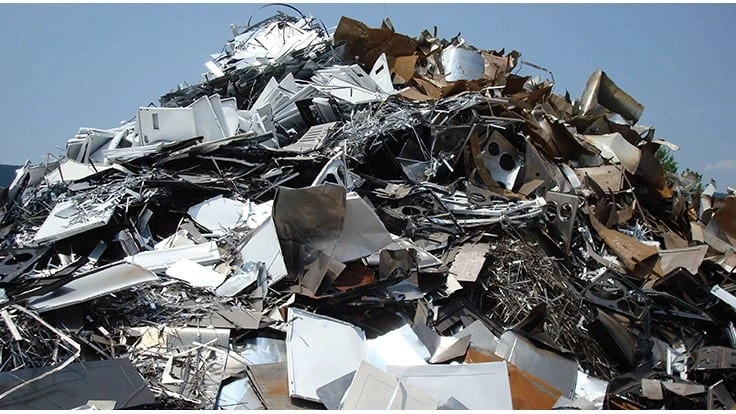
Photo by Recycling Today staff.
Cleveland-Cliffs, now one of two producers of steel in the United States using blast furnace and basic oxygen furnace (BOF) technology, has its roots in iron ore mining and iron feedstock production. In its newly released sustainability report, the company signals it intends to stay true to its iron sector roots.
Recycling and scrap are mentioned in the 74-page document, but in the news release announcing the report, including in comments by CEO Lourenco Goncalves, the emphasis is on low-carbon methods of using iron-based products in BOF and electric arc furnace (EAF) processes.
Goncalves states, “As we transformed our business in 2020, we developed an integrated, sustainable business model which we believe is the real benchmark in steel production, for the U.S. and for the rest of the world. That includes natural gas-based direct reduction; sinter-free blast furnaces using pre-reduced iron as feedstock, along with customized pellets; and, last but not least, electric arc furnaces free from the vast amounts of dirty pig iron originating from highly polluting countries, so common in other EAF operations in the U.S.” (It is unclear which EAF steelmakers Goncalves is referring to in the final portion of that comment.)
At a Fastmarkets AMM online event this April, Goncalves said his company was bullish on the future of direct-reduced iron (DRI) because the ferrous scrap market was reaching the limits of its ability to supply steelmakers, in his opinion. “In the long run, for the next several years, we should expect scrap prices to appreciate in the international market,” he stated.
On page 16 of the new sustainability report, the company states, “In 2020, Cleveland-Cliffs’ operations recycled 4.5 million tons of scrap steel.” The report also states, “Steel can be recycled without losing its strength” and that “these characteristics make steel an ideal material for a circular economy.”
The Cleveland-Cliffs positioning relative to virgin iron-based products is almost certainly tied to protecting its investments in iron mining, hot briquetted iron (HBI) and DRI production and to ensure it has access to steelmaking ingredients.
EAF steelmakers including Schnitzer Steel Industries, Gerdau and Commercial Metals Co. have long been involved in the scrap processing and steelmaking sectors. In the late 2000s, Nucor Corp. and Steel Dynamics made major moves to do the same, with Nucor buying the David J. Joseph Co. and Steel Dynamics purchasing OmniSource Corp.
Most recently, an EAF steel company in Peru has purchased two scrap yards in Florida as a way of securing feedstock into the future.
The effort by Cleveland-Cliffs to position low-carbon iron-based steel production as meeting long-term sustainability targets is being replicated in Europe. A German ferrous scrap association and its general manager have issued a statement saying in part, “If we really want to operate climate-neutral in Germany and the EU by 2050, [we need] incentives for companies to increasingly use secondary raw materials and invest in future technologies in the circular economy, because green steel is made from scrap.”
Latest from Recycling Today
- WM completes $40M automation project at Philadelphia MRF
- Speira commissions new furnace in Germany
- ABB report portrays paper sector circularity, emissions reduction
- RMDAS and Davis Index numbers portray stalled ferrous market
- Attero adds NGO veteran to its board
- AMCS launches the AMCS Platform Winter 2024
- Cirba Solutions celebrates construction milestone at Ohio plant
- Study outlines plan to transition US plastic packaging, textiles to circular systems by 2040