Can wood-plastics composite production help turn wood waste into gold?
More than a few wood processors might be wondering how or why some of their competitors have moved into "the plastics business." ExtrusionTek Milacron, Batavia, Ohio, is a maker of equipment for the plastic-wood composites industry, and has some insights into the technology behind this growing market for wood waste.
Wood-fiber/plastic composite is a material made of up to 70 percent wood products that are mixed and saturated with melted plastic in an extrusion machine and die-formed into a profile—usually deck board, railing or fence material.
Louisiana Pacific Corp., Portland, Ore., has recently moved into the business with its WeatherBest decking, introduced at last year’s International Builders Show. Many wood industry businesses are ideally suited to making the transition to production of wood-fiber/plastic composites.
THE GROWING MARKET
Published reports say that as many as three million decks are built, replaced or repaired in the U.S. each year, and only 10 percent have been converted to material other than wood. But this figure could rise as builders seek to avoid being associated with the negative publicity associated with CCA-treated wood, which is being phased out as a building material. Even before the CCA (chromated copper arsenate) controversy peaked, studies were projecting a doubling of demand for wood/plastic composite by 2005, from the 700 million pounds produced in 2000. Decking accounts for about 60 percent of this.
Wood-fiber/plastic is gaining market share because of advantages over wood and metal in terms of longevity, appearance, life cycle cost and overall value. The composite material has seen sales grow as fast as capacity can be added.
Many other products typically made from wood or metal are now available in wood-fiber/plastic: window/door components, industrial block flooring, playground structures, picnic tables, pallets, benches, fencing, marine applications and landscape timbers/edging to name a few. The low-maintenance composite is attractive, highly insect- and rot-resistant, slip-resistant and paintable. It is also stiffer than pure plastic products and can span the same centers as wood. It "works" and cuts just like wood; can be glued; and it can be fastened with the same screws, nails or staples.
The material is likely to become more common in the construction materials and demolition debris recycling stream as it gains popularity.
THE INGREDIENTS
Wood-fiber/plastic may be up to 70 percent wood material, but formulations vary dramatically. The most commonly used resin is polyethylene (PET), while other plastics involved include PVC, PP, PS and ABS. Foaming agents can be used to reduce final product density and conserve material. One common source of plastic is used HDPE grocery bags, ground to an appropriate flake size. Virgin powder PVC can be used, but pelletized resin is unsuitable. Various additives may include lubricants, colorants, binders and stabilizers.
Virtually any wood waste can be used as feedstock, including hard/soft wood, particleboard and MDF waste. Other types of fibrous waste are being used, too, such as rice hulls, peanut hulls, straw, flax and bamboo. The material is often ground to a specified particle size of 40 mesh or smaller. Sanding dust, typically 200 mesh or finer, is ideal.
Again, formulations vary radically to create the final physical specification for the end product: stiffness, specific gravity, color, etc. Even thermoplastic-capped material can be produced with a co-extrusion process and compatible resins.
Advantages of Counter-Rotating, Intermeshed Twin Screw Extruders |
• Positive displacement conveying characteristics (good for fluffy materials) • Narrow residence time distribution • Very good pressure generating capability to handle a variety of tooling • Good degassing characteristics • Good control over melt temperature • Ideal for processing heat and shear sensitive materials • High torque capability to achieve high output rates and gentle plastification at slow screw speeds. Source: ExtrusionTek Milacron —Brian Taylor |
THE MANUFACTURING PROCESS
Conical counter-rotating twin screw extruders are leading process technology in the composites industry.
The primary piece of processing equipment for wood-fiber/plastic, the extruder, must mix, heat and process the dry-blended raw material into a homogenous and consistent "melt." Critical factors include tailoring the extruder’s screw geometry to the compound, matching temperature to speed and balancing flow from the tips of the screws into the die. The functions of conveying, melting, mixing, de-volatilization, homogenization and pressure generation must be in synch for the processed material to be successfully delivered through the shape die without defects.
The dominant extruder technology in wood-fiber/plastics processing is the counter-rotating conical twin-screw machine, with more than 100 installed systems in North America. Conical twin screw extruders are ideal for conveying and pumping "fluffy" feedstocks, such as wood-fiber, due to the seal developed in the screw intermesh and the inherent compression.
Screw to screw, the flights have the same geometry and are slanted in the same direction in the nip region, reducing the open spaces between the flights and minimizing leakage from one screw channel to the next. Incoming material is conveyed away from the nip of the screws, around the flights, converging at the bottom of the screws. In effect, the twin screw extruder is a positive displacement pump that conveys material at a fairly low rpm with low compression, minimal shear and low frictional build up.
