Purchasing the right baler for an application or set of tasks is a terrific first step, but it certainly is not the end of the story.
The owner and operators of a baler can take a wide variety of approaches to properly using and maintaining their capital investment.
Buddy Himes, a long-time recycling equipment service technician who now owns and manages Himes Service Co., Waco, Texas, has seen best practices, worst practices and everything in between.
In an interview with Recycling Today Editor in Chief Brian Taylor, Himes provides some sound advice for owners and operators on how to maintain their baling equipment and ideally avoid the types of problems that cause operational misery.
Recycling Today: What are common causes of catastrophic baler failure? Buddy Himes: The most common thing is lack of attention or no attention to preventive maintenance (PM). If the equipment is checked whenever the schedule calls for, then the chance of having a catastrophic event happen is limited quite a bit. It really takes away a lot of that risk.We do PM schedules on equipment [and] run quarterly, semi-annual and annual checks on equipment around the country. Of course there is a cost to that, but the good side is that we have found that [our customers] are having a lot less breakdowns and severe motor failures and pump failures—for lack of better definition, blowing the baler apart.
We can see that a baler may really be due for re-line or about to blow an O-ring. Pay attention to [the baler] and you can’t imagine much money that will return to your pocket by avoiding downtime.
Along with that, a lot of the manufacturers, and some of us in the aftermarket, are putting more and more emphasis on a PM program linked to [built-in] computers. That lets the operator know in the morning that it’s time to check something in particular. The computer reminders, we have found, are good to keep in mind when you’re buying equipment.
Some of the manufacturers have incorporated a dual system. If it’s left to one person, and [the system] alerts him to, say, check the oil filters, there is a way to get around that if he needs to keep running—and so it never gets done. This was really brought home by company owners and supervisors. They want that notice at the same time and want a supervisor to be required to enter a code to clear the baler to keep it running. So, only the supervisor can go around that warning.
RT: How can operators know that they are putting too much stress on their baler’s cylinder or chamber? BH: I think that falls into the category of operators being well versed in what they are supposed to be doing. And then, also, the tolerances of the baler come into play. If you let the wear tolerances get out of shape and you keep pushing the baler, that’s where you get into problems.Additionally, the operator needs to know what that equipment is capable of doing and not go beyond that. On the metal side, if the manual says you can only do up to 1/16-inch-thick aluminum or steel, don’t try to run ½-inch material.
I’m an advocate of, when installing baler, to present a list of things the baler cannot do. If it’s not meant to do, say, demolition material, then that baler is not going to make that material any more dense. They need to know what the limits of the baler are and follow them pretty closely.
RT: What are some common mismatches you see between an application or material and baler style? BH: If you try to bale plastic in equipment not designed for it, you’re going to get bad bales that are not good for shipping. Two-rams seem to have a better time processing plastic, but paper is often better off heading to a single-ram baler.Just from a housekeeping situation, if you’re baling cans in an extrusion type baler, you’ve got a lot of holes in there, and these cans just come out.
Many single-rams don’t have shear blades, just a press. Those aren’t best for aluminum and light metals, because there is no way to shear it.
RT: What are the negative consequences of inadequate hydraulic system maintenance? BH: We can tell you a lot about that. Right now, we seem to run into a lot of hydraulic problems out there in the field. Operators have not been checking their fluids. They should take a sample of that fluid and send it to a lab every six months. Change those filters when they are supposed to be changed!Pumps are going to wear and produce metal flake. If you have metal flakes building up in the fluid, they will start getting into valves and into vein pumps. Now you start losing pumps. They can go from $2,000 to $6,000 apiece. One customer we know had these problems—they were losing five pumps per year at $3,500 per pump. They realized what they needed to do and they haven’t lost a pump this year.
The cost of that problem is almost as bad as letting baler blades get out of spec. Right now, a 16-inch cylinder costs between $60,000 to $80,000. That’s not the cost of labor or downtime—just the part. Valves are from $200 to $300 apiece. You start replacing those and you run into costs, plus lose two or three days to downtime.
Many older balers, the parts are harder to get a hold of at all. This is true for machines going back 25 or 20 years.
We have customers who have never changed a pump in 20 years. They send that oil out, they get it tested and they run external filter systems on them once every four or five months.
With internal filters, the oil normally filters out to 10 microns. An external filter buggy can go through a 5-micron filter. That takes out even more than what the manufacturer specifies. It keeps the oil a lot cleaner and helps them keep the pumps a long time.
