
Jim [Keefe, publisher of the Recycling Today Media Group] asked me to do a high-level stage setting: where are we in terms of challenges and opportunities facing the recycling industry, specifically the plastics recycling industry.
Just two years ago I decided to step out of the company I founded—the hardest decision I ever made but probably the most rewarding because now I get to tackle a wider range of solutions all over the world, trying to figure out how to indeed close the loop and make plastics part of the circular economy.
What I’d like to do is set the stage for what are the challenges and opportunities in making this happen. I am going to do that with four questions:
- Why are we here?
- Where are we?
- Where do we want to go?
- And, most importantly, how do we get there?
ONE: WHY ARE WE HERE?
How many remember [The Graduate] from the 1960s? What was the one word of advice to this recent college graduate?
Plastics.
Whoever put that line in there knew what he or she was talking about.
You remember that line because it was funny. Who in the ’60s in their right mind would have gone into the chemical or plastics industry? It wasn’t sexy or hip.
This is another reason that we’re here. [Biddle begins playing a clip of comedian George Carlin].
“The planet will be here for a long, long, long time after we’re gone, and it will heal itself, it will cleanse itself because that’s what it does—It is a self-correcting system. The air and the water will recover,” Carlin says. “The earth will be renewed. And if it’s true that plastic is not degradable, well the planet will simply incorporate plastic into a new paradigm: the earth plus plastic.
“The earth doesn’t share our prejudice toward plastic,” Carlin continues in the clip. “Plastic came out of the earth. The earth probably just sees plastic as another one of its children.
“It could be the only reason the earth allowed us to be spawned from it in the first place: It wanted plastic for itself, didn’t know how to make it [and] needed us. It could be the answer to our age-old philosophical question, Why are we here? Plastic,” the clip of Carlin concludes.
George Carlin has a different perspective about why we are all here today, but it is all about plastic—at least this session is largely, but not entirely, about plastics.
TWO: WHERE ARE WE?
I think we’re all aware that we are on a more crowded planet. It’s a very steep rate of increase in the level of crowdedness, which leads to things like a resource squeeze. I think that’s what many of us in this room are taking advantage of with our businesses.
From many different perspectives, people see this as a problem for society [and] for businesses going forward. McKinsey is making a life consulting about it. Even the U.S. military is concerned about resource scarcity driving conflict in the world.
Why should we worry, though?
If we look at the last 100 years, resource prices overall on a basket of commodity goods fell by 50 percent.
How is that possible when the world population was growing so dramatically during that time, and we were consuming more and more stuff? How did we drive down commodity prices by 50 percent?
It’s because many of you in this room and others figured out how to do their business very efficiently.
In the last 10 years, all of that gain was wiped out and more. Now, talking to you here today it’s a little hard to get you too excited about this because I know we’re in another dip as in 2008. But how many in this room actually believe [commodity prices] will continue to go down and are not going to have this general upward trend?
I don’t think so.
McKinsey points out that there is going to be 3 billion new middle-class consumers coming on the market in the next 15 years. Three billion middle-class consumers, and they want all of the same stuff we enjoy.
McKinsey estimates that we are going to need an 80 percent increase in steel alone. And they believe we need to invest $1 trillion a year just to manage this resource scarcity issue. Even if they are off by a factor of 10, that is still a big number—and I don’t think they are off by a factor of 10.
For me, this is a problem. But, more so, it is an opportunity, particularly for those of you in this room who know how to solve this problem.
We know there are financial and environmental consequences to extracting more [metal and ores] from a finite supply. It’s getting harder to find the stuff, in the ground at least, and therefore the costs are going up in general.
How do we solve this problem? How have we solved this problem?
Many of you in this room are responsible for the solution to this problem by reusing these minerals and not forcing them to be extracted from the planet to meet this growing demand.
How do plastics compare with other materials?
Most plastics today are made from petrochemicals or natural gas. Today it feels like we have an abundance of those raw materials, but we are going to more extreme measures to get to that remaining abundance in the planet.
Using recycled plastics can save between 80 percent to 90 percent of the energy needed to make them from virgin material. We can save 2 tons to 4 tons of CO2 (carbon dioxide) per ton of virgin produced. And recycling keeps plastics from ending up in harmful places—one of the things I’ll talk about in a moment.
In 2014 Europe recycled about 6.6 million tons of plastic—that’s a lot of plastics to recycle, but it is only about 14 percent of their annual use.
“The earth doesn’t share our prejudice toward plastic. Plastic came out of the earth. The earth probably just sees plastic as another one of its children.” – George Carlin
The U.S. recycles less than 10 percent [of its plastics] by estimates of the U.S. EPA (Environmental Protection Agency).
