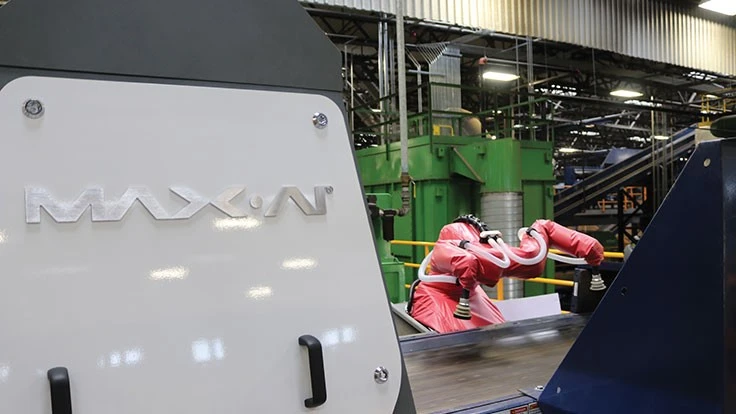

We launched our Max-AI® AQC (Autonomous Quality Control) robotic sorter at WasteExpo in 2017. But our Max-AI (artificial intelligence) technology is capable of so much more, as we’ve shown in the subsequent two years.
In addition to our Max-AI® AQC, our Max-AI technology can be implemented throughout a material recovery facility (MRF) in standalone detection and reporting equipment; the Max-AI® VIS (Visual Identification System); in robotic sorters; and in collaboration with optical sorters, such as the NRT SpydIR® with Max-AI. To enable our customers to use the information collected by Max-AI, our team also created the Total Intelligence Platform (TIP), which provides real-time and trending information on material composition, system performance and more. Max-AI’s ability to see and think has opened the door to unforeseen levels of automation, intelligence and performance.
Never content with the status quo, we debuted our next generation of Max-AI technology at WasteExpo 2019, including our new AQC-C (collaborative) robotic sorter.
Meet the CoBot
We all know that collaboration is the key to accomplishing many tasks, and that’s especially true in a MRF. Employees collaborate with one another in addition to working in tandem with sorting equipment to efficiently and effectively sort recyclables. Additionally, most MRFs are tight on space, making the addition of new equipment challenging.
Manual sorters are flexible, can move positions and fit between chutes. But manual sorters significantly increase operating costs, especially over multiple shifts. They can be difficult to hire, train and manage, and even more difficult to keep in the dirty, dull and dangerous job that is MRF sorting.
We had to solve these challenges for our customers, and we did with our newest innovation, the Max-AI® AQC-C.
Consisting of a Max-AI® VIS and at least one collaborative robot, or CoBot as we like to call them, the Max-AI® AQC-C is quickly and easily installed into existing MRFs. These units can be installed in just a few hours.
Our CoBots work safely alongside people, unlike our AQC, which is positioned above the conveyor and requires structure to support the robot and guard employees. The AQC-C is positioned next to the belt, between chutes—the same way a person is positioned. The AQC-C can be installed in sort cabins, on narrow walkways and in other tight locations alongside your employees. It is also easily scalable, with the ability to install up to four robotic sorters behind each Max-AI VIS. Each sorter can sort up to 40 picks per minute and up to four different material types for a total of 160 picks per minute with four CoBots!
In cases where footprint limitations are a factor, the Max-AI® AQC-C is an ideal solution because it can work essentially any place a manual sorter can. But, unlike a manual sorter, the Max-AI® AQC-C won’t get tired, sick or injured, and it will show up every day and sort all day without a break. Offering the ultimate flexibility, customers can add one, two, three or four AQC-C units per VIS, enabling them to easily adapt to their processing needs as they evolve over time. AQC-C units also can be moved among VIS units throughout a facility as your sorting needs change!
_fmt.png)
VIS stands alone
The revamped Max-AI® product line includes VIS in its standard design with all equipment. VIS analyzes and reports material composition data to MRF operators and directs sorting equipment. In the past, we incorporated VIS into the equipment structure. This change, based on our two years of experience installing Max-AI solutions, is advantageous as it makes possible a separate installation of VIS from a robotic or optical sorter, which benefits Max-AI customers in many ways.
