
"Plastics.”
The one word of advice given to Dustin Hoffman in the 1967 movie “The Graduate” has certainly proven prophetic. The world is awash in plastic from bottles to bags, films to fiber and toys to textiles.
But what “The Graduate” didn’t tell us was how significant plastic’s impact on the planet would be. Every day, the equivalent of more than 2,000 garbage trucks full of plastic finds its way into our oceans, rivers and lakes. In fact, the world is producing twice as much plastic waste than it was two decades ago, with the bulk of it ending up in landfills, incinerators or in the environment. Only 9 percent is recycled, according to some estimates.
The tide is beginning to turn
While most plastics produced today are made from crude oil or natural gas, global production of recycled plastics has more than quadrupled in the last 20 years. Crude oil prices are creeping higher, and some states have passed laws requiring postconsumer recycled content in plastic packaging, while some corporations have committed to using recycled content in their plastic packaging. Coca-Cola, for example, has pledged to use 50 percent recycled polyethylene terephthalate (PET) in its bottles by 2030.
Increasingly, consumer goods manufacturers are designing plastic packaging to ensure its recyclability so it can be more easily converted into usable secondary raw material.
This movement presents challenges—and opportunities—to plastics recyclers that shred, granulate and pelletize these materials for reuse. A new generation of machines is available, delivering more speed and efficiency than ever. These machines range from two-story-tall shredders that can process a diverse range of plastics down to granulators the size of washing machines that convert scrap from a single injection molding machine into fine plastic regrind for pelletizing in a closed-loop system.
For almost everyone seeking to enter the market and/or ramp up capacity, a compelling case can be made for buying, refurbishing and repurposing used machines. Whether new or used, high-volume or bench-top, none of these machines can operate at peak efficiency or profitability over the long run without knives optimized for the machine and the application.

Knives: From A to Z
Fisher Barton’s Zenith Cutter Division, based in Loves Park, Illinois, first began to apply its industrial knives expertise to the challenges of processing plastics in 1985. Since then, we have become a leading manufacturer of a complete system of granulator knives, shredder blocks, pelletizer knives and screens for the industry’s leading recycling machine original equipment manufacturers (OEMs) as well as a leading maintenance, repair and operations source for knife replacement, regrinds, repairs and service for the fast-growing marketplace of recycling companies.
In the world of plastics recycling, one size does not fit all, and materials range from the most common and easily recycled PET used in beverage bottles and high-density polyethylene to polyvinyl chloride, low-density polyethylene, acrylonitrile butadiene styrene and others.
We cover the complete range of sizes, capacities and material types for shredders producing tons of ground plastic per hour to the precision knives and screens needed for fine granulation, with more than 30,000 different knives in our database matching the specifications required by the vast majority of new machine makes and models, as well as those of many legacy machines dating back some 30 years.

A cut above
But that’s not nearly enough. Today, we find that an increasing number of applications can’t be adequately addressed with a simple, off-the-shelf standard solution. Customization and innovation are requirements in a plastics recycling landscape that’s becoming more challenging than ever.
Through careful analysis of the customer’s application, machine type and capabilities, suppliers like Zenith Cutter can optimize a knife solution based on the geometry of its cutting edge; the application of advanced heat treatment and finish grinding resources; and the ideal material, whether high-chromium tool steel, high-speed steel, stainless, powder metallurgy, carbide tipped or coated. The result is a knife that performs as well as or better than the original equipment and delivers longer tool life, greater throughput and requires less downtime for resharpening or replacement.
Some suppliers are experts at reverse engineering knives for older machines. For instance, our knowledge base and the resources we have in-house and those of our parent company, Fisher Barton of Watertown, Wisconsin, can give us an edge for the many recycling companies ramping up with used machines to meet new plastic recycling mandates and ever-growing volumes of plastics material. Matching knife to machine is important but also difficult. Often, the OEM of an older machine doesn’t have the records or provide the support, and in almost every case, the machine is repurposed for a completely new set of plastics recycling challenges. A recycling company trying to apply an off-the-shelf knife product thinking it’s “good enough” could learn quickly that the machine is underperforming.
Consider the importance of equipping a granulator with the correct rotor and bed knives. Granulating is a critical step in reducing plastics to predefined sizes. Granulators use sets of rotating and fixed knives that are precisely sized and positioned to create a gap for the material to be granulated. The material passes through this gap between the rotating knife and the fixed knife and is cut to the desired size. For thin-walled PET bottles, the gap could be as little as 0.002 inches, and the gap is wider for thicker material. However, when the knives aren’t precise and uniform, the gap can vary in width, creating inconsistent cuts and tool wear.
Additionally, the cutting edge geometry and knife material play an important role. Selecting the right bevel option for the rotating knife, for example, based on plastic wall thickness, material type, feed rate and machine size is of critical importance. A reverse bevel geometry, for example, is ideal for dense materials and high volumes. A single keen edge produces a clean cut but is better suited for thinner-walled materials.
Downstream, it’s imperative the screens used are sized correctly and designed for extreme wear. We offer 1,000 different screen sizes for all models of granulators and shredders.
In search of the totally new
Finding and applying knives that fit perfectly into a customer’s operations and can improve used and even new machine performance is a process.
