
CompuCycle, an information technology (IT) asset management firm based in Houston, relies on shredding equipment from SSI Shredding Systems Inc. of Wilsonville, Oregon, to help it recycle 40,000 to 60,000 pounds of electronic scrap per day.
CompuCycle operates electronics and plastics recycling plants and recovers metals and plastics in-house without having to rely on the services of downstream processors.
“One of the reasons we opened our [electronics] facility in 2019 is because we were compromised by other certified processors and recyclers; that’s when we decided to do it ourselves,” CompuCycle President Clive Hess says. “It’s a commitment that we made to our customers that once we pick up your equipment, chain of custody remains with CompuCycle throughout the entire process.”
Worthwhile investments

CompuCycle invested in equipment from SSI in 2019 to help it process end-of-life electronics.
Prior to that, CompuCycle only had a mobile shredder, and its scrap was shipped to other processors to be separated and recycled. Now, along with the mobile shredder, the company has two SSI shredders at the electronics processing facility and one SSI shredder at its plastics recycling facility next door.
CompuCycle’s electronics facility in Houston uses SSI’s Quad Q100 and Quad Q70 model shredders. Magnets recover the steel, while eddy currents recover aluminum and copper and optical sorters separate plastics by color.
The Quad Q100 and Quad Q70 are low-speed, high-torque, four-shaft rotary shear shredders that break down end-of-life IT equipment on CompuCycle’s electronics processing line. The company says it selected the SSI shredders for their energy efficiency, shock protection, self-cleaning design, application-specific feed hoppers and cutter configurations.
“In the Houston plant, we can process 40,000 pounds a day, and the ITAD plant processes over 120,000 assets annually,” Clive Hess says.
At its electronics recycling plant, CompuCycle says it can process as much as 60,000 pounds of material in one eight-hour shift, depending on what’s being processed. The company used 40,000 to 60,000 pounds as the volume benchmark when selecting the SSI equipment.
“We decided we wanted to use the best equipment, not the cheapest,” Clive Hess says. “SSI has a price, but the reliability is fantastic. You need to weigh all those factors if you’re going to put in a plant. It must be reliable and get the throughput that you need.”
He adds there have been no setbacks since the equipment was installed. “When we run into challenges, SSI is very responsive to work with CompuCycle to settle whatever issue it may be.”
To keep the equipment running optimally, in-house maintenance technicians perform checks every morning, making sure all fluids are topped off and that cutters are working properly.
“We have a pretty comprehensive maintenance schedule [with] full-time maintenance technicians,” Clive Hess says.
Expanding capabilities

CompuCycle opened its plastics recycling plant next door to its electronics facility late last year, and it includes an SSI Uni-Shear SR500 shredder—a single-rotor shredder and grinder that reduces bulky material in a single pass. The machine is designed to shred material that contains minimal metal, using a screen to produce particle sizes ranging from 12 to 17 millimeters that can be sorted efficiently by density using three float tanks.
“CompuCycle wanted a shredder versatile enough to handle bulk-fed loads of e-plastics originating from any processor out there,” says Dave Fleming, SSI vice president of sales and marketing. “Our SR500 Uni-Shear can hold up to 4 cubic yards of volume and make small, well-liberated output size, so it’s perfectly suited for this task.”
The company also added an electrostatic separator to sort acrylonitrile butadiene styrene (ABS) from polystyrene (PS).
Within the plastics plant, CompuCycle can process 6,000 pounds per hour, or 24,000 pounds in an eight-hour shift, with the aid of the shredder, Clive Hess says.
“With the SSI equipment that we have, we do it all, we don’t rely on anyone else, and we know what to do and we are responsible for what we do,” he adds. “We have the infrastructure, security and process, which is what differentiates CompuCycle from everyone else.”
Keeping it in-house
CompuCycle receives electronics generated within Texas and surrounding states from corporate businesses, residents and other electronics recycling companies. Devices the company processes include printers, video equipment, cables, cellphones, computers, cords and more.

