
Iron foundries have been part of the North American business landscape since the 17th century, and by the early 19th century, cast iron pipes were being produced in the northeastern United States.
By that measure, North Carolina-based Charlotte Pipe and Foundry Co., founded in 1901, could be viewed as a relative newcomer, but the company has been manufacturing iron pipes for more than 120 years.
Charlotte Pipe and Foundry hasn’t rested on its legacy despite its lengthy tenure, however, and its forward-thinking nature is visibly evident in the form of a $460 million greenfield iron foundry the company commissioned last year in Oakboro, North Carolina.
Staying true but not standing still
“Charlotte Pipe has always been committed to investments that will benefit our associates, our customers and our shareholders,” Roddey Dowd Jr., vice chair of the company’s board of directors, said at an October 2023 groundbreaking event to celebrate the new facility.
Referring to its century-old foundry in Charlotte, North Carolina, which has been phased out with the opening of the Oakboro facility, Dowd added, “While our Uptown Charlotte location has provided stakeholders with a solid platform to deliver outstanding results, our new Oakboro foundry will allow a more efficient layout of our plant and equipment and give us the flexibility to expand to meet future needs.”
Investing to grow and diversifying are not new concepts for the 2020s philosophy at Charlotte Pipe. As a fifth-generation, family-owned company, each of those generations seems to have taken steps to ensure Charlotte Pipe remains relevant in its core plumbing products and iron foundry markets.
The company launched a plastics division in 1967 following investments in iron foundry automation and technology in the 1950s, correctly gauging future market interest in lightweight and affordable plastic pipe alternatives.
Charlotte Pipe’s geographic expansion got underway in the 1980s with facilities in Texas and Pennsylvania.
Succeeding Dowd family generations and other company leaders added more product lines over the years, particularly in the growing plastic pipe sector, and added or acquired facilities in Alabama, Florida and Utah. Currently, the company is designing and building a 134,000-square-foot polyvinyl chloride (PVC) pipe production facility near Wichita, Kansas.
In the metals sector, Charlotte Pipe made a major commitment with the 2022 acquisition of Neenah, Wisconsin-based castings firm Neenah Enterprises, which operates as a wholly owned subsidiary.
Neenah, with roots of its own tracing back to the 19th century, operates construction and industrial casting foundries in Neenah as well as in Medley, Florida, and Lincoln, Nebraska.
Throughout the last several years, even as the company acquired new foundries and expanded its plastic pipe production portfolio, the leaders at Charlotte Pipe were drawing up and finalizing a plan to relocate and modernize its flagship iron foundry.

Best (and carefully) laid plans
Moving the foundry 35 miles from its Charlotte location to outlying Oakboro was far from impulsive and not caused by feeling unwelcome in its long-time home, the company says.
“Building a new foundry to replace our existing Charlotte plant was first contemplated in the 1960s and then again in the mid-2000s,” Bradford Muller, vice president of corporate communications, tells Scrap Recycling. “We have long considered relocating because we were landlocked in our Uptown Charlotte site.
“There was no pressure from the local community or elected officials in Charlotte for Charlotte Pipe to move.”
Instead, the move was prompted by a restriction on growth opportunities at its historic site.
When announcing the start of the Oakboro project in 2020, the company indicated it had invested heavily in capital equipment, environmental control technology, infrastructure and people during the previous decades to operate an “efficient, modern [and] safe foundry” at its existing location.
“However, after long and careful consideration, the board of directors has made a determination that it is in the best interest of the company to build a new, state-of-the-art foundry,” the company said at the time.
How production lines connect and how hot and cold metal, material handling equipment and people operate can all be upgraded when a company draws up a new floor plan.

The planners at Charlotte Pipe also kept in mind its critical feedstock of ferrous scrap, which provides a large percentage of the raw material for the new Oakboro facility, which will consume as much as 150,000 tons per year.
The company seeks out clean auto cast, 2-foot plate and structural, or P&S, and shredded clips as ideal scrap grades for its cast house and casting lines.
Charlotte Pipe buys sufficient volumes, so rail shipping can be cost-effective. The company added a rail spur to connect its new plant to the short-line Aberdeen Carolina & Western Railway, which crosses central North Carolina.
The Aberdeen line connects to the Norfolk Southern Railway, giving the Oakboro foundry rail access to bring in ferrous scrap from the East Coast and the Midwest.
“With our rail system, we can procure scrap from northern Michigan down to Miami, Florida,” Muller says. “Typically, our scrap comes from the Eastern Seaboard from New York to Savannah, Georgia.”
On the outbound side, many of the company’s shipments depart via truck, with an exception. “We ship cast iron pipe and fittings (finished goods) via rail to only one location, our warehousing facility in Cedar City, Utah, to better serve our customers in the western United States,” Muller says.
The investment in rail service is one of several that has Charlotte Pipe optimistic about its future in Oakboro and beyond.

Preparing for a long-term future
Although Charlotte Pipe had considered building a greenfield foundry for more than 50 years, several circumstances aligned within the past five years to greenlight the significant investment.
“We had operated on the current site for more than 100 years, and we were finally able to successfully build the new foundry after acquiring sufficient land and capital necessary to complete the project,” Muller says.
The land the company acquired in Oakboro gives it 700 acres on which to build and grow.
“In July 2020, we broke ground on an ambitious $460 million plant, which opened in September of 2023,” he adds. “At its peak, the project saw upwards of 500 men and women on the job site each day, resulting in more than 1.2 million man-hours worked over three years.”
Charlotte Pipe has invested $58 million in the Oakboro plant’s environmental systems and controls, including an on-site 70,000-megawatt substation. Such investments are not new or exclusive to Oakboro, the company says, noting all Charlotte Pipe products are made in the U.S. and “meet or exceed federal, state and local environmental regulations and standards.”

