
Photo by Ryan Meza Angel Photography

For Dave Vaccarezza and his sons, Casey and Rudy, following through on their commitments and giving back to the community are points of pride. They share this ethos with the 200-plus employees of their company, Cal-Waste Recovery Systems. In fact, the company’s official motto, as well as the name of its charitable giving program, is “Giving More Than We Take.”
Rudy, the company’s director of business development, says, “We are a pure customer service company. Part of that is fulfilling the needs of customers whether they are asking directly or not.”
The Galt, California-based company provides residential and commercial recycling, green waste, organics and trash collection services in Calaveras, Alpine, Sacramento and San Joaquin counties and residential collection in the California cities of Angels Camp, Arnold, Bear Valley, Copperopolis, Galt, Lake Tulloch, Mokelumne Hill, Murphys, Rancho Calaveras, Rancho Murieta, San Andreas, Valley Springs, West Point and Woodbridge.
The Vaccarezzas’ desire to be a “progressive force” in the solid waste industry led the company to add construction and demolition (C&D) removal, concrete and paint washout and other related disposal services roughly two decades ago. Cal-Waste also opened a material recovery facility (MRF) in 2012, Rudy says, which is the same year he began working for his family’s company full time.
Today, the company operates the MRF in Galt as well as four transfer stations: one each in Galt and Sacramento and two in Calaveras County. For the last two years, the Vaccarezzas also have operated a small landfill in Arizona that is owned by Mojave County.
Casey, who is director of operations at Cal-Waste and Rudy’s older brother, says the company is successful in part because the Vaccarrezzas and their employees make a point of doing what they stay they are going to do.
While Casey joined the company six years ago after working outside the industry, he says he and Rudy have been involved in the business their whole lives, with the family home having been behind the truck yard at one point.
Casey and Rudy are the third generation of the Vaccarezza family to own and operate Cal-Waste. Their father, Dave, who serves as CEO, joined the company in 1970 when he was 23 years old.
A history of service & innovation
Colombo Vaccarezza began one of the predecessor companies that eventually would become Cal-Waste by collecting rubbish using horse-drawn wagons from residents of Lodi, California, in 1927 to provide feed for the family’s hogs. According to Cal-Waste, Colombo received the rights to haul food scraps but was required to take away the residents’ dry trash every other week, as well. Just a few years later, Cal-Waste was providing these services using four trucks.
In 1950, before formal recycling services were introduced, the company began recycling cardboard and repurposing food waste into compost to reduce the volume of material placed in the local dump. Colombo’s brother, Rudy, took over the business in 1952. By 1956, Cal-Waste was collecting refuse in an open truck, where employees sorted paper, rags, metal, glass and rubber in transit.
In 1958, the company added four new packer trucks and a modern cardboard baler that helped Cal-Waste serve 14,000 commercial and residential customers.
Cal-Waste formally introduced recycling services to the residents it served in 1989 to meet California mandates. The company distributed buckets where residents could place their glass, paper and metal for recycling.
In 2012, Cal-Waste opened an $11-million MRF featuring equipment supplied by San Diego-based CP Group to help meet a state requirement to recycle 75 percent of the commercial waste generated in California.
From the moment the MRF opened, Rudy says, Cal-Waste charged a processing fee, which is a move some MRF operators made more recently in response to the market upheaval China created when it stopped buying postconsumer recyclables from the U.S.
He says the company decided to do so because of Dave’s experience with the effects of commodity speculation in the early 1990s. From that, he concluded, “We are not material speculators, we are processors,” Rudy says.
“California is committed to recycling whether it makes money or not,” he adds. Charging a processing fee allows Cal-Waste and its municipalities to share the commodity market-related risks.
Casey says Cal-Waste is focused on providing quality service to the residents and businesses it serves, a philosophy that dates back to the 1950s and to his grandfather, Rudy. According to Cal-Waste’s website, the elder Rudy insisted that company trucks be washed daily and that drivers and collectors wear clean, white uniforms.
Today, Cal-Waste has centralized customer service, Rudy says, and employees are cross-trained to answer the variety of customer inquiries that come in. All services are customized, down to the types of equipment used on-site. “We don’t have long-term contracts but short-term ones,” he says. “That means we’re only as good as our last service. We need to show our value every time we touch them.”
