

Auto shredder residue (ASR), fines from shredded electrical and electronic equipment and waste incinerator bottom ash all have one thing in common: They contain valuable metals that are worth recovering. Therefore, processing these fine materials is of high importance.
BHS-Sonthofen of Sonthofen, Germany, has further optimized its standard process for fines processing by making significant investments in research and development. This standard process consists of presorting and several shredding stages using a rotor impact mill, which can accomplish multiple challenging processing steps at once. These steps are followed by sorting via screens as well as by magnetic and eddy current separation. Each plant is individually adapted to the customer’s requirements given the large variance of the input material.
Electrical scrap and ASR, as well as incinerator bottom ash and other residual fractions, all contain a wealth of valuable metals. However, recovering these metals individually is a real challenge. The composites found in the input materials, as well as the structure of the individual components, make separating and sorting more difficult. For instance, copper from shredded cables is shielded by insulating material. Freeing the cables from their sheathings is just one important aspect of recovering copper and aluminum as well as gold and platinum. To sort the exposed wires and separate them from the rest of the metal fraction on the separating table, they must be shaped into balls. This is the only way to recover pure copper.
Another challenge in processing these fractions is the wide variance in infeed material. Even with seemingly identical input material, the differences are striking. For example, the material components in ASR vary significantly depending on the class of the shredded end-of-life vehicles and the year they were built, as well as the proportion of additional electronics they contain. When light and heavy fractions from the shredder or cable residues are recycled, the material must be prepared in such a way that the metals are ready for sale at the end of the process.
A custom approach
Such a wide variety of materials requires a process that ensures the highest yield of high-quality metals through continuous development. We invest considerable time in research and development to optimize the processing of metal-containing fines measuring 25 millimeters (less than 1 inch) or smaller. As a result, not only is a wider range of infeed materials possible but so is higher throughput with lower operating costs.
We offer an established standard process for recycling metal-containing residues. However, as Jörg Ehrich from the Process Development department at BHS-Sonthofen says, “Here, ‘standard’ almost has to be put in quotation marks. The core components for our recycling process for ASR and other fractions containing metal are set. However, we adapt the process in great detail together with the customer according to their individual requirements and are able to modularly enhance the structure of the process. This is a crucial step because I have yet to experience two customers coming to us with a truly identical input material. We use our tests to make sure that the adjustments actually fit the input material’s characteristics.”
The tests with original feed material, which Ehrich’s team run together with customers at the Sonthofen Test Center, form the basis for the recommended process. The tests and their results also are used for further process optimization as a foundation for detailed plant engineering and an individual profitability calculation.
Repeat shredding, reduce wear
The first step in the process involves an initial presorting of the input material, in which screens and a zigzag sifter sort out every particle greater than 25 millimeters, or 1 inch, in size, as well as dust. This step reduces wear on the equipment and makes the process run more smoothly.

The most important step is after this initial presorting—using the RPMX rotor impact mill. Unique to its class, this high-performance shredder with a vertical shaft ensures the feed material is subjected to the optimum level of stress, thanks to its unique impeller rotor and special anvil ring. The high circumferential speed of the rotor generates centrifugal forces. At the same time, the shredding tools cause impact and shear forces, which result in high energy input into the feed material. A rotor cover plate also helps direct the material from above into a narrow gap between the ring armor and the impact hammers. Therefore, the entire height of the milling gap is used for the crushing process, ensuring longer dwell time and more stress on the input material. An intensive ball-shaping effect is created between the horseshoe-shaped hammers and ring armor, which sets the stage for subsequent separation and sorting of the nonferrous metals and other materials.
According to the desired result, the input material is processed in the rotor impact mill until it is small enough to exit the machine through the gap.
The RPMX works selectively by crushing and pulverizing mineral and brittle particles that were not removed from the feed material during presorting, breaking down composite materials and metals. Rubber and plastic components also pass through the mill but remain largely intact—the machine merely detaches them from other materials so they can be removed.
However, to be able to sort valuable components, it is crucial the rotor impact mill shapes ductile materials, including pliable metals such as copper and aluminum, into balls. This is the only way to cleanly separate nonferrous metals from other materials afterward. In the standard process, each batch passes through the mill two to three times. Light material and dust are separated and discharged before each round of shredding to avoid unnecessary stress on the machine.
Shredded, shaped for sorting
The final shredding step is followed by sorting the processed material. In this part, the material runs over a hopper onto a screening machine, which sorts it into different fractions depending on how they are to be further processed. The individual fractions are separated into the categories “heavy” (all metals and metal mixtures) and “light” (materials such as plastics and rubber).
Overbelt magnets separate the heavy fraction into magnetic and nonmagnetic fractions. The latter undergoes an additional separation step. An eddy current separator sorts the fractions into heavy metals, such as copper, gold and silver, and light metals, such as aluminum.
