Since 1986 ACI Plastics of Flint, Mich., has been providing plastics recycling services with a focus on the automotive components sector, such as instrument panels and bumpers.
In that two-decade-plus span, the domestic auto industry has been
ACI Plastics at a Glance |
Principal: Scott Melton, president and owner Location: Flint, Mich. No. of Employees: 60 Equipment: Four grinders and one shredder; two custom separating lines for layered plastic materials; and extruding and pelletizing equipment Services Provided: Recycling and toll processing of post-industrial and obsolete automotive plastic scrap, including items such as automotive bumpers and instrument panels made of different types of plastic molded in layers; closed-loop re-grinding for molders; and custom blending of recycled, virgin and mixed plastic resins. |
Although ACI Plastics can indeed feel the impact of the down portions of those cycles, the company is benefiting from a greatly increased interest in recycling and recycled materials that automakers and other manufacturers are showing.
PURITAN PRACTICESProducers of recycled-content plastic resins do not delude themselves that there is anything easy about serving their customers. "The separation and recycling process is really about purity," says ACI Plastics President Scott Melton. "Customers can’t have impurities if they’re putting this material back into their instrument panels or other products."
That has been the challenge taken on initially by ACI founder Mark Lieberman and now carried on by Melton and the 60 associates of ACI. (Lieberman, the plastics broker who started the company, sold his stake in ACI in the summer of 2007.)
ACI handles a wide variety of materials and produces recycled-content feedstock for sale and on a toll processing basis.
Size reduction by grinding, shredding and pelletizing is a key service, as is blending and compounding of materials to create desirable feedstock for its customers.
What has helped ACI distinguish itself in the plastics recycling market, however, is its innovative thinking and attention to the materials separation process.
Much of the value-added service that ACI provides to its customers involves taking in scrap that has more than one type of plastic in layers (or that is otherwise attached) and processing it until high-purity recycled-content products emerge.
ACI’s research and ability to innovate have not simply allowed it to recycle painted TPO (thermoplastic olefin) vehicle bumpers and other automotive components, but to actually create, establish and expand such markets.
"We’re the only recyclers in North America that we know of that can take in automotive instrument panels and separate the plastics to a 99.98 percent purity level," says Melton.
"The separation system we have will separate all three components and recycle 100 percent of the material," says Melton. "The substrate goes back to the molder, the skin is reground and used as an inside layer in garden hoses, and the foam can be used either as carpet padding or in the Ken-Dri powder material we make that can absorb water on surfaces like baseball fields," he says.
BUMPERS AND BEYONDAmong the types of scrap a visitor to the 125,000-square-foot ACI Plastics plant sees are incoming shipments of TPO automobile bumpers in a variety of colors.
ACI takes in as many painted TPO bumpers as its buyers can find, but the ability to process this material and make a desirable end product has not been a given throughout the company’s history.
With the obsolete TPO auto bumpers that the company collects from auto dismantlers, the key has been the removal of paint, using a process the company developed in 1997.
The end product ACI produces from painted bumpers can be molded into a new bumper, Melton says, not as a blend, but as a sole feedstock. "Most other suppliers provide a material that can be used as an 80/20 or maybe a 50/50 blend."
The ability to turn mixed, painted TPO bumpers into a closed-loop product that can go back to bumper molders was an early breakthrough for the company that it has used as a pattern with other materials, such as instrument panels.
Online Sidebar - Global Viewpoints |
"Dismantlers are getting bumpers whether a recession is going on or whether the economy is going great," says Melton.
It has also connected ACI to a network of scrap generators above and beyond the molders and other factories from which it sources scrap.
On the sales side, ACI’s home in Flint means that it is tied to the Midwest’s auto industry and other manufacturing that occurs in the Great Lakes region, but Melton says the company has broadened its customer base on the sell side just as it has on the buy side. "We don’t have any one customer that makes up more than 13 percent of our sales," he notes.
The variety of materials it sells and its ability to serve customers in different ways has helped ACI broaden those bases.
Just in the realm of bumpers, "We deal in 30 or 40 different types of TPO," says Melton. "Automakers do not necessarily unify on one spec."
He adds, "We think of ourselves as a technology-based recycler. We really try to innovate and meet specs that compare with virgin material. We don’t just put scrap through a pelletizer and hope someone will use it."
ACI’s goal is to work with its customers in a way that maximizes either profits or material sourcing for that customer. "We do function as closed-loop processors for many molders," says Melton. "But we also create products to sell to the wider market, and we’ll custom-blend materials to provide a solution for a customer."
Melton estimates that about 50 percent of ACI’s activity is toll processing for customers while the company takes ownership of the other 50 percent of the scrap that it handles.
The company operates four large grinders and a shredder to downsize material. Each grinding line is outfitted with a dust-control system and an all-metal separator. Two custom separation lines are set up to address mixed or layered plastic materials. Four large mixing tanks are used to remove paint from TPO bumpers. And storage silos at the back of the property store materials that will later be shipped in bulk in tanker trucks.
