
Every state in the country has different permits to enforce the Environmental Protection Agency (EPA) Clean Water Act (CWA). Several states even have specific permits assigned to industry sectors. In California, for instance, the Industrial General Permit (IGP) is issued by the State Water Resource Control Board (SWRCB) and covers most manufacturing, materials handling and recycling facilities. Additionally, areas in California’s Santa Ana Watershed have specific requirements for scrap metal recyclers.
In several recent discussions, the SWRCB has indicated that future IGP inspections will be more detailed. In particular, the handling of miscellaneous, nonstormwater liquids, as well as handling and controlling exposure to stormwater by the metals themselves, were noted as critical areas of emphasis.
In California, the IGP requires permit registration documents, required sample data and compliance documents to be reported through a public system. Therefore, it is critical that uploaded documents accurately reflect the standard operating procedures on the permitted facility. It’s also important that facilities maintain clean and managed facilities.
Litigation pressures
Using tools like Google Earth or Bing, environmental organizations (e.g., Heal the Bay, Coast Keeper, Surf Rider and others) are able to virtually “visit” multiple facilities from the comfort of their desktops. Examples of this type of “inspection” now abound in legal briefings. The image above is an example of photographs that could be used in legal briefings to support a case against improper stormwater management of a facility in Southern California. Images like this are freely available on the internet.

The 60-day notice of intent to sue in this instance included photos similar to the photo above to demonstrate how the site “failed to develop and/or implement best management practices (BMPs) that achieve compliance with best available technology economically achievable and best conventional pollutant control technology (BAT/BCT).”
The filing specifically states, among other issues, that:
- “Photographs show a lack of adequate BMPs at the facility, including large piles of scrap with no covering or containment.”
- “The facility is paved and littered with debris and stained from stormwater pollutants, including oil.”
- “Sources of pollutants at the … facility are numerous, including but not limited to: scrap metal ferrous and nonferrous outdoor storage areas, scrap metal, miscellaneous machinery, obsolete equipment and used appliances, piles of turnings and cuttings; and on-site material handling equipment and forklifts. Pollutants associated with the … facility include but are not limited to: toxic metals, such as copper, iron, zinc, lead, cadmium and aluminum; petroleum products, including oil, fuel, grease, transmission fluids, brake fluids, hydraulic oil and diesel fuel; chemical admixtures, battery fluids, refrigerator and other appliance fluids, acids and solvents; total suspended solids and pH-affecting substances; and fugitive and other dust, dirt and debris.”
Although several statements provided in the suit were largely conjecture, such conjecture has proven to be effective, resulting in large fines and settlements, some exceeding $100,000.
Cost-benefit analysis
When selecting appropriate stormwater controls for a facility, owners and operators should conduct a cost-benefit analysis. For example, for the small site mentioned previously, it may make more sense to build a 25- to 30-foot tall roof for the site rather than to invest in lifetime operations and maintenance costs for implementing stormwater treatment controls for a suite of chemical constituents (metals, oils, solvents, sediments, oxygen-demanding organic species, etc.). To treat toxicants, a treatment train of appropriate treatment control unit operations and processes must be appropriately designed, installed and maintained as documented in previous studies developed for the EPA.
An appropriately sized, multiple-barrier treatment control system likely would contain trash control, sedimentation and a filter system with a series of ion exchange media followed by sorption media. These combined systems likely would cost $50,000 to $100,000 and would create an annual maintenance fee of $10,000 to $30,000. The price does not linearly correlate with property size, but costs increase as facilities get larger with larger quantities of stormwater requiring treatment.
Collecting all runoff water in large tanks to be hauled off-site to a liquids waste receiving location may be another alternative.
With the California IGP, a facility moves up in compliance level from one year to the next if it continues to exceed allowable levels. After a first year of exceedances, the facility must have a qualified industrial stormwater pollution prevention plan (SWPPP) practitioner, or Qualified Industrial Storm Water Practitioner (QISP), develop a plan for addressing the issues. QISP certification requires more than 40-hours of online training provided by the state and an eight-hour in-person training, along with two exams. This plan may include structural and nonstructural (e.g., operational) BMPs.
