
When I was first asked to contribute this article on avoiding overspending during the design/build of a recycling facility, my initial thoughts were on discussing the incidental items, such as thickness of concrete, types of overhead doors and other items along those lines. While these items do play an important part in designing your facility, I believe controlling the “costs” of your new recycling facility hinge more on site selection, efficient and safe design, durability and designing an efficient building layout that is “right-sized.”
We like to look at recycling facilities in two different ways. You have the initial capital outlay to purchase the site, to design and build the facility and to install the equipment. Then you have the ongoing operating costs of the facility, which include your employees and all the building- and equipment-related operations and maintenance costs.
I will briefly dive into how a material recovery facility (MRF) owner can save money in both of these areas—initial capital outlay and ongoing operations—and how to apply these suggestions to your next project.
SAVING AT THE OUTSET
The major factors at play here are the site selection and the building size. The site itself can cost an owner millions during the construction phase. Not fully vetting a site before purchase can lead to many unforeseen costs down the road. This also varies based on whether you purchase an existing building or a clear site. Existing buildings can be full of issues, such as too many interior columns that get in the way of the equipment, improperly sized electrical services, insufficient water pressure to take the fire sprinkler system up to code, concrete that is not designed to carry the loads required, improper clear heights within the building for the equipment or operations and many others. Along with these issues, environmental issues, such as asbestos or other contaminants, also could be present.
Clear sites could pose issues such as poor soils that require overexcavation and replacement, poor traffic patterns arising from how the site is shaped, poor access to highways and other major access points, the grade change may be too great for a building of the size you need and, lastly, you could have bad neighbors.
All of these factors can cost MRF owners excessive capital that they didn’t plan on when they started the process and built pro formas to obtain approvals for their projects.
To avoid many of these unexpected costs, it is important to get recycling facility design experts involved early in the project so they can assist in the process of selecting the right piece of property upfront. It likely will increase the cost of the due diligence period, but you will be armed with more accurate information to make your decision. Spending an extra $50,000 to $100,000 upfront could save you 10 times that or more down the line. The costs associated with a wrong decision regarding where to site a MRF typically are high.
Once a site is selected, the next step is designing the recycling facility itself. In my opinion, it is best to hire your design/build partner along with your preferred recycling equipment vendor at the outset of the design phase. This forms the team that will bring this project to its completion and increases communication and understanding during the process. It is very important for your design/build partner to understand recycling facilities and the nuances that go into designing them.
The most important part of the design phase is right-sizing the building. You wouldn’t install a 50-ton-per-hour system to handle 25 tons of volume, right? Then why build a building that can handle 50 tons per hour?
I have visited many recycling facilities that are much larger than they need to be. While the larger size allows for growth potential, it also creates an inefficient facility and greater capital outlay than was required. If the goal of this piece is to tell you how to not overspend on your MRF, then right-sizing is No. 1.
Facilities should be designed to handle your volume for the next five to 10 years (depending on your individual market conditions). This is all vetted out during the early design phase for the project. Begin by developing a chart that tracks your projected throughput for the next five to 20 years. Work with the design/build company and the equipment vendor to determine the volume the MRF will handle and design the current project for that volume. Then move directly on to the phasing plan for the facility. What additions will be required to accommodate future growth?
Laying out these plans now ensures that you design the site to handle growth and not impede your operations. You can then start to plan and budget for these additions based on how well you are hitting your growth goals.
Following this process allows you to save capital now, manage your current volumes and plan for future capital outlay based on revenue. Including the equipment vendor in this process allows the supplier to tell you how equipment design is affected and allows the vendor to provide a plan for you to use as part of your future expansion.
WITH PURPOSE
When it comes to the facility itself, it is important that it is designed to handle the operations that occur within it. Waste facilities in general take a lot of abuse. Whether it is from tipping loads, bale movement or material handling within the building itself, it is highly important that you plan for all of these factors during the design process.
Our goal in designing and building these facilities is to keep your on-going maintenance costs as low and manageable as possible. A few key points to keep in mind are to:
- keep all mechanical piping away from any material handling/mobile equipment work areas;
- protect all your columns as if you know they are going to get hit because they will;
- use a high-strength, durable concrete mix for tipping floors;
- size push walls and material storage areas to handle the proper storage of material based on your individual needs;
- design bale storage areas to handle stacks of bales and size them sufficiently to store bales until they are shipped;
- work with the equipment supplier to identify the exact requirements of the various pieces of recycling equipment, each of which have different concrete load points, so you don’t have issues installing the equipment;
- watch the placement of interior columns, if they are required, so as not to interfere with equipment layout;
- stay on top of the locations of pits, which will change slightly during the equipment design process, so they are not installed in the wrong locations.