“The material can be perfectly sorted during eddy current separation due to the fact that the RPMX has already shaped all the soft metals into balls, and the hard metal parts are well-separated,” Ehrich says.
The sorted metal concentrates are immediately ready for sale.
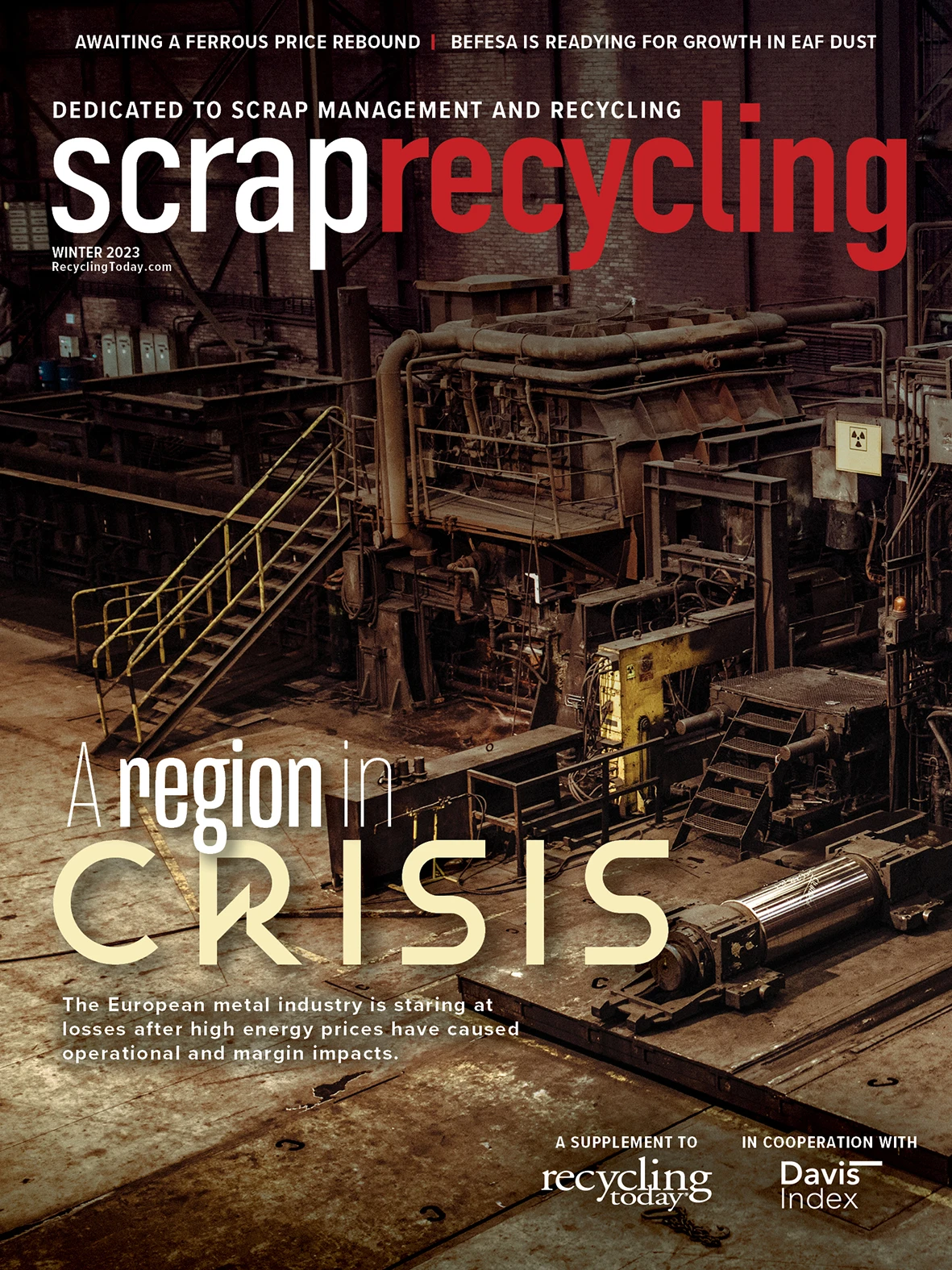
Explore the Winter 2023 Scrap Recycling Issue
Check out more from this issue and find your next story to read.
Latest from Recycling Today
- Athens Services terminates contract with San Marino, California
- Partners develop specialty response vehicles for LIB fires
- Sonoco cites OCC shortage for price hike in Europe
- British Steel mill’s future up in the air
- Tomra applies GAINnext AI technology to upgrade wrought aluminum scrap
- Redwood Materials partners with Isuzu Commercial Truck
- The push for more supply
- ReMA PSI Chapter adds 7 members