
As electric compact wheel loaders (CWLs) begin hitting the market, those who are not early adopters understandably have questions. Do these CWLs have the same power as their diesel equivalents? Will charging ruin the flow of my workday? What about maintenance?
The answers might surprise you.
What is required to charge an electric CWL?
For optimal charging time, it’s strongly recommended to have a 240-volt, 32-amp Level 2 AC-charging setup that uses an SAE J1772 charging adapter or J plug. If this terminology is new to you, don’t be intimidated. This is the same setup recommended for electric cars, and 240 volts is what many household appliances run on. While you can use a 120-volt outlet, charging will take longer.
A 240-volt, Level 2 AC setup will fully charge a Volvo L25 Electric CWL in six hours. A common household 120-volt outlet will do the job in 24 hours.
Off-board fast chargers and solar-powered charger options also are available for electric CWLS.
AC Level 2 charging is best for battery life, but it’s all about a user’s needs.
Research and development will provide a wider range of charging options in the near future, and, as electric vehicles continue to roll out into the market, improved charging infrastructure will follow.
It is not recommended to charge with a gas-powered generator because that goes against the goal of this machine: to be more environmentally friendly.
How long will it hold a charge? Will that affect my workday?
A CWL can be used in many ways, and the different job site applications can alter how long the batteries last.
Batteries should be charged whenever there is a pause in the workday. Because we use lithium-ion batteries, there is no memory effect (reduction in the longevity of a rechargeable battery’s charge related to incomplete discharge in previous uses). So, you can top them off during a break and continue throughout the day.
It’s also best practice to charge from midlevel to full as opposed to draining the battery completely before recharging. When charging from as low as 30 percent back up to 80 percent or 100 percent, it’s better for overall battery life. These aren’t the lead-acid or nickel-cadmium batteries used in early versions of electric power tools that were affected by the memory effect. If those batteries weren’t charged properly, they became useless after a short time. Lithium-ion batteries are more advanced and forgiving.
I’ve seen customers doing heavy applications that include cutting, grading and large workloads who have worked through the morning and needed a quick charge at lunch. Meanwhile, customers who use the machine intermittently or in lighter applications have found it can last longer. From our testing, the reported work time is four to six hours, depending on the application.
Does it need to be turned off during the day to save energy?
No. Volvo electric CWLs come with auto electric motor shutdown. If an operator stops the machine, the electric motor turns off almost immediately. To get working again, the electric motor turns on instantly and provides immediate power.
Diesel equipment operating time is defined by engine runtime, and many of those hours are counted while the machine is idle. Jobs that add 10,000 hours on a diesel machine might only add 6,000 or 7,000 hours to an electric machine. These saved hours lower operating costs and total cost of ownership while also improving resale value.
Another benefit is that the lights on Volvo electric machines (rotating beacons, work lights, travel lights, etc.) are LED, so they’re very low power consumers.
Does an electric CWL have as much power as a diesel machine?
The Volvo L25 Electric CWL specifications are nearly identical to its diesel counterpart, except for a marginally higher operating weight and static tipping load.
We’re not initially offering a high-speed version of this machine to better maintain the battery during a full workday. The maximum speed of the L25 electric wheel loader is set at 12.4 mph. The good news is that high speed isn’t required for most applications but is necessary for an application when you need to drive from site to site without hauling the machine.
A popular aspect of an electric machine is that its motors provide instant torque. There’s no feeling of a delay, which happens with some diesel machines.
How is maintenance different on an electric CWL?
Maintenance is much simpler on an electric machine. Diesel exhaust fluid or filters are not needed, and essentially the only supplies required are grease and hydraulic oil. This is much different than with a conventional machine, which requires engine maintenance as often as every day, with additional preventive maintenance.
Electric components like a lithium-ion battery, inverter, AC-to-DC power converter, battery management unit and charging plug need visual and functional inspections. Any components not working will be replaced rather than repaired.
Because of the use of electricity, much of the additional training needed is about safety. Technicians need to learn some new concepts and functions, but that’s part of our ever-evolving industry.
The lifetime of battery-electric components should be equal to or better than that of the diesel engine. Volvo CE conservatively estimates users will see 35 percent savings in maintenance costs and time over the course of the machine’s life.
Why should I use an electric CWL instead of diesel?
Think of all the new and different ways electric CWLs can be used thanks to their zero emissions and lower noise. They can work indoors and outside of normal business hours, plus they have a fast-charging option to work longer hours.
Incorporating sustainability measures will be good for long-term profitability, too. More local and state/provincial governments are adopting clean air policies, so if you want better odds of winning bids, you need to prove you’re using equipment with reduced or zero emissions.
Don’t forget to assess the total cost of ownership and not just the purchase price of such a machine. Electric machines offer fuel savings, less maintenance and extended component life—and that’s in addition to work you might be able to win because of the sustainability and noise differences.
Hear it from an actual user.
Eberhard, a German company that offers civil engineering, deconstruction, recycling and remediation services, tried a Volvo L25 electric CWL last year. The machine was used at a landfill and for road clearing, small-scale material handling and as a forklift.