ACI has also ventured into the production of branded resins and blends, many of them made with recycled resins but also some made from virgin resins. Its branded products include Enviraloy and Impact recycled resins and C-Flex and P-Flex virgin TPE (thermoplastic elastomer) resins.
The virgin resins are used by makers of such things as earplugs, baby bottles and gaskets for the RV industry.
PEOPLE POWERWith 60 employees and 125,000 square feet of space, it may be difficult to think of ACI as a small company, but Melton still does. "We concentrate on building a quality product," he remarks. "We are not the cheapest source out there, but we don’t lose many companies to competition."
Melton says he strives to keep a small company atmosphere in the workplace as well. "I give managers a lot of autonomy," he says. At the production level, "We try to hire good people and spend a lot of time training and re-training them."
The company has reached out to Goodwill Industries to act as a training site for people newly entering the workforce. "We have an apprentice program through Goodwill where people can train here in forklift driving, administrative roles or in our lab and receive a certificate of completion," says Melton. The company also works with Goodwill to employ developmentally disabled people in some disassembly tasks.
An overall goal for Melton is to keep the atmosphere one that is more reminiscent of a small, family company. "In a work day, you need to both have fun and make money, and you have to do them in proportion. If they’re not in proportion, things won’t work," Melton continues. "We are a small company, and the good news is people here see the owner of the company every day. The bad news is, they get to see the owner of the company every day," he quips.
Melton credits plant manager Paris Stetkiw for organizing what can be a very complex set of activities taking place in the plant on any given day. "Paris does a terrific job organizing things here," says Melton.
The company also relies on Scott’s wife Ann Melton to oversee the sale of end products. "We ship a lot of our product within this region, but we also ship material as far as Hong Kong and Taiwan," Melton notes.
GREENER PASTURESSince Melton left the banking industry in 1995 to work full time for ACI (a customer of his when he was a banker), the company has had to face several challenges, including a fire in the plant building in 1997.
Despite challenges such as the fire or the financial distress of Midwestern auto suppliers who serve the domestic auto industry, Melton is optimistic about the overall market for recycled plastics and ACI’s ability to serve that market.
One of the more encouraging trends has been the declining resistance by manufacturers (in the automotive sector in particular) to use recycled content in their plastic products. "A lot of automotive industry manufacturers today have a spec that allows for 20 percent recycled resin—that’s actually a big step for auto manufacturers," says Melton. One automaker may well be poised to zoom past that 20 percent figure, he notes.
"Overall, I think the acceptance today is much greater," he says. "There is a new group of people at manufacturing companies with a willingness and desire to work with recycled resins. And it helps at ACI that we have plant managers and extruders who have a great depth of experience—it’s a good group of people to work with customers who have questions."
The increased acceptance of recycled rubber may also benefit ACI. The company is working with Lehigh Technologies Inc., Naples, Fla., to incorporate ultra-fine recycled rubber powders into a wide range of plastic compounds. Lehigh uses cryogenic grinding technology to create recycled rubber powders that can be incorporated back into rubber or plastic products. Melton says ACI and Lehigh are both "bridging the gap between what recycling was and what it will become."
Rather than battening down the hatches in the face of declining Midwestern automotive production, ACI is instead faced with the choice of where and how to pursue additional opportunities.
Melton says there are several states in contention to be the home of an additional ACI facility should the company need to expand to serve its customer base. "There are customers trying to draw us to Ohio, but we also bring in a lot of material from the South and would like to save freight by being closer to them," he notes. "And there are also customers asking us to be in Mexico."
Even in the Midwest, Melton sees opportunities to grow in a world where the recycling of materials is both gaining favor and making increased financial sense.
"I still call on customers who say it’s easier for them to landfill scrap and throw it away—they don’t even want to go through the [financial] numbers," Melton remarks. "When I hear that, I know there are still untapped markets for us to reach, which means ACI can keep growing."
The author is editor in chief of Recycling Today and can be contacted at btaylor@gie.net.
Get curated news on YOUR industry.
Enter your email to receive our newsletters.
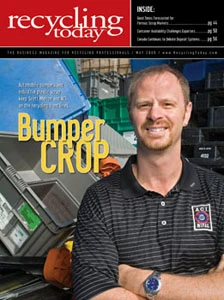
Explore the May 2008 Issue
Check out more from this issue and find your next story to read.
Latest from Recycling Today
- Nucor expects slimmer profits in early 2025
- CP Group announces new senior vice president
- APR publishes Design Guide in French
- AmSty recorded first sales of PolyRenew Styrene in 2024
- PRE says EU’s plastic recycling industry at a breaking point
- Call2Recycle Canada, Staples Professional expand partnership
- Circular Services breaks ground on north Texas MRF
- Tariff uncertainty results in choppy nonferrous scrap flows