For nearly 30 years, the plastics recycling industry in the Northeastern United States has included two separate companies that have quietly grown to each become major players in that market.
Both Nicos Polymers and Debco Plastics have roots on Long Island, though each company separately engaged in different processing methods and each largely pursued different paths to add value to secondary plastic
Location: Nazareth, Pa. No. of Employees: 100 Equipment: More than 20 grinders, the majority manufactured by Cumberland Engineering Corp.; a heavy-duty shredder made by Vecoplan; compounding and pelletizing equipment made by NRM, Xaloy and Beringer Services Provided: Recycling and toll processing of predominantly post-industrial plastic scrap, including multiple-resin items and materials requiring customized formulas; recycled plastics compounding, blending, pulverizing and pelletizing; product destruction
materials.
At A Glance: Nicos Polymers LLC
Principals: Ron Schinik and David Krinsky of Crownbrook Capital, James Knicos of Nicos Polymers and David Garfinkel of Debco Plastics
In a 2007 move driven by investment group Crownbrook Capital, New York, the two companies are coming together to create a plastics recycling powerhouse that should continue to serve the plastic scrap market on the East Coast, in the Midwest and beyond.
Operating from a facility in Nazareth, Pa., with 180,000 square feet of plant space, Nicos Polymers LLC is offering a full range of processing and marketing services to generators of plastic scrap throughout North America.
GROWTH PATTERNS. By the time Knicos started his plastic recycling company in 1978, 11 years had passed since the character portrayed by Dustin Hoffman in "The Graduate" had received his advice that the future lay in plastics.Knicos and his wife Tara started out buying and selling material and operating initially from a one-car garage and then 1,200 square feet of leased space on Long Island, N.Y. The company moved into an 8,000-square-foot building on Long Island before moving to Pennsylvania in 1988 to a building twice that size.
The company had been adding grinders throughout its existence, but made its biggest move in 2000, when it built its current 180,000-square-foot plant in Nazareth.
In the span of 30 years, Nicos Polymers has gone from a husband-and-wife team operating from a garage to a 90-employee company that has been sold to an investment group that intends to fund even more growth.
From the beginning, Knicos has concentrated on what he calls "industrial grade plastic scrap."
The company has expanded into different resins and materials throughout its history, says James, and has always invested in grinding capacity to match. "It took awhile to obtain the capital for our first grinder in 1979," he recalls. That first machine had a 30-hp motor, though his largest grinder now is powered by a 300-hp motor.
"We have more than 25 production machines—grinders and pulverizers—plus assorted blenders and mechanical systems that remove contaminants," he notes.
The considerable production capacity will soon be joined by pelletizing
machinery operated by Debco Plastics and its founder David Garfinkel.
Online Sidebar - Out of the Gate
Click here to view online only sidebar
Debco Plastics, which was based in Freeport, N.Y., before its move to Nazareth, was acquired by Crownbrook Capital at about the same time it acquired Nicos Polymers.
"We’re combining two very good companies in Nicos and Debco," says Ron Schinik, one of the investment partners of Crownbrook Capital. "Debco’s expertise in re-processing and compounding pellets will be a terrific match with what Nicos does."
Crownbrook closed on its purchase of Debco in January of 2007 and its purchase of Nicos in June. "We saw that these two companies dovetailed nicely and there was very little overlap in operations," says Schinik. "We saw the best of both worlds with these two companies. It was a great fit, and they’re both best in breed. And it has been a seamless transition to date."
By volume, the companies are also heavyweights. Nicos Polymers recycled approximately 90 million pounds of plastic in 2006 and is on track to exceed 100 million pounds in 2007. Adding the Debco capacity for 2008 will yield further production at the already-busy Nazareth plant.
IN AND OUT. At any given time, there is most likely from 1 to 5 million pounds of plastic scrap on the premises at the Nicos Polymers facility.While that figure sounds large, it actually demonstrates the quick production turnaround time the company has achieved, as it processes some 100 million pounds of material this year.
Production at the facility is close to non-stop, as Nicos deploys two 10-hour shifts on weekdays and generally operates for six hours each Saturday. Debco operates 24 hours a day for five or six days each week.
A parade of scrap materials is received through more than 20 loading docks—a parade that is notable both for its volume and its variety in material and form.
Materials include pipe, siding, fence and window scrap, plant trimmings, floor tiles, plastic bottle trim, thermoform and sheet waste, scrap generated at garden hose factories, baled stretch film, plastic racks, injection-molded scrap and purgings from molding and extrusion plants.
Also noteworthy is the geographic radius from which material is drawn. Nicos Polymers sales support and IT administrator Bob Perrone estimates that radius stretches out some 1,000 miles for some types of scrap.
