
While other recyclables may be struggling in terms of generation, mixed rigid plastics represent a growth area. This category includes crates, buckets, baskets, toys, trays, thermoform containers (such as clamshells) and similar materials.
North American recyclers can thank China’s Operation Green Fence for spurring much of the growth in domestic mixed rigid plastics recycling. Add to that a dawning of uses for mixed high-density polyethylene and polypropylene (HDPE and PP) that provide end markets for recovered material, and things are looking up.
“Some of this has to do with nonbottle rigid plastic containers, specifically the stream that contains polypropylene,” says Liz Bedard, director of the rigids program for the Association of Plastics Recyclers (APR), Washington. “PP is a desired resin with good properties,” she adds.
Before China implemented Operation Green Fence in late 2013, most mixed rigid plastics recovered in the U.S. were shipped overseas. That was not necessarily a bad thing, but it also meant the domestic market did not have much infrastructure in place to reprocess this material.
Bedard says at that time, “There was not a stream of domestic PCR (postconsumer recycled) PP.”
Domestic market demand changed in response to China’s Operation Green Fence, she says. For a while after China introduced the policy, mixed rigid plastics were stockpiled in the United States. “Then we saw domestic markets start to be created,” Bedard says.
“We need to increase demand [for recycled materials] enough to justify the infrastructure required to sort and reclaim materials,” says Patty Moore, principal with Moore Recycling Associates, Sonoma, California.
Companies like Plastic Revolutions, Reidsville, North Carolina, see opportunities in reprocessing this material. Last year, the company installed a shredder to reprocess lower-grade mixed rigid bales. Plastic Revolutions’ line reduces incoming bales of material into 2-inch flakes.
“We wanted to grow our business,” Ed Handy, general manager of Plastic Revolutions, gives as the reason the company expanded its reprocessing capacity to handle mixed rigid plastics.
He says real competition exists in the domestic market for bottle bales, with people fighting for supply. “To grow, we needed to add another stream.”
Currently, when virgin plastics are flat-out cheap, manufacturers ask themselves how they can justify buying recycled material, which can come at a comparable or higher price, in some cases.
That is not to say recycled products are not moving. “There are markets for mixed rigids now,” Handy says. “I’m not saying there is big money selling them, but at least they are saving the landfill charge,” he says of the companies that are generating these bales for sale. “There are enough people processing mixed rigids that there is somewhere for them to go.”
Regarding the products it produces from mixed rigid bales, Plastics Revolutions can sell them, Handy says, adding that the soft price is not specifically related to the materials. Rather, it reflects the lower prices being seen for all plastic resins—virgin included.
Collections climb
One thing is for sure: Collection of mixed rigid plastics is growing.
Since 2009, APR has surveyed the largest city in each state, as well as Washington, annually. (These cities are not the 51 largest cities in America.) In 2009, 30 of those 51 cities were collecting some form of No. 1-No. 7 plastic containers; by 2015, 46 of 51 were.
Bedard credits some of this increase to the growth of curbside residential single-stream recycling programs. “This is what municipalities are telling their residents to recycle at the curb,” Bedard says. “Things have been changing over the years.”
The ability of material recovery facilities (MRFs) to handle Nos. 1 and 2 (polyethylene terephthalate, or PET, and HDPE) bottles is commonplace. Much of the ability to recover Nos. 3-7 plastics has to do with the footprint of the MRF. “If a MRF is pretty tight already, here’s another category to process. But if the MRF has the space to choose to segregate their material differently, it is not a problem,” Bedard says.
Moore Recycling Associates conducted a study for the American Chemistry Council, Washington, on nonbottle rigid plastics recycling. The firm found collection of postconsumer nonbottle rigid plastic increased 27 percent in 2014 compared with 2013, reaching 1.28 billion pounds. That represents an increase of 276 million pounds from 2013. The study credited this growth to the expansion of curbside residential recycling programs to include this material.
Handy has found that to be true, saying that curbside recycling programs that allow this material “have increased the amount of mixed rigids for sure.”
Domestic reprocessing capacity for this material also has increased since 2013. According to Moore’s calculations, the U.S. has more than 1.03 billion pounds per year of nonbottle rigid plastic reclamation capacity. That figure includes washing or reprocessing unwashed material directly into regrind, pellets or end products. 2014 also saw an uptick in companies reporting that they had nonbottle reprocessing capacity: 39 companies compared with 36 in 2013.
Canada is home to a least 150 million pounds of nonbottle reclamation capacity, as well.
Approximately 64 percent of the 1.28 billion pounds of this material collected in the U.S. in 2014 was reclaimed in the U.S. or Canada in 2014, the remainder was exported overseas, primarily to China.
Handy says he is aware of the degree of nonbottle rigid plastic reprocessing capacity expansion in North America since the introduction of China’s Operation Green Fence. “It used to be there were no outlets in the United States. It all was going to China,” he says.
While China’s Operation Green Fence did not kill that export market entirely, it did slow the amount of material China bought and made more of it available to reprocessors in North America.

Moore acknowledges Operation Green Fence’s role in expanding domestic reprocessing capacity but says she still believes greater end user demand for recycled materials is needed.
That’s where a company such as Procter & Gamble (P&G), Cincinnati, comes in.
Stephen Sikra, technical manager of material science and technology for P&G, says, “We are absolutely committed to using more PCR [postconsumer resin] content and have been for 25 years.”
P&G has a goal, established in 2014, to double its use of PCR by 2020, particularly in North America and in Western Europe. Since establishing this goal, P&G has increased PCR content in its packaging by 15 percent, Sikra says. Today, some P&G packaging uses 25 percent PCR, while some uses 50 and others use 100 percent.