The neural network AI is trained for each installation after VIS gathers data from the material stream. When VIS is installed prior to the sorting equipment, whether robotic or optical sorters, it allows for the AI to be trained and optimized for the sorting task it will be performing. This change also enables the collection of detailed material composition data to verify that the purchased equipment is the correct solution for the MRF or whether an equipment modification is appropriate. We’re not interested in selling you a one-size-fits-all solution because we know that is never the case in a MRF environment. Instead, we want to ensure you’re investing in the right equipment for the task at hand—our customers are truly our partners, and we design solutions tailored to maximize their profits.
VIS can be used to learn more about a MRF’s material stream. It also can be used in combination with a number of sorting devices at a MRF for the ultimate operational versatility and responsiveness.
By standardizing the VIS design, we provide the flexibility to add equipment to VIS units or to move equipment in the future as a MRF’s processing needs change. Where else can you find that degree of versatility?
Easier maintenance
In addition to these innovations, we’ve updated the design of our Max-AI® AQC to better facilitate maintenance.
_fmt.png)
We’ve introduced gull-wing doors so technicians and operators can easily access service areas. We also improved access to air filters and to the robotic sorters’ end-of-arm tooling. Visible notification lights have been incorporated to alert operators to areas in need of maintenance.
All of these changes have been designed to increase your ease of ownership and maintainability and to improve productivity and uptime. These changes also allow for faster installation within a smaller footprint.
Dominant technology
BHS’ continuous innovation has made Max-AI® the world’s most-installed AI-powered recycling solution. The technology is driving improvements in MRF design, operational efficiency, safety, recovery, system optimization, maintenance and more.
Join the automation revolution and contact us today to learn more about how Max-AI® technology can benefit your operations and adapt along with your MRF’s sorting needs.
To view the Max-AI® AQC-C in action, visit bhslink.com/max. As they say, “Seeing is believing,” and we’re prepared to help you discover the benefits the new Max-AI product line can offer your operation.
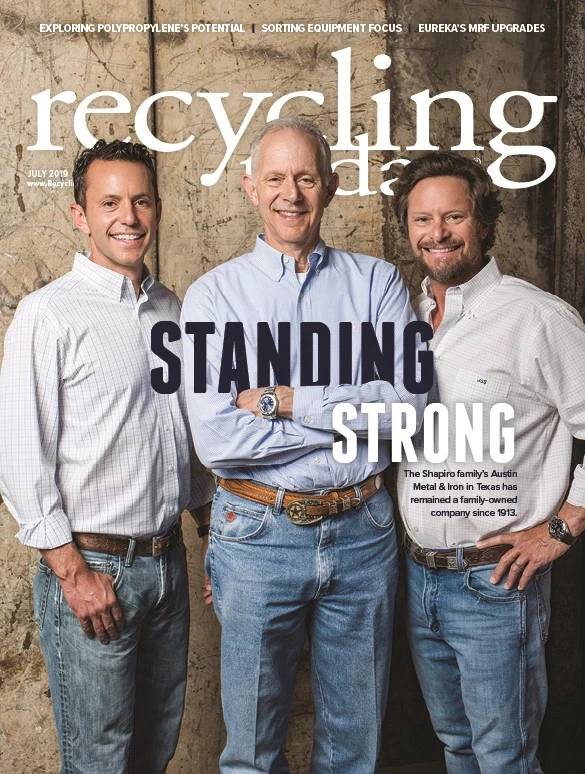
Explore the July 2019 Issue
Check out more from this issue and find your next story to read.
Latest from Recycling Today
- Aqua Metals secures $1.5M loan, reports operational strides
- AF&PA urges veto of NY bill
- Aluminum Association includes recycling among 2025 policy priorities
- AISI applauds waterways spending bill
- Lux Research questions hydrogen’s transportation role
- Sonoco selling thermoformed, flexible packaging business to Toppan for $1.8B
- ReMA offers Superfund informational reports
- Hyster-Yale commits to US production