

A partnership between SABIC and Malaysia-based plastics recycling company Heng Hiap Industries (HHI) to produce circular polymers from advanced recycling of ocean-bound plastics (OBP) is paying off as customers introduce products using the recycled plastic.
Since Saudi Arabia-based SABIC announced the partnership about 18 months ago, products ranging from food packaging to packaging labels have used the recycled plastic, according to Matthew Marks, leader, circular economy, Americas, at SABIC’s Petrochemicals business unit.
“Our certified polyolefins from ocean-bound plastic are available globally, although, as with any such novel initiative, initial volumes are limited,” Marks says. “The supply chains and processes for recovering ocean-bound plastics are very new and are still in the early stages of development. The intention is to increase these volumes over time as the supply chain continues to build and infrastructures develop.”
HHI partners recover the discarded plastic from ocean-feeding waterways and inland areas, primarily in Malaysia, within a 31-mile radius of an ocean. The OBP recovered is sorted and separated, ready for processing by mechanical or advanced recycling.
“Thanks to the integrated approach, the recovered plastic can be sent to one of these routes according to its suitability and material makeup,” Marks says.
The recovered material slated for advanced recycling is sent to HHI, where the company converts the used mixed plastics into pyrolysis oil, which SABIC then uses in place of traditional fossil materials in manufacturing certified circular polymers sold as part of SABIC’s TruCircle portfolio.
Pyrolysis is a type of conversion technology that uses heat and chemistry in a reactor to break down the plastics into an oil-like liquid feedstock, Marks says.
“The process takes place in [the] absence of oxygen to ensure high-quality products,” he adds. “Potential contaminants are isolated and removed. The produced oil re-enters the chemical production chain at the refinery or cracker level as secondary raw material, replacing virgin feedstock. The resulting products are used to manufacture chemicals, including plastic of identical quality to those [of] traditional fossil materials.”
The material has been certified under the Zero Plastic Oceans accreditation, and HHI is the first organization to receive certification confirming the material it recycles qualifies as ocean-bound, according to SABIC. France-based Zero Plastic Oceans is a nongovernmental organization dedicated to addressing plastic pollution.
“Together with SABIC, HHI currently aims to collect approximately 2,000 tons annually of plastics that has the potential to end up in our oceans,” Marks says.
SABIC and Polivouga, a Portugal-based flexible film products maker, announced a collaboration last year to produce frozen seafood packaging. SABIC uses postconsumer OBP recycled through pyrolysis technology to produce certified circular polymers: SABIC linear low-density polyethylene (LLDPE) and low-density polyethylene (LDPE). Polivouga uses those polymers to produce flexible packaging for Nueva Pescanova Group, a Spanish seafood company.
The collaboration was SABIC’s first TruCircle project using certified recycled OBP polyethylene (PE), the company says.

“This is an exciting circular packaging solution for us since it demonstrates how used plastic that has the potential to end up in our oceans can be brought back into a circular material stream to be converted into high-quality food packaging,” Sami Al-Osaimi, SABIC vice president of PE and sales, said when announcing the partnership.
The PE film manufactured using feedstock made from recycled OBP is approved for food contact and offers the same tear and puncture resistance as competing PE packaging made from virgin fossil PE resins, Polivouga CEO Tiago Barros said at the time of the announcement.
Another product comes from UPM Raflatac, a global supplier of label materials, which in June 2022 introduced its new Ocean Action label made with SABIC’s circular polyolefins from OBP.
“It does not only help prevent the plastic waste from ending up in the oceans but also offers brand owners the possibility to meet their recycled content targets for packaging,” Eliisa Laurikainen, business development manager at UPM Raflatac, said when announcing the product. “The Ocean Action label material is an easy-to-use drop-in solution created especially for food and cosmetics end uses as it has exactly the same performance as the current fossil-based labels.”
Ocean Action label material is available as white and clear top-coated polypropylene (PP) films with RP37, RF37 and RP74 adhesives and polyethelyene terephthalate 23 PCR and glassine liners, Hesinki-based UPM Raflatac says.
It sources film from Taghleef Industries. Headquartered in Dubai, United Arab Emirates, Taghleef uses granulate produced in the process to make the film.