Electronics are shipped to CompuCycle in pallets and gaylord boxes, where they are weighed before being fed to the Quad Q100 and Quad Q70 shredders. After the steel, copper and aluminum have been separated, plastics are shredded into even smaller pieces with the Uni-Shear SR500 in the plastics plant.
Once processed, the various commodities are packed into 2,000-pound-capacity bulk bags for shipping.
While many electronics recyclers stop at producing a mixed plastics product, Clive Hess says many plastics reprocessors and IT manufacturers won’t accept mixed plastics. Therefore, at its plastics plant, CompuCycle continues to separate plastic by density into single polymers, such as polypropylene (PP), polyethylene (PE) and ABS.
“Making single-polymer plastics that original equipment manufacturers [OEMs] can reuse to produce new electronics or other products while adhering to international recycling standards is a game changer for domestic companies and those that need their plastics shipped globally,” CompuCycle CEO Kelly Adels Hess says in a news release outlining the company’s investment in plastics recovery.
Sorting plastics by polymer helps CompuCycle maintain a circular economy that minimizes reliance on finite resources, aids in supporting OEM sustainability goals and serves as a best practice in e-scrap recycling, the company says.
Most of the consumer electronics CompuCycle receives are recycled, and their materials recovered. The company’s corporate clients’ devices often can be reused and resold. However, some companies want everything destroyed, which CompuCycle can do with its SSI equipment and processing plant.
CompuCycle says when it receives material from larger companies, around 80 percent will be processed for reuse and 20 percent will be processed for scrap. With smaller companies, about 80 percent is recycled and 20 percent is reused.
“We do a lot of residential recycling for cities and counties, and 100 percent of that material in our processing plant is scrap,” Clive Hess says.
Understanding e-plastics
He says education needs to be prioritized within the electronics recycling industry, adding that many firms lack knowledge about plastics.
“The challenge we faced in the plastics industry was that electronic processors in the past processed all mixed plastics and then sent them to companies that received such a contaminated batch of plastics,” he says. “Most of the plastics industry doesn’t want electronic plastics.”
CompuCycle is testing its plastic samples and has received positive results, Clive Hess says. The firm is optimistic about its ability to process plastics and advance domestic and international solutions.
“There is a lot of communication that we are having with the plastics compounders explaining to them our process, which is not just shredding, its shredding and separating,” he says.
Get curated news on YOUR industry.
Enter your email to receive our newsletters.
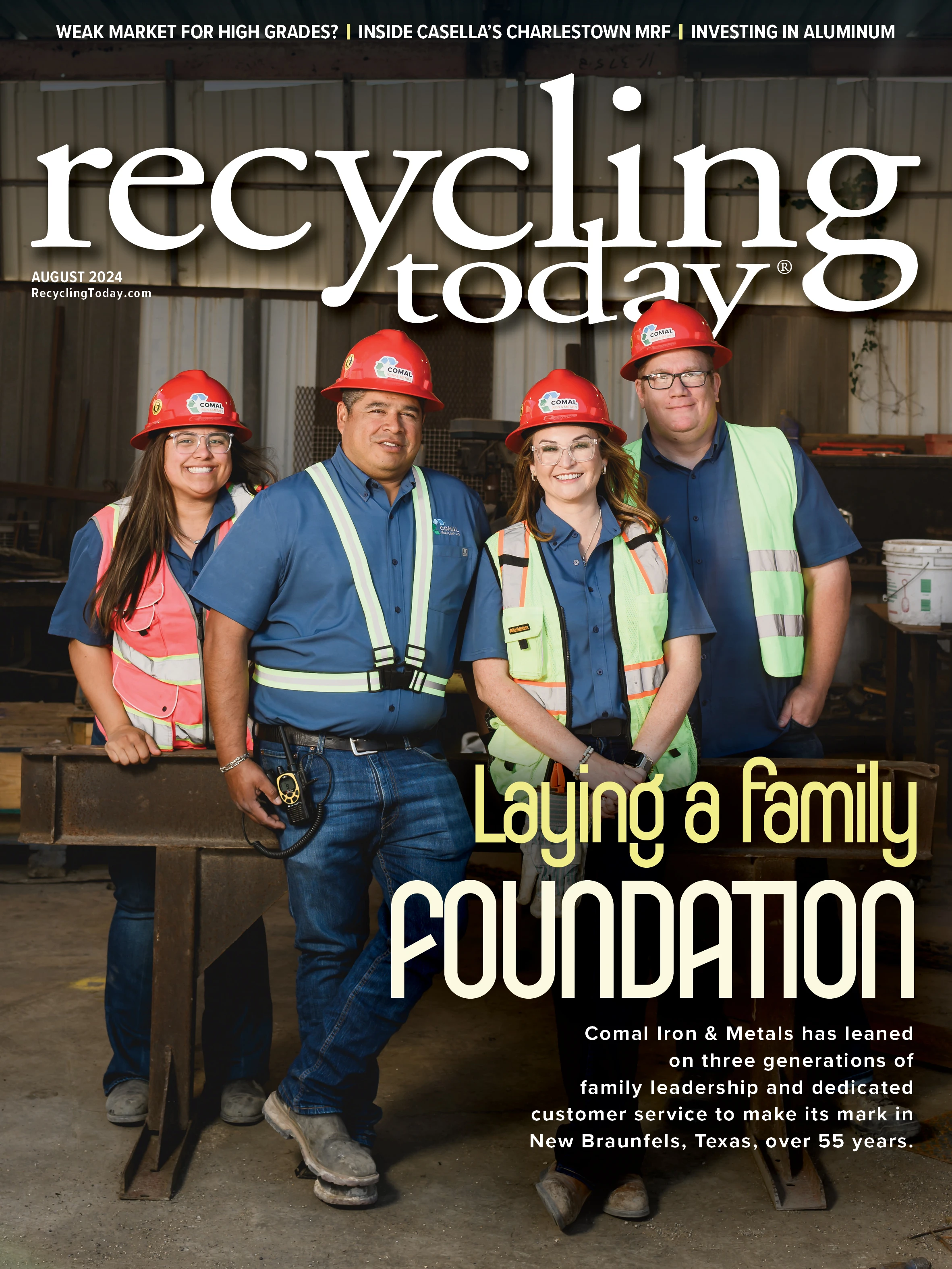
Explore the August 2024 Issue
Check out more from this issue and find your next story to read.
Latest from Recycling Today
- Greenville, Mississippi, launches aluminum can recycling program
- Cotton Lives On kicks off 2025 recycling activities
- Georgia-Pacific names president of corrugated business
- Sev.en Global Investments completes acquisitions of Celsa Steel UK, Celsa Nordic
- Wisconsin Aluminum Foundry is a finalist for US manufacturing leadership award
- MetalX announces leadership appointments
- Sofidel agrees to purchase Royal Paper assets
- US Plastics Pact report charts expansion path for recycled content in packaging