_fmt.png)
Catalytic convertor processor PMR, with locations in Delray Beach, Florida; Boisbriand, Quebec; and Mississauga, Ontario, has been in the scrap catalytic converter business since 1996. In the two decades since, the company has grown from a specialized converter core buying company, relying on its buyers for converter information and toll refining results, to one of the leading converter information providers and toll refining purchasers in North America, says Chrysten Newton, marketing director of PMR Inc.
“Over the past 20 years, we have expanded operations from the ground up to include three processing facilities located across North America with a reputation built on pioneering technology as well as innovative supplier tools.”
She adds that the company is focused on delivering satisfaction and transparency to its customers in an effort to develop long-term business partnerships with its converter suppliers.
In the Q&A that follows, Newton and Cliff Hope, PMR senior account manager, share how catalytic converter compositions have changed over the years, how this has affected processing and recovery and how the company goes about valuing loads it receives from its suppliers.
_fmt.png)
PMR: Auto manufacturers will load converters with different concentrations of platinum, palladium and rhodium based on the environmental requirements of the state the car is being delivered to; the combination of precious metals that will most efficiently convert toxic gas emissions to less harmful fumes [that are] released into the environment; and lastly, the load that will do the job for the least amount of investment.
With that said, looking back 20 years, platinum did play a larger role in the value of a converter. However, in the years to follow, carmakers began to load converters more heavily with palladium due to it being less expensive.
Many suppliers fall prey to the misconception that platinum is the sole market price to be looked at when selling their converters, not knowing that over the years there has been a change in loading between the two metals (platinum and palladium). Within the current market, palladium represents more than 60 percent of metal content within a given converter and accounts for more than 3 ounces compared to 1 ounce of platinum.
Additionally, car manufacturers are using different precious metal loads in different combinations for each and every engine block.
Over the years, we have come to observe that older automobiles will have larger converters with lower loads of precious metal, while more recent models can have a much smaller converter with a higher load that exceeds the value of its older counterpart.
RT: As automakers strive to improve fuel efficiency and reduce vehicle emissions, how will this affect the metal content in autocats?PMR: There are many factors automakers are investigating to reduce emissions and improve fuel efficiency, including but not limited to using lighter materials (lighter fuel use), battery-powered systems (i.e., the start and stop button) and smaller engines (that burn less gas).
Generally, however, carmakers do not share information pertaining to PGMs (platinum group metals) content loadings within catalytic converters. As recyclers, we only discover the loadings a few years after production when the vehicles have been disassembled for processing and converters have been removed for further refining and assay.
What we can confirm is that results and assay analyses have shown a trend where newer model vehicles contain smaller engines and smaller converters that have higher loadings of precious metals than their older counterparts to adhere to increased emissions standards policies.
We cannot say for certain what effects fuel efficiency and emission standards will have on PGMs loading in converters, but we can anticipate the possibility of increased average metal loads as legislative change approaches and fuel-efficiency standards need to be followed. For instance, the Euro 6B legislation or even changes within the gasoline sector could create pressures to increase loadings of PGMs content.
RT: How does the autocat’s filter substrate affect processing?PMR: The autocat filters found strictly in newer DPF (diesel particulate filter) models (first introduced around 2006) do not affect in-house processing significantly. These filters undergo similar step-by-step handling; however, [they] need to be separated prior to smelting.
RT: Are you encountering processing issues associated with the use of silicon carbide filter substrates? How much of the incoming catalytic converter stream do these devices currently represent compared with ceramic substrates?PMR: The primary issue with silicon carbide filters found in newer DPF models is encountered during the smelting process. The silicon carbide filters require an alternate smelting atmosphere than regular OEM (original equipment manufacturer) converters, otherwise a distortion will be present in the separation of precious metals. As a result, different smelters have arranged their own procedures and differentiated recipes to handle and correct this possibility of distortion.
Silicon carbide filter substrates represent less than 5 percent of the overall catalytic converter stream within our company’s operations.
RT: How are you addressing issues related to silicon carbide substrates?PMR: As previously mentioned, the carbide filter material undergoes independent treatment, where a concentrated balance is produced during processing. Consequently, final results are not affected during the separation of precious metals.
RT: How can auto salvage operations best prepare autocats for shipment to your company?PMR: PMR guarantees simple shipping solutions for our suppliers, where we do all work upon delivery. All that is required from our suppliers is to send us their stocked and shrink-wrapped Gaylord boxes of converters and, upon receipt, ceramic, foils and DPFs are separated in-house. It is as simple as (1) fill your box and (2) ship to us.
