Efficiency is a key element to success in any business, and entrepreneurs need tools and equipment that help their operations run as smoothly as possible. For Davis Rubber Co. in Little Rock, Ark., which turns scrap automobile and truck tires into useable end products for a variety of markets, that means using equipment that helps save costs and time without sacrificing high productivity.
In business since 1924, the company has built on decades of experience recycling rubber and now makes a number of products from lower-end tire derived fuel (TDF) to higher-end uses like playground rubber and rubber mulch, according to Davis Rubber’s Roger Davis. To get the job done, Davis has relied on two key pieces of equipment from manufacturer Columbus McKinnon Corp. of Sarasota, Fla. A CM Tire Shredder has been on the job for more than five years. Davis added a CM Liberator about a year and a half ago.
The company was looking to replace its old shredder with the CM model five years ago, and Davis was looking for a machine that would keep his business running at high capacity and also provide some cost savings. A key feature that has helped him accomplish his goals is Columbus McKinnon’s "Multi-Stack" knife technology, which utilizes multiple width knives in the same machine and allows worn knives to be sharpened and reused. Davis says the system has created big savings for his company by not having to spend as much to change blades in the shredder.
To round out the team of equipment, Davis added a CM Liberator to recover the steel from the processed tires. "Like a lot of folks, we needed to come up with an answer for the steel from tires," he says. "We were land-filling it, and we couldn’t do that if we wanted to stay in the business. We needed to be able to recycle that steel."
Davis’ positive experience with the tire shredder led him to look at the Liberator as his solution. "Compared to the other machines, it’s very quiet," Davis says of the Liberator. "It has a very large volume compared to other equipment, and from people who have come and looked at my end product, they tell me it’s cleaner than what other machines make," he says.
The team of CM machines has lowered the costs of changing blades and increased throughput at Davis Rubber Co., which are two chief reasons Davis himself would recommend the machines to his colleagues. "I would tell them to give [the machines] a hard look," he says.
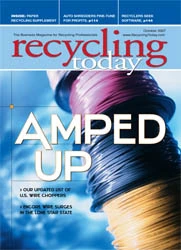
Explore the October 2007 Issue
Check out more from this issue and find your next story to read.
Latest from Recycling Today
- Toppoint Holdings expands chassis fleet
- Lego creates miniature tire recycling market
- Lux Research webinar examines chemical recycling timetables
- Plastics producer tracks pulse of wire recycling market
- Republic Services, Blue Polymers open Indianapolis recycling complex
- Altilium produces EV battery cells using recycled materials
- Brightmark enters subsidiaries of Indiana recycling facility into Chapter 11
- Freepoint Eco-Systems receives $50M loan for plastics recycling facility