Challenges to reprocessing
For P&G and other brand owners to increase their use of PCR derived from mixed rigid plastics, they must be able to buy quality material. But mixed rigid plastics can pose challenges during reprocessing.
“No. 1, mixed rigids have a lot of metal in them,” Handy says. These metallic items range from axles on toy cars to screws and bolts found on formed items.
He continues, “Your processing equipment has to be able to handle metal to process mixed rigids.”
Magnets and eddy current separators are obvious solutions to remove metals from plastics. However, for them to be effective, the material first must be shredded. Shredders used in this application must be able to handle the metals found in the plastics.
A second challenge is the commingled resin types. Rigid plastics are primarily a mix of PP and HDPE, though the bales also might contain PET thermoforms, low-density polyethylene (LDPE), polystyrene (PS) and polyvinyl chloride (PVC).
As in previous years’ studies, in its 2014 study Moore Recycling Associates found that PP was the largest proportion of nonbottle rigid plastics at 38 percent, with HDPE following closely behind at 34 percent. According to the study, PP, HDPE and PET showed significant increases in 2014 compared with 2013. The increases in PP and HDPE mostly were because of the increase in mixed resin rigid bales produced, whereas the increase in PET was primarily because of material reported as segregated resin and secondarily to the mixed resin rigid bale increase. LDPE, PS, PVC and “other” also increased, again mostly because of the increase in the number of mixed resin rigid bales produced from 2013 to 2014.
In the Moore Recycling Associates study, material reported as segregated resins (e.g., HDPE injected products, such as drums, buckets and crates; PP battery casings; and PET thermoforms) made up 58.3 percent of the total material reported as recycled. That figure was down 8 percent compared with 2013.
“The success of the expanded plastic recycling system depends on assurance that there will be buyers for the collected material.” – Patty Moore, Moore Recycling Associates
The nonbottle rigid plastic portion of mixed resin rigid bales, predominantly from municipal recycling programs, made up 31.5 percent of the volume reported (an increase of 12 percent relative to 2013). Prepicked rigid bales (with and without bulky) made up the largest volume of mixed resin rigid bales reported, coming in at 69 percent by weight. Recovery was up by 14 percent compared with 2013. The next largest category of mixed resin rigid plastic was “all rigid plastic (with or without bulky)” at 15 percent, with bulky rigid bales dropping to third at only 8 percent in 2014 compared with 23 percent in 2013.
Despite the variety of material that can be in these bales, Handy says, “You wind up with a product of PP with a certain percentage of PE in it, and vice versa. The clean regrind that you get out of the process is cross-contaminated with PP and PE.”
A good setup that uses the proper sorting equipment can minimize cross-contamination, however, he adds. “You can get that percentage way down,” Handy says.
But with a typical load of mixed rigid plastics bales being roughly equal proportions of HDPE and PP, sorting it completely to get a pure stream of PP and a pure stream of HDPE is “next to impossible,” he says. “You’re always going to have a product that is 85 percent PE and 15 percent PP. You have to market it that way and find people who can use it that way.”
Plastic Revolutions has been able to do that successfully, Handy says.
Moore says most U.S. reclamation capacity is for relatively clean—and often larger—PE and PP items. She says this is because that class of materials can be handled more cost effectively than small items and often do not need to be washed.
“Many buyers are seeking clean PE- and PP-based bulky rigid materials, such as buckets, crates, battery casings, storage bins and hangers,” Moore says.
Five percent of domestic reclaimers reported making mixed-resin products, such as lumber and other extruded products.
However, as infrastructure for plastics recovery grows, Moore says it is essential for all the resins found in the mixed bales to be in demand.
“The success of the expanded plastic recycling system depends on assurance that there will be buyers for the collected material,” she says.
Get curated news on YOUR industry.
Enter your email to receive our newsletters.
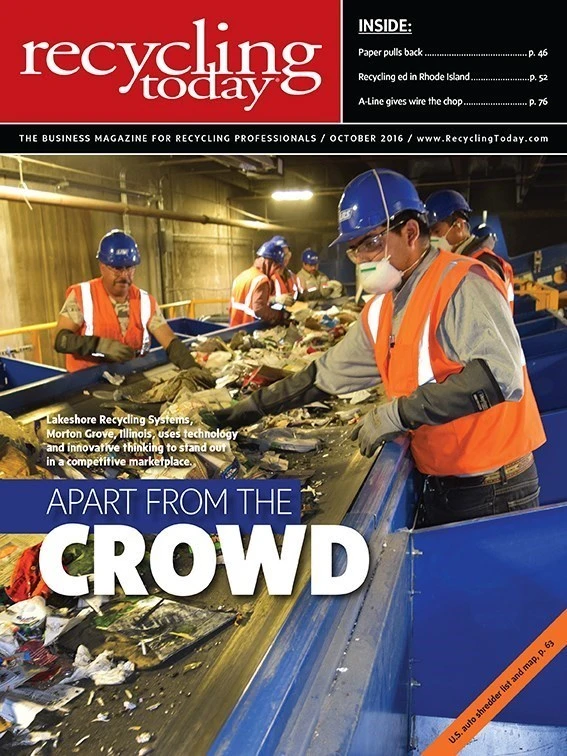
Explore the October 2016 Issue
Check out more from this issue and find your next story to read.
Latest from Recycling Today
- Toppoint Holdings expands chassis fleet
- Lego creates miniature tire recycling market
- Lux Research webinar examines chemical recycling timetables
- Plastics producer tracks pulse of wire recycling market
- Republic Services, Blue Polymers open Indianapolis recycling complex
- Altilium produces EV battery cells using recycled materials
- Brightmark enters subsidiaries of Indiana recycling facility into Chapter 11
- Freepoint Eco-Systems receives $50M loan for plastics recycling facility