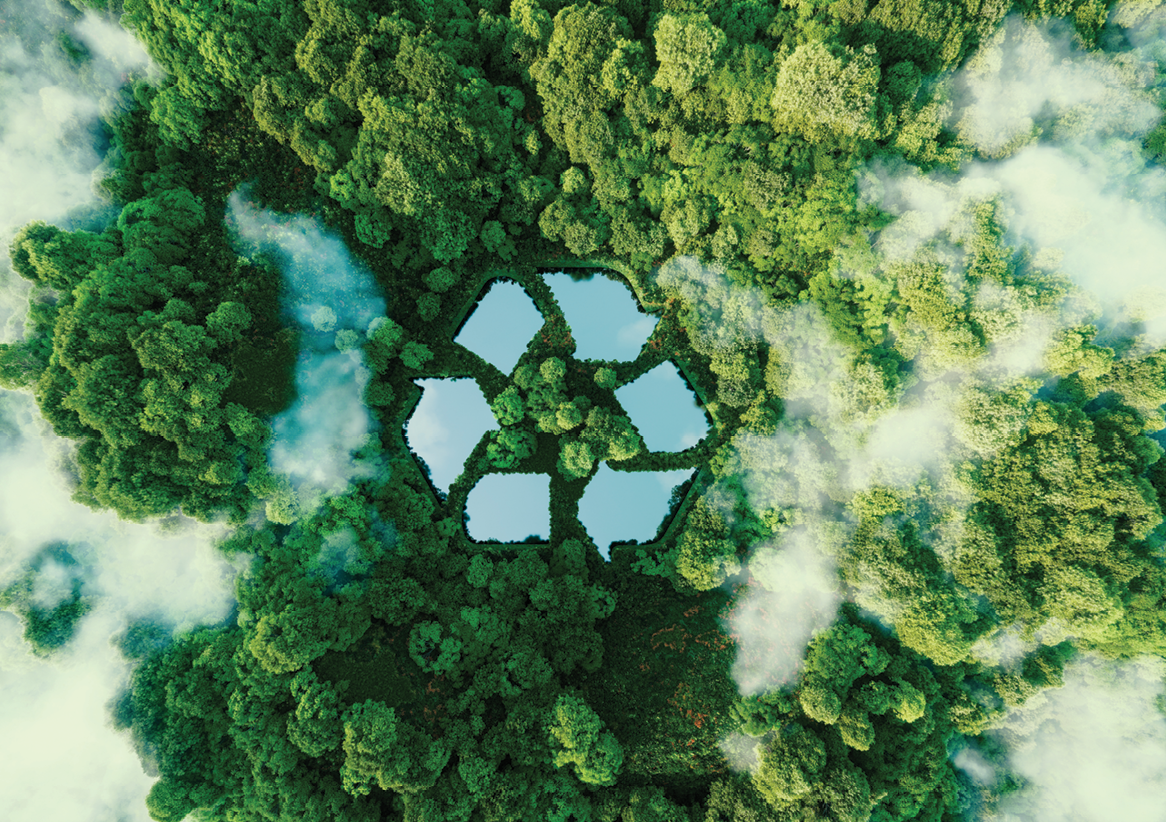
To Jon Buchan, Sawgrass Sustainable LLC truly is a technology company that happens to ply its craft in the polymers industry.
“Where we excel is in conserving our planet’s precious resources,” he says. “And, to some degree, in our own small way, helping to ensure humanity’s ability to thrive into the future.”
Sawgrass began in 2016 as a textile recycler specializing in processing nylon and polypropylene (PP) into fiber and pellets. The company is headquartered in Lafayette, Georgia, with additional facilities in Dalton, Georgia, and Scottsboro, Alabama.
As the years passed, competition for those feedstocks grew, and Sawgrass Sustainable used its technological capabilities to pivot.
By its fifth year, the company started to work with large injection molders to formulate its resins with other postconsumer and postindustrial plastics, such as high- and low-density polyethylene, or HDPE and LDPE; high-impact polystyrene, or HIPS; acrylonitrile butadiene styrene, or ABS; and polymethyl methacrylate, or PMMA, for example— materials that could be considered hard to recycle.
Sawgrass operates advanced mechanical recycling and extrusion lines and uses traditional methods to sort material, but the company also is developing a hybrid of mechanical and chemical processing that occupies a smaller footprint and could open up new feedstock sources.
Additionally, Sawgrass continues to develop polymer additives and bioreinforced resins that incorporate fillers such as coconut fiber, hemp fiber and cellulose, among others.
