A study published by U.K.-based Waste & Resources Action Programme (WRAP) provides evidence that foamed concrete mixes using recycled and secondary aggregates offer comparable characteristics and levels of performance to those using primary material.
Researchers found the consistency, cube strength, drying shrinkage and leaching potential of foamed concrete using recycled and secondary aggregates to be comparable to that of equivalent sand foamed concrete. The study revealed no significant variation in the performance of foamed concrete using recycled and secondary aggregates from single and multiple sources and the material can be recycled repeatedly requiring little energy consumption.
More detailed findings from the study have been incorporated into WRAP’s technical guidance document, "Specification and Quality Control of Foamed Concrete Incorporating RSA," which is now available free from WRAP’s AggRegain Web site at www.aggregain.org.uk.
Morbark Hosts Demo DaysThe sound of trees and scrap wood being shredded and chipped echoed in Winn, Mich., Sept. 20 and 21 as more than 200 owners and dealers of Morbark processing equipment gathered in that manufacturer’s home town.
The company, celebrating its 50th anniversary in 2007, hosted its Demo Days event during a stretch of beautiful late summer weather, as invited guests, dealers and prospective dealers toured the Morbark factory and a nearby proving ground, where whole tree chippers, horizontal grinders and tub grinders were on display.
Among the stars of the Demo Days show were three track-mounted horizontal grinders (or wood hogs) that worked their way through a variety of tree branches, trunks and stumps.
Two large tub grinders also handled large amounts of material, while a pair of chippers worked through whatever tree trunks and branches were fed their way.
Customers interested in Morbark’s Talon Debris Shear were also able to see it work its way through thick tree stumps, and the company’s three-station multibagger was demonstrated by bagging wood chips.
During the two-day event, guests heard directly from Morbark President and CEO Lon Morey, son of Norval Morey, the company’s founder.
The family-owned company now employs some 600 people, most of whom work from the company’s 1.6-million-square-foot campus in the small town of Winn. The entire complex has grown outward from the original garage where Norval Morey started his business in 1957.
Morey credited the Morbark workforce for the greatest contributions to the company’s success. "We have one of the best groups of people working at Morbark today that we’ve ever had," said Morey. "They’re helping us make good decisions," he commented, praising the company’s employees for their dedication to quality training and continuous improvement.
Of the company’s 1.6 million square feet under roof, some 1.2 million of it is factory space that is currently producing about 100 pieces of equipment to be shipped out each month.
Morbark consumes some 30 million pounds of steel each year, generating about 500,000 pounds of steel scrap annually. As many as 300 welding machines help fabricate Morbark’s equipment, including some robotic welding units.
Despite the size of the company now, Morbark Vice President of Sales John Foote said, "Our company is still run like one big family."
Demo Days guests were able to receive Morbark family hospitality in the form of a Thursday dinner, a barbecue lunch on Friday and a tailgate party at the Central Michigan football game on Saturday for which Morbark had a block of some 1,000 tickets—a jumbo-sized family gathering.
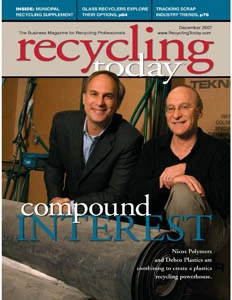
Explore the December 2007 Issue
Check out more from this issue and find your next story to read.
Latest from Recycling Today
- IDTechEx sees electric-powered construction equipment growth
- Global steel output recedes in November
- Fitch Ratings sees reasons for steel optimism in 2025
- P+PB adds new board members
- BlueScope, BHP & Rio Tinto select site for electric smelting furnace pilot plant
- Magnomer joins Canada Plastics Pact
- Out of touch with reality
- Electra names new CFO