Conical twin extruders are characterized by gentle plasticizing that ensures strict control of residence time, in conjunction with excellent pressure generation. The conical twin is also one of the most energy efficient extruders.
The conical twin’s natural compression, created by moving the material from a large diameter to a smaller diameter, facilitates the dramatic bulk density change during the transformation from feedstock to melt. The smaller diameter at the screw tip reduces the area that the melt can push back against, thus generating substantially less back pressure while pumping highly viscous material into the die.
Operating conditions are also typically very stable with the conical twin. The extruder will run without adjustment for days at a time once the desired settings are reached, resulting in a highly consistent melt flow with lower stock temperatures. Lower melt temperatures minimize sizing and cooling problems, and the consistent melt flow reduces problems of too much weight in one place and improves dimensional tolerance. Selection of proper extruder screw geometry is a primary consideration, and designs vary widely from process to process, user to user.
PROCESSING ISSUES
The low bulk density, poor flow characteristics and, in many cases, broad range of particle sizes make feeding and conveying wood-fiber/plastic difficult. The conical twin’s feed zone has a very large intake volume – typically 30 to 40 percent of the overall volume of the screw – to handle these feeding challenges. The natural compression from the converging screw tips is also beneficial in conveying low-bulk density materials and helps eliminate segregation of materials with varying particle sizes.
Melting is more difficult with wood-fiber/plastic composites because the wood can act as an insulator, and mixing can be more difficult in many cases due to the range of particle sizes. Large beginning diameters of conical barrels and screws maximize heated surface in the feed zone for greater melt efficiency and control.
Mixing is handled by utilizing special pre-compression/mixing zones that mix at low shear rates, minimizing fiber breakdown. Working of the material between the two screws at slow screw rpm, rather than between one screw and the barrel wall, enables mixing at low shear rates.
The positive displacement characteristic, along with the small discharge diameter and low screw rpm, allow the conical counter-rotating twin screw extruder to pump melt into a die against high head pressure, while simultaneously minimizing shear and frictional heat input. Head pressures vary from 800 to 1,500 psi for large solid products, or 3,000 to 5,000 psi for engineered profiles.
De-volatilization (returning from vapor to liquid or solid form) is a major challenge for wood-fiber/plastic composites because wood has a natural affinity for moisture. The ideal situation is to dry the wood fiber prior to blending to a moisture level of 0.5 to 1.5 percent. Higher levels of moisture can be accommodated, but it sacrifices throughput rate.
Current throughput rates for the larger conical twin screw extruders are:
• 92mm: 1100-1700+lbs./hr
• 86mm: 500-1100 lbs./hr
• 80mm: 400 - 900 lbs./hr.
Many advances have been made to improve processing of wood fiber composites, such as the twin-screw pre-heater and crammer feeder. The pre-heater is used upstream of the crammer to elevate premix temperature to 200 to 240°F.
At this temperature, steam generated from the wood fiber and plastic can be released through an atmospheric vent or a vacuum system prior to the material dropping into the vertical crammer. The pre-heater allows a higher volume screw design, and the crammer, downstream for the pre-heater, ensures full filling of the feed flights for highest throughput.
Getting started
What equipment do wood processors collecting suitable scrap for wood-fiber/plastics composite processing need to get started? Besides the extruder, here’s what else a recycler may need:
• Downstream equipment, such as calibration and gauging systems, flying saws, cooling bath, texture applicator, etc.
• Upstream equipment, such as dryer and vacuum delivery system, possibly even a ribbon blender
• A resin supplier familiar with wood fiber/plastic applications.
• Laboratory tests of your material and extrusion system to determine satisfactory product quality and throughput
• An extruder supplier with a library of successful screw geometries for wood-fiber/plastic and the ability to custom design and produce screws to meet manufacturing requirements.
The author works for ExtrusionTek Milacron in Batavia, Ohio.
Get curated news on YOUR industry.
Enter your email to receive our newsletters.
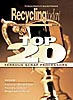
Explore the March 2002 Issue
Check out more from this issue and find your next story to read.
Latest from Recycling Today
- Hitachi forms new executive team for the Americas
- Southwire joins Vinyl Sustainability Council
- Panasonic, Sumitimo cooperate on battery materials recycling in Japan
- Open End Auto Tie Balers in stock, ready to ship
- Reconomy names new chief financial officer
- ICIS says rPET incentives remain weak
- New Jersey officials award $16.2M in annual recycling, waste reduction grants
- Linder Industrial Machinery announces leadership changes