In addition to extensive engineering, research and development and manufacturing resources, we draw heavily on the resources that our parent company offers to improve on the design and functionality of our knives. The Fisher Barton Technology Center, for example, is fundamental in our ability to understand and apply the materials and coatings needed to improve our knives. Is a blade experiencing premature wear or failure? We can use a Zeiss scanning electron microscope to perform an analysis of fracture surfaces and microstructures, or we can use a Keyence laser scanning microscope to analyze the material in 3D right down to 1 nanometer in resolution. Abrasion, erosion and fatigue testing can be performed with the ultimate goal of finding and applying the ideal alloys, coatings and processes.
Zenith Cutter and Fisher Barton also collaborated to develop the patented Shredzilla, a carbide-capped shredder block for use in most 40-millimeter shredders. Compared with solid carbide cutters, this shredder block offers similar tool life but at a 30 percent cost reduction. It also lasts two to five times longer than solid steel knives and requires 50 to 60 percent less downtime for blade changes.
Reduce, reuse and recycle are key drivers in plastic production and at the local, state and federal government levels. Recyclers are ramping up to meet enormous demand, extend plastics’ life cycle and divert waste from the landfill and environment. Knives cut plastic down to size and play an important role in making these recycling efforts more efficient, so take your time to select the right ones for your operation.
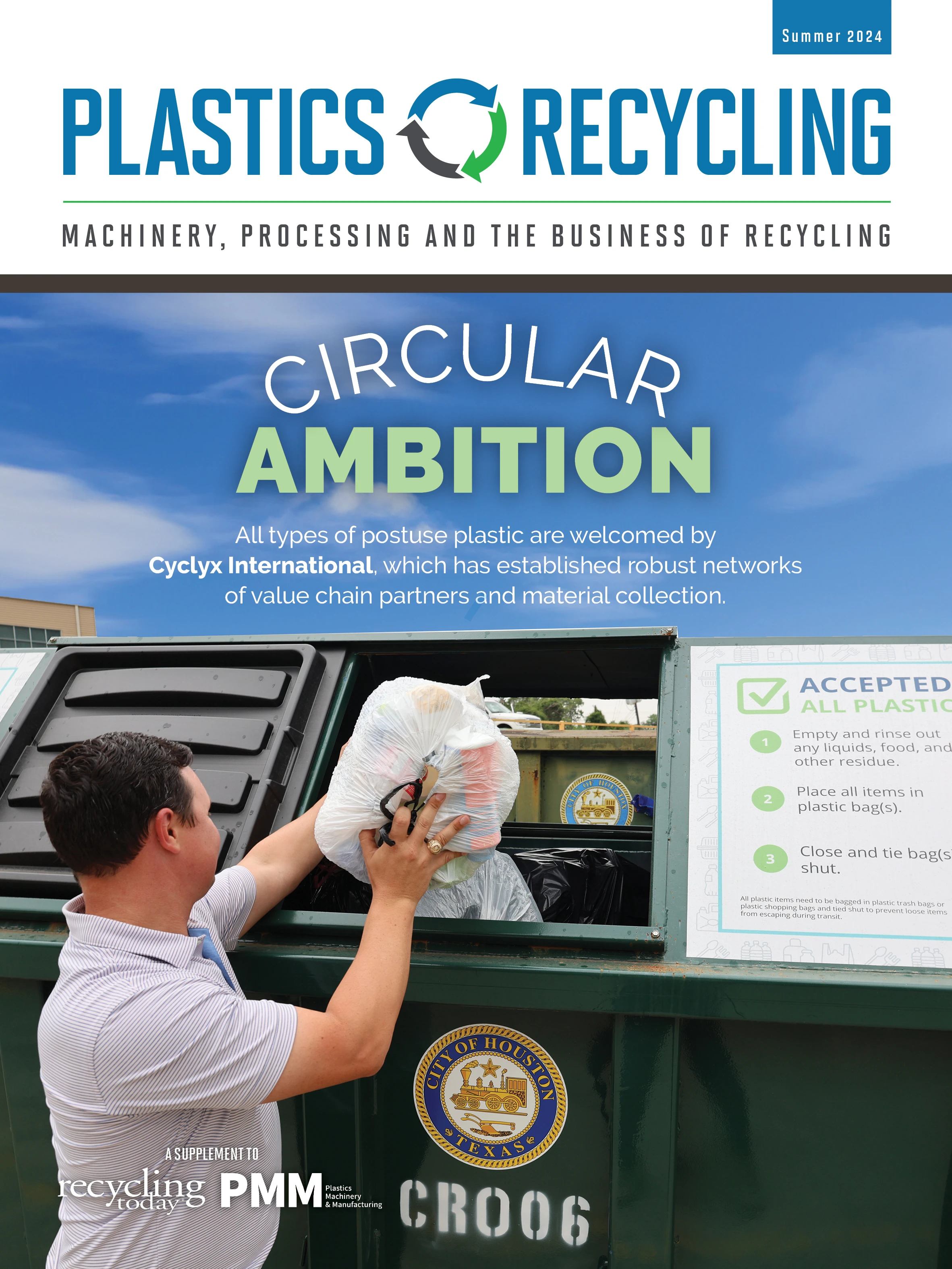
Explore the Summer 2024 Plastics Recycling Issue
Check out more from this issue and find your next story to read.
Latest from Recycling Today
- Athens Services terminates contract with San Marino, California
- Partners develop specialty response vehicles for LIB fires
- Sonoco cites OCC shortage for price hike in Europe
- British Steel mill’s future up in the air
- Tomra applies GAINnext AI technology to upgrade wrought aluminum scrap
- Redwood Materials partners with Isuzu Commercial Truck
- The push for more supply
- ReMA PSI Chapter adds 7 members