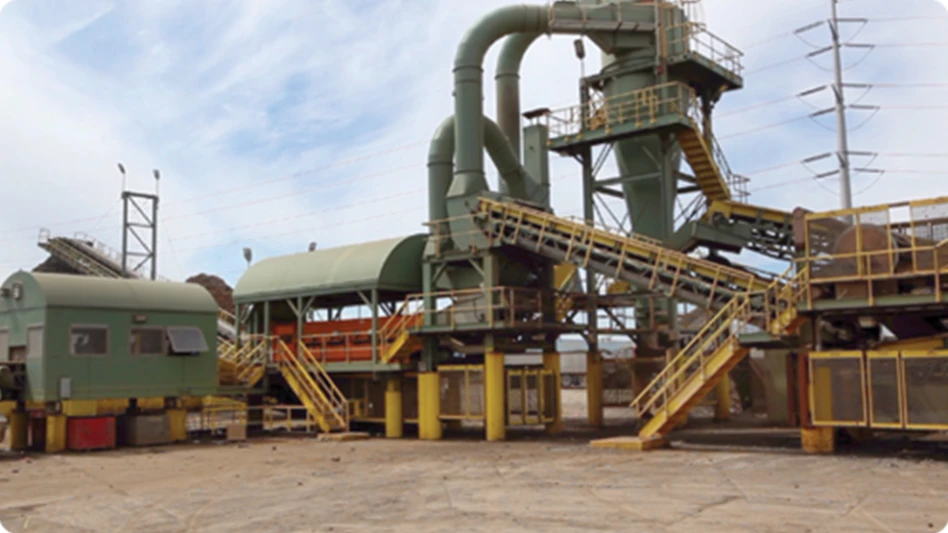

The product designers and manufacturing experts at Eriez know shredding plant operators sometimes face two conflicting challenges: to harvest the maximum amount of metal downstream from a shredder while also producing the clean, high-quality grades the market is looking for.
Achieving either the absolute highest volume or the highest quality historically has involved tradeoffs, Eriez Market Manager-Recycling Mike Shattuck says. “Typically, the higher the recovery of material, the lower the grade, and vice versa,” he says.
The equipment industry veteran says research and experience gained by Eriez and its customers, however, has made great progress in allowing recyclers to reach for both lofty goals: improved grade and recovery.
The Eriez effort has gone into addressing not only the volume king at shredding plants—the ferrous fraction—but also nonferrous grades. At Eriez, the target on the ferrous side involves creating “upgraded shredded scrap [that] will lower the amount of copper-bearing material (typically less than 0.20 percent) and increase the grade of the scrap,” Shattuck wrote in an Eriez white paper.
The first of three pieces of Eriez equipment that can help produce this result is its P-Rex (Permanent Rare Earth Xtreme) drum magnet. That device’s industry-leading wide and deep magnetic field allows not only a clean fraction of ferrous to be harvested, but also copper-bearing materials such as meatballs (which have value to a different part of the market).
“Consumers of either ferrous or nonferrous scrap are unlikely to step back from their increasing quality demands.” – Mike Shattuck
“Meatballs and copper-bearing materials are historically two of the toughest materials to recover magnetically,” Shattuck says. “The superior strength and reach of the P-Rex recovers the hard-to-get items and eliminates missed ferrous ending up in the nonferrous system. When steel is in the nonferrous mix, it is not only a loss of revenue, but can also cause damage to nonferrous equipment and potentially cause fires in the fluff or zurik piles.”
Next in line, mixed shredded scrap heads to an Eriez Shred1 ballistic separator where “the less magnetic material (copper-bearing, debris, irony aluminum) is affected more by the ballistics of the high-speed belt than the attraction of the magnet in the head pulley of the conveyor and are thrown over a splitter,” Shattuck says.
The low-copper fraction, (typically 0.20 percent copper or less) accounts for about 75 percent of the total ferrous stream and reports to the stacking conveyor as a finished product. The remaining 25 percent copper-rich product (product that went over the splitter) will then pass under a scavenging drum, where nonferrous and debris will be separated from the ferrous product.
This ferrous product then goes to the picking station. Since it is free of remaining nonferrous and debris, the pickers can concentrate on only picking visible copper-bearing material. This not only results in increased copper pickings but can be done with fewer pickers, eliminating labor. The nonferrous separated at the scavenging drum will go to the nonferrous plant, increasing overall nonferrous recovery.