Those innovations are the result of Sawgrass’ commitment and considerable investment in research and development (R&D).
“We consider ourselves a technology company now, and a lot of that is driven from the fact the typical feedstocks that used to be plentiful [are less so],” Buchan says. “As more and more of these very large-scale chemical recyclers have come online, they actually compete with mechanical recyclers for the same material, so we’ve had to continue pivoting.
“We’re very R&D-focused. We’ve had to pivot a bit because what we’ve seen is the world is changing in regard to the commonly available materials that we all used to know and love as recyclers.”
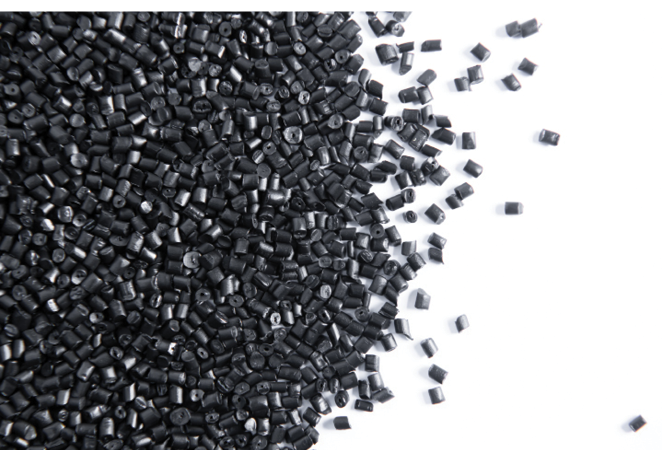
Diverse offerings
Sawgrass employs more than 80 people across its three facilities and processes postindustrial and postconsumer materials sourced from what it calls “overlooked” streams, such as flexible packaging, automotive textiles, industrial fabrics like carpet, health and hygiene and traditional textile manufacturing.
The Lafayette facility primarily focuses on recycling nylon 6, nylon 66 and PP, and turns some textile material, such as yarn, back into fiber. More recently, though, the plant has been regrinding automotive parts.
The Dalton location, opened early in the company’s development, serves as a sales office.
Sawgrass expanded into Alabama early in 2024 with the acquisition of automotive plastic recycler Carpenter Materials Group, which gave the company 170,000 square feet of additional extrusion space.
The company operates three divisions: material transformation (MTD), specialty chemicals and additives (SCA) and masterbatch and compounding (MCOM).
MTD represents Sawgrass’ more traditional recycling operations, which include bringing in scrap and turning it into pellets. The company also offers compounding and pre- and postblending services.
Sawgrass uses optical sorters equipped with artificial intelligence to sort most of the materials it procures as well as hand-held near-infrared (NIR) spectroscopy devices to sort textiles like yarn. After they are separated by resin, the plastics are shredded and agglomerated before being fed into the company’s seven extrusion lines outfitted with inputs that can infuse additives when required.
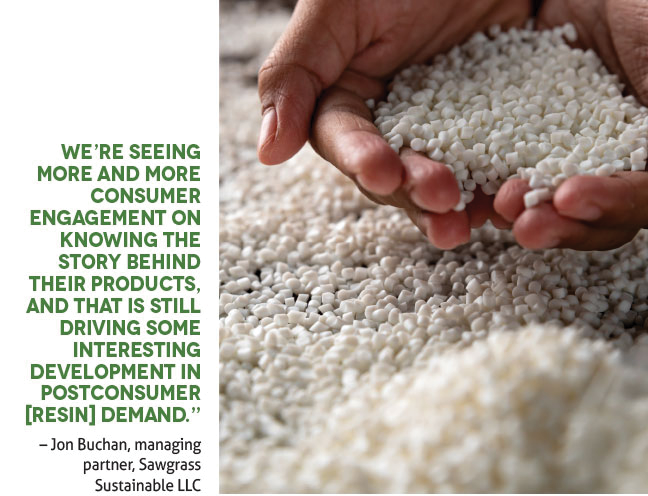
“That’s where we came from, and it’s still an important part of our business,” Buchan says of the MTD division.
The other two divisions represent Sawgrass’ entry onto roads less traveled.
Through its MCOM division, Sawgrass takes recycled biological components, like cellulose and other materials, to make resins for use by injection molders.
“A lot of this is going into automotive,” Buchan says, adding that MCOM also is making sustainable masterbatches that allow other compounders to use organic materials without “all the fuss and hassle of having to deal with that.”