Knicos adds that processes developed by his company to address the recycling of mixed-materials plastics (such as the garden hoses) extend that radius "to the West Coast, Canada and the deep South."
On the outbound side, Nicos ships its granules and flakes not only throughout North America, but to Europe and Asia as well.
As with all recycling operations, obtaining material remains a key task. Perrone says manufacturing and processing plants are an important part of the Nicos supply chain. "We contact any plastics-oriented manufacturer and provide an analysis of the usability of their scrap materials," he notes.
Online Sidebar - Destructive Tendency
Click here to view online only sidebar
During those visits, the company is also willing to conduct a waste audit to look for other opportunities and supply solutions for issues relating to the life cycle of products and sustainability.
"What is common is that we find there are materials that they didn’t realize could be reclaimed," says Perrone. "As we go past the Dumpster or Gaylord box or refuse bin, we’ll see stretch film in there or that they are throwing their purgings out."
The company’s willingness to work with blended, attached or mixed materials has provided many opportunities, says Perrone. "Sometimes there may be two materials in that purge, and they didn’t know we can separate it."
Nicos has thus become a recycler of formerly landfilled materials, such as industrial roofing with nylon reinforcement and garden hose containing a nylon fiber support layer. "In that sense, we’re problem solvers and troubleshooters for people," says Knicos.
Once material is at the plant it can head to one of several pre-processing or grinding machines, where it is eventually converted to plastic flake. By volume, some 70 percent of material is being picked up from a plastics manufacturer, processed at Nicos and then returned in a toll processing loop to the manufacturer.
Nicos Polymers takes ownership of the other 30 percent of its material, however, creating saleable plastic flake.
The Debco operation, on the other hand, takes ownership of almost all materials, producing flake and pellets for the same consumer base as Nicos. The blend of trading philosophies between the two companies creates a revenue base greater than the sum of its parts and mutual benefits on the manufacturing, trading and profitability levels.
HUMAN TOUCH. Technology and the research and diligence behind that technology are part of the Nicos Polymers story, but the company’s people have also helped place it in its leadership position, says Knicos.The company’s employees have been loyal both to Nicos Polymers and its customers. Several key employees, such as Operations Manager Daniel Sheehan, made the move with the company from New York to Pennsylvania.
Perrone has been with Nicos for five years and is highly complimentary of the company’s operating style and philosophy. "I have never in my life worked for a company like this with the degree of respect that Jim and Tara extend to their employees," he comments. "It’s a business decision to treat their employees as they do, but it comes from their heart, honestly. They make no bones about making sure everyone knows that."
James and Tara Knicos say the way they treat employees more than pays off in the way those employees treat Nicos Polymers and its customers. "Glitches are not passed off with an ‘It’s not my job or department’ attitude," says Knicos. "It’s a family here—it really is," says Tara. "The culture and the philosophy of the company has been to take care of its employees, and if you take care of the employees, they’ll take care of the customers. In that way, we’re customer focused. It’s very difficult to lose a customer once they’ve been treated right."
Consequently, Nicos Polymers’ customers are loyal, and so are employees.
VOLUME LEVEL. With Nicos focusing on post-industrial scrap streams and being located in the Northeastern United States, access to material might seem like an issue. But the company’s leaders are convinced that the American economy will continue to provide opportunity.Even with some manufacturing processes moving offshore, those that remain are more focused than ever on the efficiency that recycling can bring. "Certainly, with the price of raw material and oil going up, it makes recycling more valuable than it has ever been," says Knicos. "There is more opportunity now than there was 28 years ago when the business started."
In Schinik’s mind, how Nicos Polymers continues to grow may not yet be determined, but he is convinced that it will. "I’m very excited about the fact that there are a lot of people out there who can leverage our expertise," he says. "I think the reality is that a lot of the multi-nationals from a waste stream perspective are just starting to learn that it’s easier to reclaim some plastic materials versus dumping them."
If Nicos Polymers can help them learn, it will keep the Nazareth facility moving full-steam ahead.
The author is editor in chief of Recycling Today and can be contacted at btaylor@gie.net.
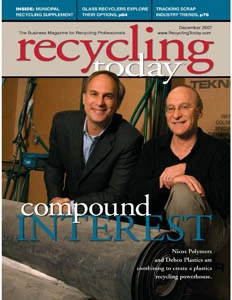
Explore the December 2007 Issue
Check out more from this issue and find your next story to read.
Latest from Recycling Today
- IDTechEx sees electric-powered construction equipment growth
- Global steel output recedes in November
- Fitch Ratings sees reasons for steel optimism in 2025
- P+PB adds new board members
- BlueScope, BHP & Rio Tinto select site for electric smelting furnace pilot plant
- Magnomer joins Canada Plastics Pact
- Out of touch with reality
- Electra names new CFO