Shattuck cites numerous benefits of this downstream array, including increased automation, maximum recovery and quality of ferrous scrap, maximum recovery of copper-bearing materials such as motors and wire and reduced labor requirements.
Consumers of either ferrous or nonferrous scrap are unlikely to step back from their increasing quality demands, Shattuck says, giving shredding plant operators considerable incentive to investigate the Eriez product line.
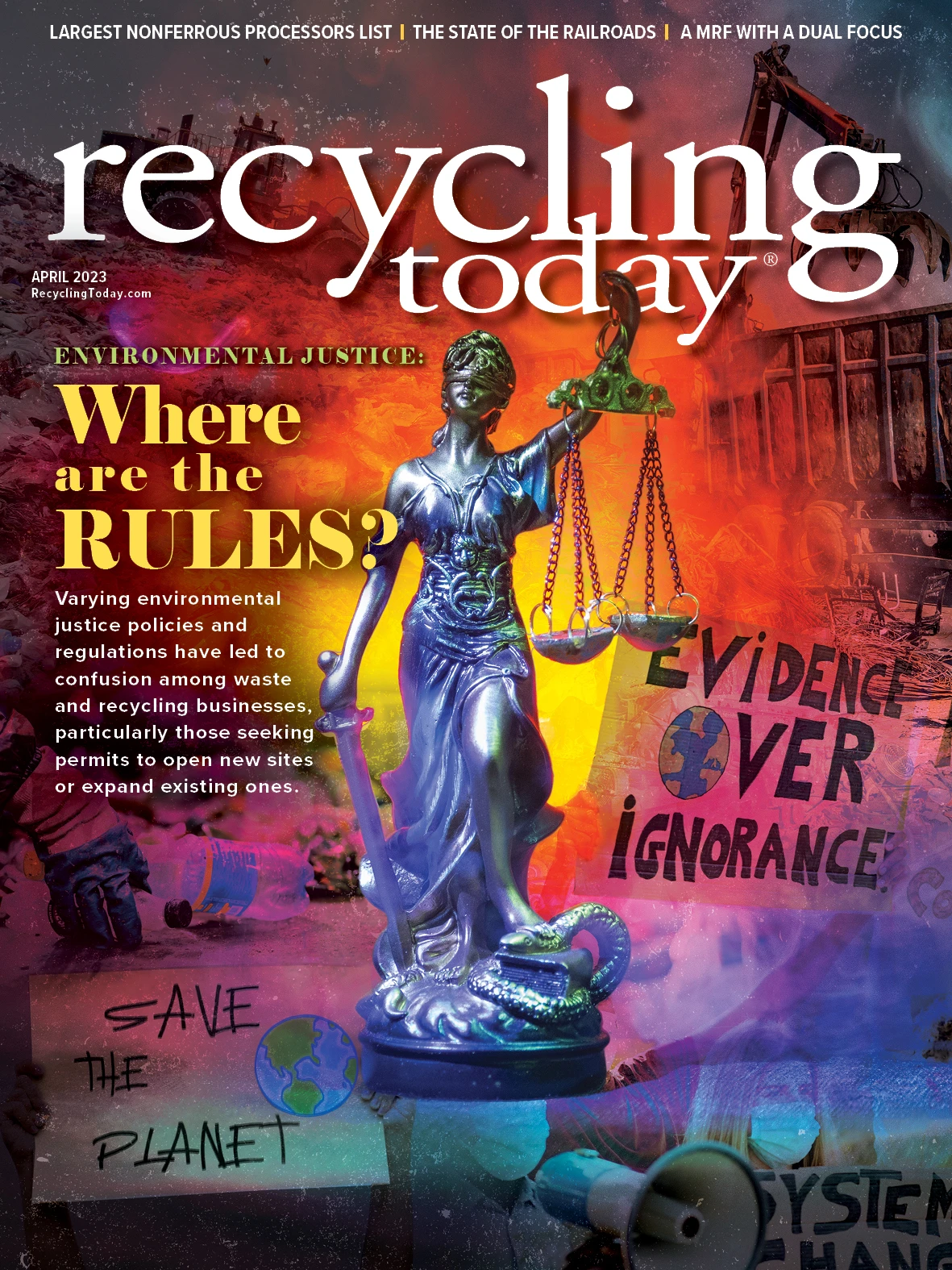
Explore the April 2023 Issue
Check out more from this issue and find your next story to read.