
According to the Brussels-based World Steel Association, the recovery and use of steel industry scrap and
Global scrap consumption in 2015 stood at 650 million metric tons, while the global seaborne trade of scrap stood at around 84 million metric tons in 2015 (an average of approximately 7 million metric tons per month).
Scrap has become an important component in Chinese steelmaking. Between 2010 and 2015, when China’s crude steel production grew by 26 percent, its scrap consumption for making crude steel grew by almost 34 percent.
Breaking down China’s scrap use
The production of crude steel in China in 2015 stood at 803.8 million metric tons. Six percent of this was made in electric arc furnace (EAF) mills, which comes to around 48.2 million metric tons. The induction furnace route produced around 40 million metric tons of crude steel, while the figure for the BOF (basic oxygen furnace) method stood at 715.6 million metric tons.
The scrap intensity in Chinese EAF furnaces is around 550 to 600 kilograms (1,200 to 1,300 pounds) per metric ton. At this charge level, that translates into 28.9 million metric tons of scrap usage in the EAF sector in China.
In the induction furnace sector, the scrap intensity is around 1,000 to 1,100 kilograms (2,200 to 2,400 pounds) per metric ton of crude steel made. At that level of charging, that means some 40 million metric tons of scrap usage for 40 million metric tons of steel produced via induction furnace.
Iron and steel foundries in China are reported to have consumed about 15 million metric tons of scrap in 2015 to create about 30 million to 35 million metric tons of foundry products.
As per a report from McKinsey, total scrap consumption in China in 2015 stood at 180 million metric tons, which translates into 96 million metric tons of scrap used in China’s sizable BOF sector (at a scrap intensity of 134 kilograms, or 295 pounds, per ton of steel produced).

Argus Steel Feedstocks, in a report dated April 25, 2017, states, “The provinces have been instructed to cut off power and water supplies to scrap-fed mills and demolish induction and electric arc furnaces to ensure operations do not [re]start.”
Sources in China indicate the authorities actually are in the field to dismantle the scrap-fed mills, particularly the induction furnaces and those EAFs that are already idle. The deadline for the closure of such mills was June 30, 2017.
What happens if the Chinese authorities have succeeded in achieving what they have set out to do?
New scenarios
If the Chinese authorities have succeeded in shutting down induction furnaces and some EAFs, we are looking at a reflowing of almost 5.75 million metric tons of scrap per month in the market. This is over and above the 7 million metric tons already available for export from China. If they succeed in demolishing only the induction furnace mills, this still creates about 3.3 million metric tons per month of scrap suddenly becoming available for export.

In either situation, we are staring at a bloodbath on the ferrous scrap price front and severely altered dynamics of the global scrap trade.
This sudden influx will lead to a sharp drop in prices of ferrous scrap totally, altering the trade dynamics. In
During the week of May 8, 2017, Taiwan was reported to have booked Chinese-origin shredded grade scrap at $240 CFR (cost and freight) Taiwan. (Since China has a 40 percent export duty on scrap, and assuming $5 as freight, the effective FOB price comes in at $167). May 10, it was reported that Japanese Steelmaker Kyushu Works received a small shipment of scrap from China.
Platts has reported that regional scrap importers Tokyo Steel and Taiwan’s Feng Hsin have ordered trial lots of Chinese scrap, while South Korea’s Hyundai Steel is inspecting scrap in China this summer. Chinese material has even been offered into India, with talk that some containerized sales have been completed.
A media report dated May 17 states, “In South Korea, mills were not interested in U.S. deep sea cargoes after the recent emergence of Chinese scrap exports about four weeks ago.” The buyers have started demanding a price lower by $10 to $20 per ton for U.S. deep sea bulk heavy melting steel (HMS).

