T
he Golden State may have a laid-back reputation, but make no mistake—recycling is serious business in California. The state boasts one of the strongest, strictest commitments to municipal recycling inthe nation. Regulations established 15 years ago call for each California city to recycle a minimum of 50 percent of the waste it generates, which is no small order for a state with a 35 million-plus population.
San Francisco has raised the bar above and beyond what the state government has called for by setting its own goal of achieving a 75 percent recycling rate by 2010. And it’s getting there with the help of a material recovery facility (MRF) of massive proportions—Norcal Waste Systems Inc.’s Recycle Central on Pier 96.
THINKING BIG. The 200,000-square-foot, $38 million MRF started operations in the fall of 2002. On average, Recycle Central processes around 700 tons of material per day, including numerous grades of scrap paper, OCC, ferrous and nonferrous cans, glass bottles and PET and HDPE plastic containers. That comes out to more than 175,000 tons of material sorted and baled per year, though the maximum capacity of the Recycle Central is 2,100 tons per day, or 546,000 tons per year.
To help the city reach its 75 percent recycling rate, Recycle Central processes recyclables from just about every structure in San Francisco, including single-family homes, apartment buildings, condos, restaurants, office buildings, commercial areas and department stores, Robert Reed, Norcal’s director of corporate communications, says.

"That’s a tall order," Reed says of San Francisco’s 75 percent recycling goal. "San Francisco is an environmentally minded city, and Recycle Central provides key infrastructure necessary for it to provide many of the city’s more popular and effective recycling programs."
The facility is a tribute to meticulous sorting technology, employing seven recycling lines to handle the tons of material that come into the MRF jumbled together through San Francisco’s blue-bin system.
Norcal operating company SF Recycling & Disposal Inc. runs the facility, which was designed and outfitted by Enterprise Co., a Santa Ana, Calif.-based manufacturer of solid waste processing equipment.
Orval Gould, president of Enterprise, saw Recycle Central on Pier 96 and the Integrated Materials Recovery Facility (iMRF) at Norcal’s transfer station go from designs on paper to working realities. The plants took three years to design and nearly another two to construct, he says.
Gould says the sheer scale of the project was intimidating at first. "Nobody had ever made [a MRF] of this magnitude—it was a real challenge," he says. "We thought the building was too big when we started and, when we were through, it was like it wasn’t big enough."
SUPER SORTING. At Recycle Central, the curbside material begins its journey at the base of a three-level conveying and sorting system. During pre-sort, employees remove non-recyclables. The material then goes over a metal disc screen, which separates grit from the recyclables.
Grapes of Wrath |
Northern California grape growers responsible for 30 vineyard tracks have used Norcal’s Four Course Compost program, in some cases for three consecutive years, to nurture their soil. The program, which began collecting food scraps from San Francisco restaurants, bakeries, coffee shops and residences and has spread to Oakland and Los Angeles, has been a big hit for the vineyards of the Golden State, according to Robert Reed, Norcal spokesman. "Using this compost has definitely revitalized some older vineyards and enhanced the uniformity in the active ones," says Remi Cohen of Napa’s Bouchaine Vineyards, which has used Four Course for three years. "The 2003 vintage year will be the first time Bouchaine has an estate-bottled Pinot Noir and an estate Chardonnay, and I attribute the quality to our composting program." Norcal’s haulers collect about 300 tons of food scrap every day from San Francisco households and 2,330 food-related businesses in San Francisco and Oakland. Representatives from Norcal say Four Course adds nitrogen to encourage leafy growth and phosphorus to promote a strong root system. Linda Hale, supervisor of Madrone Vineyard Management Group, credits Norcal’s Four Course Compost with giving the soil balance and spurring growth at her company’s vineyards. "In 2002, we planted green-potted vines. We now have two-year-old vines that look like five-year-old vines," Hales says. "We are harvesting about 2.5 tons per acre on essentially two-year-old vines." The Four Course Compost program is made possible through the efforts of three companies. Golden Gate Disposal & Recycling Co. and Sunset Scavenger Co. collect the food scraps and other compostable materials. Jepson Prairie Organics, a composting operation located outside Vacaville, Calif., receives the materials and produces the finished compost. All three companies are subsidiaries of Norcal Waste Systems Inc. The program has piqued the interest of a number of California cities, and has even attracted attention outside the United States, Reed says. Norcal has received inquires about the Four Course Compost program from the United Kingdom, South Korea, Taiwan and Canada. |
Another disc screen separates ONP from mixed paper and containers. ONP goes over a post sort before it goes into a storage hopper to be baled by grade. The mixed paper and containers go over another disc screen, which separates them. The mixed paper goes off to post sort before being sent to storage containers for baling.
The containers go into live floor hoppers for storage. From the hoppers, they’re fed onto a container sort line, where PET and HDPE are sorted out. The line then goes under an overhead magnet, which pulls out the steel cans. The remaining material goes through an eddy current separator, which takes out the aluminum, leaving only glass, which goes over a sort belt to be sorted by color—amber, green and clear.
The remaining material, which includes small pieces of paper and dirt fines, then goes through a glass cleanup system that produces 95 percent clean mixed broken glass, Gould says.
That leaves the non-recyclables, which end up on a main conveyor that moves the material to a compactor where it is compacted and shipped to a landfill.
Recycle Central has seven recycling lines—four for dry commercial recyclables, two for residential recyclables and one for commingled containers. The facility is even equipped with a standby system that has a rubber and a metal disc screen in case the operators want to process more material than the regular systems can handle or while maintenance is being performed on the main system, Gould says.
