ASPHALT SHINGLES TESTED FOR ROAD USE
The North Carolina Solid Waste Management Trust Fund has granted Ross & Associates, Raleigh, N.C., about $30,000 to commission and oversee performance tests aimed at determining the viability of using post-industrial asphalt shingles as a component in hot mix asphalt pavement. The tests will be conducted by the National Center for Asphalt Technology at Auburn University, Auburn, Ala. Mixes containing no shingle material, along with those containing 5 percent and 10 percent shingle material, will be tested and compared. Results are expected in mid-October.
The North Carolina Department of Transportation has already approved the use of post-industrial asphalt shingles at 5 percent of the hot pavement mix, but that amount does not provide the needed economies of scale to make the use of asphalt shingles viable. According to Ross & Associates, 8 percent to 10 percent shingle content is ideal.
If the tests are favorable, the NCDOT will authorize the use of additional asphalt shingles in road paving projects. And in the long term, the North Carolina Recycling Business Center, Raleigh, N.C., which is working to encourage construction and demolition debris recycling of all types in the state, would like to see 1 percent or 2 percent post-consumer asphalt shingles tested for use in pavement, as well.
According to state-generated statistics, of the construction and demolition debris generated in North Carolina, asphalt shingles represent 23 percent, and so there is strong motivation to find a cost-effective recycling use for the material.
MAXGRIND RECYCLES RESTRAUNT DEBRIS
Environmental Equipment Systems, Enfield, Conn., a recently appointed distributor of recycling grinders from Milwaukee-based Rexworks Inc., faced an unusual situation during its first Maxigrind demonstration. A restaurant owner in downtown Rutland, Vt., bought out a neighboring establishment and hired a contractor to demolish the building. The project included grinding the debris, and the entire job was to be done in the parking lot between the two buildings while the restaurant continued to serve its customers.
Every demolition and grinding job generates noise, dirt and dust, but because of the close quarters and busy location of this job, public safety also had to be considered. EES decided the job was a good way to demonstrate the Maxigrind 460G recycling grinder.
A Cat 325 excavator was used to knock down the structure and break up the debris prior to grinding. The Maxigrind was then put into action. The grinding phase of the job was completed in nine hours. Observers were impressed by the low noise level, the lack of dust and flying debris and the maneuverability of the Maxigrind in limited space.
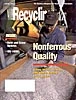
Explore the August 1996 Issue
Check out more from this issue and find your next story to read.
Latest from Recycling Today
- Smithers report looks at PCR plastic’s near-term prospects
- Plastics association quantifies US-EU trade dispute impacts
- Nucor expects slimmer profits in early 2025
- CP Group announces new senior vice president
- APR publishes Design Guide in French
- AmSty recorded first sales of PolyRenew Styrene in 2024
- PRE says EU’s plastic recycling industry at a breaking point
- Call2Recycle Canada, Staples Professional expand partnership