
Copper cable that is recovered for recycling usually comes from a building that is being remodeled or demolished. But a cable recycling project taking place in Cleveland can be described as anything but typical because the cable is located about 2,000 feet below the ground inside a salt mine.
To put the depth of the mine in perspective, 2,000 feet is twice the height of Cleveland’s tallest building, Key Tower. Machinery and other items that take the five-minute elevator ride through the earth down to the mine don’t usually come back up because it is too difficult. In fact, vehicles are taken apart to get them down the elevator and are reassembled once in the mine. An entire mechanics’ garage, washing station and fueling station all within the miles of salt-rock that extend below Lake Erie.
Mining began at the site in 1965. The mine spans several miles, and the floor, ceiling and walls are all made of salt, which is cut out in what is called a “room and pillar” design. Cargill has owned and operated the mine since 1997. It is part of the Wayzata, Minnesota-headquartered company’s Cargill Deicing Technology division, based in North Olmsted, Ohio, and one of three salt mines the company operates. The other two are in Lansing, New York, and in Avery Island, Louisiana. The Cleveland mine employs about 193 people and produces road salt that is shipped throughout Ohio as well as to several nearby states.
George Campbell, mine general foreman, says areas that have been mined fully are designed to slowly collapse into themselves. Anything within the old sections of mine that doesn’t need to go back up to the surface stays in the mine. Until recently, that meant old cable, which continued to hang in the ceilings for many years, even though it was no longer in service.
“Over the years it had been determined that the cost of removing these items was expensive and time consuming,” Campbell says.
A GOOD IDEA
About a year ago, Scott Evilsizer, an electrician who had been with Cargill for just one year at the time, proposed an idea to remove the cable without taking away from valuable work time.

Cargill encourages its employees to volunteer, allocating three days per year to do so. Many of the mine’s employees work long hours and late shifts, making it difficult to find a way to give back to the community through service. Evilsizer suggested that employees volunteer their time to remove the cable, donating the proceeds from recycling the material to charity.
“With Cargill’s commitment to community service, employees such as Scott have brought new and innovative solutions to recovering this metal,” Campbell says.
Evilsizer presented his idea to Storeroom Manager Jennifer Rhodes. Rhodes discussed the idea with supervisors, who agreed to proceed with the volunteer opportunity. Other miners soon chipped in.
“Our employee brought it to us, so we wanted to do everything we could to support him,” Rhodes says. “It was something that he was really passionate about.”
Rhodes describes the cable recycling project as a volunteer opportunity that “suits the lifestyle” of many of the miners.
“We staff seven electricians throughout the mine, and all of them have chipped in,” Campbell says. “As well, we have our maintenance department and belt crew recover most of the wire and take it to the electrical connex (a large shipping container), where it is separated and boxed.
“This project continues on the surface, where multiple employees also contribute. It has become a companywide volunteer project,” he adds.
“Salt is a corrosive substance that will forever keep us finding ways to be innovative in how we dispose of and recover our precious minerals and metals.” – Steve Horne
The recovered wire and cable often comes from areas of the mine that are no longer being mined. The wire and cable provided Cargill with many years of service but now is being replaced. “We are currently upgrading our incoming power and need larger wire to carry the voltage we need to operate our equipment and ventilation system,” Campbell explains.
Evilsizer says he remembers thinking when the upgrading began, “It’s kind of sinful to bury all of that wire.”
Most of the cable is recovered using a cable truck, and the company reuses what cable it can.
Damaged sections, usually those with multiple splices, are cut into small pieces and placed in Gaylord boxes. The exposed copper is blackened from being inside the corrosive atmosphere of the salt mine, but inside its protective casing, the copper is the shiny, reddish metal one expects.
Once the boxes containing the pieces of wire and cable are full, they are hoisted up to the surface via the skip elevator.
Campbell says time management is a challenge when trying to recycle underground. “We find the time to collect the wire as it is our intent to reuse as much as possible, but getting it transported out of the mine sometimes takes a while. We only want to send this up when it will not interfere with operations.”
Cargill also recycles wire and cable from its above-ground buildings. All of the material is picked up by a local recycling company and taken to a third-party processor that removes the jacket from copper. The copper is weighed, and Cargill is paid market value for it.
A WORTHY CAUSE
Rhodes says Cargill always knew the material was valuable, but it took someone like Evilsizer, who had the initiative to organize the effort and to find an outlet for the cable, to get the ball rolling for the company.
Cargill raised more than $19,000 after recycling only two batches of cable.
All the money the company raised through cable recycling was donated to St. Jude Children’s Research Hospital, based in Memphis, Tennessee. According to Cargill employees, the charity was chosen because of its dedication to families, children and its community. “Cargill and its employees have the same interest,” Campbell says. “It’s how we give back.”
Employees had a goal to raise $25,000 for the charity by mid-September 2015 when Cleveland hosted its St. Jude Walk/Run to End Childhood Cancer, and employees exceeded this goal, raising $26,000. The employees are continuing the recycling program into 2016.
Steve Horne, mine manager, says the sky’s the limit. “There are always projects at the mine that will require electrical upgrades,” he says. “Salt is a corrosive substance that will forever keep us finding ways to be innovative in how we dispose of and recover our precious minerals and metals,” Horne adds.
“Continued growth in community service programs is always a goal at Cargill,” he says. “One hundred percent employee involvement is our goal. We will continue to challenge our employees until we reach it and this is one way to help us achieve our goal.”
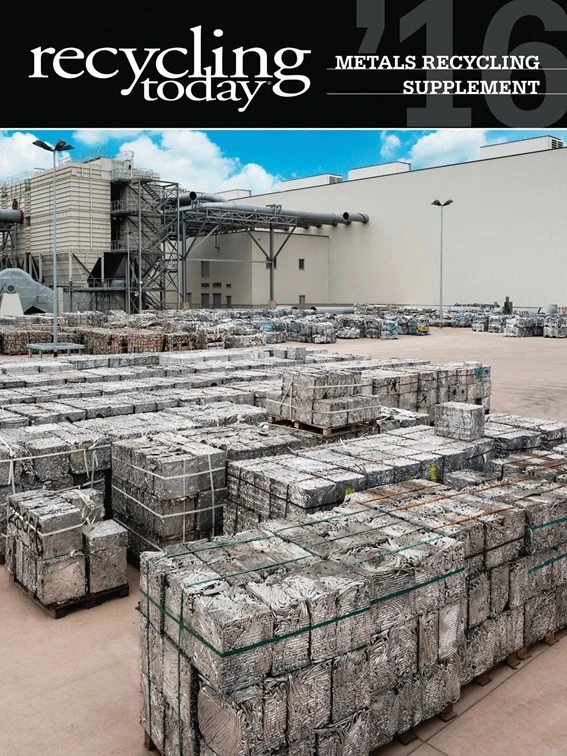
Explore the Jan 2016 Metals Recycling Supplement Issue
Check out more from this issue and find your next story to read.
Latest from Recycling Today
- ICM to host co-located events in Shanghai
- Astera runs into NIMBY concerns in Colorado
- ReMA opposes European efforts seeking export restrictions for recyclables
- Fresh Perspective: Raj Bagaria
- Saica announces plans for second US site
- Update: Novelis produces first aluminum coil made fully from recycled end-of-life automotive scrap
- Aimplas doubles online course offerings
- Radius to be acquired by Toyota subsidiary