The team says it enjoyed its low emissions, silence and minimal vibration. Eberhard says it plans to use the L25 electric on construction sites in downtown Zurich and other cities where requests for silence and low emissions are growing.
“As our organization has grown, we wanted to look at alternative machines that don’t rely on diesel,” Eberhard owner and CEO Bruno Meier says. “This is our first foray into the world of electric machines and it’s going well.”
If you have questions or concerns, treat it like any other important business decision and connect with your dealer or original equipment manufacturer.
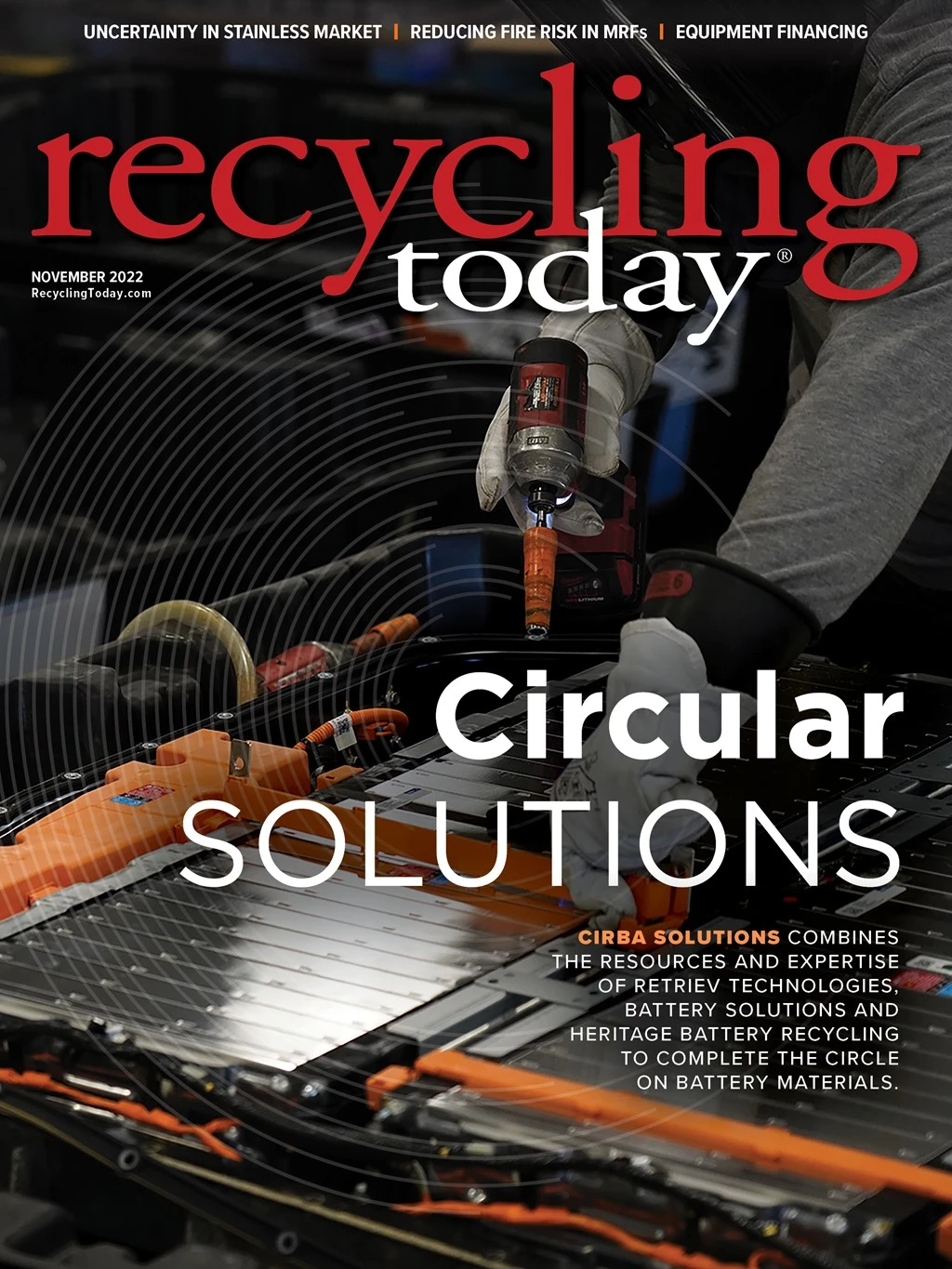
Explore the November 2022 Issue
Check out more from this issue and find your next story to read.
Latest from Recycling Today
- ReMA opposes European efforts seeking export restrictions for recyclables
- Fresh Perspective: Raj Bagaria
- Saica announces plans for second US site
- Update: Novelis produces first aluminum coil made fully from recycled end-of-life automotive scrap
- Aimplas doubles online course offerings
- Radius to be acquired by Toyota subsidiary
- Algoma EAF to start in April
- Erema sees strong demand for high-volume PET systems