
The management team at Butler-MacDonald had spent more than a year assessing its operation, talking to customers and evaluating equipment to give the Indianapolis recycler and recycled resin supplier new capabilities and faster turnaround times in the future. But just as it was about to sign a hefty contract with Erema North America Inc., Ipswich, Massachusetts, for a new recycling line, the COVID-19 pandemic cast uncertainty over the industry.
“We were in the final stages of negotiating a contract with Erema,” says J. Scott Johnson, CEO and president at Butler-MacDonald. “We could have pulled out right then and there because we had not signed anything, and no money had transferred. But we took a week to think about it, and one of the advantages you have from being in business 38 years is you realize that for every setback there is an equal or better recovery.”
He continues, “I refused to give in to the idea that now was the time to give up. We went ahead and made the purchase, and I still feel as strong about that decision now as I did back then, if not stronger.”
Butler-MacDonald’s management recognized a growing demand to recycle lighter, thin-walled containers that it could not profitably meet with its current equipment. So, the company worked with Erema to build a new extrusion system that includes proprietary design modifications.
Johnson says Erema was willing to adapt to meet his company’s needs. One example is the inclusion of a DSW 40 twin-screw stuffer that allows the injection of additives directly into the barrel of the extruder. The advantage is more-homogeneous blends and less chance of stratification in the preconditioning unit, plus a potential reduction in additive costs, Johnson says.
“It is a universal machine that will process a wide range of materials, and we run a lot of different polymers,” Johnson says.
The new extrusion system is an Intarema 1714 TVEplus. It is specially designed for materials that are difficult to recycle, such as heavily printed film and very moist materials. Erema says the machine features ultrafine filtration, thorough melt homogenization and high-performance degassing in a single step. Melt filtration takes place upstream of extruder degassing, which results in higher quality recycled pellets.
The Intarema TVEplus machines also feature Erema’s patented Counter Current technology that increases throughput by changing the direction of rotation inside the cutter/compactor. The plastic material moves in the opposite direction of the extruder screw. The speed of the material increases, and the extruder acts as a sharp edge and cuts up the plastic. In addition to the extruder screw being filled nearly pressure-free with preheated material, it can also be processed at lower temperatures at high throughput.
The new Erema line will give Butler-MacDonald a total of 12 lines. The new line with a 140-millimeter extruder is scheduled to go into operation at Butler-MacDonald in mid-December. At full capacity, it will have an average throughput of 3,600 pounds per hour, depending on the plastic being processed.
Johnson says it will add about 22 million pounds per year to his company’s total output. The new system will reduce Butler-MacDonald’s turnaround time from the current average of five to six weeks to just one to two weeks.
“A lot of our customers are brokers or other recyclers we do the work for,” Johnson says. “They have money invested and they want to get it turned into something profitable as quickly as possible.”
Butler-MacDonald will use an Erema HG 344D hot-die-face pelletizer with direct-drive technology and an Erema vibration table for cooling and drying the pellets, which are as close as possible to being immediately ready for packaging.
“When you are generating 5,000 pounds an hour, you can eat up a lot of warehouse space,” Johnson says. “We are hoping that this new system reduces warehouse space to about a quarter of what it used to take.”
The new Erema line will give Butler-MacDonald a total of 12 lines. The company has about 55 employees working shifts 24 hours a day, six days per week. Johnson says he is trying to hire 15 to 20 more employees.
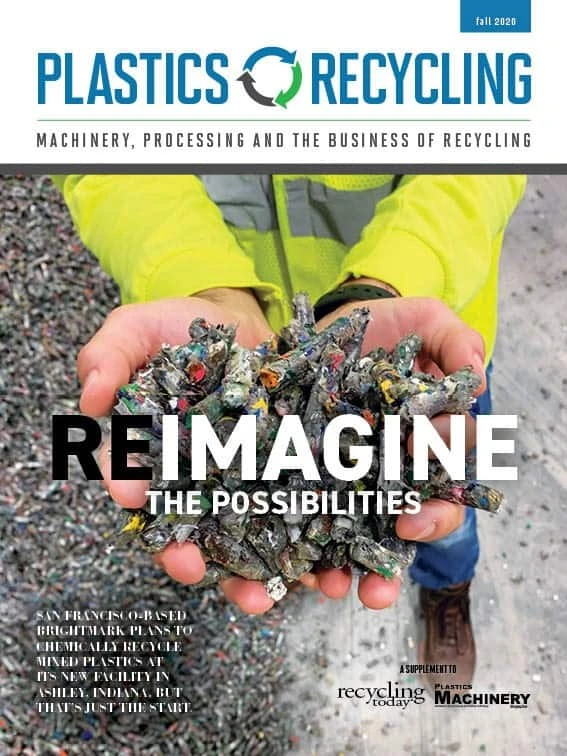
Explore the Fall 2020 Plastics Recycling Issue
Check out more from this issue and find your next story to read.
Latest from Recycling Today
- Athens Services terminates contract with San Marino, California
- Partners develop specialty response vehicles for LIB fires
- Sonoco cites OCC shortage for price hike in Europe
- British Steel mill’s future up in the air
- Tomra applies GAINnext AI technology to upgrade wrought aluminum scrap
- Redwood Materials partners with Isuzu Commercial Truck
- The push for more supply
- ReMA PSI Chapter adds 7 members