Buchan notes that with some automotive companies setting recycled-content deadlines for various components, Sawgrass is poised to help them with its ability to provide recycled-content biobased resins for what he calls “automotive appearance parts,” which carry aesthetic appeal.
“The consumer now wants reinforcement that there is a natural element [that they can see in the vehicle],” he says. “That’s a change in consumer habits. What we’ve seen for so many years is when we make a biocomposite, [automotive manufacturers] didn’t want to see any wood in it, [for example]. They wanted it hidden. And now, all of a sudden, we’re getting strong feedback, and we’ve been working on systems that allow the right type of cellulosic dispersion on the surface while still creating interfacial adhesion with the polymer that allows it to not be degraded.”
Buchan says biobased fillers, whether in the form of coconut or walnut shell, hemp fiber or cellulose, tend to degrade the polymer over time, but Sawgrass is working to create systems for compounders and injection molders that will stop that degradation.
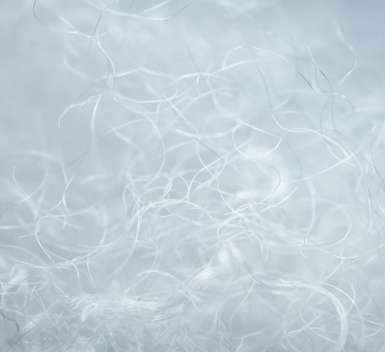
Then, there’s the SCA division, which represents a new frontier for the company. Buchan says Sawgrass is creating processing aids based on materials that typically are landfilled, such as multilayer films from the packaging industry that include various cohesive and adhesive liners, and single-use pharmaceutical products.
The company is merging elements of chemical and mechanical recycling into a processing line that can fit into a smaller space than those traditionally used in large-scale facilities. Buchan says these “microfactories” can be placed near large feedstock sources and come online within three months, providing Sawgrass with materials that can go back into circular initiatives.
Buchan says these microfactories will be sold through distributors and provide a 100 percent-recycled source of high-quality processing aids and process enablers.
“This has been a major source of our investment, and it’s really where we see a lot of our future efforts going,” Buchan adds. “We can take their material [at these plants], deconstruct it at a molecular level and then offer them back to [customers], so it promotes circularity.”
Added benefit
Recently, Sawgrass developed a life cycle assessment (LCA) solution for its customers that closely tracks each material stream the company works with.
“In the LCA, we’re looking at all of the things that move the dial,” Buchan says. “We’re looking at what happened to the material before we started [with it]. We look at what we pay for it. … What we’re looking for is the predisposition or likelihood of that material ending up in an end-of-life scenario and our ability to interrupt that move toward the grave, if you will. Everything in every one of our streams gets its own score, and then we even look at the transportation of the material, how far it’s got to move, and then we put all of it back into an online portal” that is viewable by the customer, he says.
The service allows Sawgrass customers a transparent view into what’s happening to their material and even tracks carbon emissions generated or saved, down to individual truckloads.
“This is a very important piece of what we do for a lot of our customers, giving them the transparency and the ability to go in and look at all the material coming in,” Buchan says. “They can use it to drive their own sustainability [initiatives] and be able to tell that story. … As [material] is being consumed, they can literally see it and have reassurance that it’s being disposed of properly and it’s actually going back into value instead of going to waste.”
Opportunities on the horizon
Buchan acknowledges current challenges in the plastics industry, such as negative public perception, lack of educational outreach regarding recycling and the need to improve collection networks. He notes that pricing pressure continues to be a factor for recycled resins.
But, Buchan also sees bright spots. “We’re seeing more and more consumer engagement on knowing the story behind their products, and that is still driving some interesting development in postconsumer [resin] demand. We love to see that, and that’s very encouraging. That also seems to be driving a lot of our biocomposite demand and the ability to innovate and deliver solutions that work with bio or organic components. People care.”
He says the industry could see positive outcomes as extended producer responsibility laws for packaging begin to take effect in some states and are considered in others. Such laws come with recycled-content mandates, and Buchan says some brands are willing to stick by their nonlegislated recycled-content commitments even if it means tighter margins.
Sawgrass will remain a “custodian of the polymer,” he says.
“Putting so much of our top line back into R&D and coming up with intellectual property that actually matters and moves the dial on recyclables and the recyclability of certain materials is very fulfilling for us as an organization.”