On the technology and automation side, Charlotte Pipe says it uses the latest tooling and machinery to meet increasing demand and makes investments in process improvements and equipment that have led to increased productivity and shortened lead times.
Charlotte Pipe describes the foundry in Oakboro as one of the largest and most modern in the world and says the investment ensures the firm will remain deeply rooted in the Charlotte region and continuously operate in North Carolina.
“A generational project, the relocation and expansion of our legacy foundry is a strategic move by Charlotte Pipe to improve its processes and offerings in ways that will allow the company to continue serving the plumbing industry and our community for the next 100 years,” CEO Hooper Hardison says.
The idling of the old foundry in Charlotte’s Uptown neighborhood also has created a property development opportunity for Charlotte Pipe.
In late 2022, the company engaged Dallas-based real estate services and investment company CBRE to market its 55-acre parcel of land in Charlotte, likely after a sizable industrial dismantling and demolition project takes place.
The now up-and-running Oakboro foundry and the $80 million PVC pipe production project underway in Kansas have Charlotte Pipe poised for a future that will allow it to remain one of the largest makers of cast iron and plastic pipe and fittings in the U.S.
Get curated news on YOUR industry.
Enter your email to receive our newsletters.
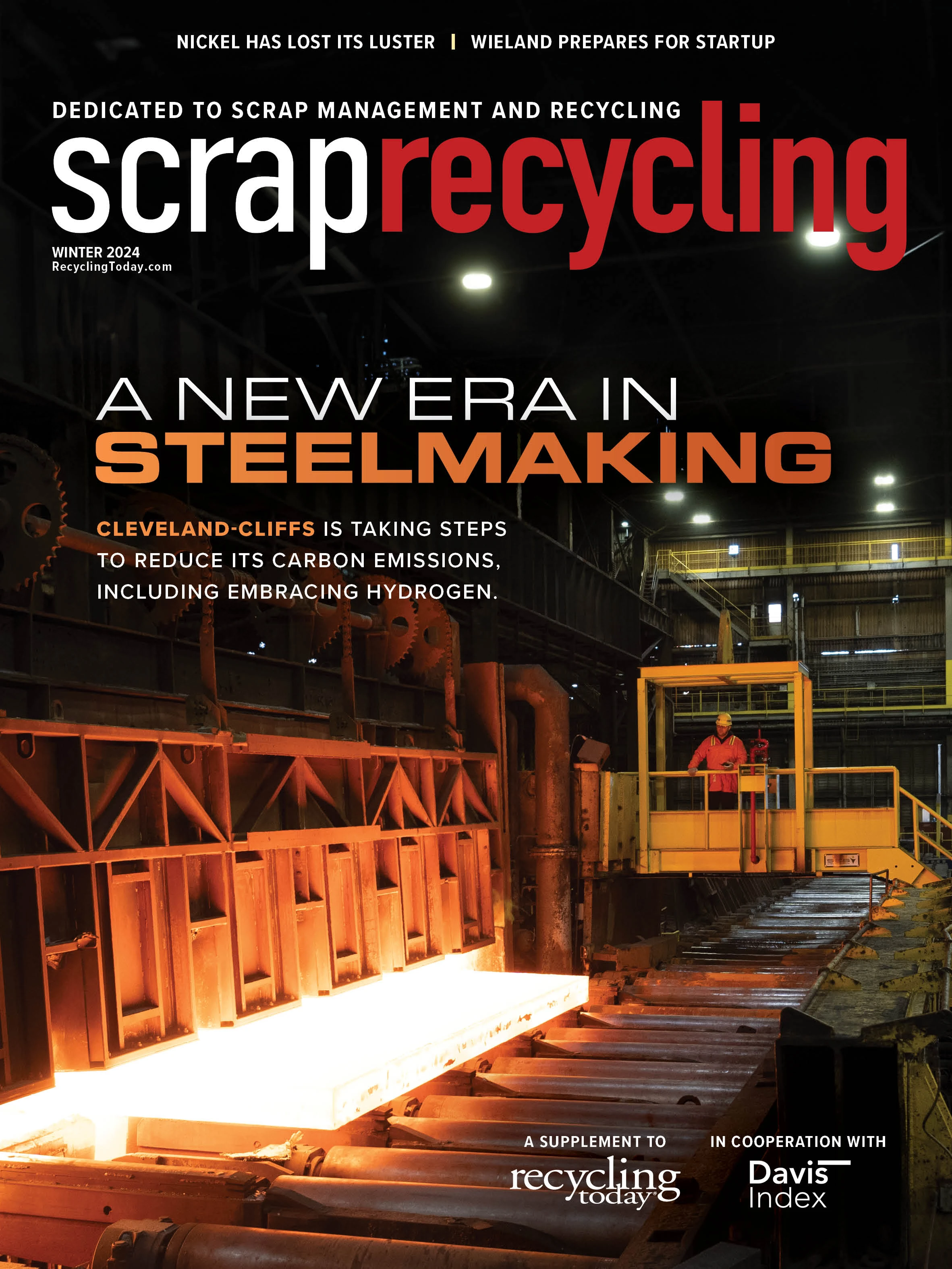
Explore the Winter 2024 Scrap Recycling Issue
Check out more from this issue and find your next story to read.
Latest from Recycling Today
- Republic Services, Blue Polymers open Indianapolis recycling complex
- Altilium produces EV battery cells using recycled materials
- Brightmark enters subsidiaries of Indiana recycling facility into Chapter 11
- Freepoint Eco-Systems receives $50M loan for plastics recycling facility
- PET thermoform recycling the focus of new NAPCOR white paper
- Steel Dynamics cites favorable conditions in Q1
- Hydro starts up construction in Spain
- Green Cubes unveils forklift battery line