Plastic has traditionally not been recycled as much as metals. Many people think that is because metals—steel in particular—have a very high value compared with plastics; plastics are a throwaway, worthless material.
But, plastics are actually several times more valuable than steel on a price per weight basis, and some plastics [are] considerably more [valuable]: 10 times more.
If there is so much of this darn stuff in the world, and it is so valuable, why in the world is the reuse/recovery rate so tiny compared to steel?
Well, the simple reason is that it’s not easy. If it were easy to recycle plastics, this wouldn’t be the case, right? You wouldn’t have a valuable material not being reused.
Metals have very different densities over a wide range. They have different electrical and magnetic properties. And they even have different colors. Those properties are exploited to separate metals and metal ores very efficiently and effectively.
Plastics, on the other hand, have overlapping densities over a very narrow range. Their electrical and magnetic properties are either nonexistent or very similar. And any plastic can be any color.
The traditional ways of separating materials simply have not worked for plastic, and we’ve had to be much cleverer.
Another consequence of plastics being difficult to recycle and metals being easy is that those of us in the developed world, particularly the U.S., I’m sad to say, ship our difficult-to-recycle stuff overseas. We continue, even with the Green Fence (China’s initiative to crack down on mixed materials shipments into the country) and with the market down, to ship much of our difficult-to-recycle streams to developing countries.
That in and of itself is not a bad practice, and I’m not here to suggest that it’s a bad practice. I am just here to talk about the consequences of that. Whole cities in China, for example, have been developed to handle our waste streams. They do a very good job of recycling what they can—the ones and twos and sometimes some other plastics—because that is what a human being can see as unique and separate from our waste streams, and they are getting the stuff that largely we have missed out of the mixed waste streams. I’m not trying to make a blanket statement because I have seen some very sophisticated recycling operations in China, as well.
This is not how we want to be defined as what we do with even some of our waste, in my opinion. It is certainly not how I want to be defined. Yet this is how we deal with some of our problematic waste that we have not figured out how to sort and process and handle properly here.
We seem to care about how our stuff is made. How many remember the pressure that Nike and other manufacturers of apparel, particularly sporting goods, received from the public because of their use of sweatshops? They changed their policies very quickly.
More recently Apple and other electronics manufacturers have come under similar scrutiny.
The unmaking of our stuff is much riskier if it’s not done properly than the making of our stuff. It can be done right, but often it is not.
There are a lot of movements to ban plastics. I have spent 35 years of my life in the plastics industry, so I don’t like to see this for any reason, not just because it impacts the career I’ve decided to choose for myself but [also] because I think this is bad.
Plastics offer incredible benefits, which is why we use them in the first place; it’s not just a cost benefit. There are huge water, energy [and] resource savings because we use plastic in our automobiles.
The American Chemistry Council did a study recently that said if we replaced plastic packaging with the next most logical nonplastic material, we would increase the burden of plastics in the U.S. by 55 million tons with all of the consequences that stem from that—more transport costs, etc.
THREE: WHERE DO I WANT TO GO?
I still think plastics are one of the coolest materials on the planet. I don’t want plastics out of my life, but I do want them out of my oceans, and I want them out of the wrong places.
I want to see plastics occupy a more accepted and a more understood role, and that’s frankly one of the reasons I left MBA Polymers, so I could advocate on how to solve these problems so the answer is not banning this valuable material. I want to see them deliver resource efficiency in a more complete way, which means managing end of life. To be very specific, we have got to do a better job with resource efficiency and with responsible waste management in particular.
We’ve got to start looking at waste differently. Now, I know I’m talking to the converted here, and this is nothing new to you, but it is for many of the audiences I talk to. Waste is not a waste—it’s a resource. We all know that; that’s why we’re here. We are mining resources from waste and are not looking at it as waste.
The four areas that I think we need to focus on with respect to plastics are:
- biodegradable plastics – This is a hard one because as a recycler I fought biodegradable plastics for almost two decades. Now I am a believer that there is a role for biodegradable plastics in streams where there is no logical, sensible way to get the stuff collected.
- collection – We still have to collect a lot more. We have gotten a lot better in the U.S., but we have got a lot more to go.
- recycling – We need to recycle more of what we collect in the U.S. instead of just shipping it off and hoping and praying it gets recycled by someone who gives us a few pennies a pound for it.
- energy recovery – For what we can’t recycle responsibly, I am a firm believer that there is a role for energy recovery to get us to full resource valuation—to get the full value out of our resources.
FOUR: HOW DO WE GET THERE?
