Is it worthwhile for building contractors to consider recycling their construction and demolition (C&D) debris rather than assigning it to a landfill? The answer varies by region and even metropolitan market, but for an increasing number of contractors the answer is yes.
Some states and municipalities are taking measures to push builders down the road to recycling, while others will let market forces dictate when it’s time for contractors to consider recycling their leftover concrete, lumber, wallboard, gypsum and other building materials.
Peter Yost, project manager for the National Association of Homebuilders (NAHB) Research Center, Upper Marlboro, Md., believes there are some outstanding opportunities for budding entrepreneurs in the C&D recycling industry.
Job site clean-up services that have started up in several markets are “basically turning away business,” according to Yost, because their methods of C&D debris disposal and recycling offer several benefits to builders. In states where source separation is not mandated, such companies allow contractors to place debris in one bin or fenced-in area. The job site clean-up services then do the sorting themselves to determine what can be recycled and what goes to a landfill.
The companies profiled by Yost and co-author Eric Lund in the NAHB Research Center publication Residential Construction Waste Management: A Builder’s Field Guide offer site cleaning services that focus on making the recycling process easy for builders as well as being cost-effective and providing a clean-looking job site.
The latter benefit fits in nicely with the growing trend among homebuilders of inviting their customers to visit the job site throughout the construction process. “Just about every builder we approached [while writing the field guide] was very interested in the concept of the clean-up service,” says Yost.
But even this attractive recycling option will only be looked at by most builders if it can compete on a price basis with the standard method of contracting with a waste hauler. Haulers usually charge a weight- or time-dependent fee to bring a roll-off dumpster on site that will later be taken to either a C&D or municipal landfill. Many residential clean-up services charge an up-front fee based on the size of the house being built.
The tipping fees charged by landfills still create the greatest regional difference in the popularity of C&D debris recycling. Those fees not only vary by market, but can fluctuate within any given market based on the opening, expansion or closing of one key landfill.
In several markets, however, state or municipal governments have pushed the scales of landfill versus recycling one way or another by the way they regulate landfills or in their strictness or leniency in granting permits for new or expanded fill sites. And the federal government recently passed its first piece of legislation directed toward the operation of C&D landfills, which may result in increased tipping fees at C&D landfills in some states over the next 18 months, according to Yost.
At the local level, there are programs in place or market forces at work in a number of states and municipalities that are changing the way contractors and haulers handle their C&D debris.
PORTLAND
Oregon has long been known as a state where environmental concerns run deep. “It’s Oregon – siting a landfill is not an easy thing to do,” says Debbi Allen, president of River City Resource Group, Portland, Ore., explaining metropolitan Portland’s $79 per ton average tipping fee. High tipping fees and environmentalist leanings contributed to Portland’s status as a leader in its C&D recycling rate.
Allen and River City helped design C&D debris programs in cooperation with Portland’s regional government and industry associations such as the Home Builders Association (HBA) of Metropolitan Portland. Initial research found that in some cases up to 4.5 tons of landfilled material were being generated at single construction sites. “It was an outstanding amount of waste that had the potential to be diverted,” says Allen.
While initial efforts focused on wood and other forest products, as the program expanded, so did the recycling infrastructure. High-profile projects that focused on minimizing landfilled scrap also captured attention. The commercial contractor who built the Rose Garden sports arena in downtown Portland claimed a 92 percent diversion rate and a total of 45,000 tons of construction debris recycled. Now, the contractor building the major expansion at Nike’s corporate campus hopes to achieve a 95 percent diversion rate, according to Allen.
Even though the programs have come a long way in only six years, Allen says that convincing contractors it was worthwhile to change their methods was not necessarily easy. “It has taken a lot of effort,” she says. “Clearly, it all comes down to the bottom line. Right now, with tipping fees at that $79 rate, the bottom line benefits can be shown.”
But beyond the bottom line, Allen believes acceptance of the recycling option is growing. “I believe this whole generation of contractors has grown up with a stronger environmental ethic,” she says.
LOS ANGELES
Several hundred miles south on the Pacific Coast, dramatically lower tipping fees – and significantly lower diversion rates – exist in Los Angeles. According to Kelly Ingalls, senior management analyst for the Los Angeles Integrated Solid Waste Management Office, mixed C&D debris is being accepted at rates as low as $20 per ton outside the city and $24 per ton for material generated inside the city. “The city of Los Angeles does not have a mandatory recycling ordinance; it’s what the market will bear,” says Ingalls.