The resourcefulness and innovation the company was known for in its early days lives on. Cal-Waste retrofits its trucks internally, pairing new chassis with old bodies to reduce costs. The company also splits it truck bodies in-house. “We really run a fabrication shop as well as a maintenance shop,” Rudy says.
Cal-Waste alternates every-other week between collecting municipal solid waste (MSW) and mixed recycling and MSW and green waste, Rudy says. However, with the changes in California’s organics diversion requirements, it will begin collecting mixed organics and MSW weekly this year. This will necessitate expanding Cal-Waste’s fleet by 30 percent, he says.
With new truck orders taking a minimum of 11 months to fill, Rudy says Cal-Waste “made commitments early and got creative, working with dealers to secure chassis they have to pair with bodies we have. Then the manufacturer will spec attachments to the bodies we have.” He says this approach has shortened delivery lead times to six months.
Cal-Waste has internalized container repair and was an early adopter of route optimization software, tablets and vehicle cameras, Rudy says. “The industry as a whole has done that now,” he says of the adoption of fleet-related technologies, “but we have led that charge.”
The company also was the first in the area to address food waste in institutions, such as school districts, Rudy says. He adds that more than of 90 percent of the schools in San Juaquin and Sacramento counties are working with the company to divert this material.

MRF upgrades result in service upgrades
In late 2019, after recognizing the need to reduce contamination and in light of the declining global market value for some recyclables, Cal-Waste invested about $20 million to upgrade its MRF, selecting CP Group as its equipment provider. The upgrade was designed to increase the facility’s throughput in addition to improving the purity of recovered recyclables. It also continued the company’s history of applying new innovations, as it was the first MRF to include CP’s auger screens.
Casey says the upgrade also addressed the need for additional recycling capacity in the area, while Rudy says the upgrade also shows the company’s customers that Cal-Waste is “always trying to do better.”
Cal-Waste’s revenue has grown considerably since its MRF expansion, Casey adds, which increased capacity from 11 tons per hour to 30 tons per hour, enabling the company to process more than 130,000 tons per year.
Cal-Waste receives up to 400 tons of material per day, 90 percent of which is residential recyclables. “Ten to 15 percent of the material we collect ourselves,” Casey says. “The remaining 85 to 90 percent is from other municipalities and processors.”
Rudy adds that Cal-Waste has six residential collection franchises in the area.
The MRF upgrade included the addition of a primary auger screen, a glass breaker screen, an AWScreen, a CPScreen, a scalping auger screen and five optical sorters from Nashville, Tennessee-based MSS, a division of CP Group.
“What makes our MRF a little different is we have two sets of augers,” Casey says.
The MRF uses a metering drum to deliver material to the sorting system. Its primary auger sorts based on size, with the oversized material heading to the presort line. This auger screen reduces the burden depth of the material and sorts out sharps and other small hazardous materials, so people on the presort line don’t have to encounter these dangers.
Casey says the undersized material that falls through the first auger screen goes to a second auger screen for further sizing.
The company is segregating and baling natural high-density polyethylene (HDPE), colored HDPE, polyethylene terephthalate (PET), old corrugated containers (OCC), hard pack fiber, Nos. 3-7 plastic, aluminum, tin and mixed rigid plastics, Casey says.
Despite the recent upgrade to its MRF, Cal-Waste is installing four more MSS optical units, which should be up and running by the end of April. Casey says three of the units are being added to the paper line, while one will be added to the container line. Their installation will help Cal-Waste “keep up with growing volumes and keep the diversion rate high,” he says.
Rudy adds that they will also help Cal-Waste reduce its residual rate and return more revenue to its customers.
Yet to come


The company is gearing up to process food waste, which Casey sees as a new opportunity. He says Cal-Waste is figuring out which technology to use so it can begin processing this material. As of early March, however, the company was hauling the organics it collects to another company’s facility for processing.
Rudy says a new transfer station Cal-Waste plans to open will provide it with the space to process organics and sort C&D material. The company is working to secure a location in San Joaquin or Sacramento counties and plans to complete acquisition of the land in the second half of the year and to be operable by 2024.
These new services coupled with Cal-Waste’s focus on service will help the company to grow over the next decade.
“We are a local garbage company that acts—my dad uses this term, and I’ve come to accept it—like a 95-year-old startup,” Rudy says. “We don’t rest on our laurels. We are always trying to be better than we were yesterday.”
