It seemed as if all the world’s problems were set upon their doorsteps during that time period—with financial crises from Asia and eastern Europe dragging down commodity markets while the rest of the North American economy prospered.
But free trade advocates may be able to come out of hiding in 2000, as steel mills and foundries in overseas markets continue to raise their production rates. If their capacity rates do increase, they should consume enough scrap and metallic melting units to lift ferrous scrap prices back up to a more comfortable level above $100 per ton.
PROSPECTS FOR MELTING
Scrap dealers often look at their industry as being operated in a reverse fashion—with the buy side of raw materials being the critical aspect of the operation. As long as there is scrap coming across the scale and if there are industrial accounts to be serviced, then the difficult part of the process has been accomplished.
The global nature of today’s scrap market and the streamlined nature of the steel industry today may be changing that line of thinking at least a little bit. The volume of material coming in is still critical. But in an era of just-in-time inventory, if the melting capacity of favored scrap consuming mills is greatly curtailed, scrap dealers can be left in a bad situation. If the demand for ferrous scrap dries up too soon, processors can be left with large volumes of scrap that continue to lose value as they take up space in the scrap yard.
Many scrap dealers found themselves in just this situation in late 1998. While they may have been doing considerable volume on the buy side, there is no worse negative margin position to be in than when scrap has nowhere to go.
Many scrap dealers found themselves in just this situation in late 1998. While they may have been doing considerable volume on the buy side, there is no worse negative margin position to be in than when scrap has nowhere to go.
The North American steel industry—and electric arc furnace (EAF) operators in particular—had been riding high with capability utilization rates (also called capacity rates) of 88% or higher for some time heading into the mid-1998 slump.
At that time, though, the low prices and glut of steel coming from depressed economies overseas caused sudden slashes in steel mill capacity rates. EAF mills that had been reliable buyers of ton after ton of ferrous scrap began slashing orders dramatically. Overall steel industry capacity rates, as calculated by the American Iron and Steel Institute, Washington, fell sharply, reflecting a similar drop in scrap melting activity.
The North American steel industry fought a difficult battle to retain as much market share as possible during the “onslaught” of foreign steel. Have mills been able to ramp production back up, or are imports still keeping capacity rates at a sub-par level?
Until mid-October, the answer appeared to be that U.S. mill capacity remained at a level well below 85%. That number, however, was finally reached for the first time in a long while during the week of Oct. 16, when an 85.7% capacity rate was reached with the production of 2.1 million tons of steel.
Before that recent uptick, however, the AISI continued to voice concern about the effect imports were having on steel production in the U.S. “The steel crisis in the United States continues,” says AISI chairman Paul Wilhelm, commenting upon August figures for steel import levels and their prices. “The problem is, imports remain at an unacceptably high level, and this is making worse the damage from last year’s record import surge. As a result, we see little to no restoration of fair market value, and serious injury to America’s steel companies and employees continues.”
Improvements in some overseas economies may finally be easing that situation, and the 85% capacity rate for the week of Oct. 16 can be considered a good sign compared against the 74% and 75% rates that were being recorded in January of 1999.
THE COMPETITION
Another problem ferrous scrap has been facing on the sell side comes from competition in the forms of imported scrap and from scrap substitutes.
While imported steel may have come from several nations with excess inventory, the former Soviet Union is tagged as the primary source of imported ferrous scrap. Russia, the Ukraine and other former Soviet nations have been engaged in the dismantling of obsolete factories and military bases, and have been selling off the metal for hard cash.
An indication of the rate at which scrap metal has been pouring out of Russia can be seen in the volume of stainless steel scrap that has left that country. According to E.J. Hayes of Abacus Consultancy, Chelmsford, U.K., in 1990 just 2,000 metric tons of stainless steel or other nickel-bearing scrap left the Soviet Union for western destinations.
In 1997 that total had zoomed to 346,000 metric tons. For 1998 the total declined somewhat, but remained high at 324,000 metric tons. According to Hayes, that number declined not because Russia was melting more of its own scrap, but simply because the total universe of obsolete facilities to be dismantled in the former Soviet Union is finally starting to decline.
Gary Schnitzer of Schnitzer Steel Products, Oakland, Calif., calls the nine million tons of ferrous scrap sent from Russia to the U.S. in 1998 “phenomenal,” and notes that the practice of scrap exports coming from former Soviet nations “continues unabated.”
As could be expected, at the same time ferrous scrap imports were pouring into North America, once reliable export markets dried up due either to internal economic woes or because of a similar availability of low-cost scrap coming from Russia and other nations.