Nonetheless, there are markets for recycled debris materials in L.A. and a recycling infrastructure does exist. A guide published by Ingalls’ bureau lists more than 20 concrete and asphalt recyclers and a similar number of facilities that accept scrap wood for recycling or grinding.
The most recent study that looked specifically at C&D debris diversion rates was done in 1990, according to Ingalls, but the 1995 overview for solid waste found a 44.5 percent diversion rate for Los Angeles as a whole.
“I think the construction and demolition contractors are very cognizant of and familiar with recycling opportunities,” says Ingalls. “They’re familiar with the facilities and they’re familiar with the costs. A lot are doing it for market-based reasons.”
While it’s hard to confirm whether contractors are typically below, above or right at the overall 44.5 percent diversion rate, Ingalls said that approximately 85 percent of the debris culled from one of L.A.’s recent earthquakes was re-processed in some manner.
Markets are currently stronger for concrete and paving materials than for wood, due in part to a policy that requires paving contractors working within the L.A. city limits to account for where scarified pavement (road surface stripped from its bed) will be going. The policy has helped solidify a pavement recycling infrastructure.
CHICAGO
Just a few years ago, C&D debris was in the headlines in Chicago. They were not the types of headlines that made anyone in the Windy City very proud, however. After several high-profile cases of illegal dumping of C&D debris were prosecuted, the Daley administration looked at the recycling of debris as a way to prevent similar cases from occurring in the future.
A previous lack of enforcement, says Ken Davis, information coordinator for the Chicago Department of the Environment, had allowed dishonest companies to claim they were hauling away debris to be recycled, only to dump it illegally. One of the prosecuted cases involved an illegal dumpsite that contained about 700,000 cubic yards of road debris.
Since 1993, the city has required recyclers to have a permit and has “tripled the fines for violators,” says Davis. But he is confident that the “fake recyclers” are out of business now and that within the Chicago area there is the capacity installed to re-process concrete debris in particular.
In fact, the most striking initial success in the recycling arena in Chicago has been in the re-use of concrete and road debris. “We’re paving hundreds and hundreds of miles of roads per year now,” says Davis, who notes that the scarification method of re-paving roads creates debris that, in most cases, can successfully be recycled.
The concrete recycling infrastructure that is now in place has also steered building contractors toward recycling. “We’re now quite commonly seeing developers do the recycling of concrete material right on site,” notes Bill Abolt, first deputy commissioner of the Chicago Department of the Environment.
But Chicago area contractors do not have that same infrastructure in place when it comes to the recycling of wood, drywall and other materials likely to be found in mixed debris piles. Low tipping fees that range from $20 to $45 per ton have not been enough to convince haulers and contractors that they need to find another option. According to Abolt, the same State of Illinois guidebook to demolition debris handling that lists dozens of concrete recycling operations contains just one company listed as a recycler of mixed C&D debris.
Abolt does not foresee any change in the divided market situation in metropolitan Chicago. “The concrete recycling infrastructure is here to stay,” he says. “I don’t think there’s any doubt about it – the economics clearly work. In fact, I think they’ll get even better. But at the same time, we don’t see anything in the near future that will change the mixed C&D picture either.”
As of now, mixed debris generated in the Chicago area that contains primarily wood and drywall will most likely be landfilled.
NEW JERSEY
A recent court decision has drastically increased the options construction and demolition contractors in New Jersey have in regard to debris disposal. A federal court ruled last year that the state of New Jersey had improperly restricted the interstate hauling of debris and threw out the existing regulations.
The state law had allowed each county to control the flow of C&D debris generated in its own jurisdiction. But when a federal judged ruled that the practice unduly interfered with interstate commerce, the new regulations that resulted from that decision meant haulers not only had the option of shopping for low tipping fees in other counties, but also across state lines. Subsequently, landfill operators in Pennsylvania with low tipping fees have become an attractive option for contractors in western New Jersey.
“It was cheaper for builders to recycle when tipping fees were high – when the county could control the fees,” says Marie Krusan, executive director of the Association of New Jersey Recyclers (ANJR), Bridgewater, N.J.
The state’s previous regulations and high tipping fees had helped nurture the creation of several C&D recycling companies. How are they faring in the face of a new competitive climate? “It really varies depending on what part of the state they’re in,” says Krusan.
