
Seventh Generation, the household and personal care products company headquartered in Burlington, Vermont, describes itself as a “pioneer in corporate responsibility.” The company says it wants its products “to make a difference—from their development through to their production, purchase, use and disposal. We are always evaluating how to reduce their environmental impact, increase performance and safety and create a more sustainable supply chain.”
One of the ways Seventh Generation is making a difference is by using recycled polyethylene terephthalate (PET) and high-density polyethylene (HDPE) in its packaging. The company currently uses 100 percent recycled content PET bottles and 100 percent recycled content HDPE bottles for its dish and laundry detergents, with the exception of its 100-ounce laundry detergent bottles. Derrick Lawrence, director of packaging development at Seventh Generation, says the reason these large bottles must include virgin content is because their size and geometry require more strength than postconsumer recycled plastic provides. The 80 percent postconsumer recycled plastic in the 100-ounce bottles is complemented by 20 percent virgin plastic that is made from sugar cane and is fully recyclable.
Seventh Generation uses nearly 30 million bottles—or 16,000 metric tons of resin—annually, Lawrence says, adding that the overwhelming majority of the bottles by weight are HDPE. However, the company recently transitioned its 72-ounce hand/dish soap bottles—a popular product—to PET, so that ratio will shift slightly in the future. “Most of the weight is still in our laundry bottles, and that is all PE.”
Lawrence says Seventh Generation’s use of recycled content is “core to our beliefs.” He adds, “Our core consumers are attuned to the sustainability of our products and our packaging, so it helps us continue to attract green consumers.”
The recycled-content journey
Seventh Generation uses the following hierarchy to rank its preferences for plastic packaging: postconsumer recycled plastics, virgin plant-based plastics and virgin petroleum-based plastics. Lawrence says that by 2020 Seventh Generation seeks to convert all its packaging to use recycled or biobased materials. As of the end of 2015, the company reduced its use of virgin plastic derived from petroleum by 195 metric tons and increased the recyclability of its packaging by 20 metric tons compared with 2014, according to its “2015 Corporate Consciousness Report.”
In 2010 Seventh Generation began its journey to increase the use of recycled content in its plastic packaging from the industry minimum of 25 percent as established by the state of California. By the end of 2015, Lawrence says the recycled content of Seventh Generation’s packaging averaged 84 percent. “It started out slowly, and I would say over the last three years we have increased it significantly,” he says of the company’s use of recycled-content plastic bottles. “We made some big strides in the last three years in our packaging, especially around PE and PET.”

Lawrence says the company originally used stock bottles from a variety of manufacturers. “As we’ve grown as a brand and as a products company, we’ve developed our own custom bottles over time. As we’ve done that, we’ve consolidated that supply to just a few manufacturers. And that helped us continue to grow the amount of PCR (postconsumer-recycled resin) that we use,” he says. “We tend to focus that development where manufacturers are comfortable using higher levels.”
Lawrence says Seventh Generation gets most of its bottles from two major suppliers, and it also has three to five minor suppliers.
When it comes to the company’s plastic packaging, “It’s not just about bottles for us, though those are the things people talk about the most,” he says. “We have made big strides in our closures as well.”
Lawrence says most of Seventh Generation’s closures are made from polypropylene (PP) that contained 50 percent recycled content as of 2016. “By the time this article comes out in 2017, we will be using 100 percent PCR PP for both the spouts and the closures that are in our laundry detergent bottles,” he says.
The company has been able to increase its use of recycled PP as the supply of that material has increased, Lawrence says. “PP historically for us has been a difficult material to get a good quality supply of,” he says, noting that small parts often are made from this resin and that these items generally are not captured at material recovery facilities (MRFs) but instead end up in waste residue.
In addition to the growth in recycled PP supply, Seventh Generation has begun to focus its attention on this resin as it has achieved its recycled-content goals for PET and HDPE, Lawrence says.
Difficulties encountered
Lawrence says converting to 100 percent recycled HDPE bottles presented more challenges than converting the PET bottles. “With HDPE, through the extrusion blow-molding process and the nature of the material we get, in general, the larger the bottle, the more stress-crack issues we have,” he says. “That is why some of our larger bottles include either virgin petroleum [plastics] or, in the case of our 100-ounce laundry bottle, a virgin PE made from sugar cane.”
Lawrence says that while PET hasn’t been a challenge from a stress-crack standpoint, clarity has been an issue. Seventh Generation addressed this by researching a number of suppliers and test molding a variety of recycled resins to see the variation in color. “We’ve gotten to a point where, on a shelf by itself, a consumer might not notice the difference—it’s a bit grayer than a virgin bottle. If you put them next to a virgin bottle, you might notice the difference. But for our consumer, it hasn’t been an issue.” He adds, “We tend to wear those differences as a badge of honor.”
“It’s not just about bottles for us, though those are the things people talk about the most. We have made big strides in our closures as well.” – Derrick Lawrence, Seventh Generation
Seventh Generation spent a lot of time early in the transition process working with HDPE resin suppliers and blow molders to reduce color variation, gels and black spots, Lawrence says, adding that those issues have been reduced significantly over time. “That was an issue early on in using PE, which I think is part of the reason some companies have continued to stay at really low levels. We spent lots of time with our raw material suppliers to get to a specification for us that eliminates most of those issues: gels, spots and color variation.”
Recycled HDPE generally cannot be dropped into existing processes and designs with the same results as virgin material, he says. “There are design considerations when using postconsumer material we have found that help us to push the envelope in how much postconsumer material we can use.”
The company’s suppliers have been responsive to working with Seventh Generation on its recycled content goals, Lawrence says. “We tend to work with people who value our business and with incumbent suppliers who would like to retain our business, so they have been very happy to help us along the way.” He adds, “We have been with some of these suppliers for quite a while, and our business has grown significantly, and so has theirs.”
