
When Ron Gonen co-founded New York City-based Closed Loop Partners in 2014, his goal was simple: reform the way companies and municipalities recycle in the United States.
Gonen, who served as the New York Department of Sanitation’s deputy commissioner of sanitation, recycling and sustainability during the administration of former Mayor Michael Bloomberg, saw an opportunity to streamline and improve recycling operations across the country through smarter investments. Along with co-founder Rob Kaplan, a former director of sustainability at Walmart, Gonen created Closed Loop Partners to serve as an investment platform that could help companies and municipalities fund ambitious projects aimed at improving recycling rates, reducing contamination and increasing participation that might otherwise have difficulty getting financed.
Through the organization’s Closed Loop Fund, Closed Loop Partners deploys no-interest and low-interest loans to help vetted third parties finance their specific initiatives. For their efforts, the company takes a small management fee, while investors expect their principal investment to be returned with a little interest.
The organization’s fund, which has attracted more than $100 million in co-investment to date thanks to the participation of high-profile corporations such as Coca-Cola, Procter & Gamble, 3M and PepsiCo, has been deployed to help bankroll 38 projects. In 2017, the company invested more than $40 million for 17 projects across the U.S. and Canada.
Making adjustments
Closed Loop Partners has helped fund a number of auspicious programs in the years following its inception. While Gonen says all the projects that have been funded by the organization are performing as expected and paying back on schedule, he acknowledges that the recycling landscape has shifted considerably since the organization was first conceived.
“One thing that has definitely been highlighted for us since we started is the quality of bales needs to be significantly improved,” Gonen says. “I think, traditionally, there was a view that as long as you increased supply (i.e., put more carts on the street and built more material recovery facilities, or MRFs), that would be good for the recycling industry. But there was one additional step that we’ve realized needs to be part of that equation, which is putting advanced equipment in MRFs to make sure the bales are of high quality.”
Gonen says the need to invest in advanced equipment to update MRFs and improve the quality of bales is more pronounced in the face of China’s ban on U.S. recycling imports. To meet the increased purity demands of the market, today’s companies must decide whether to invest in new sorting technologies or see diminished end markets for their materials, he adds.
“I think we’re starting to see a shift,” Gonen says. “We’re seeing companies that have high-quality bales being able to weather the disruption [caused by China], and I think they’re going to come out on top. And I think you’re seeing companies with low-quality bales start to put out the red flag and go back to their municipalities saying they need to charge more, so I don’t think things are going to end well for them unless they start investing in producing high quality.
“High-quality bales are moving, that’s the main thing,” he continues. “And if you produce high-quality bales, there are people in the market who want to work with you. That is something that I think is getting lost in the whole China conversation.”
Enforcing a higher standard is not just something that should be left to MRFs, Gonen says. He says municipalities should include specific purity rates into their contracts to ensure recovery facilities can economically process materials. He says bale quality above 90 percent should be the standard, though above 95 percent is the ideal.“We need to get to a place where municipalities are writing that spec into their contracts,” Gonen says. “What you have now is MRFs with very low-quality bales that they can’t move coming back to their municipal accounts saying that recycling isn’t working and they need to start charging more for it. They really should be saying, ‘I didn’t invest in the proper equipment in my MRF and, therefore, I’m producing low-quality bales I can’t move, so you must subsidize my business.’ This is hindering the expansion of recycling, and I think it’s going to be key moving forward to mandate a certain bale quality if a MRF wants to submit a contract proposal.”
Although the Chinese ban has upended business for many recyclers, Gonen says this disruption ultimately can be positive.
“The China situation is going to cause some short-term hiccups and pain for folks; but, long-term, I think it’s a great thing, especially for the U.S. industry because there are too many people in the recycling industry producing low-quality bales that they were thoughtlessly shipping off to China,” he says. “I think what you’re going to see with the current regulations is that the companies producing low- or medium-quality bales are either going to be driven out of business or they’re going to lose their market, which is going to help the better performers in the industry.”
Gonen says another positive of China’s ban on scrap imports is how it has spurred a massive opportunity to invest in recycling and the circular economy in North America. He says domestic companies are hungry for recycled materials and creating more refined recycling streams could help forge inroads with these major manufacturers.
Through Closed Loop Partners, Gonen says he hopes to act as a conduit to help connect manufacturers with recycling haulers and processors to generate the right kinds of materials for industry.
“A company may want a lot of postconsumer recycled plastic (PCR), for example, but there is someone else doing the hauling [and] sorting; someone else turning this into a preform and then selling it to that manufacturer,” Gonen says. “They have little visibility into pricing, quality, who’s doing a good job, who’s doing a bad job, etc. That has limited their ability to increase the amount of PCR they’re using, which has unfortunately inhibited the recycling industry’s ability to grow and become more profitable. So, we’re looking at ways to help companies like the Cokes, the Pepsis, the Unilevers, the P&Gs get better connected to the haulers and sorters so they can have better ownership over the materials they want to use.”

