T he current trend toward single-stream recycling is driving the way recyclers purchase equipment. What was once a field of many small-to-medium-sized recycling centers has evolved into fewer, though larger, centralized processing facilities.
This movement has increased the need for faster processing capabilities in order to keep up with the immense volume of material coming into these facilities daily. All of this has driven manufacturers to achieve greater strides in equipment performance and capacity—from separators and magnetics to conveyors and balers.
Though single stream recyclers now handle a wider variety of materials, including paper, plastics, aluminum and metals, plant managers still strive to contain operating costs by minimizing the amount of processing equipment used.
MEETING NEW NEEDS. To remain competitive in this changing environment, baler manufacturers have responded by offering equipment that is not only faster, but also multi-functional, with the ability to effectively handle a large range of materials to produce various bale sizes and densities.
Today, single-stream recycling operations must effectively bale fiber, plastic, aluminum and light metals with high throughput and reliability. They must also be able to quickly change from baling one material to another. As production volumes soar at recycling facilities, so have baling capacities. Today’s models have capacities of up to 28 tons per hour of OCC. Additional baling efficiencies come into play with features such as automatic tensioning controls that can maintain optimum bale density, regardless of the material.
COMPLEX YET SIMPLE. With the demand for versatility and operator safety, baling machinery has also evolved to include more sophisticated controls. While these controls may contain complex programming, at the same time, they make operating the machine simpler, saving labor costs for employers.
Manufacturers take strides to keep controls operator friendly by employing touch-screen operator interfaces. Touch-screen control panels assist operators visually with baler set-up. The screen interface also simplifies system monitoring and troubleshooting. A well-designed touch screen can allow an operator to control the feed conveyor, the baler’s wire tier and fluffer, the bale length and product changeovers.
Large-volume processors, in particular, must consider whether they want to use a shear blade or a pre-press flap to address material sitting above the baler’s shear line at the time of compression. Shear blades are designed to cut material off at the shear line, while pre-press flaps push material below the shear line prior to compression.
Many baler models also offer optional features designed to minimize jamming during the compression cycle. American Baler has a patented "stamper" that recognizes potential jams and will automatically press material below the shear line. Operators can program the unit to repeat the "stamping" up to four times to ensure unobstructed compressions and continuous baler operation, helping single-stream recyclers seeking high productivity with minimal downtime.
For any recycler, the bottom line is total operating costs per ton of material. Cost factors that often get overlooked include electrical consumption, labor and maintenance, wire usage and final freight of baled material. Many of the large balers built today are virtually self-operating, greatly reducing labor costs. Advanced wire tiers can greatly reduce wire usage, saving thousands of dollars throughout the life of the machine. Freight costs are further reduced by equipment that consistently produces dense, heavy bales to maximize the number of bales per shipment.
Another important point brought to the forefront by the single-stream movement is equipment reliability. This involves more than simply how long the baler runs without downtime. It includes how quickly one can recover from equipment failure.
Manufacturers with a nationwide network of stocking distributors and around-the-clock, seven-days-a-week factory support are vital to keeping balers operating at full capacity. Some balers today are available with modems integrated into the machine control so that troubleshooting can be done via phone by factory technicians. Though this isn’t a catchall solution, the anticipated downtime can be greatly reduced at a minimum cost.
Equipment manufacturers would be unwise not to consider the needs of the single-stream recycling customer. However, other important factors worth consideration include price, available space, labor and maintenance requirements. The decision to purchase one large, high-production baler or several smaller, medium-to-low production balers is dependent upon the customer’s facility and its material purity and separation requirements.
Sponsored Content
Labor that Works
With 25 years of experience, Leadpoint delivers cost-effective workforce solutions tailored to your needs. We handle the recruiting, hiring, training, and onboarding to deliver stable, productive, and safety-focused teams. Our commitment to safety and quality ensures peace of mind with a reliable workforce that helps you achieve your goals.
Sponsored Content
Labor that Works
With 25 years of experience, Leadpoint delivers cost-effective workforce solutions tailored to your needs. We handle the recruiting, hiring, training, and onboarding to deliver stable, productive, and safety-focused teams. Our commitment to safety and quality ensures peace of mind with a reliable workforce that helps you achieve your goals.
Sponsored Content
Labor that Works
With 25 years of experience, Leadpoint delivers cost-effective workforce solutions tailored to your needs. We handle the recruiting, hiring, training, and onboarding to deliver stable, productive, and safety-focused teams. Our commitment to safety and quality ensures peace of mind with a reliable workforce that helps you achieve your goals.
Sponsored Content
Labor that Works
With 25 years of experience, Leadpoint delivers cost-effective workforce solutions tailored to your needs. We handle the recruiting, hiring, training, and onboarding to deliver stable, productive, and safety-focused teams. Our commitment to safety and quality ensures peace of mind with a reliable workforce that helps you achieve your goals.
Sponsored Content
Labor that Works
With 25 years of experience, Leadpoint delivers cost-effective workforce solutions tailored to your needs. We handle the recruiting, hiring, training, and onboarding to deliver stable, productive, and safety-focused teams. Our commitment to safety and quality ensures peace of mind with a reliable workforce that helps you achieve your goals.
Sponsored Content
Labor that Works
With 25 years of experience, Leadpoint delivers cost-effective workforce solutions tailored to your needs. We handle the recruiting, hiring, training, and onboarding to deliver stable, productive, and safety-focused teams. Our commitment to safety and quality ensures peace of mind with a reliable workforce that helps you achieve your goals.
The future holds the promise of machines becoming more automated and smarter, with the ability to provide additional detailed information to the end-user. This is in addition to the production reports, alarm messages and motor run-time reports that are accessible today.
Manufacturers are also seeing a boom in the types of materials being baled, including plastic, wet pulp and carpet padding. This will inevitably lead to the pursuit of new developments in baling technology.
The author is national sales manager for American Baler Co., Bellevue, Ohio. He can be contacted via e-mail at rwilliams@americanbaler.com.
Get curated news on YOUR industry.
Enter your email to receive our newsletters.
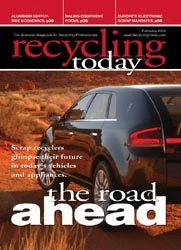
Explore the February 2004 Issue
Check out more from this issue and find your next story to read.
Latest from Recycling Today
- Altilium produces EV battery cells using recycled materials
- Brightmark enters subsidiaries of Indiana recycling facility into Chapter 11
- Freepoint Eco-Systems receives $50M loan for plastics recycling facility
- PET thermoform recycling the focus of new NAPCOR white paper
- Steel Dynamics cites favorable conditions in Q1
- Hydro starts up construction in Spain
- Green Cubes unveils forklift battery line
- Rebar association points to trade turmoil