FUEL FOR THOUGHT
Recyclers of demolition wood must weigh the options of relying on the biomass fuel market versus some of the other wood recycling options, according to the University of Florida’s Tim Townsend. The C&D recycling researcher spoke to attendees of a session at the National Association of Demolition Contractors (NADC) Annual Convention in Orlando in early April.
In an overview of hot topics and market prospects for C&D recyclers, Townsend noted that wood recyclers are involved with several of the leading issues and also face some of the most volatile markets.
Screening out wood with lead-based paint (LBP) and chromated copper arsenate (CCA) are among the issues facing wood recyclers. Both of their leading markets—the wood fuel and mulch markets—are unwilling to tolerate high levels of either LBP or CCA. Fuel users want to keep their emissions clean, while mulch vendors do not want to risk exposing their customers to contact with the toxins.
Townsend says he does not see any markets for wood supplanting these two leading markets, although in the new construction process some contractors have been grinding their scrap wood on site and using it as mulch and ground cover.
Wood fuel markets can be volatile, with recyclers sometimes dependent on the fortunes of one major regional consumer.
Landfill operators who do not want the unpleasant odors arising from scrap drywall may help spur the gypsum recycling market. Townsend noted that recycling loops for the material have been created in the Pacific Northwest, with scrap drywall used by drywall manufacturers, by Portland cement makers (who can accept up to 5 percent gypsum content) and by farmers seeking to enrich the calcium content of their soil. At some facilities, the scrap paper portion of scrap drywall is added to compost piles.
Recycled concrete and asphalt markets remain stable in most regions, although these markets could be spurred on if more states begin to develop specifications for using recycled aggregates in highway applications, Townsend noted.
By volume and weight, finding markets for soil and other "fines" remains a priority for C&D recyclers. Some recyclers are marketing their fines as a fill or cover product called recovered screened material (RSM). This product is generally not dense enough to be used as fill for construction applications, said Townsend, although it is acceptable for embankments, berms and as alternative daily landfill cover.
ALBERTA TO GET BIOMASS PLANT
Canadian Gas & Electric Co. (CG&E), Calgary, Alberta, is reportedly moving forward with the construction phase of a wood-fueled power plant in Grande Prairie, Alberta.
The company was originally prepared to commence construction on the 25-megawatt biomass plant in the spring of 2002, but is just now getting underway with construction.
According to the CG&E Web site, www.canhydro.com, the plant will use Canadian Forest Products Ltd. (Canfor) wood waste to generate both electricity and steam for use in two nearby lumber mills.
CG&E has had as a goal to contract for the sale of up to 100,000 megawatt hours annually, which represents approximately 50 percent of the anticipated operating capacity, to third parties prior to construction starting.
CG&E decided to contract the additional power in order to reduce the project’s exposure to Alberta spot power prices, which have been highly volatile over the past two years.
BOOK TOUTS 'RESTORATION ECONOMY'
Renovation, restoration, building material re-use and C&D materials recycling are portrayed as a massive and growing industry in the book, The Restora-
tion Economy, authored by Storm Cunningham, editor of a quarterly journal devoted to the subject.
According to Cunningham, $1 trillion worth of renovation and restorative activity may be taking place annually on a global scale already, but building renovation and site redevelopment are not perceived as one connected industry.
Cunningham’s book covers environmental topics such as watershed restoration that are fairly far removed from using recycled aggregates at urban building sites. But he makes the case that the two are connected in the same way that land clearing contractors and real estate companies both perceive themselves as land developers.
In his book, published by Berrett-Koehler Publishers Inc., San Francisco, Cunningham makes a case that popular support has already shifted away
from the new development of farmland and forested land toward the restorative development of existing buildings and existing plots in settled areas.
The book carries an endorsement from former Indianapolis Mayor William Hudnut III, who says it "points us toward restorative development as a smarter, more economically compelling alternative to sprawling new development."
