
A scale used for buying and selling products based on weight is one big cash register. On large volume weighing, such as that done with in-motion scales, truck scales, bulk weighing and railroad scales, any scale calibration errors can result in hundreds of thousands of dollars—and sometimes into the millions—in losses. Calibration costs are mere pennies on the dollar considering the potential losses of an inaccurate scale.
The value of calibration
Scale calibration can be considered a risk management issue—the longer you go without verifying scale accuracy, the higher the risk. A simple calculation can help an owner or manager determine the specific loss risk of his or her operations: Take the number of weighments per year and multiply it by an error in pounds and then by the price per pound or per ton.
Take for example a business that weighs an average of 200 trucks. The business operates five days per week (261 days per year), with approximately 52,200 weighments per year. The scale is off by 300 pounds; unless drivers are complaining, it is unlikely that such a deviation would be noticed. If the product price is 5 cents per pound, the annual weigh error would be greater than $780,000.
Determining improper calibration
In many instances, few outward signs are visible when a scale needs calibrating. An owner might be made aware that the scale is not properly calibrated if the accountants have concerns about weekly totals, if the scale was hit and damaged, if users are complaining or if the scale will not zero out on the instrument readout when the load is removed. Sometimes, the operator/ weighmaster just has a general feeling that something is wrong.

For example, a driver may get a scale ticket saying the truck weighs 85,000 pounds, but had just left his own scale with a ticket at 84,000 pounds, signifying a difference between the two scales that has to be reconciled. Or, in some cases, a trucker’s shipment may be weighed three to six different times. He weighs in and gets the weight of the tractor, then picks up a trailer with goods and weighs out. Then he drops off his load at a site and is weighed in by the person buying the goods. To this we can add another weighment to determine if the truck is street legal or maybe one by the highway patrol for the total vehicle weight before making the delivery. If any of these totals are way off, the difference indicates a calibration issue.
Note that you can be aware of being out of calibration much earlier with digital scales than with analog ones.
Calibration frequency
Calibration frequency is really based on two factors: the requirements of law and the value of the commodity. In other words, how critical is the accuracy of the weighment?
Most operations typically calibrate their scales annually, just before the state certifier visits to verify the weights on a scale. However, this may not be often enough if the scale is being used intensively or if what is being weighed is especially critical. If being off by 20, 40 or 60 pounds makes a big difference to the bottom line, more frequent calibration should be considered. Monthly calibration may even be called for, with spot checks between calibrations.

Some scale companies even offer intermediate scale checks or spot checks rather than a full-blown calibration. The services, about half the cost of a full calibration, can be used to verify a few loads, alerting the owner or manager if the scale needs to be calibrated more frequently.
More frequent calibration is important for high-value commodities. For example, one should calibrate more often for copper than manure. More frequent calibration also is recommended for high-volume applications or if the weight is critical to a process (as in for batching, mixing or recipe work where the blend is important). More frequent calibration also may be called for if the scale is under a mixer or agitator with a lot of vibration, because that is more likely to drive the calibration out of bounds. So, while the law requires annual calibration, in many situations more frequent calibration would be prudent.
Proper calibration basics

To ensure proper weighing, it is essential that operations adopt a periodic routine calibration plan with a reputable calibration service company. An inspection always should be done in accordance with NIST (National Institute of Standards and Technology) “Handbook 44: Specifications, Tolerances and Other Technical Requirements for Weighing and Measuring Devices” regulations for commercial weighing applications. A simple drive over and a sticker will not suffice and could be a total waste of money and time.
Instead, work with a service provider to develop a service agreement to specify the months the scale will be inspected. Some companies offer preferential loyalty discounts on service rates. The larger companies also may provide full-service agreements that cover everything from calibration to repairs.
Using a truck scale as an example, the scale company should drive over the vehicle scale with a specialized test vehicle looking for repeatability. Then the calibration expert should unload a specialized certified weight cart that will travel over each section to ensure all sections weigh exactly the same. If a scale does not need calibration, the service provider will use NIST maintenance tolerances or better to assure that the scale meets all government regulations on calibration. If a calibration is required, the inspector will then use NIST acceptance tolerances that are specifically identified within the NIST “Handbook 44” regulations.
Once the scale passes repeatability tests and section test calibration, the scale technician will drop up to 25,000 pounds of certified test weights onto the scale for a final calibration test. The United States government regulates that a scale must be calibrated with 12.5 percent of the total capacity of the scale with certified test weight (a 200,000-pound scale multiplied by 12.5 percent equals 25,000 pounds). Certified test weights typically are calibrated by local weights and measures departments annually and are serialized and traceable to a national standard.
Scale operators always should ask their service providers to furnish them with:
- the service provider’s weights and measures license number;
- a copy of the certified test weight documentation for conformance and traceability;
- licensed technicians; and
- a written test report that covers section testing and overall calibration with “as found” and “as left” readings.
Peace of mind
A scale is a precision measuring device, built with delicate high-precision components. It can have silent failures that affect calibration without any warning or obvious indication. Be sure to routinely have your scales inspected and tested. To avoid problems, you may want to schedule regular service with an authorized scale calibration firm, based on the factors mentioned previously. Make sure you schedule an annual calibration just prior to state inspection by weights and measurements personnel. This will help you avoid the real risk of red tagging, when the state inspector says the scale is so far out of bounds that it cannot be used for business until it’s remedied.
Get curated news on YOUR industry.
Enter your email to receive our newsletters.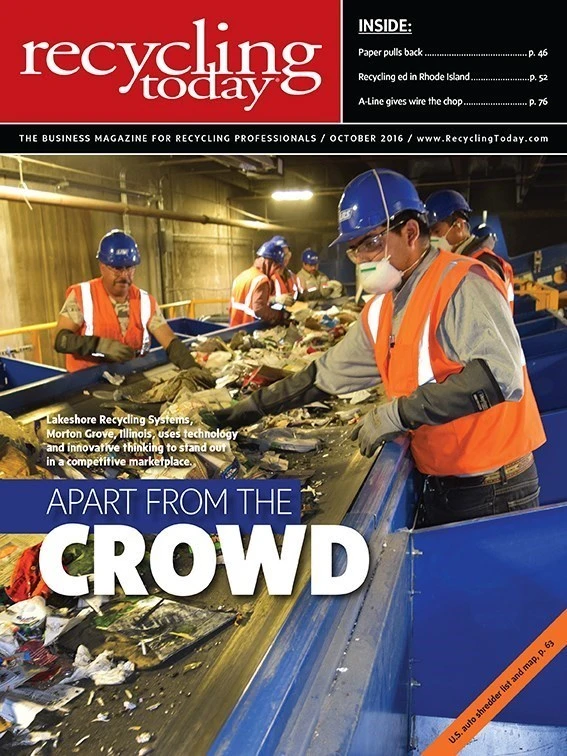
Explore the October 2016 Issue
Check out more from this issue and find your next story to read.
Latest from Recycling Today
- Li-Cycle reports 2024 financials
- PureCycle, Landbell Group working to advance PP recycling in Europe
- S&P Global launches mixed plastic scrap pricing for US, Europe
- Organizations call for coordination on product safety
- Circular Services acquires Waste Recycling Inc.
- Aqua Metals issues 2024 progress report
- e-Stewards, Bloom ESG release environmental benefits calculator
- RecycLiCo engages Fusion Projects to assist with facility site selection