While making recycled aggregate products out of demolition debris is common among C&D
recyclers, the approach varies, as does the equipment used. Recyclers must weigh a variety of economic and environmental factors to arrive at the best approach for the job in question. In some cases, processing material on site with a mobile or portable crusher makes the most sense. In others, it may be best to transport the material to a designated C&D recycling facility for processing with a stationary crushing plant.
Yet, for similar economic and environmental reasons, having a designated C&D recycling yard does not exclude the use of mobile or portable units. Therefore, how does a C&D recycler determine the best approach for his business?
A number of factors, including job size and location, hauling costs, environmental and residential impacts and local regulations governing the disposal of C&D debris, come into play when determining whether to process material on the jobsite or to haul it to a designated processing yard.
Recyclers should also consider whether the resulting products can be used at or sold from the jobsite. "If so, then you turn what would be a cost into a benefit," Jim Schreiner of Telsmith, Mequon, Wisc., says. "If you can’t use or sell the material, the next question is, can you reduce the hauling and/or dump costs by doing some processing on site? Frequently the number of truck hauls can be reduced by doing some crushing, and dump fees can be reduced or eliminated by cleaning the material," he adds.
Apart from these more obvious considerations, the management team for Universal Engineering Corp., Cedar Rapids, Iowa, says determining a crushing system’s degree of mobility also depends on federal, state and local government approval procedures; per-job and annual erection and dismantling costs; and the equipment available to feed the plant. Dan Ferguson, CEO; Tom Werning, CFO; Gerry Mangrich, sales manager; Lou Winchip, chief engineer; Pat Geraghty, field service and quality control; and Scott Ferguson, sales coordinator, comprise Universal Engineering’s management team.
GOVERNING FACTORS
"The preparation of material is integral to the success of the operation," Ron Denny, recycling systems sales manager for Grasan, Mansfield, Ohio, says. "If they have to recycle on site because of rules, regulations or stipulations, then the crusher needs to be portable in order to get on and off the site."
Denny continues, "On the other hand, if it needs to be transported to a central location because of either dust, noise or contamination on the site, certainly stationary equipment is a positive there, because you can handle greater amounts of material and make more spec products."
In regard to permitting, stationary plants are less popular with recyclers than portable plants, Jay Giltz of Eagle Crusher Co., Galion, Ohio, says, adding that 95 percent of the plants Eagle sells are portable.
"If it’s portable and it’s under 150 tons an hour, then there are no federal regulations on the unit," Glitz says.
A general goal of portable crushing systems, according to Universal Engineering, is getting the highest capacity available while retaining portability and efficiency in set up and tear down, which maximizes productivity and uptime.
Some large C&D recyclers, however, may best be served by a combination of crushing equipment.
"I’ve found that most large sites, both waste management and rock and quarry, now are dual action, in a sense," Paul Van Klaveren, international marketing director for Crushtek, Norcross, Ga., says. "They will have a stationary plant that processes large amounts of whatever product it is they are processing and, in addition to that, they will carry mobile, or track-mounted, units within the yard itself," he says. The mobile crusher, which varies from a portable crusher in that it is mounted on tracks rather than on wheels, is then moved where it’s needed within the yard to preprocess material before it goes to the stationary unit.
"Track-mounted crushers seem to be more popular because contractors can move them around easily," Jim Lincoln of Kolberg-Pioneer, Yankton, S.D., says. "You just pull them in on a trailer, drive them off and start crushing." Portable crushers, on the other hand, have to be cribbed, which involves the perpendicular layout of cribs or timbers that help to support the crusher.
Whether a recycler chooses a portable, mobile or stationary unit, power should not be an issue.
POTENT PORTABLES
"Over the last decade, the industry has developed new crushers and new plants that put more crushing capability onto portable plants," Schreiner says. "There has also been a lot of development in portability, reducing mobilization costs."
Jock Voelzke of Construction Equipment Co. (CEC), Tualatin, Ore., also credits technological advances with increasing the ability of crushing equipment. "As technology has grown, we have found ways to put larger and better crushers on portable plants."
Grasan’s Denny also finds that mobile and portable crushers have grown in production capabilities. "Portable and track- mounted equipment has greater ability than it did before. It’s more sophisticated," he says.
According to Universal Engineering, new technology and crusher designs have allowed manufacturers to offer more cost effective, higher production systems in both stationary and portable applications.