Following a second year of exceedances, the facility becomes a Level 2 facility and then must have a professional engineer design structural treatment controls to address the issue or provide a justifiable cost-benefit assessment if the capital improvements to meet the numeric levels cannot be implemented within the next year. In either case, a plan must be developed for meeting levels in the future.
Compliance options
This scenario creates quite a dilemma for facility owners. What should an operation do to comply with regulations and avoid costly legal fees and fines?
Using tools like Google Earth or Bing, environmental organizations (e.g., Heal the Bay, Coast Keeper, Surf Rider and others) are able to virtually “visit” multiple facilities from the comfort of their desktops.
Operators have several options:
- Do nothing (which is not recommended). You could try to fly under the radar and hope that you aren’t fined or sued. The costs of doing this are:
- $0 (if you’re very lucky);
- up to $10,000 per day (if the regional board decides to apply the full penalties allowed); or
- $10,000 to $100,000 (or more if you are sued).
- Build a roof to cover your facility. Hire an engineer to design the structure, get a building permit and cover your facility so rainwater does not enter your industrial work areas. This apporach often is the best alternative for small yards.
- Costs for roofing vary by robustness in design. Simple tarp-style covers may suffice in some cases, pre-engineered hangar-style fabric covers are available and brick and mortar walls and roofing can be used. It is best not to use a galvanized roof as they can leach zinc and other heavy metals.
- Compliance costs are only $200 per year for a No Exposure Certification once there is no exposure to stormwater.
- Collect all the stormwater from your facility in storage tanks/vaults to be hauled off-site by a disposal company. This option is limited by on-site spatial constraints for the storage tanks (above or below ground) and by the costs of the storage facilities.
- Collect stormwater and treat it to meet the standards listed in the IGP. This option is limited by spatial constraints, capital costs for new facilities and on-going operations and maintenance costs for the treatment controls (may include routine vault sediment/debris removal or replacement of filter media). Larger facilities should strongly consider this method as it may also provide long-term cost advantages.
The recommended alternatives all come with additional costs; but, with proper planning, most facilities can find a way to avoid fines and lawsuits. Implementing one of these alternatives also lets an operation reposition itself as a safe, clean and respected industry leader that values the environment and does its part for the community and the economy.
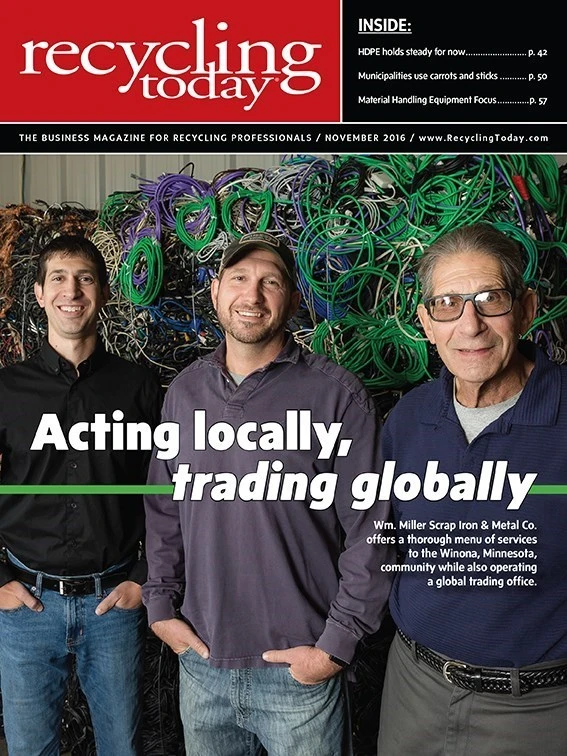
Explore the November 2016 Issue
Check out more from this issue and find your next story to read.
Latest from Recycling Today
- Magnomer joins Canada Plastics Pact
- Electra names new CFO
- WM of Pennsylvania awarded RNG vehicle funding
- Nucor receives West Virginia funding assist
- Ferrous market ends 2024 in familiar rut
- Aqua Metals secures $1.5M loan, reports operational strides
- AF&PA urges veto of NY bill
- Aluminum Association includes recycling among 2025 policy priorities