Rethinking what gets landfilled
Changing the recycling practices in the U.S. requires changing the status quo of how waste has traditionally been handled. With this in mind, Gonen says his organization is committed to working with companies that are more focused and strategic about diverting recyclables from landfills.
Gonen says that supporting privately held regional companies, such as Lakeshore Recycling Systems, Morton Grove, Illinois; Balcones Resources, Austin, Texas; Pratt Industries, Conyers, Georgia; Recology, San Francisco; and First Star Fiber, Omaha, Nebraska, can have a big impact in helping divert recyclables, which is why he says Closed Loop Partners is focused on finding ways to get these companies to a scale where they can better compete for contracts with some of the biggest players in the space.
“We’re seeing a bifurcation in the industry,” Gonen says. “There are the large haulers and landfill operators like a Waste Management—they do have a sizable recycling practice, but they’re mostly focused on filling their landfill—versus these privately held regional companies that are starting to get to a decent size that are primarily focused on waste diversion and recycling. These smaller companies have a hauling division and a MRF, and they’re completely aligned strategically and economically with the customer, which is the municipality or the commercial business.”
In addition to supporting more strategic haulers and operators, Gonen says the importance of recycling—and its benefits—needs to be better communicated to customers.
“There is still a lot of work that needs to be done to communicate why recycling and the circular economy is so important for American citizens,” Gonen says. “I think there is still the perception that you should recycle because ‘It’s the right thing to do,’ but people hear about how sometimes their recyclables don’t actually get recycled, or how there is this problem in China or how their city isn’t getting paid for recyclables, and I think we can all do a better job in helping people understand the reason it’s important to recycle is that you avoid the fee of having to pay to send material to a landfill. We can definitely do a better job communicating that message.”
Part of communicating this message requires cutting down on misinformation about what should and shouldn’t be recycled. While some environmental and special interest groups have made headlines calling for the widespread ban of plastics, Gonen says individuals need to know the nuances between different types of waste and how they affect the recycling stream before they can make educated decisions on what to put into the recycling bin and what to throw away.
“I think that what needs to be clarified in this whole conversation is that not all plastics are bad, in my opinion,” Gonen says. “The ones that are bad are the ones that cannot be recycled into another product and cannot be sold by a MRF for over $70 per ton because that’s what it costs a MRF to process that material. You have a whole suite of plastics in the market today that either can’t be sorted properly, don’t have a market or have a market but it pays $20 per ton. Those types of plastics are a massive burden on the recycling industry. Plastic bags, for instance, get into MRFs [and] cause the machinery to break; they’re considered contamination, and you have to pay to get rid of them. If there is a market for them, it’s certainly less than $70 per ton.”
Gonen says producers of some of this hard-to-recycle material, such as plastic bags and straws, should take the current call to ban these items as an opportunity to innovate and figure out how to develop proper sortation technology for the specific type of plastic or product they produce and to do so in a way that can help develop end markets that pay more than $70 per ton.
He notes that the groundswell of companies and municipalities coming out against difficult-to-recycle single-use items is a positive for the industry, as it can help start the larger conversation on what types of materials are bad for recycling and which ones, such as polyethylene terephthalate (PET), high-density polyethylene (HDPE) and rigid polypropylene (PP), are of high value to recyclers.
“We need to graduate rather than lump all plastics together into one bucket so we’re able to instead come up with a long-term strategy on how to deal with plastics,” Gonen says. “I think plastics should be allowed into the market if they can be easily sorted by a MRF and sold for more than [their] processing costs. If [they] can’t, you’re either asking the taxpayer or MRF to subsidize the landfilling or the processing of that product, and I don’t think that’s fair.”

Develop lasting solutions
To help manufacturers and recyclers develop innovative solutions to today’s recycling headaches, Closed Loop Partners unveiled its Center for the Circular Economy in March. The organization is a research and development (R&D) center where manufacturers, municipalities and investors can come together to foster ideas to move the recycling industry forward.
One of the cornerstone initiatives being undertaken through the center is the push to give paper and plastic cups a second life. The NextGen Cup Consortium, led by Starbucks and McDonald’s, is committed to identifying and commercializing existing and future recovery solutions for single-use hot and cold paper cups that often end up landfilled.
Gonen says he hopes the center will serve as a forum for innovative solutions that can be supported by the organization’s in-house funding mechanism.
“We’re primarily an investment firm, but one of the things we recognized when we were looking for bottlenecks and solutions to those bottlenecks we could invest in is that sometimes the bottleneck and the potential solution to it was too nascent for us to make an investment,” he says. “So, we realized there was an opportunity to create an R&D center that could do research and development into what the cause of the bottleneck was, what the potential solutions were and to help incubate those solutions and perhaps provide some grant or seed funding to get them to a place where either us or someone else can invest in that to scale.”
