In 1983, the state of New York implemented the New York State Returnable Beverage Container Act, or "The Bottle Bill." This bill imposed a deposit of 5 cents on all bottles and cans containing soft drinks, beer and other beverages. Distributors and retailers are responsible for collecting and refunding deposits to consumers.
GETTING TECHNICAL |
Adjacent to the Eriez world headquarters in Erie, Pa., the Eriez Technical Center has more than 100 types of permanent magnetic, electromagnetic, vibratory, screening and electronic metal detecting equipment. This equipment separates, concentrates, moves, feeds, detects and recovers a wide variety of materials. Since it first went into operation in 1964, the Eriez Technical Center has conducted tens of thousands of application tests on all types of materials and processes. The Technical Center receives product samples from all over the world for Eriez engineers and technicians to determine the most efficient and profitable ways for customers to process or handle materials to obtain the desired results. Samples range from coffee beans to crushed flashlight batteries. Eriez encourages customers to visit the Technical Center, not only to see the results of the testing but to participate in the actual testing procedures. The company says customers’ on-site participation assures accurate interpretation of test reports and provides the opportunity to discuss any specialized procedures necessary for customer samples. |
New York, the third most populous state in the United States, generates plenty of deposit bottles. For the last period reported by the New York Department of Environmental Conservation, 2005-2006, the numbers are staggering:
• $289.5 million in total deposits paid;
• 5.8 billion bottles and cans returned during the year; and
• 94.5 billion bottles and cans returned since 1983.
A COOPERATIVE EFFORT
The implementation of the state’s Bottle Bill led to the development of the Central Recycling Co-op (CRC) of Elmira, N.Y. Beverage distributors established the co-op in 1983 for the sole purpose of carrying out the distributors’ requirements under the state’s Bottle Bill.
CRC has customers in seven counties of south-central New York State. In the course of a year, the company’s 12 trucks return more than 135 million empty deposit beverage containers from more than 300 accounts (grocery stores, redemption centers, etc.) for processing. The total volume consists of 88 million cans, 25 million PET (polyethylene terephthalate) bottles and 22 million glass bottles.
Aluminum cans and plastic bottles are baled, and glass is sorted by color and crushed. Until 2005, CRC simply sold the recycled glass to a glass crushing facility. All that changed in 2005 when the company built a glass processing facility and began processing crushed glass, producing a furnace-ready cullet that could be sold directly to glass bottle manufacturers.
Prior to CRC building the glass processing facility, the co-op sold its cullet, which was contaminated with aluminum and steel caps and paper, to other processors, who removed the contaminates from the glass and sold the clean cullet to bottle manufacturers.
Building the facility allowed CRC to sell uncontaminated cullet directly to the bottle manufacturers at a higher price than it was getting previously when it needed the services of a middleman to clean up the material. It also gave the co-op the opportunity to expand its business, purchasing cullet from other recycling facilities for processing and purchasing whole bottles from many other sources throughout the Northeast for de-casing, crushing and processing. The co-op’s cullet sales have doubled as a result.
DECONTAMINATING & CRUSHING
Here’s how the process works:
The deposit containers are delivered to the CRC facility in a variety of manifestations. They are segregated by material type: glass, metal and plastic. The bottles arrive either pre-crushed from another recycling facility or "cased" from a beverage distributor or retailer. Bottles that are in cases must be "de-cased." In this process, they are run through a trommel screen to separate the cardboard cases from the glass. If the glass is a mixture of colors (typically green, amber or flint), it must be hand sorted first, which is a labor-intensive process.
HISTORY OF BOTTLE BILLS |
It was not until after World War II that cans began replacing glass bottles in the beer industry. The convenience and disposability of cans helped boost sales at the expense of refillable glass bottles, and by 1960 approximately 47 percent of beer sold in the U.S. was packaged in cans and no-return bottles. Soft drinks, however, were still sold almost exclusively in refillable glass bottles requiring a deposit. Can market share was just 5 percent. But things changed with a dramatic shift from refillable soft drink "deposit" bottles to "no-deposit, no-return, one-way" bottles and cans, which resulted in an explosion of beverage container litter. By 1970, cans and one-way bottles had increased to 60 percent of beer market share, and one-way containers had grown from just 5 percent in 1960 to 47 percent of the soft drink market. The so-called "bottle bills" were intended not only to reduce beverage container litter, but to conserve natural resources through recycling and to reduce the amount of solid waste going to landfills. Seven states reported a reduction of beverage container litter ranging from 70 percent to 83 percent and a reduction in total litter ranging from 30 percent to 47 percent after implementation of the bottle bill. The bottle bill states also achieved high recycling rates. Today, 11 states and eight Canadian provinces have deposit laws requiring refundable deposits on certain beverage containers. |
The glass then moves through a custom designed Eriez vibratory pre-screen feeder with a .75-inch perforated hole plate, designed to remove bottle caps and other nonferrous and ferrous contaminants from the glass. The glass then passes by an Eriez stationary magnet, which picks up more metal contaminants in the stream.
Cullet that passes through the pre-screener goes directly to the stationary Eriez magnet for final ferrous removal then on to an Eriez metal detector and Eriez eddy-current separator for removal of aluminum contamination. The processes for screening and cleaning the cullet become more precise as the material moves through the plant.
Any product (glass and contaminants) that does not pass through the pre-screener goes into a Hazemag crusher then to the second Eriez vibratory screener. Material that passes through the second screener is mixed with the material from the process described above and then goes on to the stationary magnet, metal detector and eddy current. At each "station" of the system, contaminants are removed from the cullet. If the screener misses a contaminant, the stationery magnet is designed to remove it. If ferrous material is not removed by the stationary magnet, the metal detector is designed to remove it. Finally, the eddy current detector ensures that the cullet is as "pure" as it can be by removing aluminum from the stream.
Material that is screened off is removed from the system and rerun from the vibratory feeder onward to recover as much of the glass as possible. CRC discards the final screenings after the rerun.
"I wanted to work with Eriez because of their reputation as a world class operation," says Richard Dubois, president of CRC. "I looked at several systems while planning this operation, and Eriez was the one I wanted. They worked with us; they had us bring contaminated glass to their facility in Erie, where we pre-tested the concepts. Eriez’ expertise really helped to customize the footprint and sizing of the line. We have a unique space here, and everything had to fit just so."
Dubois adds, "Everything works. Our customers say the cullet is the best they’ve ever seen. It’s a high-quality product, thanks to Eriez."
The author is product manager, resource recovery, at Eriez and can be contacted at agedgaudus@eriez.com.
Get curated news on YOUR industry.
Enter your email to receive our newsletters.
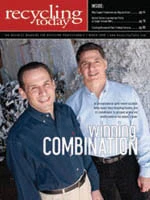
Explore the March 2009 Issue
Check out more from this issue and find your next story to read.
Latest from Recycling Today
- Altilium produces EV battery cells using recycled materials
- Brightmark enters subsidiaries of Indiana recycling facility into Chapter 11
- Freepoint Eco-Systems receives $50M loan for plastics recycling facility
- PET thermoform recycling the focus of new NAPCOR white paper
- Steel Dynamics cites favorable conditions in Q1
- Hydro starts up construction in Spain
- Green Cubes unveils forklift battery line
- Rebar association points to trade turmoil