
Who would have guessed a few years ago that the moribund steel industry would come to outshine many of the more vibrant industries of that time? In the eyes of the investment community at the time, the steel industry was no longer an icon of 1950s-era U.S. economic and industrial muscle, but an industry in the throes of collapse.
In the late 1990s and earlier this decade, nearly two dozen U.S.-based steel companies filed for bankruptcy protection in a relatively short span of time. Evaporating pricing power, the influx of cheaper overseas steel and high legacy costs were some of the reasons critics pointed to as they practically wrote off the domestic steel industry.
However, while many people were swept up in the euphoria of the hottest technology trends, the steel industry, both domestically and globally, has made quite a remarkable comeback. A plethora of acquisitions and mergers have shaken up the fragmented industry, leaving the industry with improved pricing power, according to some industry observers.
The doomsday forecast for the U.S. steel industry has now been replaced with greater optimism, as a more efficient U.S. steel industry is competing very well against overseas steel companies. But even with this more upbeat outlook, many industry observers say that about the best to hope for would be the continued operation of existing domestic steel mills.
NEW KID ON THE BLOCK. A possible sign of resurgence involves a company called SeverCorr and its plans to build a greenfield electric arc furnace steel mill in Mississippi. The company plans to capitalize on a technology that will allow it to compete for the more lucrative auto industry market. The company has said that its business model will give SeverCorr a major advantage against overseas competitors.
Several barriers could prove to be formidable challenges to a new steel industry entrant. However, for SeverCorr, which has long-time steel industry executive John Correnti as its president and CEO, these challenges are instead seen as great opportunities for a company nimble enough to not only survive, but to thrive in the current environment.
That current environment includes the state of the automotive industry, which SeverCorr hopes will buy a significant amount of its finished steel. Tough times are being predicted for Ford Motor Co. and General Motors. The companies recently have announced plant closures and thousands of layoffs.
However, Correnti, formerly CEO of Nucor Corp., Charlotte, N.C., says SeverCorr’s Columbus, Miss., mill will be close to a number of other large auto manufacturing plants, including those run by BMW, Toyota and Honda. In fact, the steel plant is located in a region of the country that is proximal to 14 different auto manufacturing plants that produce around 4 million vehicles per year, or roughly 25 percent of the passenger vehicles produced in the United States.
And an additional neighbor is also possible, as economic development officials in Mississippi and Lowndes County (where Columbus is located) are preparing an incentive package to offer to automakers seeking to build a new facility in North America.
The SeverCorr mini-mill is a joint venture between the management of SteelCorr LLC and the Russian steel company Severstal Group. In addition to Correnti, top officials at SteelCorr also have backgrounds in the steel industry with companies such as Nucor and Birmingham Steel.
Severstal already has a presence in the United States, having acquired Rouge Industries, a Michigan-based steel company, slightly more than two years ago.
The SeverCorr steel mill is slated to produce around 1.5 million tons per year of flat rolled steel. The company hopes to have the facility open by the end of 2007 and, Correnti says, expects from 15 percent to 20 percent of its output to be sold as an exterior steel product to the auto industry.
Traditionally, much of the steel used for external automobile parts comes from steel mills in the North and Midwest, so building a steel plant that could provide the automakers in the South with the same type of material at a sharply lower freight cost could give SeverCorr a major advantage.
However, one risk lies in the fact that the steel production method the SeverCorr mill will use has not yet been used in the United States for this purpose, so skeptics wonder whether the proposed steel mill can meet the quality specifications required of automobile steel.
Correnti says the company currently plans for roughly 20 percent of the mill’s output to go to the auto industry, with close to 85 percent of that material being used for exterior parts and the remainder going toward unexposed vehicle parts. The company’s additional customers will be in the building industry, oil refineries and other industries using flat rolled steel.
The mill, when fully operational, will require around 1.7 million tons of raw material per year. This could be a daunting task in today’s market, as China is soaking up a tremendous amount of ferrous scrap. Correnti seems nonplussed about the competition for material.
However, he notes that SeverCorr is also mindful of the need to diversify its raw materials beyond ferrous scrap. The EAF will also take in pig iron, hot briquetted iron and direct reduced iron that, Correnti says, will help keep the company from becoming too susceptible to the potential wild swings in ferrous scrap prices.
SeverCorr has opted to allocate the scrap procurement business to Jefferson Iron & Metal, an Alabama-based scrap recycling operation. While Correnti acknowledges that there are some larger scrap companies SeverCorr could have gone with, Jefferson, because of its location and understanding of the market in the South, gives the company an advantage, he says.
Working with Jefferson Iron & Metal should allow SeverCorr to strengthen its rapport with many smaller scrap yards in the South. This may be even more essential going forward, as global competition for raw material increases.