While imports have offered considerable competition, also vying for melting tonnage at mills are pig iron, direct reduced iron (DRI), and other forms of scrap substitutes, including processes that allow EAFs to smelt their own scrap substitutes.
Many of these scrap substitute companies look upon their materials as supplements to scrap in the steelmaking process. Skeptics of this position note, however, that every ton of scrap alternative material that is used means one ton less of scrap is melted.
For makers of scrap substitute materials, the second half of 1998 and 1999 might not prove to be much better than it has for scrap companies. But technical developments underway are being watched with interest by steel companies and scrap dealers alike.
Midrex Direct Reduction Corp., Charlotte, N.C., has been a long-time maker of DRI production equipment. In the late 1990s, the company has been marketing its FastMetR and FastMelt pellet making and rotary hearth furnace technologies.
The FastMet process allows steelmakers to make DRI pellets by extracting iron from iron ore fines or steel mill wastes such as iron oxide dust and mill scale. The extracted iron is mixed with pulverized coal and formed into pellets that are fed into a rotary hearth furnace. Once formed, these DRI pellets can then be fed into Midrex’s FastMelt equipment, which feeds the DRI directly to a melter that produces hot metal that can be fed directly to a steelmaking furnace.
In Butler, Indiana, Steel Dynamics Inc. has been using a similar process to provide feedstock for its 2.4 million tons-per-year EAF mill, one of the largest in the U.S.
A number of other companies in nations ranging from Brazil and Australia are also marketing variations of rotary hearth furnace technology.
The reliable feedstock could be sought by steelmakers fearful of an eventual shortage of obsolete ferruos scrap items.
LOOKING LONG-TERM
The low-cost scrap metal that is pouring into North America (and low shipping rates) and the burgeoning of scrap alternatives certainly present causes of concern for ferrous scrap dealers. Long-term prospects for the future of ferrous scrap, however, can hardly be considered bleak.
Steel industry analyst Peter Marcus, who is managing partner of World Steel Dynamics Inc., Englewood Cliffs, N.J., began predicting several years ago that the EAF steelmaking revolution would eventually result in a shortage of obsolete iron and steel scrap.
Even during times of scrap price plunges and narrow margins, Marcus remains convinced that the steel industry is still facing a looming shortfall of scrap and other melting units. “Gains in recovery of [obsolete scrap] are potentially dampened in the next 12 years by the relatively slow growth of the global reservoir of steel scrap that is, on average, eight to 30 years old,” Marcus told attendees at a recent ISRI function.
Marcus contends that a slower overall growth rate in the demand for steel products from 1997 onward will ultimately lead to an obsolete scrap pool that can fill a smaller percentage of the growing needs of the EAF steel industry. By his calculations, the scrap reservoir has been growing at just a 1.3% clip annually since 1997, while the shift toward EAF steelmaking is causing the demand for scrap to grow at a higher annual rate.
“Steel scrap prices are poised to rise sharply, we believe,” said Marcus, who predicted prices to rise from their current $100 per ton U.S. average to $135 or $140 per ton by the summer of 2000.
“Demand for obsolete scrap is just beginning to rise on a year-to-year basis,” Marcus remarked. “In July of 1999, demand for obsolete scrap was up by about 7% on a year-to-year basis [versus 1998],” he added.
One concern that could remain for ferrous scrap’s long-term future is the overall continued viability of steel as a material consumed by the largest manufacturers in the transportation and appliance sectors.
As an example, the gains made by the aluminum industry within the vehicle component segment have received a lot of attention this decade. Can the steel industry hod its ground in critical areas such as the use of steel sheet for auto stampings?
According to data compiled by American Metal Market, the use of lightweight steel sheet grades by the auto industry has increased by 162% since 1977, compared to an increase of 143% for all grades of aluminum. The American Iron and Steel Institute (AISI), Washington, acknowledges that cast aluminum has enjoyed gains versus cast iron, but also says that lightweight steel sheet has moved in to replace older carbon steel grades.
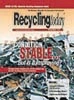
Explore the November 1999 Issue
Check out more from this issue and find your next story to read.
Latest from Recycling Today
- Fitch Ratings sees reasons for steel optimism in 2025
- P+PB adds new board members
- BlueScope, BHP & Rio Tinto select site for electric smelting furnace pilot plant
- Magnomer joins Canada Plastics Pact
- Out of touch with reality
- Electra names new CFO
- WM of Pennsylvania awarded RNG vehicle funding
- Nucor receives West Virginia funding assist