However, Schreiner says that crushing plants with higher production tend to be less mobile. "The reason is that you made trade-offs when you emphasize portability," he says.
"When recycling concrete, it is important to have good transitions from the feeder into the crusher, good clearance under the crusher for a transition onto a belt and a good magnet setup to allow it to function properly," Schreiner says. "These are all areas that are typically compromised to achieve greater mobility and lower mobilization costs.
"The net effect is that the crusher size is not the limiting factor for the day’s production," he continues, "rather, the time spent dealing with plug-ups and torn belts reduces the day’s production."
COMPANY SEEKS DIALOGUE WITH COMMUNITY |
Granite Construction, based in Watsonville, Calif., has proposed a 333-acre quarry on grazing land at Hadley Ranch, four miles northeast of Gonzales, Calif. The site would include an aggregate processing facility, concrete/asphalt recycling facility, hot-mix asphalt plant and administration complex. According to a report in The Californian, the final environmental-impact report (EIR) for the project was completed in late October. Granite applied for the EIR in November of 2001. Mike Novo, planning and building services manager for Monterey County’s Building and Inspection Department, told the paper, "We are asking the Planning Commission if they want a field trip Nov. 5, and we have tentatively scheduled a public hearing Nov. 12." Residents in the area are concerned about the noise and dust originating from the facility. Steve Grace, Granite’s land resource manager, told The Californian, "It is definitely in our interest to make this work for everybody." Granite selected the site with potential noise concerns in mind, Grace added. "We were very sensitive to that. We had our noise guys look at it and they determined it not to be an impact," Grace told the paper. According to The Californian, Granite would constantly water down the plant and pave the roads to control dust. Grace said noise baffling and insulation combined with a 1,500-foot-high ridge would separate the plant from the canyon, reducing noise levels. "The other thing we’ve advocated is a community-advisory group to work with us that is made up of people in the area," Grace said. "We want to make this work for them." |
CALCULATING PRODUCTION
Production rates for crushers vary depending on the material being processed and the resulting product. "If you are just doing size reduction, you can do a lot more than if you are trying to make a spec product," Lincoln says. "If you have to have a certain size, let’s say 3/8-inch minus, your tonnage will go down because you’re crushing it more often."
Van Klaveren says production is lower when processing hard rock, such as bluestone, because of the density of the end product. However, he says rates increase when processing concrete or asphalt.
Contaminants, such as rebar, also affect production rates. "A highly mobile plant that may achieve 2,000 tons per day in clean material may only get 800 tons per day on some jobs," Schreiner says. "Again, the more mobile a plant, the more it is impacted by contaminants."
Schreiner says the trade off is that the more mobile plant can mobilize for a small job in the range of 10,000 tons, while the less mobile plant may need to process 30,000 tons before mobilization is cost effective.
Eagle’s Giltz says the typical production rate for portable crushers range from 150 to 300 tons per hour, adding that the company’s largest portable plant easily processes 300 tons per hour of 1.5-inch minus.
"Typically, portable equipment is used in the up to 250-ton-per-hour range," Denny says. "Over that, you need to make some special arrangements for feeding and taking material away. That’s because over 250 tons an hour is a lot of material to handle with ordinary contractor-sized equipment," he says.
Space is often limited when crushing on-site; therefore, support equipment may be limited in number and smaller in scale.
"Typically, portable units are fed with small loaders and backhoes or excavators," Denny says. "On the other hand, stationary units are normally fed with large loaders or trucks. Therefore, the support equipment is relative to production as well as the crushing equipment."
Denny continues, "If you are going to maintain consistent production for an eight-hour day, and you’re equipment has the capability of 300 or 400 tons per hour, then you’re going to need to have support equipment—loaders, personnel, excavators and trucks—that can handle that volume of material."
Universal Engineering also finds that mobile and portable plants are most often fed with equipment commonly associated with smaller construction sites, such as excavators, backhoes and small front-end loaders. However, recyclers will use large front-end loaders or truck dump systems to load material into a high-capacity hopper fitted with a hydraulic breaker to feed high capacity stationary, Universal Engineering says.
In addition, portable and mobile crushers generally have less elaborate post-crusher conveyor systems in light of space constraints.
CONVEYING CONCERNS
Giltz says stationary crushing plants require a lot of area and can accommodate elaborate conveyor systems, a luxury not often associated with on-site crushing using mobile or portable units.
