
Once a world leader in plastics recycling, China has imposed restrictions on imported scrap, leaving it at home for U.S. recyclers to process. For one supplier of size-reduction equipment, the situation has translated into booming sales.
Weima America, Fort Mill, South Carolina, supplies turnkey, two-stage size-reduction systems. Tailored to Weima’s customers’ needs, the systems combine its shredders and granulators with conveyors and separation equipment from other suppliers. Sales of the systems increased 35 percent in 2018.
Weima has offered two-stage systems for a while. However, because of the changes in China’s policies, business has increased. The company’s customers include plastics processors that are processing in-house scrap and plastics recyclers.
China’s most recent restrictions, dubbed National Sword, began Jan. 1, 2018. They mean the longtime giant consumer of recyclables won’t even take bales of postconsumer plastic, says Madison Burt, vice president of sales at Weima.
“If they’re going to buy plastic, it’s going to be in a regrind form or it’s going to be in a pellet form,” he says. “Basically, it has to be a commodity. It cannot be whole-bottle HDPE (high-density polyethylene) milk jugs, baled.”
Weima’s two-stage system begins with an infeed mechanism, typically a belt conveyor. The shredder breaks big pieces down into pieces sized 2 inches or smaller.
Then the material travels on a conveyor through a metal separation system. “We use a metal detector with a reject system that would allow for even the nonferrous pieces to get ejected,” Burt says.
The conveying equipment usually is customized “because it really depends on where they’re going to put it in their building, how they’re going to orient it, where they’re going with everything,” he says. “So, infeed conveyors and discharge conveyors and all the metal detectors and separation equipment, we typically source that domestically and marry that with our equipment, include all the starters, the controls, and put all that in our control system to provide the customer with a complete answer rather than just a couple of pieces of equipment.”
Then the shredded plastic feeds into the granulator. “If [the end application] is very sensitive to fine dust, we may even go through elutriation after the granulator, basically, getting the dust out, if there is any,” Burt adds.
Otherwise, the plastic can go directly into a gaylord container as finished, consistent-quality regrind ready for reuse, the company says.
Weima typically uses its single-shaft WLK-series shredders for the first stage of these two-stage systems. Other options are a four-shaft ZMK-series shredder or a single-shaft horizontal machine.
Burt says the second stage of the system typically uses an LM- or SM-series granulator.
“Because we’re two-staging, the load on the granulator is not nearly as profound as if you were to feed it into the granulator alone. So, it’s a little bit easier to regrind when it’s been preshredded.
“The LM-series granulator does a great job,” he continues. “The SM is a little bit more of a beefier design, which would be required if you were feeding whole parts in. The LM series is economical, and, when you do it in conjunction with a shredder, it’s more than sufficient.”
The ability to break down giant chunks of material is key.
“Imagine a bowling ball,” Burt says. “If you feed a bowling ball in a granulator, you have to have a massive granulator in order to take that mass of plastic all at one time.”
However, he says, a shredder can slice into the object like a knife cutting slices from a potato.
The granulator can then “take it down to the next step, to mashed potatoes,” Burt adds.
“If you tried to feed that whole bowling ball into the granulator, you could do damage to the granulator.”
Weima machines emphasize accessibility for maintenance and cleaning. “When you deal with a contaminated material, you need to have something that’s easily maintained,” Burt says.
He adds that the company customizes the systems to each customer’s goals. For example, if the material is more fibrous, Weima has a design that prevents material from wrapping around the rotor.
The company also offers carbide knives for high-wear applications, such as 24-hour run times or processing abrasive material, Burt says.
Weima also supplies easy-to-use, touch-screen controls that are designed to allow users to easily transition from processing hard scrap to blow-molded scrap with the push of a button. “Some of the settings in that machine are preset; you simply push a button, and it goes from a mode of being able to effectively handle one material type to effectively handling another,” he says.
Versatility is key. Burt says a variety of two-stage systems could be customized toward specific types of plastic. For instance, Weima offers shredder-granulator systems with a horizontal layout for long products, such as window profiles, board scrap, carpet and polyvinyl chloride (PVC) flooring.
“Weima is flexible enough to be able to tailor our system to meet specific needs depending on what the application goals are,” he says.
Get curated news on YOUR industry.
Enter your email to receive our newsletters.
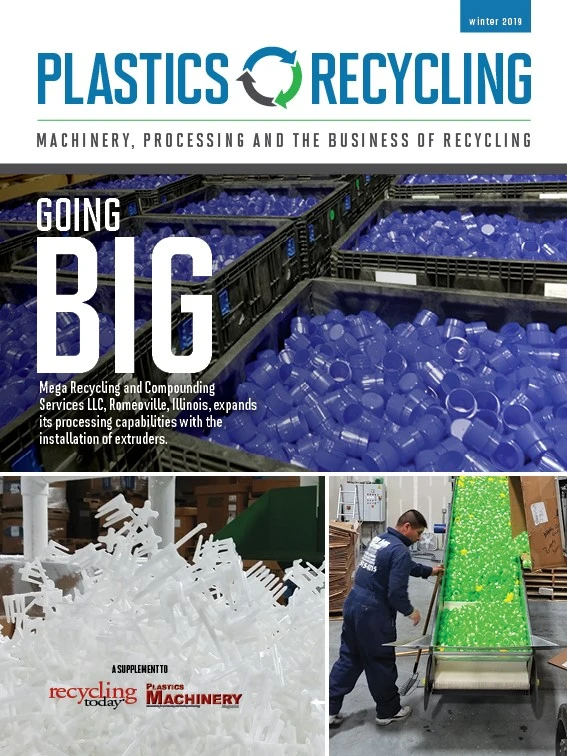
Explore the February 2019 Plastics Recycling Issue
Check out more from this issue and find your next story to read.
Latest from Recycling Today
- Toppoint Holdings expands chassis fleet
- Lego creates miniature tire recycling market
- Lux Research webinar examines chemical recycling timetables
- Plastics producer tracks pulse of wire recycling market
- Republic Services, Blue Polymers open Indianapolis recycling complex
- Altilium produces EV battery cells using recycled materials
- Brightmark enters subsidiaries of Indiana recycling facility into Chapter 11
- Freepoint Eco-Systems receives $50M loan for plastics recycling facility