Note that there are many ways to plan a facility during the design phase to help keep costs in check during construction and to avoid too many change orders or other additional costs.
The best way to manage the capital costs of your facility, therefore, hinge on picking the right site, right-sizing the building and maximizing communication between the facility owner, the design/build company and the equipment supplier. These three things should prevent overspending initially.
CONTROLLING ONGOING COSTS
Every facility is different. During a facility’s 20-year life, the ongoing employee, operation and maintenance costs exceed the initial capital outlay of the facility. Therefore, we consider these costs during the design phase and work hard to ensure they remain manageable in the long term.
While your design/build partner doesn’t directly impact the size of your workforce, the equipment supplier does. The vendor’s equipment design and your output requirements directly affect the number of employees you have staffing the line. You need to manage this.
Your designer can work with you and your equipment supplier to manage the distances the MRF’s employees have to travel to take breaks and to use the locker rooms and other facilities on-site as well as to manage other necessary foot travel within the building. For the MRF to be as efficient as possible, you want to design your equipment and building to best limit the amount of steps your employees need to take to get places. This increases the amount of time employees spend working and decreases the amount of time the picking areas are unmanned.
It also is important to keep the MRF’s employees from having to walk on the floor when possible. This helps to avoid the possibility of accidents and creates efficiencies by avoiding using the stairs.
These considerations also apply to the facility’s mobile equipment operators. Limit the amount of time they spend driving around the facility. They should make short, compact movements. Keep them contained within a designated work area so they aren’t wasting time, fuel and equipment hours driving around the MRF.
All of these factors can save you money on equipment maintenance and operations costs for the life of the facility, which can add up pretty quickly.
Building maintenance is another manageable cost to factor into the design of a MRF. In addition to some of the tips I mentioned previously, additional factors you may want to consider include:
- energy-efficient lighting;
- proper site pavement designs;
- proper locations for sprinkler heads and lighting;
- selecting and using the right materials for each application;
- planning to stack excess materials resulting from equipment being down or a problem with shipping bales;
- proper dust covers on motors and panels; and
- HVAC equipment locations.
We pride ourselves on designing structures that are operationally efficient and durable, or as we call it “purpose-built,” facilities. Knowing and understanding the operations that will take place within the building leads you to design and build it in a way that helps to avoid major issues going forward.
Limiting your new MRF’s operations and maintenance costs in the long term will increase your financial return on your investment and will increase the likelihood of a successful project.
It is important to understand these costs and the potential savings you can realize throughout the design process to better contain costs throughout the life of your new MRF.
Get curated news on YOUR industry.
Enter your email to receive our newsletters.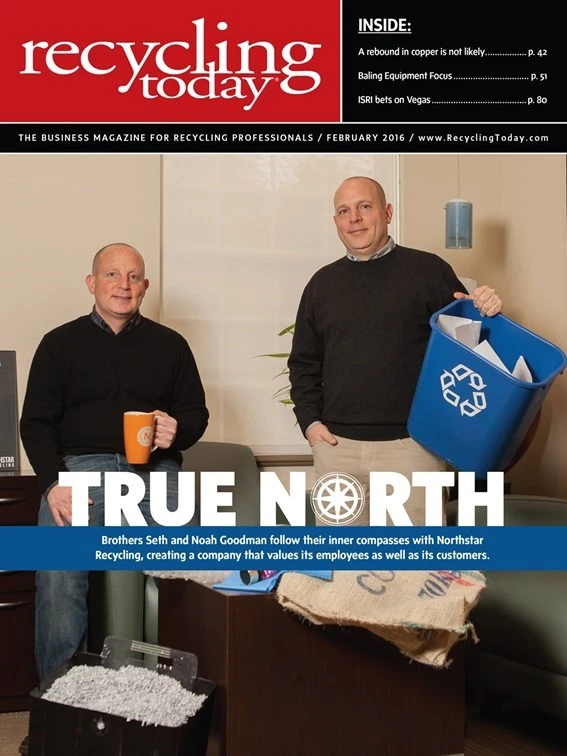
Explore the February 2016 Issue
Check out more from this issue and find your next story to read.
Latest from Recycling Today
- Recycled steel price crosses $500 per ton threshold
- Smithers report looks at PCR plastic’s near-term prospects
- Plastics association quantifies US-EU trade dispute impacts
- Nucor expects slimmer profits in early 2025
- CP Group announces new senior vice president
- APR publishes Design Guide in French
- AmSty recorded first sales of PolyRenew Styrene in 2024
- PRE says EU’s plastic recycling industry at a breaking point