RT: What are the negative consequences of poor housekeeping, operating a dusty and dirty baler? BH: All your balers are normally hooked up with a cooling system. If you start clogging up the vents, you start heating the baler up. With the breathers in the hydraulic tank and pumps, if those filters are not kept clean and changed regularly, then that dust can start bypassing into there. You get dirt in the system [and] right back into hydraulic fluid problems.If you wash a car engine regularly, it will last longer. The thinking is very similar. You don’t want dirt to act as insulation in a hot environment.
RT: How often should operators check the shearing blade gap distance, and why is that important? BH: That is absolutely important. Here’s an example. On an old Mosely machine that makes mill-sized OCC bales, the blade gap should be less than 1/16 of an inch.The face of that platen was developed for a certain psi pressure. The pressure is meant to be spread over the face of that platen. If you don’t keep that shear blade tolerance, you get the gap up to ¼-inch in size.
If you get a piece of material wedged in there—a 1-inch-by-1-inch piece—you’ll get all that pressure transferring to a 1-inch-by-1-inch space. Then something’s got to go. You’re going to blow the [chamber] floor out and push it right down. That’s a very costly repair job. Or if the blade above is mounted on an 8-inch thick bar above, you can bend or break that, and you’ll have to replace that.
To replace things like this, you’re in the $40,000 to $50,000 range. It’s extremely labor intensive.
Without the right clearance and good sharp blades, you’re making the hydraulics heat up and work tremendously hard. That’s breaking down the hydraulic fluid and then hurting the pumps and other components.
When we use a thermostat to check for hot spots, we’ll notice that a shear blade gap can cause components to operate 40 to 50 degrees above what they would normally operate at, say going from 120 to 160 or 170 degrees. That’s going to cause damage.
Normally, a baler will shut down at about 170 degrees. If it’s still running, you start losing pumps and rubber seals and having two dissimilar metals rubbing against each other.
RT: How can an operator tell that the blade is ready for replacement? BH: With most equipment you are able to flip the shear blades. The hardest material on the blades is paper. Paper will dull shear blades very quickly. When those blades get rounded, instead of cutting material, you mush it. Then, shear force is pulling it apart, and you get hydraulic shock. You can hear it bang really loud, and the pressure is so great you can actually lift the baler off the ground.Seeing visible chunks out of the blade is certainly a sign that it’s time to switch the blades out. In computerized PM programs, they give you a regular time to check the blades.
RT: What qualifications or skills should a baler maintenance person possess? BH: You need someone with kind of a general background. Someone with a little mechanics knowledge who can maybe weld a little bit, has some hydraulic background and some electrical background. It doesn’t take a degree in any of those, but some knowledge of all of them.I always suggest that they send this person to the baler manufacturers’ school or class that they might put on. They will identify all the parts of the baler, so if there is a problem to call in, he’s not talking about "the big blue thing next to the red thing," but the valve next to the manifold block. That helps tremendously when talking to the manufacturer or a service provider like me over the phone.
RT: How can recyclers remind themselves that a few dollars of preventive maintenance can save them tens of thousands of dollars of trouble? BH: That has to start with being able to recognize they need to set up a PM program and then follow it. The computer systems are great remainders.Most recyclers are running rolling stock and they have a list that they follow in terms of changing oil and other things at so many miles in that fleet. That list is right there in the shop.
But they don’t have that same list for the rest of the equipment—the baler, the conveyor, the trommel. That’s something we push for very hard. A spreadsheet with an alarm function is very effective.
Many baler companies have it available, and it’s an innovation that’s worth tapping into.
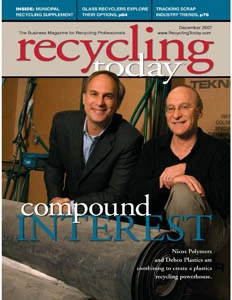
Explore the December 2007 Issue
Check out more from this issue and find your next story to read.
Latest from Recycling Today
- Sortera Technologies ‘owning and operating’ aluminum sorting solutions
- IDTechEx sees electric-powered construction equipment growth
- Global steel output recedes in November
- Fitch Ratings sees reasons for steel optimism in 2025
- P+PB adds new board members
- BlueScope, BHP & Rio Tinto select site for electric smelting furnace pilot plant
- Magnomer joins Canada Plastics Pact
- Out of touch with reality