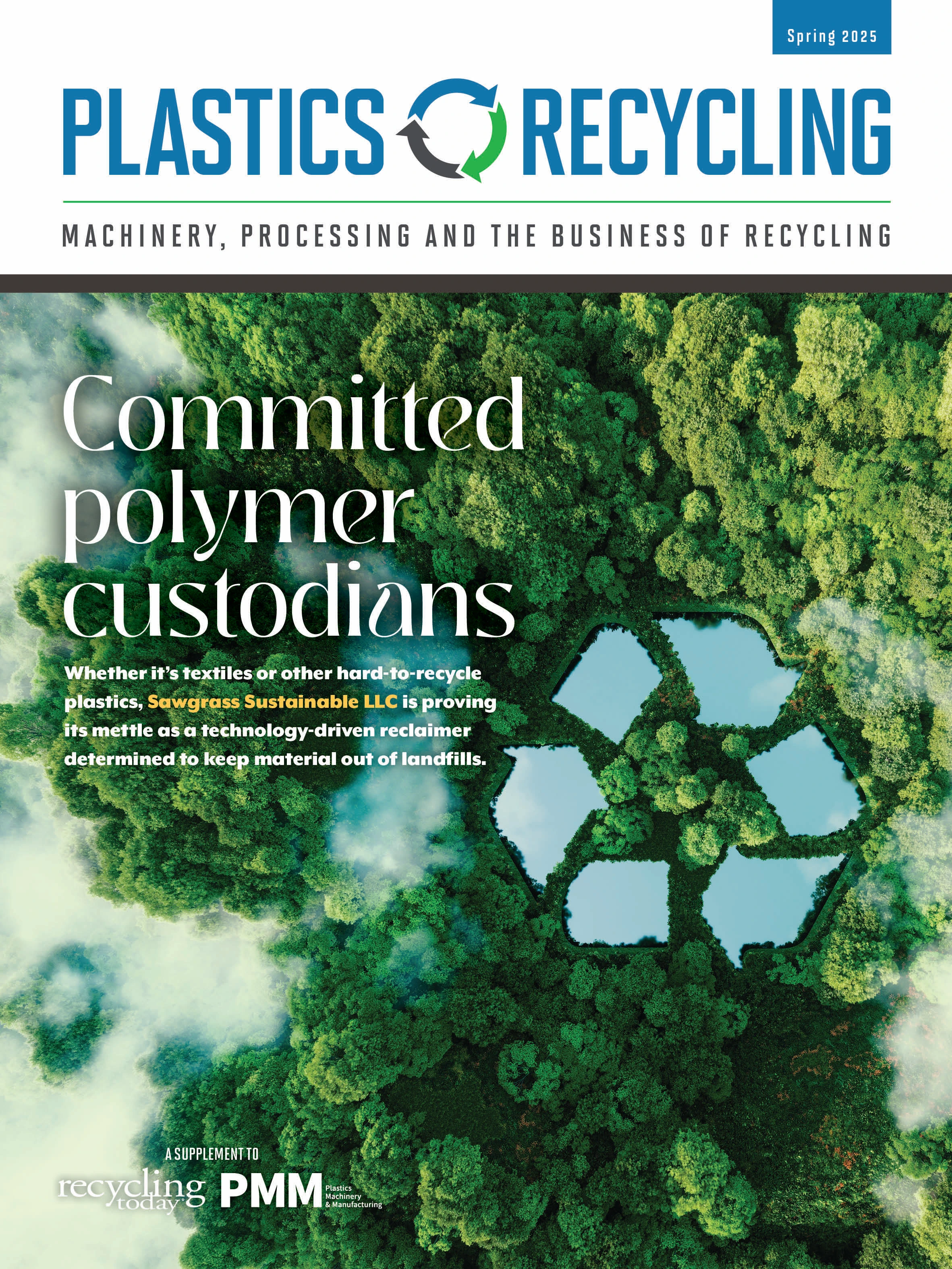
Explore the Spring 2025 Plastics Recycling Issue
Check out more from this issue and find your next story to read.
Latest from Recycling Today
- OnePlanet Solar Recycling closes $7M seed financing round
- AMCS launches AMCS Platform Spring 2025 update
- Cyclic Materials to build rare earth recycling facility in Mesa, Arizona
- Ecobat’s Seculene product earns recognition for flame-retardant properties
- IWS’ newest MRF is part of its broader strategy to modernize waste management infrastructure
- PCA reports profitable Q1
- British Steel mill subject of UK government intervention
- NRC seeks speakers for October event