
Multiple options exist when creating valuable products out of nonferrous fines. But in the view of Kyle Rice, Midwest Territory Manager at Walton, Kentucky-based STEINERT U.S. Inc., recyclers often have stopped at recovering zorba.
“Historically, zorba was the end-all product, and that would be exported,” Rice says. “That shifted with some additional X-ray equipment: X-ray transmission and X-ray fluorescence.”
Introduced three-and-a-half years ago, STEINERT CHUTEC is designed to close gaps in sorting the fines resulting from heavy metals liberation and add value by recovering red metals, such as copper and brass, and zinc, that often have been exported. Using X-ray fluorescence and a 3-dimensional sensor, the machine captures and separates desired metals as they cascade down a chute.
STEINERT CHUTEC is designed for the present as well as the future as onshoring of production capacity for red metals increases.
“The response to STEINERT CHUTEC has been very good,” Rice says. “It’s been very popular both internationally and in the domestic U.S. market where people are moving ahead and putting these in. A lot of people who already had these mixed-heavy-metals products and were having to export them now have an option to further separate them with STEINERT CHUTEC. You see a lot of onshoring of production capacity for metals like copper and brass, and these machines are going to be a part of filling that production demand for postconsumer scrap.
“In terms of being able to address all size fractions and separate them to the quality of products that you’re going to need to feed into the domestic processing locations, STEINERT CHUTEC is going to be there for the long haul,” he adds.
The machine, developed by Germany-based STEINERT, is designed to accommodate metals ranging from 5 millimeters to 30 millimeters in size, although much larger fractions are also being processed. Scrap is fed into a vibratory feeder housed inside a shell that also contains a chute. As material falls off the feeder, it slides down the chute and passes an X-ray sensor. Air valves arranged on a bar shoot jets of air at the desired metal fractions and eject them into a splitter, separating them from the rest of the scrap.
Operators can use STEINERT CHUTEC’s computer to program which metals to detect.
“We’re making the detection of the object itself, and then it’s making a quick millisecond decision on what it’s able to detect from that piece,” Rice says. “If it’s a copper piece and you’re trying to sort out copper, STEINERT CHUTEC hits it with the air jet to push it past a splitter. It’s all happening instantaneously out of freefall that it’s detecting what the composition of that piece is and making a quick decision.”
Why focus on the fines fraction when separating heavy metals? Steinert estimated there was added value in being able to detect more red metal content such as copper and brass, as well as concentrate precious metal content along with it. For that reason, STEINERT CHUTEC was designed with the highest detection resolution on the market to help separate red metal units specifically out of a fines fraction that historically has not been processed to the fullest extent of its value.
“Overall, at Steinert, we look to be a comprehensive solutions provider, and STEINERT CHUTEC was born to address the gap in fines heavy metals separation,” Rice says.
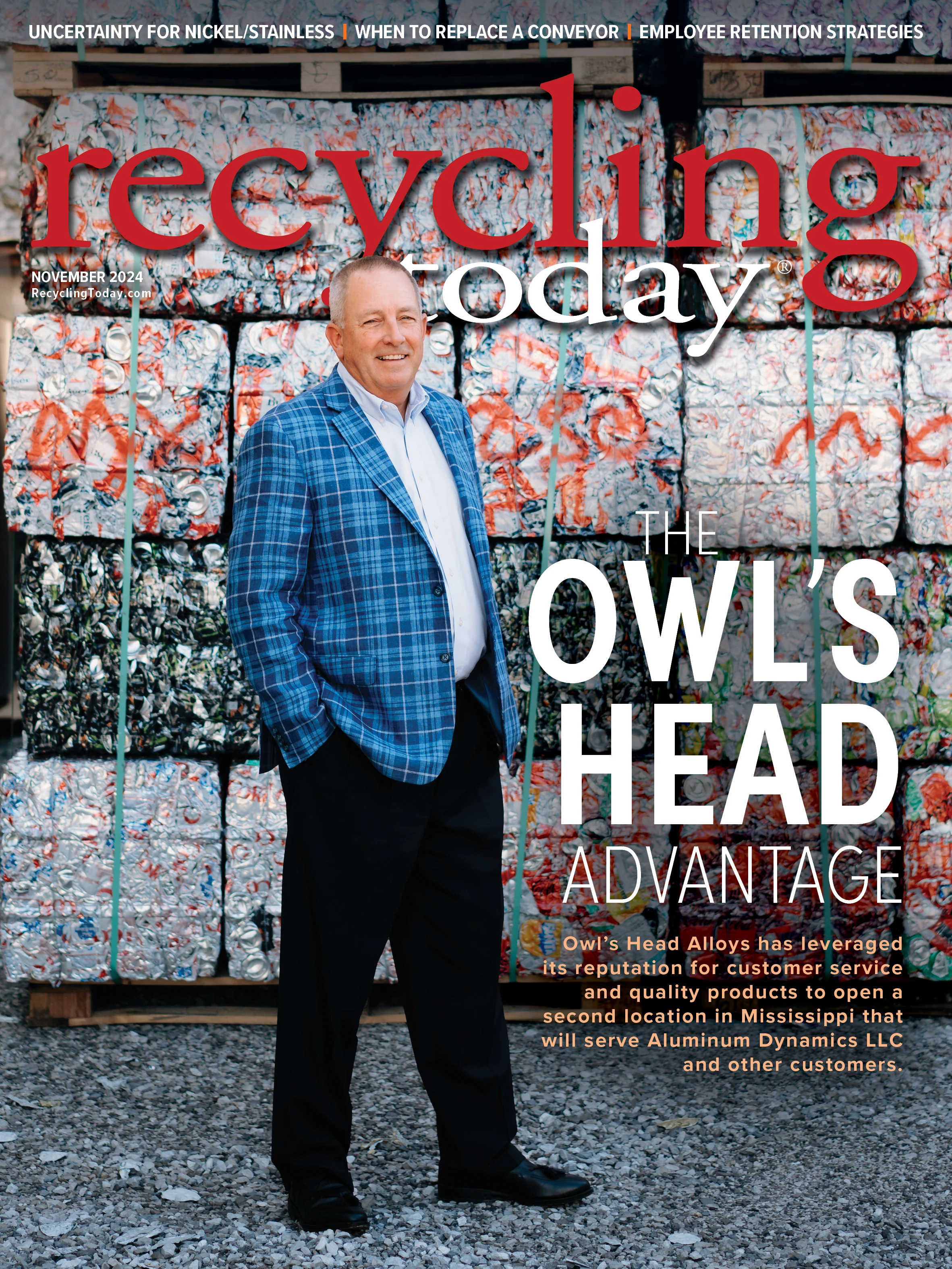
Explore the November 2024 Issue
Check out more from this issue and find your next story to read.