Let’s learn from other materials and best practices: Steel has such a high recycling rate [though] it is a pretty low-value material because it is so straightforward to [recycle] it now and on a large scale. I believe plastics recycling is following exactly the same path.
A book by Clayton Christiansen, The Innovator’s Solution: Creating and Sustaining Successful Growth, talks about the innovator’s solution. One of the examples he used was Nucor Steel, which put minimills on the map for steel recycling.
The original steel industry thought that Nucor was nuts—you can’t [upcycle] steel; it will always be a low-end rebar material. But from 1975 to 1990 [Nucor] went from rebar up to angle iron up to structural steel and sheet steel with accompanying increasing gross margins.
I see plastic doing the same thing, from plastic lumber to flower pots and bins to hidden low-demanding parts to now 100 percent used in very demanding parts. It is happening today, already.
If you are curious about this relationship with steel, The Guardian put out an article, “What Plastic can Learn from Steel in a Circular Economy” (www.the guardian.com/sustainable-business/2015/jan/29/plastic-industry-recycling-learn-from-steel-circular-economy).
[In plastics recycling today] what I see is a lot of movement of material. The transporting companies are the ones making the money in this scheme.
I think the future will be fewer touches. … Instead of every single MRF (material recovery facility) making bales that are 80 percent to 90 percent No. 1 or No. 2 material that then have to be transported and touched again and again, I think the MRFs will make a mixed plastics stream that will go to a single plastics processing facility that will then create at least five different types of plastics. The residual from that facility and the MRF can go to fuel. And the advantages to this besides the obvious fewer touches, transport and so forth is economies of scale … and more diversity instead of being stuck on just one plastic and the vagaries of that particular plastics commodity market.
I think the future will be more efficient and more financially attractive, and therefore plastics and recycling will become more sustainable in every sense of the word—environmentally and economically.
You might say, “This is nuts; you can’t do that.”
I invite you to go to a plant in northern England—an MBA Polymers plant—and I’m not just saying that because it’s my former plant. It is processing automotive shredder residue, perhaps the most complicated mixed plastic stream on the planet. It is the largest plant of its kind recovering plastics from end-of-life automobile shredder residue. There is a preprocessing facility that recovers the residual metals. It sends the mixed plastic waste to an MBA Polymers facility, and it gets energy from the rest. It is pretty close to zero waste. That is operational today. The MBA facility produces five plastics today and many grades within those five different types of plastic and sells them to Fortune 100 companies.
It is happening. It is possible. And it is much more efficient than touching it so many times.
Get curated news on YOUR industry.
Enter your email to receive our newsletters.
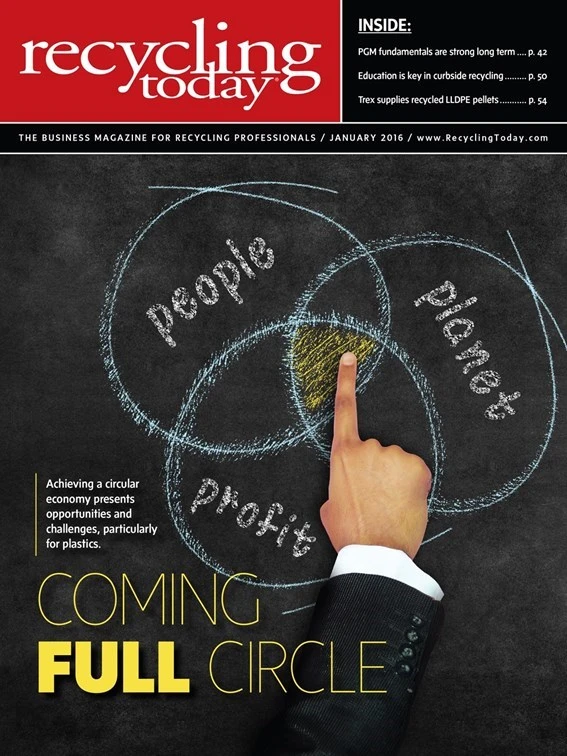
Explore the January 2016 Issue
Check out more from this issue and find your next story to read.
Latest from Recycling Today
- Enfinite forms Hazardous & Specialty Waste Management Council
- Combined DRS, EPR legislation introduced in Rhode Island
- Eureka Recycling starts up newly upgraded MRF
- Reconomy Close the Gap campaign highlights need for circularity
- Nickel carbonate added to Aqua Metals’ portfolio
- EuRIC, FEAD say End-Of-Life Vehicle Regulation presents opportunity for recyclers
- Recyclers likely to feel effects of US-China trade war
- BCMRC 2025 session preview: Navigating battery recycling legislation and regulations