
When Mark Loizeaux got the call to ask if his company, Controlled Demolition Inc. (CDI), could assist with the design, preparation and execution of a controlled demolition of the largest remaining span of the collapsed Francis Scott Key Bridge in the Baltimore Harbor, he didn’t think twice.
It was an emergency job that required him to pull men off other projects, but he immediately said yes.
“We’re based out of Baltimore, so this was a worldwide news event right in our backyard,” says Loizeaux, owner and president of CDI. “It was catastrophic. This is one of the biggest ports in the world.”
After midnight March 26, the MV Dali container vessel, based out of Singapore, lost power while traveling south on the Patapsco River out of Baltimore Harbor. The starboard shoulder of the bow hit the southern channel pier of the Francis Scott Key Bridge before crashing into one of its support columns, causing the pier to collapse and a progressive failure of the 1.6-mile bridge’s entire truss, a continuous span that encompassed two 720-foot-wide approaches.
Tragically, six maintenance workers filling potholes on an overnight shift died in the collapse of the bridge, which resulted in the subsequent closure of one of the busiest ports in the U.S.
CDI was tasked with using explosives to break down a 600-ton span of bridge truss that landed on the cargo vessel’s bow. According to Associated Press reports, that truss effectively pinned the Dali, preventing it from being refloated and leaving the harbor.
Working on the water while removing marine structures requires greater expertise, experience and coordination than demolishing structures on land, Loizeaux says, and CDI has extensive experience in the demolition of suspension, arch, truss, girder and bascule bridge elements. CDI also is no stranger to high-profile demolition projects, having completed the demolition of the former Trump Plaza Hotel in Atlantic City, Three Rivers Stadium in Pittsburgh and the Landmark Hotel Casino in Las Vegas.
CDI’s crew first finished preparation work on the span of bridge truss elements to free the MV Dali for salvage, performing precision torch cutting on the main structural bridge elements for subsequent placement of explosives. This method allowed CDI to control how the trusses would break down, causing the steel structure to be thrust away from the Dali upon explosion. Team members worked with a structural engineer every time a cut was made, Loizeaux says.

“It’s challenging when you are on the water,” he continues. “We were working in this narrow section of the Patapsco River with waves created by passing vessels and by the wind. We were very limited in our working hours due to that.”
Still, the company worked as quickly as it could to complete demolition so the port could reopen. The bridge’s collapse had put an estimated 4,000 port employees out of work while affecting another 15,000 longshoremen, truckers and small business owners who rely on port activities for their livelihood.
The port officially reopened in mid-June after being shut down for 78 days.
“What happened that early morning of March 26 was horrific; what happened next was inspiring,” said U.S. Department of Transportation Secretary Pete Buttigieg at a reopening event in mid-June. “As of this week the channel is open, the ships are moving, the terminals are operating and this great American port is full steam ahead.”
Recycling Today spoke with Loizeaux about the demolition and subsequent recycling processes associated with the Francis Scott Key Bridge.
Recycling Today (RT): Who was in charge of responding to the bridge’s collapse?
Mark Loizeaux (ML): The city of Baltimore, the state of Maryland and the federal government immediately joined forces toward reopening the channel as quickly as possible under a Unified Command structure led by the U.S. Army Corps of Engineers.
The federal government assumed responsibility for clearing debris from the 1,200-foot-wide main channel while Skanska, [a New York-based construction company], was tasked with debris removal responsibilities outside the main channel. Resolve Marine of Fort Lauderdale, Florida, was retained by the ship’s owner and its operations company to remove debris that had fallen on the ship’s bow and to salvage the vessel.
RT: How did CDI get involved?
ML: Resolve Marine had worked with us before as an explosives contractor on the demolition of the Tappan Zee Bridge over the Hudson River in New York state. For this project, Resolve Marine retained CDI to design, perform preparations for and carry out explosives separation of the 600-foot-long southern portion of the channel-span truss from the bow of the Dali.
