
Electronic recyclers have struggled to find sufficient end markets for the glass from cathode ray tubes (CRTs) from televisions and computer monitors because of its lead content. Kuusakoski Recycling, with U.S. headquarters in Plainfield, Illinois, experienced these struggles and has developed a new approach to processing the material, allowing it to be used in alternative applications.
Kuusakoski, based in Espoo, Finland, started as a metal recycling company in 1914. In 2009, the company expanded to the U.S. with the acquisition of a facility in Philadelphia to process electronic scrap. In 2015, Kuusakoski acquired Vintage Tech Recyclers, Romeoville, Illinois, which relocated its electronics recycling operations to that state. During that time, the company reached out to Peoria Disposal Co., (PDC) Peoria, Illinois, about its CRT glass issues.
“At the time, [Kuusakoski was] looking at a number of technologies: smelting and treatment and disposal of the glass,” Chris Coulter, chief operating officer of PDC, says. “We weren’t the only company that they looked at, but I think there was an immediate connection with them. When they started going down that path with us, they challenged us to do something and come up with a beneficial use for this material.”
That beneficial use, according to Coulter, was using the glass as alternative daily cover (ADC) at a PDC-owned landfill and as an aggregate material in landfill leachate recirculation or gas wells.
Keep ’em separated
Rich Hipp, CEO of Kuusakoski U.S., says the company built its glass processing factory in Peoria, as close as possible to PDC’s facility, to avoid high hauling costs.
Originally, crews at Kuusakoski manually separated the funnel glass, which contains the hazardous lead, from the panel glass, which is considered nonhazardous, before crushing the material before discovering that doing so could expose workers to hazards.
“When you [separate the glass], you’re opening up these tubes, vacuuming out phosphorous and potentially exposing employees,” Hipp says.
Now the CRTs, with their funnels and panels that are connected by a metal band, are sent to Kuusakoski’s crusher intact.
A special foam is sprayed on the CRTs as they travel on the conveyor belt toward the crusher, Hipp says, and then again when they are in the machine. It is designed to mitigate lead dust by wetting it down and making it stick to the glass. A magnet pulls the metal bands from the crushed glass, which are then shipped to a nearby scrap yard for additional processing.
When Kuusakoski first started crushing the whole CRTs, the company treated the crushed glass as if it were all funnel glass, but now Hipp says there is a safe way to separate the hazardous and nonhazardous glass after crushing.
Hipp says the company installed a separation line at its Peoria facility’s upper deck mezzanine. A light system allows the sorters to decipher between the panel glass and funnel glass.
“The reflection of the panel, which glows differently because of how thick it is, is very identifiable,” he says. “The thickness and the way it glistens in comparison to the funnel glass is so significant, [and] because [of that] it’s easy for the guys to pick.”
Employees

Hipp adds that every 10th load of clean glass that is collected is tested for lead concentration, “So we’re constantly monitoring how accurately these guys are picking the clean glass.”
Marc Artozqui, Kuusakoski’s Peoria facility manager, says an air filtration system was installed where the modified 32-hammer system by Andela Products, Richfield Springs, New York, crushes the glass.
“[The separation technology] was a technology that people were doubting from the beginning,” Hipp says. “What we’re most proud of is not only our employees who believe in this
The company attempts to keep airborne dust at bay by using a sweeper that lays a fine mist on the floor as it travels the plant.
“You can literally walk around our factory without any masks on,” Hipp says.
Kuusakoski also continually monitors the plant’s air for contaminants, he says.
Artozqui says 35,000 pounds of CRTs can be crushed per hour through this system on an average day. Of that 35,000 pounds, funnel glass accounts for 8,505 pounds and panel glass accounts for 19,845 pounds. According to Artozqui, hand sorters remove around 10,000 pounds of clean panel glass per hour from the stream. Once crushed, separated and put into roll-offs, PDC contains the lead in the funnel material through its treatment process.
Full circle
PDC treats the leaded glass Kuusakoski ships to the company using a mixing chamber
The mixing chamber uses propriety chemicals that he says, “bind up” the lead and other heavy metals to prevent leaching. The 6-inch glass shards are further broken down to 2 inches in size while tumbling through the chamber.
“It chemically converts the lead into a form with very low leachability and is fit for landfill,” Coulter says of the process.
Water is then added to the mixing unit, which ensures that the hazardous materials stay put. “It’s like making a cake,” Coulter describes. “When you have the ingredients, just simply mixing water into it brings it together. It brings it together and encapsulates it and prevents it from becoming mobile,” he says.
Once the glass is treated, it’s placed into large containers and tested to make sure the treatment was effective. Coulter says the testing process usually takes longer than the treatment process. While treatment takes 15 minutes, testing and getting results back take two to three days. The total process takes three to four days.
