
Throughout the past two decades, many wire and cable processors in North America have focused on recycling high-grade (high metals content) wire and cable, while lower grades largely have been baled and shipped to China.
The future of baled wire and cable shipments to China is unclear, as that nation’s government reaches final decisions and sets timetables on which forms of scrap it will either restrict or
In the aftermath of the summer inspections, wire processors in North America say it has become clear that scrap generators and smaller dealers are exploring their options in a changed landscape. Experienced wire chopping plant operators likewise will sharpen their pencils to determine whether access to additional types of wire and cable represents a genuine opportunity.

Ringing off the hook
News travels fast in the 21st century, and wire processors say it did not take long for the news of environmental clampdowns and drafted restriction policies in China to reach the United States and then create reactions.
“People have been coming out of the woodwork,” says Todd Safran of Chicago-based wire processor Safran Metals. “I think a lot of dealers are opening their Rolodexes and looking for new potential homes” for some of their material, he adds.
“A lot of lower grade material, such as cords, harness
In Kansas City, Missouri, Jeffrey Mallin of Mallin Cos. has experienced a similar level of increased inquiries. “It’s incredible how many people are inquiring with us about processing ASRs (auto shredder residues) and low-grade insulated wire.”
Brian Shine of Lancaster, New York-based Manitoba Corp. says, as of late summer, the calls he was fielding convinced him supply was surpassing demand in the wire and cable recycling sector. “We are seeing more inquiries from potential new suppliers,” he says. “I believe this is a combination of the situation in China coupled with a bleak demand picture domestically.”
Beau Janzen of California-based Copper Recovery says the situation presents opportunities for recyclers and equipment suppliers. (Copper Recovery processes wire in Huntington Beach, California, and also markets wire processing equipment.)
Janzen says irrespective of geography, scrap wire and cable ultimately is upgraded when it is separated from plastic cable, and any type of insulation and pure copper (or aluminum) is harvested.
“Ultimately somebody must chop the material to get the copper out, and somebody is making that money,” Janzen says. “When you sell copper chops, you are selling 100 percent copper, and there is always a buyer for pure copper.”
In the past two decades, he says, that activity often took place in China, while North American processors baled and shipped lower grades of wire. “While doing this can save a little time, a lot of money is left on the table. When a bale is made, the seller estimates the bale yield, and then the buyer makes his estimation in his favor to make sure he is covered,” Janzen says.
Worth the effort?

Scrap companies can accept a nearly endless variety of materials, including wire and cable with a wide range of metallic content percentages. Because the technology exists to recycle something, however, doesn’t mean the effort is practical.
North American wire and cable processors with chopping and separation equipment in place will have to be convinced that a profit margin exists for them to broaden the list of materials they will introduce into their processing systems.
Mallin says he sees significant hurdles to be overcome. “We don’t think our industry is prepared with the equipment and processes to economically and efficiently extract metal from some of these grades of insulated and contaminated insulated that have been going to export,” he says.
Shine acknowledges his firm has “been focused on exclusively purchasing and processing No. 1 insulated copper wire,” but says the time may be right to look beyond that. “There will clearly be more available low-grade materials, as they will require domestic processing to recover the copper content,” he says.
“Most processors that I visit or speak with are certainly exploring the viability of processing and then marketing lower grade copper-content items,” Shine continues. “We are now evaluating the potential to begin processing lower grade items.”
Safran says most North American processors are “not that prepared, in my opinion” to accept the lower grade material.
“Some of the choppers who have big chopping lines and need to feed their machines might welcome this opportunity, but I question the cost-effectiveness of running lower grade material,” he states.
Safran says existing demand for wire chops also may provide a hurdle. “I don’t believe at this time there are markets to [absorb] this processed material. Higher grade materials are sitting in inventory right now waiting for the market appetite to improve, so I can only imagine that the lower grade,
Josh Trudeau of Cable Management LLC, Meriden, Connecticut, says, “This is going to lead to lower prices for low-grade materials and higher margins for processors. This is the main driver behind higher sales of specialized equipment to process lower grade wires.” He lists “large turbo mills, automated curve feed hoppers, smart loop technology and
Janzen also says machinery suppliers will compete to help boost the North American scrap industry’s capacity to process more scrap wire and cable.
“Costs to process insulated copper wire (ICW) depend on many factors, and it is a volume-based number,” he says. “Lower grade ICW takes longer to process than power cable because you must cut it into smaller pieces to liberate the copper from the plastic insulation.”
Janzen continues, “Very small machines can be too slow to be flexible enough [and] profitable enough and overall are not effective for scrap dealers,” he says. “Very large machines require very significant investments in infrastructure, material logistics, manpower, etc. We believe now is a real opportunity for smaller and midsize dealers to make the shift and begin processing their own material with moderately sized and moderately priced equipment.”
Mallin, whose company is among the larger ones in the
Shine says he is aware the technology exists to recycle lower grade wire but adds that recyclers will have to perform the due diligence to see if a steady profit margin is feasible. “I believe the necessary equipment is available now; the challenge is cost-effectively processing lower copper-content materials and then marketing effectively the resultant copper generated,” he states.
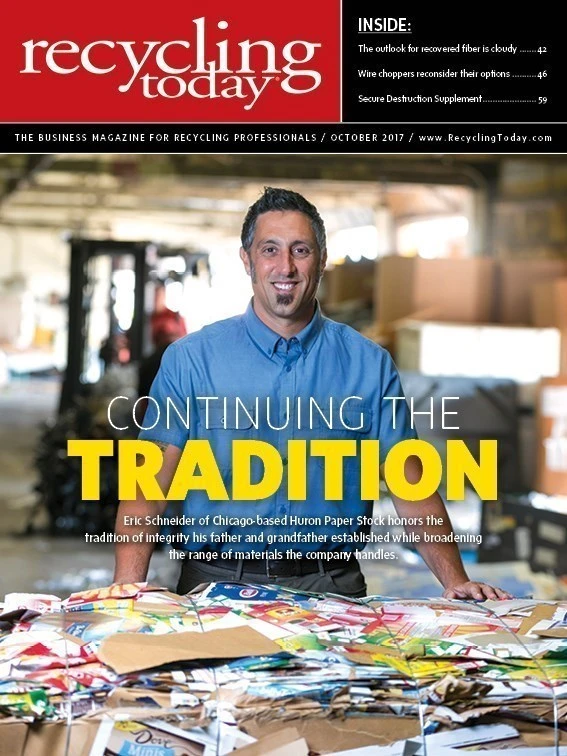
Explore the October 2017 Issue
Check out more from this issue and find your next story to read.
Latest from Recycling Today
- Two factors raise ferrous export questions in April
- Analyst: Scrap imbalance lost amid copper’s critical status
- AF&PA report shows decrease in packaging paper shipments
- GreenMantra names new CEO
- Agilyx says Styrenyx technology reduces carbon footprint in styrene production
- SABIC’s Trucircle PE used for greenhouse roofing
- Hydro to add wire rod casthouse in Norway
- Hindalco to invest in copper, aluminum business in India