The author stresses economic and business-related reasons why the trend
is taking place. The book’s full title is The Restoration Economy: The Greatest New Growth Frontier: Immediate & Emerging Opportunities for Businesses, Communities & Investors.
Additional information on the book can be found at www.berrett-koehler.com.
SHINGLES ON THE TABLE
Information on research, handling techniques and case studies invovling recycling asphalt shingles were all part of the Second Asphalt Shingles Recycling Forum, which took place April 13-14 in Minneapolis. The event featured several speakers who discussed issues facing the industry today and also allowed the more than 100 participants to talk to their peers from across the country.
The focus of the presentations was mostly on using recycled shingles in hot-mix asphalt, although other end products were also discussed. The forum was sponsored by the Minnesota Department of Transportation (MnDOT), Minnesota Office of Environmental Assistance, U.S. EPA Region 5 and the Construction Materials Recycling Association. It was partly funded by the Recycled Materials Research Center (RMRC), Durham, N.H.
Among the speakers was Jeff Melton of RMRC, who reported that the barriers to asphalt shingle recycling are both real and perceived, but that quality control and quality assurance on the parts of the shingle processor and asphalt producer are important to overcome those barriers.
Dave Newcomb, currently with the National Asphalt Pavement Association (NAPA), was at one time part of MnDOT and participated in that agency’s groundbreaking research 10 years ago on recycled shingle use in hot mix. He stated that the results, which were positive for the process, are still valid today.
He added that NAPA believes additions to hot mix, such as recycled shingles, need to meet three criteria: the end product should not be hurt by use of the waste; that use of the waste should not affect worker safety and health, nor have any other detrimental environmental effects; and the practice is economically feasible. The organization also contends that the use of the recycled debris should not be mandated.
Kent Peterson of CMRA-member Bituminous Roadways, Minneapolis, said his company is in the process of a pilot project using post-consumer shingles for non hot-mix products. But for more than five years his company has been grinding and adding shingle manufacturers’ debris into its hot mix plant. While asphalt that uses shingles is now accepted by many customers, at first he had to overcome the perception that it was a health hazard and "garbage" in the mix. He has worked to dispel these notions.
Bob Ayres of Allied Blacktop, Eau Claire, Wis., another CMRA member, shared his company’s experience using recycled shingles in hot mix. His company has only been doing it for a few years. In his operation the shingles are added at a rate of 5 percent, and using the material reduces the need for asphalt emulsion as much as 4.9 percent. With emulsion going for around $200 per ton, that can be a tremendous savings. Allied Blacktop will experiment with new mix designs, including adding shingles to make up as much as 10 percent of the mix.
Randy Williams of Roofing Recycling Center, Portland, Ore., also shared his company’s experiences using tear-off shingles in a variety of end uses. He shared the fact that Vulcan Materials has done testing on processed shingles from his site, and while the large aggregate company with hot-mix plants in his area would not divulge the results, they were positive enough that the two companies are now negotiating to work together.
Dale Decker, a consultant and expert on asphalt based in the Toledo, Ohio area, spoke on the economics of using recycled shingles in hot mix. He recommends that shingle recyclers don’t get the material too wet during grinding, as that moisture will require the hot mix plant to use more fuel to burn off the moisture, and to handle the product properly to make sure there are no contaminants in it. In general, Decker said, shingles added at a rate of five percent can save 70 cents per ton of asphalt.
Get curated news on YOUR industry.
Enter your email to receive our newsletters.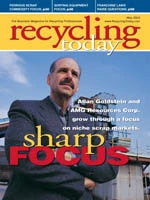
Explore the May 2003 Issue
Check out more from this issue and find your next story to read.
Latest from Recycling Today
- ReMA opposes European efforts seeking export restrictions for recyclables
- Fresh Perspective: Raj Bagaria
- Saica announces plans for second US site
- Update: Novelis produces first aluminum coil made fully from recycled end-of-life automotive scrap
- Aimplas doubles online course offerings
- Radius to be acquired by Toyota subsidiary
- Algoma EAF to start in April
- Erema sees strong demand for high-volume PET systems