COMPETING WITH THE GIANTS. Concerns about China both soaking up raw materials and selling finished steel have been foremost within the international steel industry. For U.S. steelmakers, the threat that China holds is significant, forcing many to change the way they do business.
For Correnti, the threat that China poses in the long term is more hype than reality, and he cites lower freight costs as a potential advantage SeverCorr will have over its competitors in India or China. The company’s proximity to potential consumers and its access to affordable energy through the Tennessee Valley Authority also helps make up for its disproportionately high labor and environmental costs compared to Chinese and Indian steel companies.
However, Correnti cautions that while the mill’s location imparts some advantages, it doesn’t mean that the company will coast to profitability. "You have to build them economically and fast," Correnti says of new steel mill construction. "And, once they are built, they must operate efficiently," he adds.
To accomplish the first task, SeverCorr has already broken ground on the facility, which will measure roughly 1.7 million square feet, and has about 80 percent of its construction contracts in place. OAO Severstal Group, the Russian steel giant, is investing $200 million in the project, while GE Capital is expected to provide additional financing to get the facility built as quickly as possible.
A key point in operating efficiency inevitably falls to labor costs. At full capacity, the steel mill should be able to produce around 1.5 million tons of steel with around 450 employees, which should provide an impressive labor hours-to-tons produced ratio.
The process SeverCorr will use aims to leapfrog much of the technology presently in use at other domestic mini-mills. The plant will use a compact strip process (CSP) that was developed by German company SMS Demag. Nucor also worked on developing the process and uses a version of the CSP line at its Berkeley County, S.C., plant, which can refine steel for higher-quality products.
The plant will include an electric arc furnace, two ladle furnaces, a vacuum degasser and the downstream CSP plant comprised of a thin slab caster, a continuous furnace and a six-stand hot rolling mill. The mill will also include a cold rolling mill with a coupled five-stand tandem pickling line, a skin pass mill and a hot-dip galvanizing line.
What may generate the greatest amount of interest is the CSP plant, which uses the latest technology to produce auto body sheets and high-strength multi-phase steel for the automobile industry as well as ultra-fine hot strip that can replace cold strip in suitable applications. While some industry observers question whether the mill can effectively use the CSP method to maximum effect for exterior automobile steel, the 72-inch width of the steel that the company will produce gives SeverCorr a noteworthy advantage over other steel providers, according to Correnti.
THE ROLE OF THE STATE. While SeverCorr and Severstal, as well as their financial backers, have a significant stake in the success of this new steel mill, the state of Mississippi also has stepped up, offering a sizable amount of financing to ensure the success of the steel mill. A bill passed last year by the Mississippi House (HB 14) authorized the state to provide $60 million in loan guarantees to the company.
The money is part of an overall $95 million state-funded incentive package to assist SeverCorr in building the mill. The state is providing up to $25 million to help the company with site preparations and $10 million that will be used if the company encounters cost overruns during the construction of the project.
Looking forward, the global steel industry has been shaken up by more mergers. Mittal Steel, the largest steel company in the world, has made an unsolicited offer to acquire Arcelor Steel, the second largest steel company in the world. Meanwhile, Arcelor has only recently acquired Dofasco Steel. (See the "Steel Acquisitions Timeline" on the following two pages.)
While such mergers could bring economies of scale to the business of making steel, they could also assign pricing power to fewer companies. Nonetheless, Correnti says its Columbia location should give SeverCorr a better chance of success than other potential locations would.
Charles Bradford, an independent steel analyst, notes that one big advantage for SteelCorr and its SeverCorr project is the fact that Correnti, as well as a number of the company’s executives, have a long history of successfully running steel companies.
Bradford also says if SeverCorr is successful in producing the 72-inch steel bands, the company would have a major advantage over other steel companies, considering no other steel company in the United States is able to produce the 72-inch width, a size that the auto industry is considering adopting more widely.
The biggest question that Bradford has for the project is whether the company can complete the mill on or under budget. The cost to build many of these steel mills may easily top $1 billion, according to Bradford. While he notes that Correnti and his staff are "smart" guys, he says there will be some challenges in completing the project with the announced budget.
The author is senior and Internet editor of Recycling Today and can be contacted at dsandoval@gie.net.
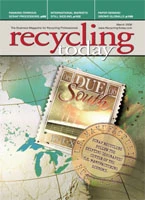
Explore the March 2006 Issue
Check out more from this issue and find your next story to read.
Latest from Recycling Today
- Radius experiences sixth consecutive quarterly loss
- US ferrous market exhibits upward pricing pressure: Davis Index
- Glass Packaging Institute applauds regulation change
- Engcon adds to Tiltorotator line
- Paper recycling is focus of two January webinars
- Disruption likely for material flows in mid-January
- Blue Whale Materials to expand Oklahoma lithium-ion battery recycling plant
- CARI names new president and CEO