Kolberg-Pioneer’s Lincoln says the goal at dedicated C&D crushing sites is to establish stockpiles of aggregate. "If you are just using a stand-alone, track-mounted crusher, it’s only going to be able to pile material about 15-feet high, then you have to move it again," he says. "Whereas, a stationary system can have huge conveyors and make stockpiles, 20, 30, 40-feet tall."
"We’ll build a radial stacker up to 150 feet, typically, which creates a significant stockpile of material," Voelzke says of CEC. "But there are those stationary plants that want two or three times that, and that is where you see the elaborate conveyor systems."
The length and the radius at which the conveyor turns regulates the particular position of each finished product, Denny says.
According to Universal Engineering, stationary plants’ elaborate conveying systems allow the recycler to produce several different products at lower transport costs because they do not need trucks to haul material from the crusher to the appropriate stockpile. However, the Universal team says on-site crushing typically requires fewer variations in finished material; therefore, portable plants are designed to be set up quickly and to produce one to three product variations.
"The more elaborate conveying systems can offer several cost/efficiency benefits that are difficult for highly portable operations because they mean extra hauls every time you mobilize," Schreiner says. "Some of the goals of these conveying systems are more elaborate stacking systems so product handling and segregation is reduced; open transfer points and chutes to minimize plugging; and magnets located in optimum locations to allow for best function and efficient handling of steel." Schreiner adds that some stationary plants even incorporate picking stations.
"We sell a lot of all-on-one-chassis plants and 50-foot stackers because, a lot of times, that is all the area that they have," Giltz says of C&D recyclers processing materials on-site.
While the post-crusher conveying system of portable or mobile crushers may not be elaborate, Van Klaveren says screening systems can be. "The technology is available to separate, divide and re-crush, it’s just a matter of fitting the needs of the consumer. You have just as many options with mobile as with stationary," he says. To achieve a variety of aggregate sizes, Van Klavern suggests that on-site recyclers can go from a jaw crusher, to an impactor, to a screen that divides the material into three different piles based on size. "Or you can close circuit and run it again."
Similarly, a Universal Engineering customer recycling roadbed in 5-mile long interstate sites uses a four-plant portable crushing system, eliminating the need for 11 trucks and the costs associated with operating those trucks, according to the company.
Regardless of a unit’s mobility, crushing plants have to address the same concerns and potential objections concerning dust and noise, though portable equipment doesn’t qualify for the same scrutiny because it is a moveable piece of equipment and not a permanent part of a work site, Denny says. "If that’s the case, the portable equipment can operate in situations where stationary equipment wouldn’t be able to," he says.
Denny adds that stationary equipment does have a higher degree of responsibility as far as regulations related to electrical wiring, water supplies, concrete footings and dust are concerned.
"I think the worst regulation issue that we come up against on a daily basis is unregulated dumping states," Van Klaveren says. "That to me has an effect on stationary and mobile crushing because if you are working within a state that has no regulations on dumping demolition waste, there’s no need for education, and there’s no need to think about the potential or the cost-savings benefit or the environment."
Universal Engineering says that contractors are faced with the challenge of meeting changing regulations concerning the disposal of construction debris. As contractors work to meet these challenges, combined with changes in technology and the public’s economic and environmental desire for renewed resources, the recycling industry will continue to grow, the company says.
"The ultimate goal of any contractor in the recycling industry is to raise productivity while maintaining good neighbor status within the community," according to Universal Engineering. "To achieve this goal, there must be a comprehensive exchange of experience and know-how between manufacturers, operators and local regulatory authorities."
The author is associate editor of Construction & Demolition Recycling magazine and can be contacted via e-mail at dtoto@cdrecycler.com.
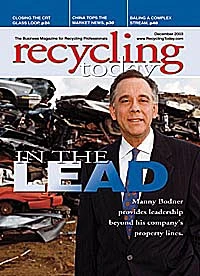
Explore the December 2003 Issue
Check out more from this issue and find your next story to read.
Latest from Recycling Today
- Astera runs into NIMBY concerns in Colorado
- ReMA opposes European efforts seeking export restrictions for recyclables
- Fresh Perspective: Raj Bagaria
- Saica announces plans for second US site
- Update: Novelis produces first aluminum coil made fully from recycled end-of-life automotive scrap
- Aimplas doubles online course offerings
- Radius to be acquired by Toyota subsidiary
- Algoma EAF to start in April