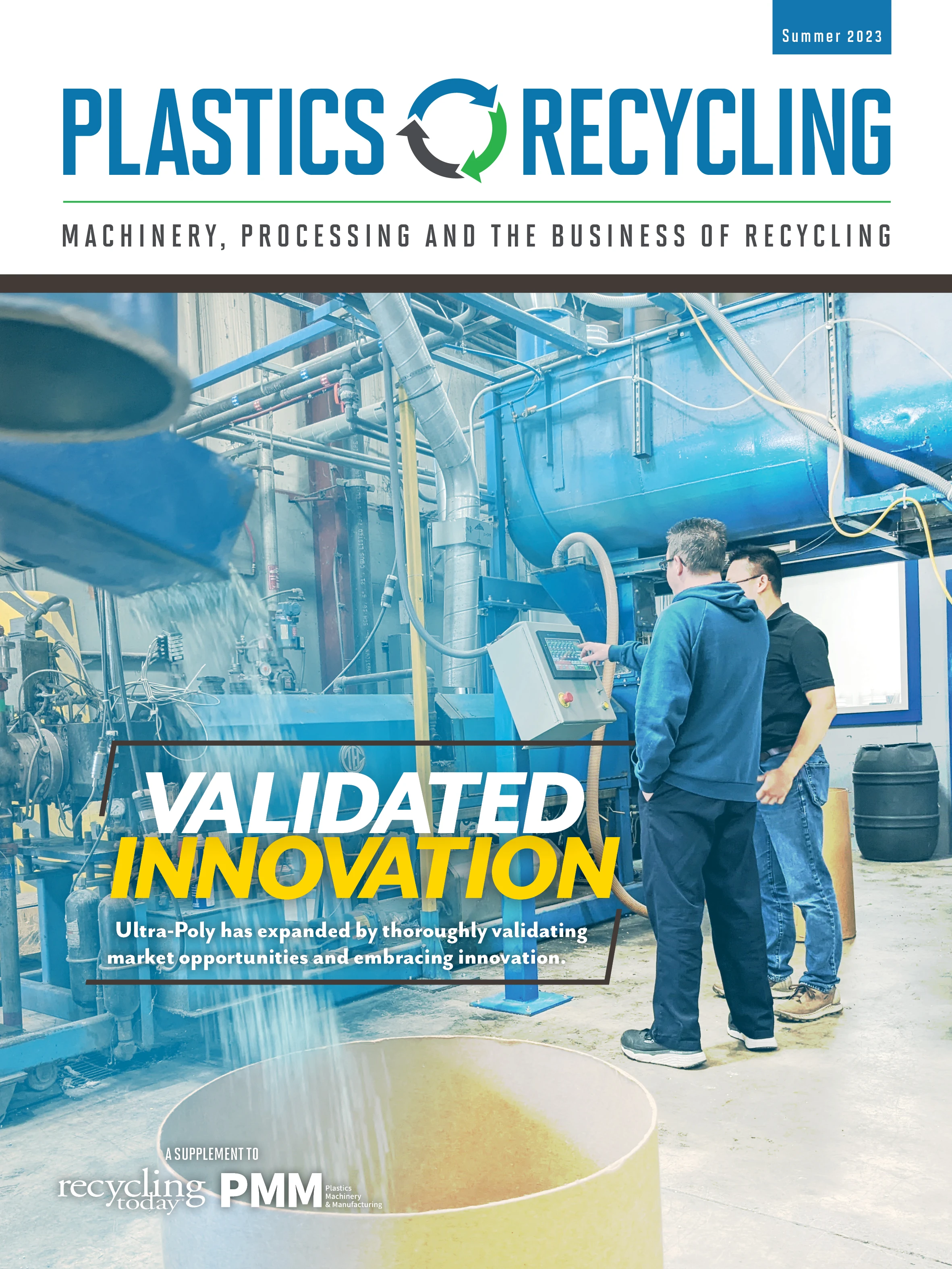
Explore the Summer 2023 Plastics Recycling Issue
Check out more from this issue and find your next story to read.
Latest from Recycling Today
- Tomra applies GAINnext AI technology to upgrade wrought aluminum scrap
- Redwood Materials partners with Isuzu Commercial Truck
- The push for more supply
- ReMA PSI Chapter adds 7 members
- Joe Ursuy elected to NWRA Hall of Fame
- RRS adds to ownership team
- S3 Recycling Solutions acquires Electronics Recycling Solutions
- Nextek, Coveris to recycle food-grade plastic film