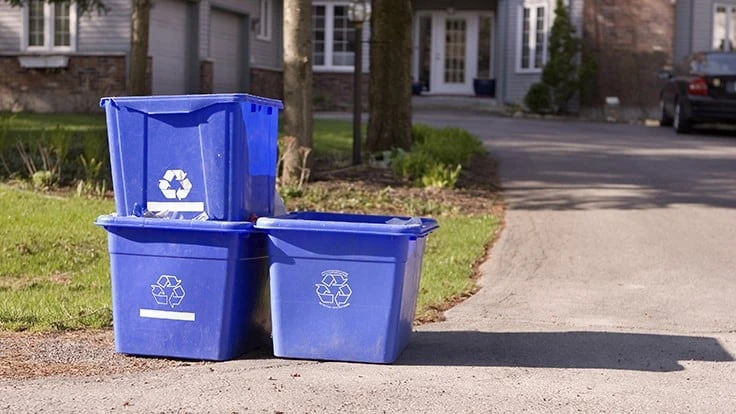
Although many communities have worked to cut contamination in recent years, this year’s MRF Summit hosted by the Solid Waste Association of North America (SWANA) and the Institute of Scrap Recycling Industries (ISRI) gave focus to the major implications it still causes for material recovery facilities (MRFs) and recycling programs across the U.S.
Featuring speakers Pete Keller, vice president of recycling and sustainability for Republic Services; Kanika Greenlee, environmental programs director for the Atlanta Department of Public Works; and Adam Ortiz, director of the Department of Environmental Protection in Montgomery County, Maryland, the session, titled “Cut Contamination at the Curbside and in the MRF,” covered how these municipal and industry leaders successfully tackled recycling contamination.
Keller said he believes contamination has become an increasingly large challenge for material recovery facilities (MRFs) over the last 15 years.
“[At Republic,] we’ve done quite a bit of customer insight work, and what we’ve found is that a lot of our customers are putting more things in the [recycling] bin because they believe they’re doing a better job for the environment,” he said. “We get a lot of things that we shouldn’t get, and we get a lot of things that clearly aren’t recyclables. … So, hopefully, through education and outreach, we can break through to some of those [people].”
To help encourage proper recycling habits, Republic launched a campaign called “Recycling Simplified” in 2018. Through the campaign, the company initially began performing route audits, invested in public relations and media opportunities, and created targeted digital and social campaigns in five metropolitan service areas (MSAs), eventually growing to eleven MSAs in 2020.
“We saw pretty significant improvements in those markets where we’ve gone out and made these investments. So, that’s something that we’re going to continue to do in the future,” Keller said. “Public outreach and communication are not an event, [they are] something that you need to invest in overtime.”
Ortiz agreed, mentioning that the recycling industry in the U.S. has been on “cruise control” for decades.
“We have not really stepped up our game in a lot of ways in what we expect [of] manufacturers and what they’re producing. In our facilities, I think a lot of us, myself included, have been slow to embrace technology, and we also haven’t expected enough of our residents,” he said.
Changing behaviors
In Atlanta, the city launched a three-year $4 million program with The Recycling Partnership to drastically increase the capture of more quality recyclable items. The program was anchored by the pilot cart tagging education campaign “Feet on the Street,” which was first introduced in 2017.
“[During the pilot,] we went to each household for four consecutive weeks and during that [period] we had a team of eight taggers and one manager, and they would go out before our trucks went out,” Greenlee said. “They would tip the lid of the cart, check to see if any of our top six contaminants were in the cart, and if so, they were left curbside communication in the form of an ‘Oops’ tag, and we did not service the cart until the resident fixed those contaminated items.”
Greenlee said the program found that rejecting the carts proved to be very helpful, with many residents appreciating the curbside feedback.
Montgomery County, Maryland, which has a service area of roughly 220,000 homes, adopted a similar program for its residents. Ortiz said the county first targeted two pilot areas of approximately 26,000 homes, where inspectors would go out every morning to check lids and tag them if there was any visible contamination.
“We did [that pilot] for six weeks and what we found was that we started with a contamination rate of about 40 percent, and by week six we were able to get it down to 20 percent,” he said. “Because of the success of that pilot, we were able to go to our budget folks and get more positions approved so we were able to do that countywide.”
Atlanta also experienced a drastic reduction in contamination, with some areas getting down to single-digit contamination rates.
“For us, we saw a 20 percent reduction in contamination,” Greenlee said. “In addition to that, we had a capture rate study done and saw a 9 percent increase in good recyclable materials.” She says that the city is currently working on a new contract with it’s MRF partner to better measure these contamination rates.
Measuring contamination
Keller said Republic measures contamination in two ways: a system audit or an audit of inbound materials.
“The primary mode is what we call a floor source, and there’s good methodology on how to get representative samples from each load, and how to measure what’s in that material,” he said. “The other mode, which is a system audit, is where you would take let’s say 40 tons of customer material and clear out all your loose inventory and bale inventory, and run that 40 tons, then measure everything that you produce.”
Ortiz, on the other hand, said Montgomery County usually performs waste sorts every three to five years, but after seeing the savings potential of the pilot program began performing them once a week.
“Once people put [their recyclables] at the curb, they forget about it,” he said. “And that’s in a lot of ways why our system is struggling and a little underwater right now. So, we need to step up, but we also need to ask others to step up that are contributing to this overwhelming amount of nuisance plastics and contamination that we’re having [webinars] like this about.”
He added that investing in recycling infrastructure, such as robotics and optical sorters, will aid in pushing the industry forward.
“In the last three to four years, I would say optical scanning technology, as related to fiber-based materials, has come a really long way,” Keller said. “Historically, we had used optics to separate resins, but now our current experience is that its state-of-the-art for fiber quality control, so that’s an area we continue to invest in.”
He added, “Because of our scope and scale, we think a one percent improvement [in contamination] is worth about $5 million a year. So, that’s something we’re going to continue to get after."
Latest from Recycling Today
- Pacific Steel selects Danieli as EAF equipment supplier
- Aluminum Association seeks certainty on tariffs
- EPA plans to revisit numerous environmental, climate regulations
- Scientists use air, inexpensive catalyst to break down plastic
- Miami-Dade Innovation Authority launches fifth Public Innovation Challenge
- EVSX installation supported by Call2Recycle Canada
- Wendt commissions shredding plant, nonferrous system at Island Recycling
- Fornnax wins Green Innovation of the Year award