Moving forward, Gonen says he sees a tremendous opportunity for investment in domestic recycling and circular economy infrastructure, but that it will take buy-in from across the supply chain for these investments to bear fruit. Luckily, he says, the industry has been receptive to working with his team to develop solutions that will allow recycling to find new life in this country after the dust from the scrap import ban in China settles.
“We have an excellent team at Closed Loop Partners and a great portfolio of investors, but it’s not without its challenges,” Gonen says. “I think we’ve all worked hard together to identify some worthy investments, and those investments are having the impact we expected. I think that’s a testament to the Closed Loop Partners team, the portfolio of investors we have but also the innovators and municipal leaders out there we’ve been able to interact with.”
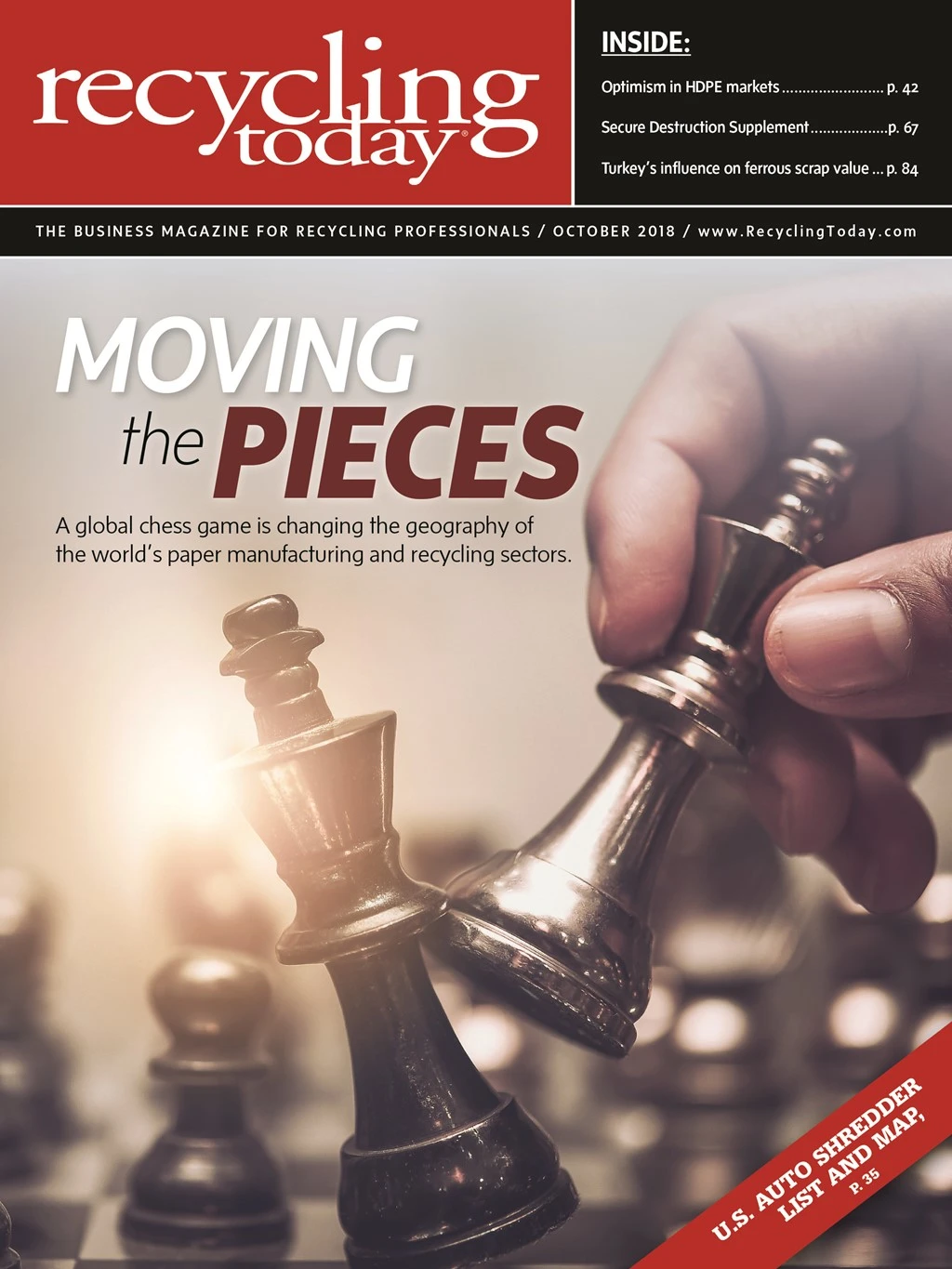
Explore the October 2018 Issue
Check out more from this issue and find your next story to read.
Latest from Recycling Today
- Electrolux commits to recycled content
- Duesenfeld system targets battery cell scrap
- Hyundai says it will make steel in the US
- APR announces Recycling Leadership Award winners
- Glass Half Full opens glass recycling facility in Louisiana
- AmpUp partners with Roundtrip EV
- Global Recycling Day event supports Pittsburgh school's recycling efforts
- President signs executive order on critical minerals