Louis Sanzaro of Ocean County Recycling Center, Toms River, N.J., says flow control issues have not had an impact on his company. Ocean County customers taking a look at Pennsylvania landfills will find considerable transportation costs to haul materials across the state. “The flow control issue does not affect us at all,” says Sanzaro.
A long-time paving contractor, Sanzaro started Ocean County Recycling more than a decade ago, in part because he was “getting tired of paying other people to dump this stuff.” The recycling operation is now its own independent profit center, according to Sanzaro, and end markets are fine.
In addition to crushing concrete and other paving materials, Sanzaro’s center accepts tree parts and stumps as well as clean wood such as two-by-fours and pallets. One of the prime uses for his tree and wood waste is as light, fluffy shredded material used as bedding for playgrounds. “That’s a great market,” says Sanzaro. “The schools and parents love it.”
Using re-processed road materials is actually better than using new materials, according to Sanzaro. “A lot of contractors have figured this out,” he says.
Mandated source separation is also an issue in New Jersey. The ANJR is trying to help C&D recycling firms by renewing lobbying efforts to overturn the source separation requirements that are in place in New Jersey. “We’ve been trying to lobby against that forever,” admits Krusan. “It’s ingrained in somebody’s mind that taking in unsorted materials is dirty.”
Most C&D recycling firms are “willing to do the separating themselves,” she says, “but they’re not allowed to do it” because of the state regulations in New Jersey.
Sanzaro, who is also president of the national Construction Material Recycling Association, Chicago, says he too is working at the state level to overturn mandated source separation. “Ease of operation for the contractor has to be a consideration,” he explains. “A recycler needs to be a convenience.”
GRAND RAPIDS
While markets in some regions have been established for the majority of materials found in C&D debris, one material increasingly used for residential siding and window casements is polyvinyl chloride (PVC). Plastics recyclers have traditionally had difficulty finding markets for PVC-based materials, and most construction site siding has been destined for landfills.
One program that was recently tested in Grand Rapids, Mich., however, has met with enough success to be adopted on an ongoing basis by the Greater Grand Rapids Home Builder Association (HBA).
The Vinyl Siding Take-Back program in Grand Rapids was created by a partnership consisting of the Vinyl Institute, the NAHB, the Greater Grand Rapids HBA, Lubbers Resource Systems, four vinyl siding distributors in the Grand Rapids area, and numerous local installers.
D’Lane Wisner, manager-environmental solutions, the Geon Co., a vinyl resins manufacturer based in Avon Lake, Ohio, helped coordinate the program on behalf of the Vinyl Institute. Wisner says the program was successful despite the fact that average tipping fees in the Grand Rapids area are a relatively low $45 per ton.
Key to its success was the eagerness of participants to take part in the program. The four vinyl products distributors taking part acted as drop-off points for materials hauled from construction sites. “They viewed the activity as a loss leader,” says Wisner, noting that while the companies had to rent an extra bin, their customers were more regularly visiting their sites and creating more opportunities for sales.
“We knew we were on to something when the distributors who were not part of the program began calling and trying to get on board,” says Wisner.
THREE KEYS IDENTIFIED
While innovative programs such as the one in Grand Rapids may help divert some C&D debris from landfills, three primary factors still have the greatest impact on diversion rates: the local tipping fees available to haulers, the existence of end markets for recycled materials, and the ease of recycling.
As long as debris can be landfilled at rates that contractors can live with – the figure is often pegged at from $35 to $50 per ton – the recycling of debris can be a tough sell. And for recycling to be an attractive alternative, sufficient end markets must exist to lure entrepreneurs into the recycling industry. Finally, contractors seem to be more willing to try recycling methods when the source separation burden is placed on someone else’s shoulders.
The author is managing editor of Recycling Today.
Get curated news on YOUR industry.
Enter your email to receive our newsletters.
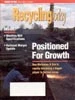
Explore the October 1997 Issue
Check out more from this issue and find your next story to read.
Latest from Recycling Today
- Global steel output tapers downward
- NWRA announces 2025 Driver of the Year, Operator of the Year winners
- The Scrap Show: Nanci Schuld of FE Trading Group LLC
- Call2Recycle Canada partners with RLG to advance battery collection
- Report delves into recovery opportunities for food-grade polypropylene
- Reimagining Supplier Payments in Metal Recycling: A Digital Leap Forward
- STEINERT Lithium Battery Detection and Removal from Waste Streams
- Driving the Future: Innovations in Waste & Recycling Technology