Europe has led the way in requiring the electronics industry to collect and recycle its growing amount of end-of-life products. While several countries have already established mandatory recycling, the Waste Electrical and Electronic Equipment Directive (WEEE) will become effective in every EU member state in 2005, followed by required collection targets in 2006.
The U.S. is not too far behind. At last count, some 36 electronics waste bills were being developed in more than 10 U.S. states. While many are focused on leaded-glass-containing computer monitors and TVs, some states like New Jersey have specifically targeted cellular telephones. The implication for all electronics products is becoming increasingly clear: Recycling of consumer electronics goods will be a growing business.
Within the U.S. recycling industry, dedicated electronics treatment facilities are rapidly developing. A report by the International Association of Electronics Recyclers (www.IAER.org), Albany, N.Y., states that more than 1.5 billion pounds of electronic equipment was processed last year in the United States.
Nonetheless, many original equipment manufacturers (OEMs), including some makers of portable devices, are still learning to manage end-of-life electronics. Portable devices are typically made up of a printed circuit board (PCB) and one or more thermoplastic and/or metal enclosures. (You can verify that this is very popular design strategy by looking around your home, office or even in your pocket.) Challenges involved in recycling electronics are distinctly different than the proven methods for processing paper, consumer plastics, aluminum or steel. For instance, recovering the glass from TVs or computer monitors is a distinct specialty that has recently developed.
GETTING PRECIOUS. Materials with the most limited use by percentage and yet the highest economic value will drive the materials recycling process.
A decision point on the recycling process will likely be based on the content of precious metals, including gold, palladium and silver, while copper is another consideration. OEMs have been fortunate that considerable compatibility exists between PCBs and existing metal smelting operations. Recovery efficiencies for the copper and precious metals are typically found to be greater than 90 percent.
Typical Amounts of Basic Materials in Printed Circuit Boards |
Polymer, glass reinforcement & ceramics 70% Copper 16% Solder (tin/lead) 4% Iron 3% Nickel 2% Silver 0.05% Gold 0.03% Palladium 0.01%
Data from Drs. Martin Goosey and Rod Kellner, “A Scoping Study- End-of-Life Printed Circuit Boards.” Dept. of Trade and Industry, UK (www.cfsd.org.uk/seeba/seeba_reports.htm) |
Some have considered the higher-valued PCBs to be a feedstock that is as good as or better than mined ore. Use of precious metals is required in some critical components and circuits, and palladium or silver may be used in some applications. While increasing the precious metal content would certainly favor recycling, practically speaking, cost limitations in the design will nonetheless keep their use to a minimum.
One of the main issues in PCB recycling is pretreatment. While the organic materials can be incinerated and reduced to ash before smelting to refine the metals, this leaves the majority of the low-valued ash, glass filler and ceramics from components to be treated as solid waste. New technical approaches include novel uses of progressive shredding and size reduction, in some cases employing shear-force acceleration to separate composites, followed by sorting based on density and electrostatics/electromagnetics.
Today, the maximum amount of material that is recyclable from epoxy-glass PCB assemblies is limited to the dominant and recoverable precious metals, which may be only 20 percent to 30 percent. From a product design perspective, different ways of increasing the overall recycling efficiency—defined as the mass of material recycled divided by incoming mass of product—has been identified through design-for-environment software.
One solution is that for a given design, increased use of some highly recyclable, non-PCB material, such as housings made of a single thermoplastic or, better yet, a metal alloy, can raise the overall recovery rate of the product. In other words, to offset the low recyclability of a PCB, using more recyclable material outside of the PCB can increase the overall amount of product that can be recycled.
An example of a relatively recyclable product we have found is a desktop battery charger with a small circuit board and a relatively heavy housing. However, the OEM cannot incorporate this design in many products that must meet strict size and weight targets.
One possible solution to increase the recyclability of PCBs beyond just metals is to not only use the available separation technology but to develop economically viable markets for filler materials based on epoxy, ceramic and glass fiber mixtures. The remaining incompatible metals can be separated from each other.
HIGH-VOLUME PLASTICS. Recycling of engineering thermoplastics is enabled by high-volume streams of a single resin type, preferably of a known resin manufacturer, with known physical properties, such as Izod impact strength, uncontaminated by other materials, such as other resin types, decorative finishes, adhesives, paper labels and metal inserts. Resin color may be of secondary importance because mixed colors can generally be blended to gray and then turned black.
Volume, however, is a key issue. If one assumes that, in the case of cell phones, some 400 million units are sold per year and that as many as 100 million could be collected for recycling, with each containing 50 grams of plastic housings, then 5 million kilograms (2.3 million pounds) of thermoplastic would be available to process per year from this source. Clearly, pooling with other feedstock would be required for ongoing processing and recycling to be viable.
There have been some successes as well as ongoing problems in making thermoplastic recycling more successful. Some research in this area can be found on the Web at www.electronicsrecycling.org/stakeholder.
WORKING TOGETHER. Equipment manufacturers can certainly use the help of electronics recyclers.
First, it is a given that all regulatory agency and company-specific requirements must be followed. Nothing will stop a business relationship faster than failing to honor certificates of destruction or having an environmental compliance issue.
Secondly, integrity in the sampling and accounting procedures is a must. OEMs know the content of their products. Data is being developed to track the content of products according to established specifications. One example of such a substance disclosure can be found on Motorola’s Web site at www. motorola.com/EHS/environment/supplier/w18.pdf.
Finally, ongoing feedback on recycling results is needed. As we enter a new area of closed-loop product stewardship, it appears that this can and will happen.
The author is with Motorola’s Environmental Technology & Analytical Services, Worldwide Supply Chain Operations in Libertyville, Ill. He can be reached at (847) 523-2993 or at Roger.Franz@motorola.com.
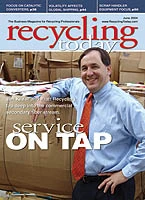
Explore the June 2004 Issue
Check out more from this issue and find your next story to read.
Latest from Recycling Today
- Reconomy brands receive platinum ratings from EcoVadis
- Sortera Technologies ‘owning and operating’ aluminum sorting solutions
- IDTechEx sees electric-powered construction equipment growth
- Global steel output recedes in November
- Fitch Ratings sees reasons for steel optimism in 2025
- P+PB adds new board members
- BlueScope, BHP & Rio Tinto select site for electric smelting furnace pilot plant
- Magnomer joins Canada Plastics Pact