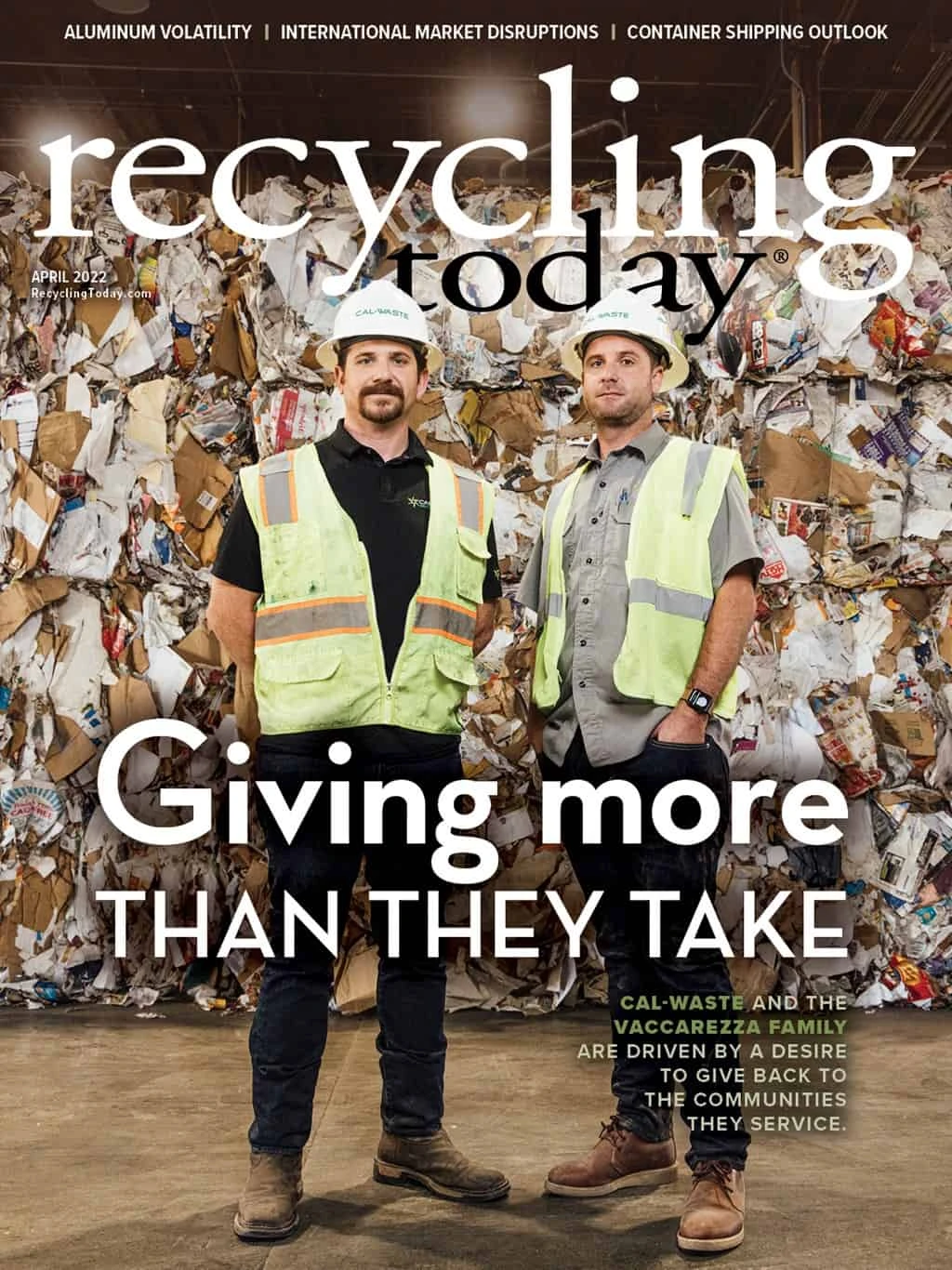
Explore the April 2022 Issue
Check out more from this issue and find your next story to read.
Latest from Recycling Today
- Radius loses money, says merger on track
- Electrostatic technology vies for role in ASR sorting
- ReMA board to consider changes to residential dual-, single-stream MRF specifications
- Trump’s ‘liberation day’ results in retaliatory tariffs
- Commentary: Waste, CPG industries must lean into data to make sustainable packaging a reality
- DPI acquires Concept Plastics Co.
- Stadler develops second Republic Services Polymer Center
- Japanese scrap can feed its EAF sector, study finds