RT: How do you value these incoming shipments?PMR: The only way payment for a load of catalytic converters can be accurately defined is when the converters have been decanned, the ceramic has been crushed and commingled and a sample of the load has been taken into the lab for testing. It is this assay that determines the recovery amounts of precious metals.
PMR takes representative samples from individual shipments (or even per location for some larger suppliers) and analyzes them by XRF (X-ray fluorescence) and ICP (inductive coupled plasma) technology to determine the total value of the load.
RT: What other services do you offer to suppliers?
PMR: As an all-inclusive processor of auto catalyst (including foil, ceramic, DPF and O2, or oxygen, sensors), PMR’s services include but are not limited to:
1. small lots – We deliver assayed results for volumes starting at 100-plus units. While most toll refiners require an average weight of 2,000 pounds, PMR is able to offer accurate refined returns starting at 250 pounds of material, allowing smaller producers to deal direct and larger producers to gain separate assay results for their multiple locations.
2. fast settlement – Final assayed results are available within 10 business days along with the option of 100 percent payment upon hedge.
3. photo grading app – This allows a supplier to send in photos of their converters (or converters they plan to purchase) and obtain fast pricing results, which they can later add to their converter inventory.
4. education and information – With a database of more than 22,000 converters, PMR offers refined pricing knowledge to its suppliers, allowing them to search converters by make, serial number, grade and country of origin.
5. PMR Supplier Services Platform (SSP) – Along with grading and pricing tools offered within the platform, PMR suppliers are able to manage their converter inventory, keep track of present and historic lots along with settlement invoices as well as access historical precious metal market data.
6. hedging flexibility – Hedging precious metal ounces is avail- able 10 days prior to shipment to a PMR facility, and no reductions will be made on current world market pricing at time of hedge. PMR allows suppliers to hedge one, two or all three metals anytime during business hours.
7. shipping solutions – PMR’s brokerage partnerships offer our suppliers not only the most economical shipping solutions but also the most simple and efficient handling with automated transport documents.
RT: What role does hedging play in your business?
PMR: Hedging plays a powerful role in business functions for our suppliers and can represent significant variations in return depending on when hedges are made. PMR is not a trader and does not play the market, but we do make that option available to our suppliers. As previously mentioned, PMR provides hedging flexibility for suppliers, which creates more opportunities to hedge at favorable market rates.
Get curated news on YOUR industry.
Enter your email to receive our newsletters.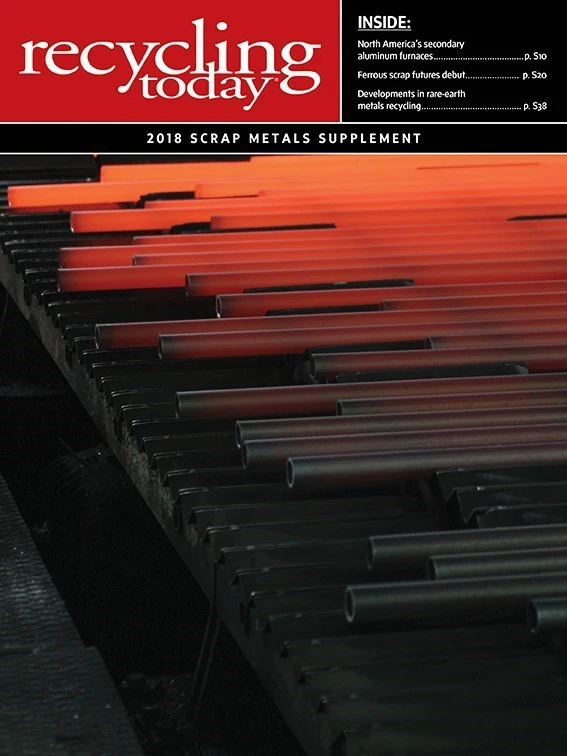
Explore the January 2018 Scrap Metals Supplement Issue
Check out more from this issue and find your next story to read.
Latest from Recycling Today
- Athens Services terminates contract with San Marino, California
- Partners develop specialty response vehicles for LIB fires
- Sonoco cites OCC shortage for price hike in Europe
- British Steel mill’s future up in the air
- Tomra applies GAINnext AI technology to upgrade wrought aluminum scrap
- Redwood Materials partners with Isuzu Commercial Truck
- The push for more supply
- ReMA PSI Chapter adds 7 members