Though the steelmakers have booked small shipments as of now, speculation is rife that they are evaluating the scrap quality. If the quality is proven and found up to the mark, Asian scrap buyers and traders heading to China for their supplies likely is a foregone conclusion.
Thus, reports are that Chinese scrap availability, despite the 40 percent export duty, already has impacted the Asian scrap market, with Southeast Asian mills starting to hold off from booking scrap from elsewhere.
In 2015 Asian countries imported 26.5 million metric tons of scrap. With almost 40 million metric tons of scrap becoming available in an adjacent nation, existing suppliers will either look at new markets or just simply drop the price and bear the brunt. The chances of the latter are high, leading to reduced margins and resulting in traders exiting the business.
Discerning a timeline
Let’s presume that China replaces its induction furnace and older EAF capacity with newer EAF mills. This will require an additional 66.7 million metric tons of EAF capacity to be set up to consume the 40 million metric tons of scrap unused by induction furnaces.
Assuming a lead time of 18 to 24 months to set up an EAF unit (provided all the units are set up simultaneously), we are looking at a period of 24 months during which the scrap trade will be disrupted badly, primarily because the Chinese companies collecting and trading scrap would rather receive cash for their scrap by trading it rather than piling up their inventories.
Moreover, steel demand in China already may have touched its peak in 2014. Despite some factors working to increase demand, including urbanization and the development of western China, China’s steel demand will continue to fall modestly in the medium to long term. This will occur in part because of slower economic growth, particularly the stagnant growth of steel-consuming industries, including construction and manufacturing.
At the same time, infrastructure in China is entering a replacement phase, with huge quantities of obsolete scrap getting generated each year. As per the McKinsey report, China’s scrap supply is likely to grow at the rate of 4 percent to 5 percent per year, reaching a level of 340 million metric tons by 2030—an increase from 160 million metric tons in 2015.
The question remains as to where this extra scrap generated per year will be consumed. Will China actually set up EAF capacities to consume the extra scrap? This is highly unlikely.
Can China consume the increased quantities of scrap in steelmaking through the BOF route? A small quantity, yes, but not the whole. The scrap intensity in China’s BOF sector in most of its better-developed steelmaking facilities is as high as 180 to 200 kilograms (400 to 440 pounds) per ton, so only a small amount of additional scrap can be used in that way.
The decline in Chinese steel demand coupled with increasing protective measures adopted by countries where China has been dumping finished and
If China does cut down on its steel output, this means its home and prompt scrap production will come down at the same time. However, this will be offset by the higher amount of obsolete scrap generation. As indicated earlier, the overall scrap generation will grow to 340 million metric tons in 2030. That’s a huge amount of scrap to be consumed by the Chinese iron and steel industry on its own.
How and when the global scrap disruptions caused by Chinese exports will be brought under control will depend on China’s willingness and ability to shift to the EAF method of steelmaking in a big way. Though
China cannot just wish away its BOF capacities and switch over to EAF, as this may warrant mass shifts of labor from BOF facilities to other units, which is more easily said than done. Second, if this move is implemented, it also will put a strain on existing power capacities. Many renewable power resources, which are developing at a very fast pace in China (particularly solar power generation capacity), likely will be diverted toward residential and other uses. However, the power generated through thermal sources very well can be diverted for EAF method steel mills. How soon this can happen is the big question to be answered.
Third, the BOF steelmakers may look for newer technologies to increase their scrap intensities. How soon these technologies can be developed and implemented, again, begs an answer.
Until answers are found, we could be in for a period where ferrous scrap prices will be southward bound, China will become a happy hunting ground for scrap traders and many scrap yard owners will face a tough time operating at the likely price levels. This disruption will last long enough to alter the trade dynamics for a prolonged period that will establish Chinese scrap prices as the “new normal.”
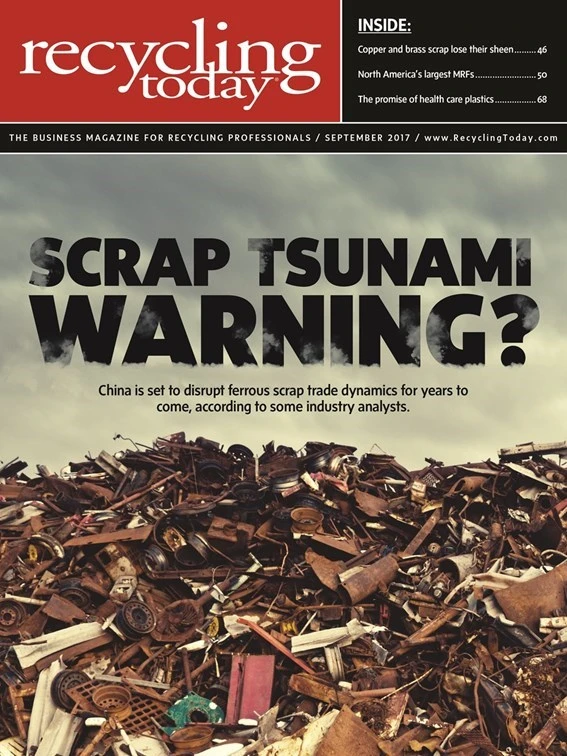
Explore the September 2017 Issue
Check out more from this issue and find your next story to read.
Latest from Recycling Today
- ReMA board to consider changes to residential dual-, single-stream MRF specifications
- Trump’s ‘liberation day’ results in retaliatory tariffs
- Commentary: Waste, CPG industries must lean into data to make sustainable packaging a reality
- DPI acquires Concept Plastics Co.
- Stadler develops second Republic Services Polymer Center
- Japanese scrap can feed its EAF sector, study finds
- IRG cancels plans for Pennsylvania PRF
- WIH Resource Group celebrates 20th anniversary