear maker in 2004 and No. 2 last year.
During that time, Gibson says rotating shears have gained favor. "Most of our customers buy rotating shears," he remarks. "I think it’s kind of a necessity for the demolition contractors, and it has become preferred by the scrap contractors. We probably sell about 80 percent rotating shears, because they can be very efficient by saving the operator the need to move the scrap handler or excavator as much."
Brad Hutchinson, co-owner of Stanley LaBounty dealer Company Wrench, Carroll, Ohio, sees a similar pattern with his customers. "Most of the demolition contractors are looking for rotating shears, and using non-rotating models only if they are doing some straight scrap processing on the job site."
Allied-Gator Inc., a Youngstown-Ohio based maker of shears and processing attachments, also offers its attachments with 360-degree rotation to appeal to its demolition contractor and scrap recycling customer base.
Hutchinson says the past two years have been critical in the growth of hydraulic attachments sales because smaller contractors and processors are starting to use the tools.
"Although the large contractors have been using them for years, believe it or not a lot of smaller demo contractors are just now starting to use these types of tools," he remarks. "Some of them had been using a wrecking ball up until the past 24 months or so."
Magnetism |
Youngstown, Ohio-based Allied-Gator Inc. has introduced the MT Series Mag Extension, which enables an excavator to perform the same functions of a dedicated material handler equipped with a magnet, according to the company. In a press release, Allied-Gator says, "This product allows the magnet to achieve a unique range of motion that is not found in any other machine arrangement capable of accepting a magnet." The MT Series Mag Extension uses patent-pending UCS technology that is also found in the MT Series Multi-Tool line and other Allied-Gator products. When used with the MT Series Multi-Tool, Allied-Gator says the MT Series Mag Extension enables a single excavator to perform demolition, processing, material handling and site cleanup, reducing the need for several machines performing single functions. |
The growth in popularity of shears and shear hybrids (variously known as multi-processors, multi-tools, concrete pulverizers or by other terms, depending on the brand) combined with an overheated scrap market has helped spur sales and, in some cases, created back order situations for the devices.
As one of Stanley LaBounty’s largest dealers, Company Wrench is carrying more than a dozen models in inventory and has others on order. But from what Hutchinson hears, when he goes to replace those he can expect to wait four months or so to take delivery on future shears and pulverizers.
HARD WORK. A loyal Gibson Machinery customer this decade has been Cleveland Scrap. The company was started by the Youngman family, owners of nonferrous processor Lakeside Metals, also in Cleveland.
The new Cleveland Scrap location has been set up to process ferrous scrap at a different site that would not displace any of Lakeside’s traditional nonferrous activities.
Break it Down |
Before material is pulverized or sheared at a demolition site, it may have a hammer put to it. Companies like Atlas Copco Construction Tools, West Springfield, Mass., are among those offering demolition hammers that break slabs of reinforced concrete down into sizes where other processing tools and equipment can handle them. Such hammers can be attached to excavators or they can be operated by manual laborers using hand-held machines. The heaviest of the company’s four standard handheld breakers in its newest line is the 71-pound LH 39, which the company say "can provide a cost-efficient alternative to rig-mounted breakers for heavy-duty applications in reinforced concrete, heavy asphalt and foundations." Atlas-Copco also offers excavator-mounted hammers, as do companies such as Breaker Technology Inc. (BTI) and Allied Construction Products LLC. BTI severe-duty breakers appeal to demolition contractors, according to the company, while Allied Construction Products distributes Rammer brand models such as the in-Series, designed to operate in narrow work areas. |
According to Cleveland Scrap President Jake Youngman, the company has enjoyed healthy flows of incoming ferrous metal since starting the business, but has retained the processing methods it set up initially.
"We’ve been running mobile shears on hydraulic scrap handlers for about two-and-a-half years," says Youngman. However, the number of scrap handlers and the number of shears the company operates has grown steadily.
As it is now set up, Cleveland Scrap has an impressive fleet of hydraulic handlers deployed throughout its eight acres of land. "The loads come in from, say, a demolition site and are taken to one of eight cutting stations, where we have scrap handling machines outfitted with one of several types of shears," says Youngman. Included in the shear collection are Genesis and LaBounty shears and two rebar shears, also made by Genesis.
For now, Cleveland Scrap conducts all of its processing without any pieces of large shearing or baling equipment. It is possible that the company may choose to make such an investment in the future, Youngman concedes, but he also says, "We’re pretty happy with our arrangement right now."
Allied-Gator Inc. learned how one of its new devices performed at a recent Allied Erecting & Dismantling Co. Inc. demolition job at former steel mills in northwest Indiana, where obsolete equipment made of cast iron had to be downsized and prepared for shipment to a consumer.
The contracting firm used an Allied-Gator MTR70 mounted on a Caterpillar machine to help recover and prepare some 63 tons of cast iron, including 25 tons that had once been an generator used to power a steam system.
Allied Erecting & Dismantling machine operator Keith Finch says he was able to break apart the generator and separate the cast iron from the copper in just one half-hour using the automated equipment.
MORE TO DO. With scrap markets remaining healthy and demolition contractors convinced that shears and shear-like devices are worth the investment, the boom in hydraulic attachments may still be underway.
In mid-March, Hutchinson helped deliver a universal processor to a demolition contractor in Hawaii who is taking down buildings to make way for the future Trump Tower Waikiki.
While a quick trip to Hawaii may not be the worst inconvenience a person can suffer, it shows to what lengths (and distances) attachment companies and their dealers will go to serve their growing customer base.
The author is editor of Recycling Today and can be reached at btaylor@gie.net.
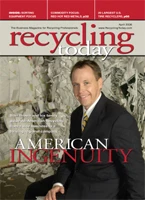
Explore the April 2006 Issue
Check out more from this issue and find your next story to read.
Latest from Recycling Today
- Fitch Ratings sees reasons for steel optimism in 2025
- P+PB adds new board members
- BlueScope, BHP & Rio Tinto select site for electric smelting furnace pilot plant
- Magnomer joins Canada Plastics Pact
- Out of touch with reality
- Electra names new CFO
- WM of Pennsylvania awarded RNG vehicle funding
- Nucor receives West Virginia funding assist