Lawrence says his team visits the company’s resin suppliers at least once annually to see what they are working on and whether the quality of the material can be enhanced. His team also visits the blow molders that supply Seventh Generation at least a few times per year.
While Seventh Generation has not encountered concerns pertaining to the quality of the recycled resins used in its packaging, Lawrence says the company’s suppliers have said they need to search farther and wider to find material that meets quality specifications. “They work with different MRFs across the country to get the best quality of starting material that they can,” he says. “The thing with single stream is that it increases the quantity but reduces the quality, and they continue to work through those issues, but it hasn’t caused any issues in our supply or the quality of our material—or the cost.”
Supply consistency
Despite the stagnant recycling rates for PET and HDPE bottles, Lawrence says Seventh Generation’s suppliers have not had issues sourcing adequate volumes of recycled resins for bottle production. However, he adds, “With PE, we’ve had periods of interruptions in supply where we have still managed to obtain enough to produce our bottles. But there have been ebbs and flows in that material depending on who is coming into or out of the market.” Industrial pipe manufacturing can be one such disruptor to supply.

These ebbs and flows in demand for HDPE can be influenced by the price of PCR relative to that of virgin material, says Lawrence.
While PP generally has been in short supply, that may be changing. “That material is actually in the system,” Lawrence continues. “It’s just a matter of them getting it sorted and cleaned and processed.
“For a lot of those bottle processors, it’s coming in already as closures,” he continues. “As they sink-float PET, they get that [PP] out. … There have been some consortiums of companies saying they will buy PCR PP if there is more supply, so I think finally the industry has heard that and is starting to bring more material onto the market.”
Using recycled content can provide more stability from a pricing standpoint as well, Lawrence says. “It gives us a little more consistency in cost of supply. We are not subject necessarily to the volatility of the market; we are to some extent, but not to the high peaks and valleys of the market as much,” he says. “If a PE converter’s plant catches fire, and the price of PE spikes around the world, we are offset from that a little bit. We’ll see it, but there will be a time lag, and that spike is not as high typically. Although the price of PCR tracks with virgin, it doesn’t track directly to it.”
Keeping end of life in mind
One of Seventh Generation’s goals is to have all its packaging be widely recyclable or compostable by 2020. “As a rule, we have to keep that in mind as we develop new products,” Lawrence says.
The company was one of the first to adopt the How2Recycle Label guidelines from the Sustainable Packaging Coalition, Charlottesville, Virginia. The labeling system seeks to reduce confusion for consumers by offering clear instructions on how to recycle packaging after its use. Each package or package component is labeled using one of four categories, according to the kind of plastic it contains:
- “widely recycled” (60 percent or more of the population has access to recycling options for the specific plastic);
- “check locally” (20 percent to 60 percent of the population has access to recycling); “not yet recycled” (less than 20 percent of the population has access to recycling); and
- “store drop-off” (plastic bags and films widely recycled at retail locations).
“We are big proponents of that program,” Lawrence says of the labeling system.
Because of the company’s focus on supporting recycling, the biobased plastic Seventh Generation uses is fully recyclable using existing infrastructure. “It is molecularly identical to PET and it is not a contaminant in the process,” he explains. “We have shied away from nondrop-in biobased material for that reason.”
While Lawrence says polylactic acid- (PLA-) based plastics, which are biodegradeable, “can be great materials in the right instances,” he adds that Seventh Generation avoids them because of its goal to maximize the recyclability of the company’s packaging. “It’s also extremely important for us as a consumer of PCR that there is material continually coming into the system that we can use. If we are not designing with recycling in mind at the end, we are not doing our part in that circle of material,” Lawrence says.
For more information: Seventh Generation, 800-211-4279, www.seventhgeneration.com
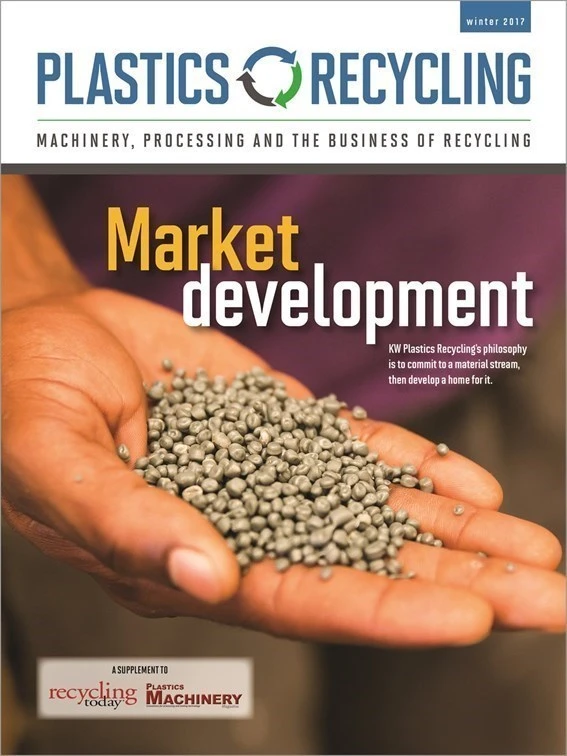
Explore the February 2017 Plastics Recycling Issue
Check out more from this issue and find your next story to read.
Latest from Recycling Today
- Aqua Metals secures $1.5M loan, reports operational strides
- AF&PA urges veto of NY bill
- Aluminum Association includes recycling among 2025 policy priorities
- AISI applauds waterways spending bill
- Lux Research questions hydrogen’s transportation role
- Sonoco selling thermoformed, flexible packaging business to Toppan for $1.8B
- ReMA offers Superfund informational reports
- Hyster-Yale commits to US production