The MRF’s commercial lines are also configured to be able to switch from positive to negative sorts, Gould says. This option gives Recycle Central more flexibility in the way materials are processed.
In addition to the facility’s positive/negative sorting abilities, all of the recycling lines at Recycle Central offer further flexibility. The ability to adjust sorting practices allows the MRF to recover different recyclables that are in greatest demand at any given time, says Reed.
Adding to the facility’s flexibility is the way it combines the efforts of automated sorting equipment with hand sorting by employees. About 138 people work at Recycle Central, most of them on the hand-sorting line.
Leno Bellomo, commodities marketing manager for Norcal, says well-trained employees who know how to recognize and remove contaminants from the material stream augment the equipment.
The workers can adjust their sorting practices to help the plant produce bales that are in the highest demand at the time, like specific grades of paper or different plastic resins, Reed says.
For instance, "If paper plants want to see more of a certain type of baled paper as feedstock, and we identify that demand in recycling markets, Recycle Central can adjust sorting practices to produce more of that type of baled paper," Reed says.
Once the material goes through the extensive sorting process, the recyclables are baled and ready for sale. Recycle Central produces 12 different types of baled commodities.
Domestic markets and several overseas customers consume resins and metals processed at Recycle Central, Bellomo says. Buyers include paper mills, glass plants and other manufacturing facilities. But paper from Recycle Central enjoys some of the highest demand, making Norcal one of the largest shippers of recycled paper on the West Coast, says Reed.
Bellomo says Recycle Central’s thorough sorting system has helped its recycled paper earn a solid reputation in foreign and domestic markets.
Looking into the Future |
Recyclers directly involved in managing operations and purchasing equipment may wish to get to the 2005 Paper Recycling Conference in time for the Sunday afternoon workshops on June 26. A workshop being organized by the American Forest & Paper Association will focus on that organization’s award-winning recyclers and recycling programs and the best practices involved. Another worskhop will feature presentations from equipment vendors who supply MRFs and recycling plants. As the demand for greater amounts of recovered fiber intensify, many recycling plants will need to handle an even greater amount of recycled fiber while at the same time, be able to source and process different grades of fiber. The 2005 Paper Recycling Conference and Trade Show will take place June 26-28 at the Hyatt Regency Atlanta in downtown Atlanta. More information on the show and online registation is available at www.PaperRecyclingConference.com. |
"We find that our material is in huge demand," he says. "Buyers know our reputation for quality mill furnish—this alleviates concerns selling globally."
In addition to the desire for flexibility, the amount of material expected to come through the Pier 96 facility was central to its design, says Gould. "Anything that works well for high-tonnage, we installed it," he says.
PARTNERS IN RECYCLING. The facility may be packed to near capacity with equipment, but that doesn’t mean there’s no room for growth. To help the city increase its diversion, Reed says Recycle Central will increase the amount of material in tons it accepts every day.
San Francisco and Recycle Central place diversion rates as the highest priority in the recycling operation. With a dozen recycling programs provided by Norcal operating companies at the city’s direction, San Francisco is already on its way to the 75 percent goal. San Francisco currently estimates that it diverts about 63 percent of the city’s waste from landfill disposal. And while many smaller MRFs across the country are facing tough decisions to cut commodities with low market value like glass, Recycle Central is under no such pressure, says Reed. "Our goal is to recycle more, not less," he says. The city also plans to direct more tons of construction and demolition debris into Norcal’s iMRF, which is also located in San Francisco and run by SF Recycling & Disposal Inc., the same operating company that runs Recycle Central.
The iMRF processes scrap metal, wood, sheet rock, concrete, asphalt and other mixed C&D material. "These materials weigh a lot," Reed says. "Far better for San Francisco to direct them through the iMRF so they can be made into new products than see them go into a landfill."
In addition, Norcal continues to expand its Four Course Compost program, Reed says. (See sidebar at right.) The program, which started in San Francisco, collects food scraps from restaurants and homes to produce compost for local vineyards and farms. Reed says the program has expanded into Oakland and is getting started in Los Angeles as well.
Recycle Central is a perfect match for San Francisco’s lofty recycling goals, says Reed. "It is important that people who want to recycle have the opportunity to recycle," he says. "We are doing everything we can to help San Francisco make steady progress toward 75 percent diversion."
Relying on its own MRF lets San Francisco manage its own waste stream, Reed says. While many cities have recycling programs in place, most have not taken the step to develop a significant recycling facility, he says.
"Cities that have not are dependent on others to process their recyclables," says Reed. "If there is a labor action or other interruption in the processing, cities that do not have their own facilities can quickly find themselves out of luck."
Having Recycle Central in its back yard gives San Francisco the opportunity to be self-sufficient in managing its municipal recycling programs. "Cities that do not have their own recycling facilities often find themselves financially dependent on outside entities like landfills and recycling operations," Reed says. Instead, Recycle Central helps San Francisco maintain independence and control of its waste management goals.
The author is assistant editor of Recycling Today and can be reach at jgubeno@gie.net.
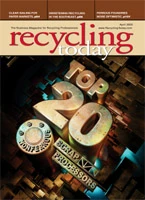
Explore the April 2005 Issue
Check out more from this issue and find your next story to read.
Latest from Recycling Today
- Fitch Ratings sees reasons for steel optimism in 2025
- P+PB adds new board members
- BlueScope, BHP & Rio Tinto select site for electric smelting furnace pilot plant
- Magnomer joins Canada Plastics Pact
- Out of touch with reality
- Electra names new CFO
- WM of Pennsylvania awarded RNG vehicle funding
- Nucor receives West Virginia funding assist