Currently, PDC treats 50,000 tons of Kuusakoski’s glass annually. Coulter says the company has the ability to process up to 100,000 tons of the material, but he doesn’t see Kuusakoski needing all of that capacity anytime soon. “It’s there if Kuusakoski and the market need it.”
Once treated, the funnel glass is placed in a mining cell at the Indian Creek Landfill, owned by PDC, to be reused later if markets develop. Before this was approved, PDC used the material as ADC at the same landfill. This option still remains.
“When you’re operating a landfill, you have to cover every day with 6 inches of clean soil,” Coulter says. “Instead of using up disposal capacity with clean soil, you’re now using it with waste—it saves landfill capacity and saves landfill life.”
PDC purchased the landfill in 2001 from LaFarge, with U.S. offices in Chicago, and reopened the site in 2004. An expansion went through in 2007. The landfill has three sections—one section was previously operated by LaFarge, and the other two units were never developed.
Nov. 13, 2012, PDC received approval from the Illinois Environmental Protection Agency (EPA) to use the glass as ADC. Jan. 26, 2015, it received approval to place the glass in retrievable storage in the landfill.
Additionally, Kuusakoski Glass has entered into an agreement with a North American smelter to accept CRT glass of an agreed specification for lead concentration on a limited basis.
Despite getting through the Illinois EPA’s rigorous permitting process, Coulter says there was “blowback” to the ADC method.
“One of the certification bodies, known as e-Stewards, as a last resort said they would accept the technology, but instead of using [the end material] as ADC to put it in a cell on its own to contain it and use it for recycling later on,” Coulter says. “Ultimately, we did pursue that and filed a petition with them. And with e-Stewards, Kuusakoski ultimately got their approval.”
E-Stewards is a certification program for electronics processors that was developed by the Basel Action Network (BAN), Seattle.
Owning and operating a landfill, Coulter says, involves building leachate recirculation wells and landfill gas wells, which require the use of
He adds, “The aggregate mixes up and speeds up the leachate process to create energy. This is going to be helpful for [Kuusakoski], their customers and us. We aren’t buying a product anymore, we’re using this instead.”
Giving the thumbs up
In early July, the Illinois EPA approved PDC’s application for using the panel glass as aggregate. Tazewell County approved the necessary permits April 26.
“A permit modification was needed for the landfill to accept it and to use it for recirculation,” Hipp says of the aggregate application. “You need a foolproof approach to make sure it can be approved for recycled aggregate. We had to go through multiple tests to make sure.”
Coulter says using the glass as ADC and aggregate material for landfill wells is still beneficial in the long run.
“It’s a really good thing,” he says. “You’re taking the material that’s really hard to recycle—glass is a hard material to
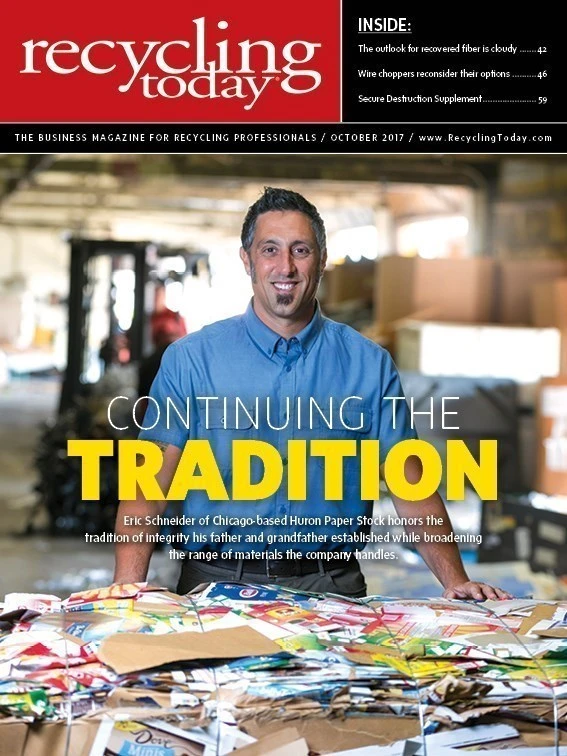
Explore the October 2017 Issue
Check out more from this issue and find your next story to read.
Latest from Recycling Today
- LME looks into sustainable metal pricing
- OnePlanet Solar Recycling closes $7M seed financing round
- AMCS launches AMCS Platform Spring 2025 update
- Cyclic Materials to build rare earth recycling facility in Mesa, Arizona
- Ecobat’s Seculene product earns recognition for flame-retardant properties
- IWS’ newest MRF is part of its broader strategy to modernize waste management infrastructure
- PCA reports profitable Q1
- British Steel mill subject of UK government intervention