When the bridge fell, the bridge truss, pier cap and roadbed debris fell vertically onto the vessel’s bow. The continued motion of the ship caused the truss to twist, adding additional stored energy to the already compromised bridge truss system.
RT: What was the scope of the demolition project?
ML: CDI’s scope was to separate the truss from the ship, including preparatory preburning operations that would identify and then cope with the stored energy in the box configuration and other truss elements. These elements had flange thicknesses up to 4 inches thick, and they were to be severed with explosives. Strain gauges and other monitoring devices were installed to provide real-time readings on truss stability so that preburning could be paused as necessary to ensure CDI employee safety.
CDI’s goal was to provide a 60-foot-wide space between the vessel and the remaining truss, in the water while rolling as much of the truss as possible off of the bow of the Dali during the explosives’ initiation sequence. There were flammable materials in containers damaged by the bridge collapse, which necessitated cold cutting to prepare the shaped-charge locations where hot work couldn’t be safely performed.
Cold cutting could not be completed on all elements above the bow due to the energized truss elements, leading to a plan that would leave a small portion of the truss on the bow and other truss elements draped over the port side for postblast crane removal.
Preparatory burning was carefully monitored by CDI and structural engineers. The sequence, and nature, of preburning was changed several times after we observed twisting in the bridge elements during torch work.
RT: What were some of the challenges your team faced?
ML: Working out of crane baskets and 185-foot manlifts on a barge proved challenging on the water due to wave action, winds and poor weather, including strong winds and heavy rain that limited working hours. Even as they otherwise prepared to refloat the vessel, Resolve Marine provided marine platforms and equipment to support our operations to remove the truss from the Dali as quickly as was safely possible.
RT: What did the actual controlled demolition entail?
ML: A total of 162 pieces of linear-shaped charge explosives were placed at 52 locations, with a net explosives weight totaling 312.69 pounds of RDX [research department explosive] and PETN [pentaerythritol tetranitrate] explosives to create the separation of the truss and the vessel and to permit as much of the truss as possible to rotate off the vessel during the blast. The explosives were positioned on the bridge using rubber bands and secured with tie-wire.
Conveyor belt at-source protection was placed by CDI to control the flying of debris from the detonation of the explosive charges.
Once the Unified Command cleared the CDI-specified exclusion zone around the blast area, Resolve Marine turned on a water fire suppression system over the damaged containers at the bow to mitigate the risk of fire.
The charges were successfully detonated at 5 p.m. May 13.

RT: What about the 21-member MV Dali crew? Weren’t these people still on the ship at the time of the demolition work?
ML: The Dali crew was sheltered below decks at the stern of the vessel in a soundproofed area during the blast, while Resolve Marine and CDI employees positioned themselves at the stern of the vessel during the explosives detonation.
The nonelectric-initiated blast had an integral 9.6-millisecond delay, directing the pressure bar away from the vessel and the windows in the bridge, which was the most sensitive element to remain on the vessel.
RT: What was the outcome?
ML: Everything went to plan, and everything went exactly on schedule. The separation was completed, and that portion of the truss intended to roll off of the bow did so exactly per plan. There was no reported damage to the vessel or its cargo, and no fire was initiated on the vessel as a result of CDI’s operations.
It was very, very challenging, but we had a great crew of wonderful guys, and everything went according to plan.
RT: Officials estimated the total amount of wreckage at 50,000 tons of steel and concrete. Are those materials being recycled?
ML: We were dealing with about 970,000 pounds of truss, so this was a huge recycling project. Key Bridge Response Unified Command was picking up all of the steel from the bridge using cranes positioned around the ship so it could be salvaged and recycled.
