![]() Les Gorden |
In 2004, Les Gorden, president of tire shredding facility Alternative Fuel Source Inc. in Odessa, Mo., saw a chance to grow his business.
What had begun in 1997 with a relatively small contract supplying tire derived fuel (TDF) to a single area power plant had evolved into a larger operation providing TDF to three Missouri plants.
In 2004, Gorden’s customers faced new environmental regulations that would change the way Alternative Fuel Source had to do business. To meet his customers’ changing needs, Gorden turned to a name his company had relied on since the start—Columbus McKinnon of Sarasota, Fla.
"We started with a Columbus McKinnon portable shredder," Gorden says. He says the setup worked well—after the shredder had ground up the tires, the material would pass under a magnet to remove some of the bigger pieces of steel wire, creating a rubber fuel product that was all his customers needed at the time.
However, in 2004, the power plants supplied by Alternative Fuel Source faced new, more stringent environmental standards that meant if they were going to continue to burn TDF, they would need a product that contained a lot less wire. "We needed to remove 99 percent of the wire so we could keep our customers," Gorden says.
Processing TDF generates about 35 to 40 percent waste material, which can lead to high disposal costs. True to its name, the Liberator "liberates" wire from scrap tires, allowing processors to generate revenue by selling their tire wire to steel consuming markets.
While Gorden originally purchased the CM Liberator to clean the steel wire from TDF, the machine has allowed him to separate his material and expand into other markets as well. "We evolved to this point where we have to have the Liberator," he says.

Gorden says the Liberator gives his company the flexibility to screen the material several times after it’s cut to take advantage of different markets that require different gradations—like the ground rubber market, which requires a ¾-inch coarse ground size.
He says the throughput varies depending on the size of the screen, but that with a ¾-inch screen, "we’re getting about 6 tons an hour through it—2 tons an hour of steel, 4 tons of rubber."
Gorden also has high praise for the service he’s received from Columbus McKinnon—starting with the first electrically powered portable shredder through to the Liberator. "They know their machines inside and out," he says. They’re great people and they stand behind their products."
Columbus McKinnon Corp.
1920 Whitfield Avenue
Sarasota, FL 34243
Contact: Richard Colyar
Phone: 941-755-2621
800-848-1071
Fax: 941-753-2308
Get curated news on YOUR industry.
Enter your email to receive our newsletters.
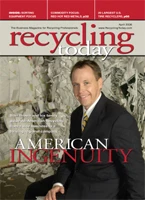
Explore the April 2006 Issue
Check out more from this issue and find your next story to read.
Latest from Recycling Today
- Green Cubes unveils forklift battery line
- Rebar association points to trade turmoil
- LumiCup offers single-use plastic alternative
- European project yields recycled-content ABS
- ICM to host colocated events in Shanghai
- Astera runs into NIMBY concerns in Colorado
- ReMA opposes European efforts seeking export restrictions for recyclables
- Fresh Perspective: Raj Bagaria