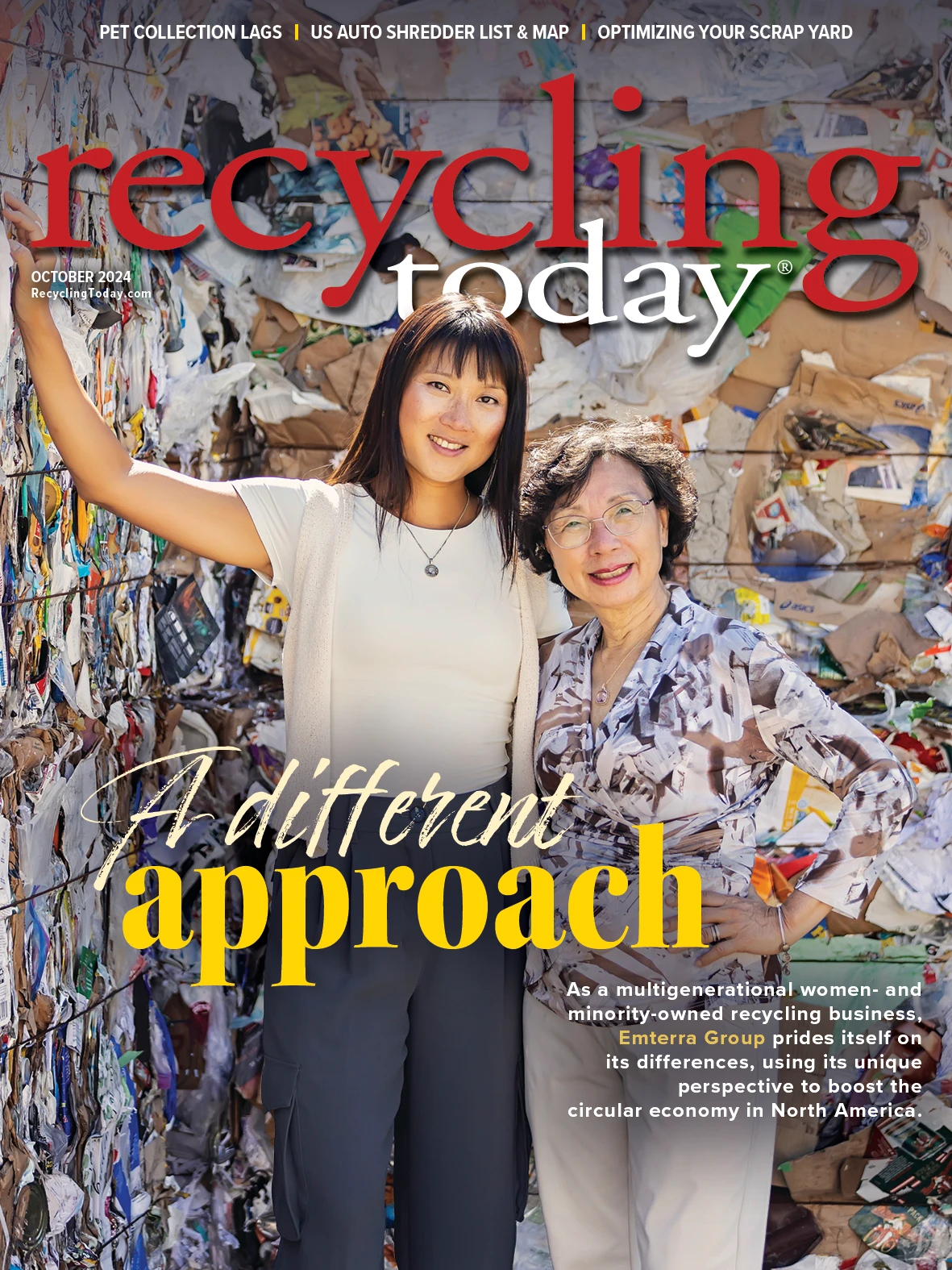
Explore the October 2024 Issue
Check out more from this issue and find your next story to read.
Latest from Recycling Today
- Aqua Metals secures $1.5M loan, reports operational strides
- AF&PA urges veto of NY bill
- Aluminum Association includes recycling among 2025 policy priorities
- AISI applauds waterways spending bill
- Lux Research questions hydrogen’s transportation role
- Sonoco selling thermoformed, flexible packaging business to Toppan for $1.8B
- ReMA offers Superfund informational reports
- Hyster-Yale commits to US production